Introduction: Edward Scissorhands - Costume
October 31st is hands down my favorite day of the year. I'm not much of a sweets person, but I do enjoy becoming someone or something else by way of costume. I also really enjoy making costumes and props ... the design, the fabrication, all the challenges and troubleshooting that come up as things don't work out they way you planned ... it's like a adult puzzle for my brain.
Let's face it ... store bought costumes leave a lot to be desired. They are cheaply made and not even close to accurate. I desire accuracy! I don't want people to recognized me .. I want them to believe I am the character. I also really ... REALLY ... wanted to be Edward Scissorhands.
I mean ... aside from not being able to touch anybody, as well as the constant risk of mutilating and/or severing your own body parts ... Edward is awesome!
Step 1: A Few Failures
My initial idea was to fabricate the scissors out of sheet metal, but it was a failure. The sheet metal was difficult to shape into compound curves/angles, sharp metals edges, and lacked the bulk for which I was looking.
Second idea was laminated layers of acrylic/plexi, but it was a failure. Way too heavy and also difficult to cut and shape. A quality table saw blade will do it, but the bandsaw doesn't really like it ... I didn't even want to try router bits.
Then it occurred to me that I could use PVC sheet material, which is light and easy to work with tools. I just happened to have a small collection of off cuts from when the rake board and facia on my house were all replaced. There are several brands of PVC sheeting/trim boards, but I used 3/4" stock made by Azek, which doesn't have the textured finish.
Step 2: Cutting and Laminating the PVC Board
I cut the PVC to the required lengths using the miter saw and then ripped them to 1" using the tablesaw. This would make the lamination 1" x 1 1/2", which was too wide .. my fingers would be uncomfortably splayed and wouldn't look right. I trimmed the 3/4" dimension down to 1/2", which left me with a 1" x 1" blank.
For laminating, I used PVC adhesive and several clamps.
Why didn't I just make one cut at 1/2" and laminate top to bottom instead of side to side? Two reasons and you'll understand shortly.
Step 3: Layout and Shaping
For reference I used McFarlane's 7" Movie Maniac Figure, as well as several pictures of the Hot Toys 1/6 Scale Edward Scissorhands Movie Masterpieces figure. I scaled up all the measurements the best I could by comparing the McFarlane figure's forearm length to my own. It isn't 100% accurate, but I don't have access to the screen used prop(s).
The first step was to mill a channel into each scissor blank, which I did using a router table and a 3/4" straight bit. This is basically a deep stop dado, which I made in several passes. Since I needed the channel wider than 3/4" to accept my fingers/thumbs inside of a glove, I set the fence for the necessary offset and raised the bit with every pass until I reached my desired depth, adjusted the fence for a wider cut, and made a final pass. I didn't get pictures of that, but I assure you, it was thrilling.
Had I laminated the blanks top to bottom, I'd now have a glue line within the thinner sides of these channels, which wouldn't be ideal in terms of strength. Laminating side to side made more sense within the idea of blade fabrication and it also gave me the center line, which I used for laying out the shapes.
I mostly used the Hot Toys pictures for the shapes of the blades. Most of them are offset into one half, but one does a cool zig-zag thing and the thumbs are different as well. I had to take a few liberties with the shapes since Edward doesn't have real fingers concealed inside of his blades.
All of the blade shapes were cut out using the band saw. Blade chatter was removed and shapes finalized using the orbital belt sander, hand sanding, and a few files ... sorry again about missing pictures .. it was also thrilling. To get the look of sharpened edges, I used a chamfering bit on the router table.
Step 4: Glove Glueup
I figured this was a good time to spray paint a base coat of black. It helped me see any problem areas that needed more sanding.
I used epoxy to glue the gloves in place. If the gloves were any thinner, I'd find a different solution since the epoxy heats up as it cures and that can't be good for your bare skin. I don't think I'd trust superglue, but construction adhesive might work ... just takes longer to cure, so you'd have to fill the fingers with dowels or newspaper ... or sit there for hours if that tickles your fancy.
To close up these finger cavities, I used the off cuts from when I ripped the blanks to width. PVC adhesive and some clamps work great, just don't get sloppy because it will melt/warp the external surfaces of your shaped blades. Any overhanging edges were quickly flushed up and shaped with a file and sandpaper.
Step 5: Silver Base and Glove Concealment
At this time I decided to give everything a base coat of silver. If I make another set of these, I'll hold off on painting until later in the process because I just ended up scratching this finish and glue would probably stick better to the raw PVC in upcoming steps.
I needed a way to conceal the glove, as well as the transitions between the blades and the glove. My initial idea was again sheet metal, but it wasn't flexible enough and was hard to shape. I ended up using a stretch black material I found .. it might be lycra. I attached it to the edges of all the blades using hot glue, which worked surprisingly well. I also glued it down to the glove in various locations to keep it in relative place, but still let it move with my hand. The edges were wrapped around and glue to the palm of the glove.
Step 6: Scissor Handles
I used plywood for most of the handles because I thought it would add a different texture and liked the look of the plies around the edges. I had some trouble getting some of them glued to the PVC with epoxy ... they didn't like staying in place as it cured and clamping wasn't very easy. Because of this, I ended up getting epoxy on the silver finish, which can be see in the finished product because it took paint different than other areas of the PVC. Making the handles out of PVC stock would work just as well and you could use PVC adhesive for a quicker bond.
Then handle shapes were cut out on the band saw. And finger holes were created using the drill press and then shaped or elongated using the oscillating spindle sander. Exposed edges were rounded over at the router table and then all parts were sanded smooth.
I painted the handles with some left over craft paint because trying to mask and spray paint would've been a nightmare ... I knew I'd get over spray if I didn't tape everything off and I knew if I taped everything, it would most likely pull off paint. Silver was touched up after the handles dried.
To match the reference photos, I glued on various washers, bolt heads, and wing nuts. The right index finger actually has a bolt and lock nut so the scissors can be opened and closed. They can't be actively controlled, but the positioning can be changed.
Step 7: Attachment Straps
To attach his scissorhands to his body, the figure has a system of leather straps around the forearms, which are then connected to the hands with various rods and mechanisms.
For the leather straps, I used some belts which I found at Walmart on clearance for $2 each. I needed four, but I bought them all (8-10). They came with cheap metal pyramid stud things pressed into the leather, but there were easily removed. I cut the belts to my desired length using a utility knife and rounded the corners using the oscillating belt sander. A leather punch was used to make new holes as necessary. To keep the straps connected and at a consistent distance from each other, I used part of the cutoff belt and attached it with superglue.
These were then buckled shut with enough room to insert my arms. They don't actually strap tightly to my arms. The main attachment point is the gloves and everything else just sort of floats in its respective place.
Step 8: Rod Thingies
Fabrication of the connecting rods had me scratching my head for awhile. Initial material choices included wooden dowels, aluminum rod, and even glue sticks, but getting them to stay attached to the gloves and straps would be a challenge. Glue wouldn't hold long term and screws inside the gloves wouldn't be comfortable. I decided to browse the plumbing section of my local big box store and found my solution in the irrigation section ... sprinkler tubing ... easy to cut, superglue adheres well, and the goof plugs make perfect anchor points.
The longest control arm is just a length of 1/8" steel rod. On the leather strap end, it is glued into a section of the sprinkler tubing .. the tubing is secured to the strap with a goof plug. The goof plugs are functioning as posts ... kind of like a reverse button if you will. The larger flat section goes on the back side of the scraps or inside the glove, the post sticks through, and the sprinkler tube gets glued onto this post keeping everything secure [See the last picture for an example of the goof plug on the inside of the leather strap]. On the scissor handle end, the rod is bent 90 degrees, inserted through a hole drilled in the plywood, and capped by gluing on a small nut [See the second and third pictures].
To make the angled rods, I just cut the the tubing with a utility knife. Each end has a 45 degree joint ... easily cut with the aid of a speed square. Middle angles were just cut by laying two sections across each other at the necessary angle and cutting them at the same time ... not only did this make the joint perfect, it was easy to cut the exact length. To make the pipe more rigid, I inserted sections of 1/8" steel rod before adhering the joints with superglue.
Once all these rods were fabricated, there were finished with metal spray paint and then glued on to their respective goof plugs/posts.
Step 9: Costume Shots
Since I was wearing a full costume, I did need a few accessories.
1. A black wig, which I cut and made all grungy. Hairspray and gel wasn't working, so I used spray adhesive.
2. A white button down shirt.
3. Dress pants, which I already had.
4. Black thermal for an undershirt ... as opposed to an entire leather suit.
5. A pair of black suspenders. I cut each side in the front and stitched them back together with safety pins. Three pins on my right side ... two pins on my left side ... cut at different heights.
6. Edwards leather collar/turtleneck piece. I made this using the remaining three cutoffs from the belts. I glued them as a stack to a felt backer, created a fake buckle on each using a brass ring and nail, then added Velcro to each end.
I can put one hand on unassisted, but need help for the second ... the reverse is true for removal. Eating anything is near impossible, but I found a way to still drink beer... opening doors isn't going to happen ... you can imagine that going to the bathroom is totally impossible.
Edward was a hit with the neighborhood kids, as well as the adults. I couldn't hand out candy, so they just had to grab their own from the bowl.
Step 10: Glamour Shots
Some close pictures of the different sides of each hand. The first four pictures are of the left hand and the last four are of the right hand.
If I had to guess, I'd say I put at least 50 hours of time into the hands alone.
Step 11: Video
Technically, a slideshow ... I didn't record any video.
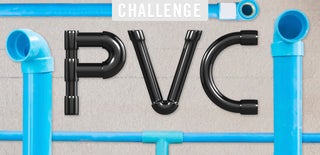
Runner Up in the
PVC Challenge
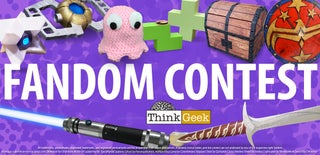
Participated in the
Fandom Contest