Introduction: TWO BOXES: ONE BIG & ONE BIGGER
INTRODUCTION
When I built the first box during late Spring of this year, I became addicted and decide to build one more – and, it is finished today, Thursday 05.09.2017. Beside my joy and fun during working with wood, there was a necessity to build both of them:
A) The first was TREASURE-CHEST (or pirate's chest) that I built for my step-grandson – to have nice and “safe” place for presents that he would get on celebration of his baptising;
B) The second was TOOL-BOX (realisation of old plan to make a combination of seating bench and box for big garden-tools), with a place at the veranda of our garden-cabin;
--- ---
From early childhood, I like to work with wood because of its qualities, but nice smell too. Mostly, I made simpler and smaller things, made for play with my brother, or housework for school. Of course, we enjoy to “help” our father when he was building some shelves for various uses, install at various places of our small flat. Later, in bigger flat, father's ambitions became bigger and he built all the possible boxes and shelves, for us and the rest of family. Finally, he built 3 big closets (cabinets) and a pair of beds for my room. As I was older in that period, I really help him and enjoy in all that. Besides helping him, I learned a lot about imagination transferred to plans, making simple sketches, work with wood and simple tools, painting and so on, but mostly about persistence, patience and acceptability of making mistakes and correcting them. My father had simple and cheap tools: one hand-saw (with contra positioned tooth, as Japanese saw), hammer, grater (plan), screwdriver, rasp, three small gimlets from boy's set of tools... Neither one electric-powered tool nor some specific tools. No great knowledge or experience, except love for wood-work, shared by both of us. (older brother turned to machines, mechanisms, engines, cars and motorcycles).
Work on both of shown projects is the result of mentioned above and belong to a group of smaller woodworking projects that I made until now. A few of them were quite big, but about them maybe in some other Inscrutable(s)... --- ---
Sorry for all printing, stylish and linguistic mistakes and wrong use of terms: The English language is not my native language – I was born in Belgrade, Serbia and lived there until 7 years ago when I moved here to Bern, Swiss. Probably that I missed something to mention and that I wrote something twice and sometimes I was not so clear. In spite of all that, I hope that this Inscrutable is understandable and useful. Conversion of centimetres to inches is rounded at all places where they are written and there could be some mistakes.
--- ---
It looks that making proper Instructable is a job serious as building boxes.
SHORT NOTES:
Just a few general notes about used technology (humble advice, tips):
- After sketching in mind and at a paper, next step would be to find proper wood for construction: nice looking, not too much expensive, easy to work with it with tools that we have, and that gives a strong and durable construction, not very heavy.
- Comparing prices, types and sizes of wood and so on – we should make the best compromise/balance (final sketch), in accordance with our conditions, possibilities, goals and wishes. During the process, something would be changed, some new problems would appear and most of that could be solved.
- Some of the tools used for cutting and shaping of metal could be used for wood too: saw for metal (for nice cuts of smaller wood strips) and rasp for metal (for fine smoothing of wood edges), sandpaper for metal (for smoothing of wider surfaces, by hand or on an electric tool). Of course, if you have that at hand, but special wood-tool isn't there.
- For painting: used brushes could be kept in pure water until next use, for a longer time, especially if we shall use similar paints/varnishes. No need for total cleaning them totally. Of course, for nice pieces of furniture, boats or aeroplanes, and so on – the best way is to buy good new brushes every time! Painting outside on fresh air but in a shadow is the best!
- Nailing: for start, I hammered nails in plates/boards so that they passed all thickness and show on another side for 1 mm (around ~ 0.04”) so that sides could be easily positioned. Then, I hammered nails to the end, the best is when a head of a nail is a little under surface – I didn't plan to pull-up them later.
- Good light, ventilation, heating or cooling are welcomed in closed space, or nice shadow and singing of birds at open space (garden in my case).
- Then, essential is to have some photo-camera for registration of process, but I forgot it sometime. Making notes and sketches during work is a good habit, especially if there are long pauses in process.
- Keep all the bills for bought material, for personal evidence, but for some other cases too.
Why build? Of course, most of the objects that we built or will build - could be bought in specialised shops or over the Internet, made with better quality and more precision, but... But, they are extremely expensive, comparing to material alone and our free work, and mostly we couldn't find exactly what we need or just want. And, the most important - we enjoy in building things by ourselves!
Step 1: A.1) TREASURE- CHEST - Introduction
From early childhood, I wanted to build a big box for my personal stuff – all very “valuable” things (toys, tools, books, drawings, letters, memorabilia and so on), but never started such project and probably through time I forgot it. I remember old days scenes with recruits go to Army when I was a child, mostly in early Autumn. All of them were carrying grey-green boxes, for their military stuff and personal things to be kept beside their beds in military barracks – no metal lockers as later appeared. I always wanted to have one, but no chances for that: when soldiers left Army and went home – they left their chests in army barracks and a new generation of recruits crashed them and use for heating during Winter (old-age recycling and ecology?)...
Besides such boxes, I was always impressed with classic coffers (suitcases), used on railway or steam-ship voyages of rich people. (from old, classic films, or from films with scenes from vintage era)
Therefore, as I didn't build one for myself, I decided to build one for my step-grandson, and that was accepted with joy by his parents (he didn't know that yet, being 15 months old). The only dilemma was what style to choose: treasure (pirate) chest or coffer for voyages (steam line luggage ). Coffer was the first option, because of style and fact that in my born-town Belgrade there were a few shops where could be bought everything necessary: good artificial leather, all metal parts (mostly brass or "messing" as we call it) and so on. However, when we were at Spring-holiday in Belgrade, I found that both shops were closed for good. Finished Chinese products were cheaper than anything that could be built at a workshop or even at home!
So, the only choice was a treasure chest, with material and parts bought in Bern, where we live! Just to find proper wood and nice metal, anodised to look as brass. The dilemma was a shape: with rounded or flat top/cover? Rounded is more elegant, but flat is simpler so I choose that!
Step 2: A.2) TREASURE-CHEST - Tools & Equipment
Working in the basement of the building where we live, it was a lot easier and more comfortable than later in the garden. Here I have small an modest workshop, but with enough of tools, including a few electric-powered. Most of the tools are shown at attached photos, with some explanations.
Having 66 years and even older backbone, I prefer to work while seating in a good chair and having an object of work at a table, with some tools that could fix it: metal squeezer fixed to a workbench and many clamps of all kinds and sizes. Of course, good carpenter table with carpenter bee should be better, but there is no place for it.
Step 3: A.3) TREASURE-CHEST – Material
I search a lot for the most practical parts and especially wood as a material!
- Finally I bought 4 boards, lightly impregnated (that isn't necessary for this project, but look nice), very well finished. Dimensions: long 200 cm, wide 14 cm, thick 1.8 cm (around ~ 78.7” x 5.5” x 0.7”) . Maybe too big, heavy and strong for this project, but a work with them is simpler. They were used for the entire construction of the box, including the cover.
- Then, I had a big pile of plywood lattes, various dimensions, from two old, abounded beds left on the nearby street. For this project, I choose a few, with dimensions: long 90 cm wide 4.5 cm, thick 0.9 cm (around ~ 35.4” x 1.8” x 0.35”). I used them for covering of all of the Treasure-Box's edges, more for esthetical then constructional reasons.
- In the workshop, I found plywood from some old wooden box: long 60 cm, wide 43 cm, thick 9 mm (around ~ 23.6” x 16.9” x 0.35”) – excellent for the bottom of the box (right size and good quality, painted white).
- For fixing: screws for wood 4 X 4.5 mm (for boards) and 4.5 x 20 mm for plywood lattes, then tiny nails 1.75 x 40 mm (for preliminary fixing).
- For decoration, two kinds of small nails with decorative heads.
- A lot of metal parts, constructional or decorative.
(all of that, shown at attached photos)
Not any glue was used.
Step 4: A.4) TREASURE-CHEST - Construction
Unfortunately, all photos with various stages of construction – were simply lost in the virtual university. Maybe they still could be found somewhere in memory of my computer – but not now? However, I hope that with my description of the process, with some sketches and photos of finished Treasure-Chest (with my notes) – it wouldn't be complicated to understand the what and how I was doing.
Having in mind planned use of Treasure-Chest, the same as calculations of necessary wooden material, I made general dimensions of Treasure-Box. The result was: long 60 cm, wide around 44 cm and high around 44 cm (around ~ 23.6” x 17.3” x 17.3”), including cover and plywood at the bottom, but without later added “legs”. Final dimensions were something different, just for a few mm - consequence of a cutting of material.
Preparation job:
- I cut all boards on planned dimensions: 9 pieces of boards long 60 cm:
- for the box: 2 for the front side, and 2 for the rear side;
- for cover: 1 for the front and 1 for the rear side, and 3 for the top;
- In the same time, I cut 6 pieces of boards long 40 cm:
- for the box: 2 for the right side, 2 for the left side;
- for cover: 1 for the ront and 1 for the rear side).
- Length of all boards is shorter for 1-2 mm because of cutting.
- I used table circular for that so the final result was good: clear cuts and all at a good right angle of 90°.
- Maybe some ½ hour was used, including smoothing of all rough edges.
The first step:
- I constructed the “first floor”: to make a rectangle of two long boards (60 cm) and two short boards (40 cm) put between long boards.
- For preliminary fixing, I used tiny nails, as an easier way for fixing, working single-handed (alone) and without long clamps. Also, some correction could be easily done.
- On that rectangle, putting it upside-down, I nailed plywood as the bottom. In spite that it had good right angles of 90°, I check that again before hammering nails.
The second step:
- I cut and fixed wooden battens for corners, that are “higher” for 3-4 cm than planned height of box's sides (two boards, one at another). It could be of any adequate cross section dimension, and I used what I already had: battens from the mentioned old bed.
- I screwed battens to the boards of the “first floor”. So, they become a pattern for the “second floor” - a rectangle of 4 boards, two long (one at the front and one at the rear side) and two short (one for the left and one for the right side).
- After re-checking all corners (if they are at a good right angle of 90°) - I used 2 screws for each board to fix it to battens at inside corners and also to fix plywood (bottom) to boards. Nails were left at the place, with heads a little under surface of boards, the same as screws were a little dig-in with heads. (strong metal clamps were used during process)
The third step:
- I started construction of cover. Having battens at inside corners higher for 3-4 cm than all sides of the box, I clamped vertical boards to them, 2 long (one for the front and one the rear side) and 2 short between them (one for the left and one for the right side).
- Then, I nailed 3 boards (long 60 cm) at the top, that secured good right angles for entire cover. I nailed vertical boards to each other.
- As everything was looking good, I fix everything with screws: vertical sides to each other and horizontal (top) to side-boards of cover.
The fourth step:
- I fixed hinges, using a few short screws and one bolt for each part of each hinge.
- Before that, I pulled cover up and left on a side. I have to rounded the front edges of battens at inside corners and harrowed them at sides, so the cover could be opened and closed easily, but still be kept at a place when closed.
Finally:
- I fixed all metal parts that are shown in photos.
- I had some old, but still good leather belts for pants, so I cut them at a size and nailed to cover – just for style!
- At all edges of Treasure-Chest were screwed plywood lattes, using shorter screws – no need for constructional strength, they are just for a style.
- At the rear side of the Treasure-Chest, I fixed small box used for complete of bottles with various beers, known as "halbmeterbierkasten" (half-a-meter beer-box) - to be used for smaller but valuable presents: envelopes with money and so on. It has a movable top for an opening to the right side when the cover is open.
Step 5: A.5) TREASURE-CHEST – Painting
As for the construction, there were not any photo of process – lost in the same way. But, results are visible on photos that show finished Treasure-Chest.
- For plywood lattes, I used brown paint bought just for this project (after finishing construction of Treasure-Chest).
- I used old lacquer for the entire Treasure-Chest, over boards, plywood strips, metal parts and leather belts... It was once clear but through years it became honey-yellow. As it is nitro-based (probably not in use now anymore), it dried in 15-20 minutes, so I painted Treasure-Chest twice – without sending between.
- Plywood at the bottom was lightly painted with wait paint, but I re-painted it at both sides with white paint from a spray-can.
Step 6: A.6) TREASURE-CHEST - Finishing
Finalising is visible at attached photos. Treasure-Chest appeared bigger, stronger and heavier than it was necessary, but for sure it could serve its purpose for many years.
After finishing everything, including painting, I install 2 pneumatic "amortisseurs" (buffers) for keeping the cover in open position. I suppose that one would be enough, but I install 2, one for each side (left and right). That was for safety reasons – cover is quite heavy, but now when it is opened – it stays like that and children could not pull it easily and injure themselves.
That was one of the most complicated work and I spent the entire afternoon fixing buffers. There was some help of scheme attached when I bought them, but I must check and re-check good position a few times, changing position of screws. Buffers must be fully pull-out when the cover is opened and fully pulled in when the cover is closed... The final result was good in spite that I couldn't be inside of the Treasure-Chest when the cover is closed and didn't have small TV-camera inside - to spy system!
In the same part of finalising process, I fixed “legs” as are shown at photos with additional plastic/metal “nuts” for easier pulling over a floor. They were painted with mentioned brown paint.
Step 7: A.7) TREASURE-CHEST – Use
It wasn't easy to bring it from basement to parking in-front of our building, as it is quite big and heavy. Also, problem was to put it in our small car – Citroen C-1.
It was accepted very well at baptising ceremony and soon it was full of presents.
Later, I transported it to kid's parents home (fourth floor, without elevator).
(But all that was manageable)
After a few days, kid's father removed “legs” and fixed 4 wheels with brakes – for easier moving around over parquet. It became even heavier, being full of children books.
Step 8: B.1) TOOL-BOX – Introduction
As was said, I needed one more bench for seating under the roof of garden-house's veranda, to be used when there is rain, or it is too cold or windy to seat out, during grill-parties with family members or friends, or neighbours. Also, I needed a bigger box to keep big garden-tools and gasoline powered grass-trimmer, a can of gasoline and so on... I had I space beside West-side of a veranda, long up to 160 cm ~ 63” - and, that was a length necessary for tools! So, I decided that dimensions should be around 160 cm long, 40 cm wide and 40 cm high (around ~ 63” x 16” x 16”) or something near that, depending on the avialiable material and precise plans.
Next goal was that general construction and especially upper plate/cover should be strong enough for seating up to three persons (our friends are quite heavy). Then, the box should be water-resistant, in spite that veranda is well constructed and protected from rain, but not quite water-closed and moisture-free during rainy and wet days. Finally, it must look decent, if not necessarily elegant. The shape should be simple, but not rude and finish must be good – looking from the 2-meter distance. Some nice pillows for seats and backrest would improve an image.
Step 9: B.2) TOOL-BOX - Tools and Equipment
Working in our garden without electricity, restricted use of proper tools, but in the same time that was a challenge to find and develop an adequate technology of work. It is important especially when somebody, as myself, works alone – without a help of “the third hand”. This Tool-Box for big garden tools is a relatively simple project, but an object is BIG!
After I choose material that will be the most practical for this project, I bought it and transported by our small car Citroen C1, at parking place some 150 meters away from the garden. From there, I pulled all that uphill along a narrow alley, up to grass-field in front of our garden house. Problem was that at the same time I bought and transported more wood material necessary for the next project. Therefore, I had a few goings up-and-down along an alley. Enough for the first day.
For "local transport", I used my old faithful “assistant” - small but strong warehouse trolley. As temporary but good workbench, I had ready 2 wooden A-type stands and universal metal ladders - and conformable plastic chair when I could work seating. All that was used a lot and paid itself a few times during past few years during building garden-cabin.
Besides cordless screwdriver/drill with 2 not-so-good batteries (tired of building entire garden-cabin), there were enough of hand-tools and clamps! (no electricity in garden)
(photos attached)
Step 10: B.3) TOOL-BOX – Material
As was shown at attached photos, I prepared:
- I bought: 4 laminated wood plates: long 200 cm, wide 40 cm, thick 1.8 cm (around ~ 79” x 16” x 0.7”); these plates are of good quality, with nice finish, and easy for work – but they are not good for vertical pressure when horizontally positioned (more about that in part about construction) and they are not water resistant (more about that in part about painting); they were really good for planned dimensions of Tool-Box: shortening them at proper length, I would get 4 pieces: 4 longer (2 for front and rear sides, 2 for bottom and cover), then 2 shorter (for left and right side) and 2 for some other use;
- I bought: 4 wooden battens (not all of them were necessary for this project, but they were cheap): long 200 cm, wide 4.8 cm, thick 2.4 cm (around ~ 79” x less than 2” x less than 1”) - good for horizontal reinforcement of vertical sides (front and rear) and lower reinforcement of upper plate/cover);
- I bought: 5 small girders (not all of them were necessary for this project, but they were cheap): long 100 cm, wide 5.5 cm, thick 4.0 cm (around ~ 40” x more than 2” x 1.6”) - good for reinforcement of box at inside corners and for “legs” under box;
- I found on street: 12 wood boards from old bed: long 139 cm, wide 7 cm, thick 1.9 cm (around ~ 54.7” x 2.7” x 0.74”) - good for back-rest when box is used as seating bench;
- I found on street: 2 of many plywood strips from old bed: long 90 cm, wide 6 cm, thick 9 mm (around ~ 35.5” x 2.4” x 0.35”) - good for upper reinforcement of upper plate/cover;
- I bought: screws for wood 4.0 mm x 45 mm (200 pieces in a box), then machine-bolts for hinges M5 x 30mm (10 pieces, I must buy 2 more!), tinny nails 1.75 mm x 40 mm (80 pieces in a box);
- rest from another project: paints and varnishes (details in part about painting)
So - everything was ready to start a construction!
Step 11: B.4) TOOL-BOX – Construction
For the start - I finalised simple sketch to make a basic box, with something corrected dimensions: long 164 cm, wide 43.6 cm, high 42 cm (around ~ 64.6” x 17.2” x 16.5”) - outside dimensions, height is without later added “legs” . That was enough for garden tools and could be placed between shelf and veranda's wall.
The first working day:
The first step:
- I was cutting all of 4 laminated wood plates in two parts: getting 4 parts of 164 cm and 4 parts of 36 cm:
- long parts are for the front and the rear side, then for the bottom and the upper plate/cover;
- short parts are for the left and right sides (2 of them) and for some other use (2 of them);
- Then I cut girders for reinforcement at corners at a dimension of 36 cm (around ~ 14.2”) that is an internal height of the box.
- All cutting was done in something more than ½ an hour, with cheap hand-saw. It could be good for this and maybe for one more project working with good wood, but not for OSB plates and so on. I bought that complete of saw's blades with one handle – for 6 Swiss Franks and a few of good saws with such variations should cost around 100 Swiss Franks (100 Swiss Franks ~ 100 USA$$$).
- Some humble advice when cutting wood with hand-saw: use good support and some clamps, as on shown photos, working relaxed: small angle between wood and saw, long and slow movements, without too much pressure. Good results, not too much energy used, in an acceptable time (we have that?).
- Just after cutting plates and girders, I cleared rough edges: first with hand-rasp for wood and then with a fine rasp for metal – good results.
The second step:
- After short rest, I start assembling the box. For working bench, I used mentioned universal ladders and a plate planned for the cover of the box! For the start, I fixed girders at shorter plates (left and rear), with mentioned tiny nails. Easy to work and mistakes could be easily corrected. Such side-plates could easily support the front plate in vertical position and later the rear plate, making half of a box.
- I mentioned that I worked alone and there is not “the third-hand help", holding alone all parts during assembly. Clamps were used whenever it is necessary and possible. The most important is to think in advance.
The box was assembled with nails and upper plate/cover was positioned, but not fixed. I spent around 2 hours on this entire operation, plus some time for preparation, maybe ½ of an hour before the start.
The second working day:
I was operating under the roof of the veranda because there were some wind outside and possible rain.
- The most problem was to bring Tool-Box inside: I used a technique of ancient Egyptians: tumbling Tool-Box over a grass like a brick and then through doors and on the table, covered by a protective plastic fabric.
- There, I fixed all joints with screws for wood, dimensions 4.0X45 mm – the more the better! Nails stayed! Problem was that not all the screws are quite the same, so often I had to change small parts for a cordless screwdriver. Sorry, I do not know their name, neither on English nor Serbian or German language – but they are shown at photos with all other tools. (no photos of this work – forgot to shot them!)
- Hinges were preliminary fixed with screws for wood and opening-closing of the cover was good.
The third working day:
I was on a grass again! Sunny calm day. (there were a few rainy days – no work at all). Transport of the Tool-Box was in the same Egyptian way!
- I levelled wooden batten what was the front support for upper plate/cover, using a few tools, shown at photos.
- Then, I replaced preliminary screws for wood that fixed hinges – with proper machine bolts M5X40mm (need to buy two more). Also, I lost one nut – hardly to find it in a grass. Good that it isn't sharp and couldn't harm (I worked barefoot – nice feeling).
- After that, I fixed support for upper plate/cover (mentioned plywood strips) and support from inside (wooden battens 4.8mm x 2.4 mm). Both of supports are fixed by screws from below and from above, through all 3 parts. The laminated plate shouldn't be strong enough to support a weight of 2-3 guests.
- Having time before dark, I made small inside box for smaller garden tools, with an additional role to protect gasoline trimmer. It is screwed to all plates on all sides, more to reinforced entire Tool-Box and support upper plate/cover, than because of itself.
A few days later:
Smaller works were finished before the Tool-Box was ready for painting. I didn't move Tool-Box to veranda again – simply left it on metal ladders and covered it by plastic protection cover, fixed with clamps.
Before painting, I fixed wooden “legs” under the bottom, to reinforce it and to keep it off the floor! Screws go from both sides: from above and from below! Later I added 4 metal/plastic “nuts”, 2 for each “leg”, but using longer screws for wood than the original I got in complete. This is another protection from water on veranda's stone-plates and for easier pulling here-and-there if that is needed.
Step 12: B.5) TOOL-BOX - Painting
As I said: laminated plates are not water-resistant, so I must protect them well, in spite that at veranda there couldn't be water, but moisture maybe and who knows...
- Except for front plate and upper plate/cover, I used a strange mixture of liquid tar (bought for the next project), old linen varnish bought once in Belgrade, planned for small boat started a couple of years ago and a little of oil-based yellow paint – to add style! I painted Tool-Box both outside and inside!
- For outside of the front plate and upper plate/cover, I used old lacquer that is water-resistant and on nitro-base (made for boats and bought for my old project). In spite that it is almost 10 years old, it was still good, but not quite clear as before – more as good honey! My wife prefers it than almost black painted all other sides and inside of Tool-Box.
- Wooden "legs" are paintted with tar-mixcure, very rich for water-resistance.
Yello paint dried quickly being nitro-based, but black was wet a couple of days.
Step 13: B.6) TOOL-BOX - Finished
When I finished painting, I transported Tool-Box to veranda again and finally – using the same Egyptian way!
- There, I finished small details – I needed more time than for big operations - and process was more boring!
- Before that, I cut in half mentioned boards from old bed and fixed them to veranda's wall with screws for wood - to serve as back-rest of bench.
- Then, I fixed locker mechanism, could be seen well on attached photos. Good thing is that screws are not visible when upper plate/cover is locked, so not easy way to brake-in (had such experience a few years ago - I lost almost all of my tools for work.
- I use simple “mechanism” to keep upper plate/cover opened: red plastic rope hanged at hook at veranda's wall!
- During those two days, I managed to drill the hole for ventilation in a shape of a heart! My wife likes that and I made that at a few places of our garden cabin. Red painting around heart looks better in life, but there is some reflex from the blitz on photos.
Problems were with batteries for cordless screwdriver – I had to work two days and charged them between.
Tool-Box is fixed in planned space for a millimetre-two free on each side!
Step 14: B.7) TOOL-BOX - Use
Simply - first I put gasoline powered grass-trimmer to its place: long “leg” was dis-assembled in 2 pieces, but there is enough of place to keep it in full size. Then I put in all big garden tools - had to cut the handle of rakes for 10 cm ~ 4”. The small inside box has a lot of place for smaller garden tools. there is a place for plastic gasoline can, too.
So, now it is in full function and I am satisfied with my work and final result! (photos attached)
Step 15: CONCLUSION, Both for Treasure-Chest and for Tool-Box
This instructable is written for similar persons in similar situations and conditions as I am, especially without computer design, CNC machines, laser or water-jet cutting, 3D printing and so on... That was especially the situation with work on the Tool-Box (working place was in garden – no electricity).
I decided to put both projects in one instructable for BOX CONTEST, as it seems more practical for me and more useful for interested home-builders, lovers of the woodwork...
However, for home-built experts in woodworking, with great knowledge and experience, excellent workshops and tools – both of my projects and entire Inscrutable could be boring and not useful, but here it is...
In both projects I enjoy a lot, from thinking, planning, sketching, buying material, constructing boxes, finalising them... I am satisfied with the final results, but of course, some things could be made better, with more precision, and better finish, or in a different way. The same, everybody could make such boxes in a different way, using different style and size, different materials and technology of work - in accordance to own conditions, circumstances and possibilities - goals and wishes, too. If my projects serve as an inspiration to somebody - I would be satisfied!
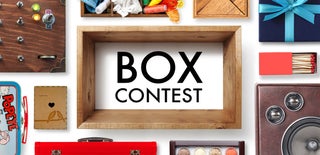
Participated in the
Box Contest 2017