Introduction: The Boominator: 360° of 115dB Music
Hi there and welcome to the Boominator Buildlog.
This is the pinnacle of boomboxes that me and my friend have been working on for the last couple of months. Many days were spend building this beast. What makes it so great you may ask. Well, multiple things:
- Capable of doing 115 dB at 1 meter
- Capable of sustaining full output for at least 20 hours.
- 360 degrees of sound
- Excellent bass performance outdoors
- LED strips around the woofers perimeter that flash on the beat
- And many more small things
Building it was almost as fun as seeing and hearing the final product :)
Before we begin the buildlog I want to thank:
-AccuSafe for supplying most of the parts and having awesome customer service
-User Saturnus for doing the audio engineering behind the design
I'll be referencing to pictures with [..]
Step 1: Preparation
Beginning a DIY build without proper preperation is a recipe for disaster. So that's where we start.
In the first picture you can see our cardboard mockup which we used to get a feel of its size and form factor. It measures 90x30x30 (triple cube, 81 liters). Pretty big, but small considering the performance. Essentially its a portable PA setup. The sketchup drawing of the design can be found here: https://3dwarehouse.sketchup.com/model.html?id=ed70429792f0ff9d421ffb972735edc
After placing our online orders we went to the local hardware store to get our 12mm 9ply birch plywood cut [2]. Man that stuff is strong.
A couple of weeks later our orders arrived. The 4 10" P.audio woofers [3+4], battery, PSU, amplifier and battery protection [5], and some general cable stuff.
Step 2: Start of Construction
From cardboard to wood. You can definitely see it getting shape now. The Boominator drivers are mounted back to back (bipole), with the magnet against the centre brace. This makes the construction very sturdy. To reduce weight, connect the two chambers and increase total chamber volume the centre brace needs to have holes in it [2] and a cutout for the handle on the side.
The handle doubles as a bassreflex port (the other way around really ;p) so it needs to have a specific size [4], otherwise it'll mess up the tuning. We cut out it using a jigsaw [5]. In picture 6 you see us rounding over the exits to reduce port noise and to get a softer grip.
Then we glued and screwed the side piece and centre brace to the baseplate [7] and repeated it for the other side [8].
Step 3: Circles, Holes and Rounds
The router was our best friend at this step. It's very difficult and tiresome to make (good) circles with a jigsaw.
Drawing it out [1], using the router with our DIY circle jig [2], testfitting the woofer and wood with a grill sandwiched inbetween [4].
Time for another mockup [5]. As you can see, this thing is a beast.
In the last two pictures we're trying out our LED strips.
Step 4: Testing and Mounting
We hooked up the woofers to see if they all worked. Once they're mounted they should last a lifetime. The upside of such a strong construction is that they probably won't be damaged. The downside is that if we manage to get them damaged, swapping it out is next to impossible.
The next picture is of our piezo tweeters. Huh, piezo tweeters? Aren't those that horrible type that sound like plastic? Yup, if you don't know how to use them they are. We filled up the grooves with sealant to prevent resonance [2]. Because piezos are capacitive elements we can use a simple resistor to create a first order RC highpass as crossover; cutting of the first 'plasticy' peak and reducing the power consumption by a small bit. Their natural response is 3.5kHz and up, which is where our woofers start to drop their response. Perfect fit!
In picture 3 the woofer and tweeter are mounted with acrylic sealant, which is drying in picture 4.
Step 5: Prepping Electronics
While we left the speakers drying we grabbed the soldering iron to prep the electronics.
To save the speakers from unneccesary excursion at frequencies it can't really reproduce we modified the highpass on our high efficiency class-D MaxAmp20 by removing some of the input capacitors.
The amplifier is 90%+ efficient and can output 2x15W in 4 ohms. This doesn't seem like a lot, but this system is so efficient that it puts out 101 decibel with 1 watt at one meter. So if 1W is already very loud, imagine how loud 30W is ;p.
Then we, or my friend really, assembled the AccuSafe [3]. He never soldered a printed circuit board (PCB) before, but it turned out great. The AccuSafe is a PCB with a comparator circuit and a relay onboard that cuts off the power the the electronics at 11.5v to prevent battery damage. It also switches to PSU/charger when available.
The front of our electronics compartiment will be wrapped with carbon. We tested our wrapping skills on a test piece first [4] and then proceeded to our real front piece [5]. From top to bottom: off/led/on, volume knob, 3.5mm input, LED switch, cigarette socket.
The cigarette socket can be used for a USB charger, voltmeter to check battery status or of course a cigarette lighter.
Step 6: Assembly
Now we get to the biggest part: assembly. In picture 1 you can see why it's so strong. It can't flex along any axis.
The grey stuff on the speaker magnet in picture 2 is chemical metal. It is very strong, very stinky and very chemical. As you can see we already wired up the woofers to the tweeters. Later they will be wired in pairs to the terminals you see on picture 3.
Next thing you know: it's assembled. Now it's time to wire it up; the tape over the speaker is to prevent hot solder from dripping on the cone while soldering. The speakers need to be wired in phase: each speaker needs to move towards or away from the center at the same time.
Step 7: Painting and Electronics Compartiment Wiring
These steps need more pictures than words.
The LED strips still shine bright despite the slightly painted parts. We used Warnex/Duratex, a very durable type of structured paint that's often used with pro-audio gear.
After a bit of testfitting we wired everything up. We used multiple meters of wire ;p. The cutout on the right is to slide over the terminals. It worked out perfectly in the end. The backside with the 230v input, LED strip controller sensitivity knob and name plate on it sealed the compartiment off. It's jammed in there as you can see.
In the last pic we are testing it out, the module is behind it.
Step 8: The Final Product
Hope you enjoyed the buildlog. Please vote on our project for the DIYaudio2015 contest if you liked it.
If you have any questions/comments don't hesitate to ask
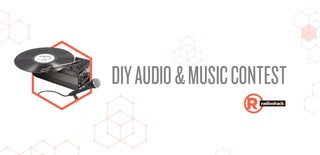
First Prize in the
DIY Audio and Music Contest