Introduction: Simple, Elegant Steel Bar Rose Arch
All gardens look more interesting with decorative features in them whether they are supporting plants or providing shelters or windbreaks for plants and humans. Arches naturally suggest an entrance or continuation and look particularly quirky and intriguing when they are up against an exterior wall like this one. You instinctively feel there must be a secret doorway - if only you could find it.
I often find that wooden structures can appear too cumbersome for their duty and this detracts from the elegance and beauty of the plants they are meant to be supporting. It is for this reason that I like to see metal structures in the garden landscape, or as is often the case you do not see them because of their finer structure, as witness the photo below in our garden, where the arch has been in place for decades and supports a giant climbing rose.
Step 1: Inspiration & Design Criteria
I designed the arch in this project for a friend, who has a very minimalist style of garden but who wanted something a little more decorative to hold up a wayward, climbing rose. I also made it in sections, which could be bolted together, as it was to be made in the workshop and then transported to the garden.
I've made several arches and one aviary from welded metal bar and can testify both to the durability of this material and to how they contribute to the architecture of the garden without being too obtrusive. Left unpainted, the metal arches develop a patina of oxide which I find tasteful and which blends well with the verdure.
My arches invariably comprise two sides embedded into the ground. Each side looks like an ethereal ladder, horizontal 'rungs' welded to two uprights. To join these sides and form the arch shape, I attach the top with bolts to the vertical ladders. I make the arch shape by bending four identically shaped sections which when joined at the centre of the structure form the shape of a Tudor arch. To decorate the highest point of the arch I like to have a finial as the finishing touch to emphasize the structure's shape. Image thanks to the British Library 15th Century Pseudo-Heloise, Poems; Art d'amour, from where I took the inspiration for the shape.
The free ends at the bottom of the arch are embedded in the ground, I normally create a guide hole for each free end with the pointed end of a heavy crowbar. Each side of the arch is brought into position so that the free ends are in the holes and they are then forced deeper into the ground by pushing down with the foot onto the lowest horizontal 'rung'. With this particular arch I knew that the soil was pretty free of any obstructions like stones or buried broken tiles but if I thought otherwise I would grind the free ends to a point to aid the insertion.
The required dimensions for the rose arch in this project were :
Height 1800mm (71"),
width 400mm (16")
span 1100mm (44").
The height was to be the above ground height, a further 400mm (16") would be pushed into the ground . I decided to make the uprights 1600mm (63") long, the balance of the required height to be that of the arch section.
Step 2: Materials
The structure was made from 12mm (½") round mild steel bar - specified by my local supplier as 'smooth weldable reinforcing bar'.
I cut the 8 brackets for joining the sections together from steel angle 25mm x 25mm x 3mm (1"x1"x ⅛").
The embellishment at the top was made from two items taken from a selection of cast metal decorative finials I had purchased some years ago from Sharratts in Leigh, Lancashire. One was a round ball (not shown) and the other a fleur de lis.
I think the addition of a finial, makes for an aesthetically-pleasing and 'finished' look to the project. To me, it turns something made from very cheap and basic metal sections into something much more decorative.
Step 3: Fabrication Arch - Sides
I cut and welded together the components that made up the two 'ladders'. The first (lowest) bottom rung of the ladder was 40 cm from the ladder bottom. the protruding ends were to be pushed into the ground. When both sides were completed, I cut eight short lengths of angle, one face of each angle was drilled to accommodate a 8mm bolt.
Each angle bracket was welded to the top of the 'ladder ends'. The four remaining angle brackets were welded to the ends of the arch top 'legs'. This was to facilitate the assembly of the arch, in particular in this case because it needed to be transported and didn't fit in the car as a whole item! However the ladder and top can be made in one piece but it makes for an unnecessarily difficult time bending something so unwieldy!
Step 4: Fabrication Arch - Top - Bending the Steel Bar
As the design requires no complicated curves, there is no need to make any bending forms for the top section. The curve is simply made by my use of a home-made bending fixture. Use a 1m or a 3' length of 'I' section rolled steel joist, at one end of which, is welded a short piece of angled steel across the width. this acts as the fulcrum when bending.
In addition to the bending fixture, I also fabricated a bending key. I made this from an old piece of wrought iron bar. (see above and below right).
The four lengths of bar were bent at one end (the apex) using the key and fixture.
The other end (the downward leg) of each was bent with the length clamped in a bench vice. I did this because I had better leverage for this bend by using the mass of the work bench to hold the bar.
I bent the first bar until I was happy with the overall look, i.e. for my Tudor Arch design, the rest were then bent to match. I found it was easy to get the feel for the rest after doing the initial length, so each only required minor 'tweaking' after I had compared them with the original.
Step 5: Fabrication Arch - Top - Welding
Before welding the the four elements of the top of the arch together, a collar of metal (a jubilee clip of the appropriate diameter) was used to temporarily secure the joint prior to welding.
The downward legs of the Arch top hung over the sides of the workbench and I also supported the top with some metal blocks. This held everything securely, whilst I was welding.
Step 6: Fabrication Arch - Top - the Finial
The finial was a composite, namely a fence rail end fleur de lis and a ball. I welded them together as the ball gave the fleur de lis more dramatic emphasis in the design.
I then welded the completed finial to the top.
Step 7: Putting It All Together
The remaining four drilled pieces of angle were welded to the lower ends of the arch top legs such that the holes were coincident with those on the ladder section.
On a stormy day, the arch took on a distinctly Gothic look and in the Winter we thought fairy lights would look good.
If you'd like to see more of my designs for home and garden, mostly made from repurposed, upcycled and scavenged materials, then feel free to visit my site The Green Lever.
All the very best
Andy
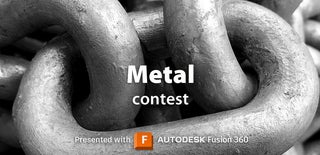
Participated in the
Metal Contest