Introduction: Steel Rack and Cold Saw Station
The shop got a cold cut saw and it was apparent that we needed a steel racking system to go along with it. There were some unique constraints for this racking system that I had to work with. First of all I had to find a place to put it within the shop. We have a large shop, but the rack couldn't protrude too far into the open work space. The location chosen required some relocation and replacement of some pre-existing storage. The new rack would extend into the paint area thus the need to create new and improved shelving for the painters on the back side of the rack.
The rack I designed has six upright supports all of which are anchored into the ground. While the structure was made to be self supporting I didn't want to take a chance of this ever falling over. On the left side there is a work station with conveyor rollers for the cold saw and cantilever arms for steel storage. On the right side there are shelves and racks for all the paint supplies. While there are commercially available units building a custom unit provided many features that aren't available elsewhere.
This is a list of materials needed to build this awesome storage rack:
2x4x20' 11ga -5
1x2x20' 11ga - 4
1x2x20' 14ga - 11
1x1x20' 14ga -1
3/4 PLY - 5
Step 1: Main Support Posts
I started the process of construction completing the cut list. There is nothing that slows down a project like having to stop and cut the next pieces you need. I find it much more efficient to cut everything first and then focus on assembly and construction without interruptions.
The base members needed holes drilled in them for attachment to the floor. Be sure to drill these holes before welding on the uprights. On the bottom of each side drill a 3/8" hole, on the top drill a 1" hole. The larger hole on the top allows for a socket to pass through for easy attachment. I chose to use a bi-metal hole saw to cut this larger diameter hole.
The backbone of the rack are six 2"x4" 11 gauge rectangular tube. Getting the bases welded onto these uprights properly is critical. There will be huge amounts of forces applied to these and poor welds will result in failure of the system.Use some scrap pieces to do a couple test welds to be sure you have your welder dialed in properly. Check your test pieces for proper penetration before proceeding. It may have been overkill, but I chose to weld all four edges to maximize the weld area. Create a jig so that you can easily repeat the process for each upright.
Attachments
Step 2: Cantilever Arms
So this step proved to be a bit tricky. To maximize weld area of the cantilever arms these were installed so they lapped on the edge of the upright. This meant that there were eight full width welds all on one side of the upright which caused some warping. I tried several techniques to reduce this including shorter beads, alternating weld areas and post weld heating. None of these techniques made much of a difference in the warping.
What ended up working the best was pre-stressing the beam in the opposite direction of the weld contraction. This was done using multiple clamps and a spare 2x4 tube laid on its side. I used a scrap 1"x2" piece as a spacer between the two beams. This process worked really well and only had about 3/16" gap over the 10' uprights.
Step 3: Standing It Up and Connecting Together
So now that the main support pieces are done it is time to stand it all up and start connecting pieces. Start by clearing the area and laying out where all the pieces will go. Use a chalk line to mark the center of the rack. From there measure over from the center line and mark the front and back edges. Stand up the first upright and mark where the holes need to be drilled in the floor. Shift the upright out of the way and drill a 3/8" hole using a masonry bit and hammer drill. Using a full size hammer drill will speed up your process. The floor in our shop is 6,000 PSI concrete which makes it especially hard to drill through with a cordless hammer drill.
The anchors I used were Trubolts made by ITW RedHead. These particular anchors are easy to install and are incredibly strong. When installed in 6,000PSI concrete the 3/8 Trubolt can hold over 2,800 lbs in tension. Here is a link to test data for the trubolt line of anchors: link. Trubolts are easy to install, but once set with a hammer they don't come out. Be sure they are going where you want them otherwise you will have to cut them out using an angle grinder.
Once the holes are drilled use a vacuum or compressed air to clear out the dust left in the hole. If there is dust left in the hole this could prevent the anchor from going in all the way. Drop in the anchor and set by hitting the top with a hammer. This drives the collar on the bottom of the bolt outwards and wedges it into the hole. Place the upright over the anchors and bolt down. Proceed to the next upright and re[eat the process. Be sure the spacing is right, once the anchors are in it is not easy to change.
Once all the uprights are up install the frame pieces that tie everything together. I ran into a couple complications with the bottom support being slightly warped. I used a pair of pneumatic cylinders to push apart the base to allow the bottom frame to slide in. Work through the main structure clamping and spreading where necessary till the main structure is complete.
Proceed to installing the floating paint shelves. Each shelf frame was welded ahead of time and then installed one by one. Get the bottom shelf installed and leveled. From there work your way up. Once you get the bottom shelf leveled use wooden spacers to support each corner and weld in place.
Before you proceed to the next step go through and check that all joints have been welded. This will be your last chance to easily access all of the joints.
Step 4: Decking and Rollers
Now that the frame is complete it is time to start decking the shelving. Using 3/4 ply cut the appropriate sizes and install. You can use self tapping screws or standard drywall screws. If you choose to use drywall screws you must pre-drill through the steel using a 1/8" drill bit. This method works especially well on 16 ga steel and is a bit more difficult on thicker gauges, but is an easy way to save on cost of fasteners.
Once the shelves and base are decked with plywood rip down some 2x material to 4" and install across the base in between the uprights. This will provide more support for the plywood and prevent items from getting lost underneath the rack. This also provides a really clean look to the rack overall.
Next move on to installing the conveyor rollers. These rollers will make moving the steel into place to cut with the saw much easier. To compensate for uneven floors or other inconsistencies some adjust-ability was designed into the rollers.
Measure out where the conveyor needs support and drill a 3/8" hole and insert a bolt. The bolts are 1-1/2" x 3/8" each with two hex nuts (see pictures for detail). The conveyor frame should be captured between the two hex nuts. Install the conveyor rollers bold side down so that the bolts are supporting the frames. Weld bolts into place (wear a P100 respirator when welding plated metal such as bolts to avoid inhaling zinc particles).
Step 5: Finishing Up
All that should be left at this point should be filling the shelves and installing the saw. Be sure to anchor the cold saw to the ground so that it doesn't move while you are using it. Once your cold saw is in place level your rollers using the hex nuts. It is important that the conveyor rollers are level so that your cuts are nice and straight.
Overall I have been very happy with this rack. It provides ample storage for steel stock up to 24' and is easily accessible which speeds up cut listing. This rack also provided almost double the storage for the paint area compared to what it had before. The one downside is the lack of lighting around the cold saw. The cantilever arms hang out over the saw and partially block the light. This is an easy fix with some local lighting hanging above the saw, but is worth mentioning.
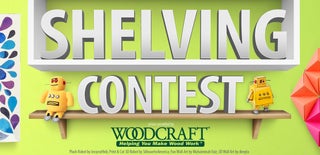
Participated in the
Shelving Contest