Introduction: Skull Goblet - Giant Lego Style
This was one of those ideas that amused me so much in my head that I just had to make it a reality, I love the juxtaposition of the jolly LEGO skull and the macabre idea of fashioning a goblet from the skull of your foes.
This is not a reproduction of any real LEGO piece, but rather designed around the key dimensions of the LEGO skeleton and normal LEGO goblets, so it fits in the aesthetic. If you've printed my giant LEGO skeleton then you can print this at the same scale and it should fit in his hand perfectly.
This dead (hahaha) simple project is covered completely in the video so I recommend you take a look, but I will elaborate in the next steps too.
Step 1: Printing
Files
Grab the files here from myminifactory
Scaling
The default files are at 8X LEGO scale (it results in a sane size, about 200ml of volume) but you can easily scale it however you like, the table below will give you an idea.
The row "Scale (from 8X)" indicates the scaling factor you can use in your slicer if you want to change from the default 8X scale.
Lego Scale | 4 | 5 | 6 | 7 | 8 | 9 | 10 |
---|---|---|---|---|---|---|---|
Total Volume (ml) | 21 | 41 | 72 | 114 | 193 | 328 | 559 |
Scale (from 8X) | 50% | 63% | 75% | 88% | 100% | 113% | 125% |
If you want it to match the default Giant Skeleton size then you need to scale up to 125% (i.e. from 8:1 to 10:1 scale)
Support
In general support is not needed, although you could use it in the recess of the stem if you like. I ended up using support because I chose "concentric" top and bottom layers for a clean surface, if you are using parallel layers then supports won't be needed.
Filament
If you are planning to put liquid in it then I highly recommend printing in ABS so that you can smooth the end result, making it water-tight. You should be aware that most filaments and printing processes are not officially (or even unofficially) food safe. From my point of view the stuff you are putting in a skull shaped shot glass at your next Halloween party is probably more toxic than the receptacle, but make your own informed choices....
Step 2: Finishing
Smoothing
I specifically chose to print mine in rigid.ink silver and white ABS so that I could use acetone vapor smoothing on it. The vapor smoothing results in a glossy LEGOesque surface which is also watertight, both features that I was after.
I highly recommend watching the video in the first post, but the process is as follows
- Find a container (that is not affected by acetone) big enough to hold both pieces
- Line the sides with paper towel (held in place with magnets)
- Soak the paper towels in acetone
- Place the objects in the container (make sure you can remove without touching them)
- Set a stopwatch for 30-45min (important or you will forget and come back to a blob)
- Remove objects without touching and leave for some hours to cure.
Glueing
Since I used ABS I could bond the skull and the stem parts with acetone, but if you are using another filament then something like Super Glue will be just fine. Simply dip the protrusion on the stem into acetone, or place a small amount in the recess of the cup. Be sure not to use so much that it squeezes out when you push them together.
Painting
I painted the face with hobby acrylic paints and a fine brush. Take your time, letting the recesses guide the brush and contain the liquid paint.
If you would like to try your hand at cutting a decal then you can use the files here which are a DXF/PDF or the face, flattened out.
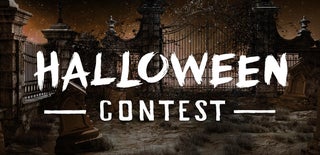
Participated in the
Halloween Contest 2018