Introduction: The Spartan Spear and Shield End Table
If you're as hopeless as I am, you too spend a lot of time yelling at your favorite shows too. So when I saw that the survival ready contest was sponsored by The Walking Dead...well I thought it would be a good opportunity to get my two cents in and put together my favorite 'apocalypse' toolkit.
Now, how to be ready for when the zombies come? Well, besides unraveling a half dozen rolls of duct tape and cardboard to craft some zombie proof body armor, (which is extremely functional but not very imaginative or attractive) I thought, "you know what would be useful?...a shield...a shield and a SPEAR, hidden in a functional piece of furniture!". That's when the Spartan End Table was born.
The 'shield' is a solid piece of 1" thick pine, with a handhold on one side and an arm strap on the other to secure it firmly during combat, while the legs are crafted out of 1" solid maple dowel for strength and flexibility in spear form. The head of the spear is not sharpened (who wants a sharp knife under their table for the kids to find?), tho it is modestly pointed for ease in dispatching zombies as they attack, offering both reach and speed. Perfect for the zombie apocalypse.
This project incorporates, what I call, the trinity of craft; wood, leather, and metal, tho it isn't necessary to be very skilled in any of them. I've opted to complicate the project by adding details that can be easily omitted, as you see fit, limiting your tool needs to nothing more than a saw and a drill...tho making the point may be difficult without a welder. Still, there are ways around that as well and I encourage people to share their ideas if they decide to reproduce the table.
Step 1: Tools and Supplies
Tools;
- Table Saw
- Jigsaw
- bench or Belt Sander
- Router and Bits
- Drill and Bits
- Screwdrivers
- Angle Grinder with .45 Cut off Wheel and 1/4" grinding wheel
- Drill Press with Forstner bits
- mallet
- rivet set tool
- utility knife
- leather punch
Supplies;
- 12"x12"x1" Pine board
- 3 X 1" dowels 22" long each
- 3 X 1/4" threaded self tapping inserts 1/2" long
- 3 x 1/4" threaded self tapping inserts 1" long
- 1/4" hanger bolts (1/4" thread at one end and screw thread at the other)
- #8 3/4" wood screws
- Decorative washers
- 3/4" wide 10 oz leather strip, (approx 20" worth)
- Leather Snaps
- Cabinet handle (large enough for your hand to fit under)
- 3/4" buckle
- brass tacks
- Chromium tanned or veg tanned leather
- Wood Stain
- Polyurethane
Step 2: Shaping the Table Top
Making a square object round isn't terribly difficult, and there are more than a few ways to do it. My method is to cut off a section of board roughly the size of the table top you want, then find its center by crossing corner to corner. X marks the spot. Tap a nail in lightly, then measure a piece of string and tie a loop into it. Extend the string to half the diameter of the round table top you want, and make another loop that's large enough for your pencil to go through. Now, with tension on the string, draw your circle and use your jigsaw to rough out the shape. You can finish rounding by using a vertical disk sander and rotating the piece, being certain to keep to your lines.
Rounding The Edge;
This is one of those parts that isn't completely necessary, but it goes a long way towards aesthetics. I use a router mounted into a table which lets me manipulate the piece, rather than the machine. The first step is to select your router bit, keeping in mind you don't want it to be too dramatic looking. This was my second table top as I didn't like the outcome of the first one and wanted to re-route it. Use a bit with a bearing on it that will limit the depth of the cut, and keep it even. One trick I use is to support my piece on two sides, with a back guard and a side guard, allowing me to 'push' the piece into a corner and simply rotate it to make a smooth even bevel.
Step 3: Setting the Inserts for the Legs and Finishing the Top
Using the center, divide your disk into 6 equal parts. Again, pretty easy using PI multiplied by the diameter, then dividing by 6. That will give you the size of each slice. We'll only be using three legs, so that means there are two slices between each leg. Measure in roughly 1.5" from the edge, on each of the three lines and make a mark. These are the positions for the legs.
Next you'll want to angle the legs out a bit, for stability. Don't angle them to dramatically or it'll look odd, and people will trip over the legs. The angle I used was roughly 5-7 degrees. Honestly, I couldn't say for certain because I couldn't find my square, but that's my best reasonable guess and should be a safe bet. This is where the drill press comes in handy, as you can set the bed to the desired angle which will make it constant for all leg set points, as well as have a preset drill depth so that you don't penetrate the other side of the board.
Now you'll need to create the tapered angle for the legs to rest in. I didn't have an appropriate forstner bit, which would have been optimal, however using a standard spade bit worked just fine. Putting a piece of tape over the drill site will prevent splintering around the hole's edges. Finally I used an appropriate sized forstner bit to drill out the opening for the inserts to thread into. Be very careful as drilling too small will splinter the wood, while drilling too large will prevent the insert from biting and threading into the wood.
Thread your inserts into the board, using a bit of 5 min epoxy to prevent them from backing out.
When all is said and done, you can sand down your piece using progressively finer grits, then set it aside. You'll probably have to do the rounded edge by hand to prevent deformation of the corners.
Step 4: The Legs
My only gripe is that my lathe wasn't long enough to put any real decorations on the legs, so I ended up leaving them plain, which really didn't look too bad. The length of each leg is exactly 22".
Wrap a piece of tape around each end you intend on cutting to prevent splintering, and you can cut them all at the same time using a chop saw.
To set the 1" inserts into the ends, you'll need to drill, using the same forstner bit you used on the top piece, being very careful not to split the piece. Don't force them in, rather thread them half way, then extract them, allowing the fragments from the cutting to pour out of the hole. Again you can use some 5 min epoxy to set them into the shafts which will prevent it becoming a weak spot. I toyed with adding a brass ring to reinforce it, but after some testing, it didn't seem necessary as the joint was plenty strong.
Finally, you'll need to drill and and set the hanger bolts into the other end. Be very careful to drill straight as any minor deviation will translate to a drastically crooked bolt. I already ruined one leg by not setting it straight. The easiest way to set them is to use two nuts tightened against each other and wrench to twist them into place. Set them so that only 3/4" of the bolt is sticking out from the end of the leg. Again, an appropriately sized hole and a bit of epoxy will prevent the end from splitting.
Step 5: Final Sanding, Staining and Sealing
Now's the time to give your piece its final sanding before staining. Staining isn't necessary, but I think it goes a long way. When the stain dries, give a light sanding using 400 grit paper and you can either apply another coat, or finish off by sealing with polyurethane.
I apply my stain and poly using a sponge because it leaves a much smoother finish than a brush does. More than that, they're disposable and you don't waste as much money or time as you do with clean-up on a brush.
Drying time...
Step 6: The Spear Point Part I
The spear point is cut from a piece of 2" bar stock and incorporates a hex coupling nut so that it can be threaded onto the end of the spear quickly and easily. Fortunately for me, I have a friend that repairs telephone poles for a living and he gave me a few bars of "elecro-hardened" steel that I could use for various projects. As I understand it, they become brittle over time, and need to be replaced, making them perfect for my needs, as my forge is currently malfunctioning (I knocked it over and broke most of the bricks). The only thing necessary is to temper them which can be done in a standard oven, so I won't be including a hardening section to the instructable.Really tho...I don't think that hardening is even necessary as I didn't edge the point. It's a poking stick for zombies and will work just fine un-hardened.
Inserting The Nut;
I used the angle grinder with the .45 cutoff wheel to notch out the bar. As you can see, I sliced it out in sections, then used the 1/4" grinding wheel to finish the end. Then I inserted the nut, ensuring it was straight and welded it in place using a mig/flux welder. Using the grinding wheel, I began the shape the nut into the bar, re-welding and filling in gaps to ensure a smooth transition.
Step 7: The Spear Point Part II: Shaping
Roughing out was done using the angle grinder, into a general 'leaf' shape. I then ground down the edges, beveling them to a near edge. This was made a lot easier by threading a bolt into the end of the spear point giving me a place to hang onto as I worked.
The final shaping took place on the bench sanders using progressively finer grits. Now, I considered sanding it to a polish, but then I really didn't want to put that much work into it and left the point with course grinding marks. Actually, I think it adds to the look, tho who knows...I may return to it and sand it some more.
Step 8: Optional: the Padded Leather Top
I was working on a theme. This is a "Spartan" shield and so it needed some finishing touches to create that aesthetic. I really didn't want painted designs and thought leather top with brass tacks would look pretty cool. In retrospect, I would have loved to recessed the leather patch, but bordering in brass tacks gives it a much more bronze age appeal, I think.
To start, I cut a circle out of chromium tanned leather that was slightly smaller than the circumference of the top, and marked the same size into the top itself. As I had already polyurethaned the top, (the leather was sort of an afterthought) I used some course sandpaper to rough out the area and applied a liberal coat of leather glue. Next, I set the leather circle in place and compressed it under weight. When the glue was dry, I began adding the tacks.
Placing the tacks is a simple process made easier if your have a rivet setting tool. The problem with tacks is that they don't always go in perfectly straight, and even a millimeter difference can look off. The good news is that they can be shifted, even a few millimeters if you use the rivet setting tool and a mallet to 'push' them. If you don't have a rivet set, you can simply drill a dimple into a piece of bar stock to create one. It's really that easy.
Step 9: The Arm Brace and the Point Holster
Ok, so I reached this part of the project and realized I had run out of snaps for the point holster. I did, however, have a large iron cross shaped concho with an expanding post on the back which would act perfectly as the piece I was missing. Personally, I think it adds to the overall look and will probably keep it.
First I cut some 3/4" strips from a scrap piece of oiled and dyed 10 oz leather I had from another project. It was a bit thick for the buckle, so I used the skiver to thin the end a bit, then punched and cut the slot for the prong. As the leather was oiled, I opted to rivet rather than glue and stitch.
For the belt end, I punched evenly spaced holes, at 1" intervals and tapered the end. I wasn't concerned about length and figured I'd fine tune in the final fitting when it came time to mount them on the shield.
Finally, I set the snap into the last strip of leather, using the female end.
Now it's time to install all the pieces.
Step 10: Installing the Hardware
The first thing I installed was the handle. This is where I learned that I'd made a mistake that I need to clarify now; Make sure your hand grip is big enough to actually fit your hand... Mine was slightly too small for me, however it fit my wife's hand just fine. I may replace it in the future, but I decided to finish the project, as-is and revisit it later on.
Next I installed the arm strap, measuring it so that it fit around my arm comfortably when loosened, but still able to be hidden under the table when fully tightened. I used the 3/4" screws with the decorative washers to hold the straps in place.
Finally, I set the position for the point, using the 3/4" screw and decorative washer to fasten it. I then used a smaller #4 screw to set the 'male' end of the snap directly onto the shield so that when it was closed, it would hold the point firmly, and invisibly under the table.
Step 11: Finished
Now is the time to screw in the legs and assemble your Spartan table. With all of its hardware, it looks like nothing more than a simple piece of furniture, but in a matter of moments, it can be a formidable defensive and offensive tool for fighting off the zombie hordes.
As usual, I hope you enjoyed the instructable, and thanks for following.
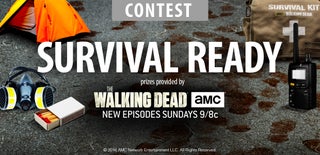
Third Prize in the
Survival Ready Contest
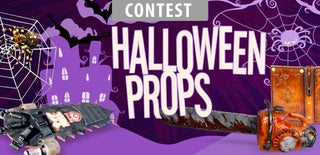
Participated in the
Halloween Props Contest 2016
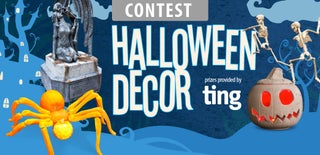
Participated in the
Halloween Decor Contest 2016