Introduction: Thor's Hammer - Mjölnir
This was one of those "I cannot really use this but wanted to try building one anyway" projects. There a lots of internet instructions on different ways to build Mjölnir with different materials. I even found numerous 3D printer files of different configurations. However, to 3D print the size I wanted, it would have taken me about two full spools of filament. So I decided a less expensive way which would take longer but let me customize it more would be to build it panel by panel. So I took some 0.2, 0.3 and 0.6 polystyrene sheets, PVC pipe, EVA foam, some 3D printed parts and my laser cutter and set to work.
Step 1:
I measured a 4.5 in by 8 in rectangle. I created an octagon with four sides measured at 4.5 to equal the dimension of the rectangle. I used my laser cutter to cut out each piece so it is exactly the same. I'm afraid my hand cutting techniques would result in some uneven edges so I prefer to use the laser.
Step 2: Putting Together the Base Structure
I 3D printed small brackets and glued them on to each side of the octagons. That allowed me to better glue the sides on and create the base structure.
Step 3: Being Patient
It took patience to put all the pieces together. It would have been 10 times more frustrating if I had cut the individual pieces by hand instead of using the laser. And while it would have taken less time to 3D print all of the pieces, it would have cost me about 10 times the amount as well.
Step 4: EVA and Dollar Store
I used some EVA foam and cheap foam from the local dollar store to line the inside of the base structure of the hammer. This gives it a more solid feeling without adding much weight.
Step 5: OK, What NOT to Do
I learned several very interesting things on this build. First I learned that it is more difficult than I expected to 3D print a scalable piece to fit exactly to something else you are doing by hand. I tried 3D printing the ends of the hammer only to find out they were too big. So, then I decided I would use the 3D printed end as a mold. However the 3D mold was printed at only 10% density so when I poured in the resin, it seeped into the holes, forever binding the resin to the inside of the mold. So, then I used the inside of the second half I 3D printed (should have only printed one half at a time and would then known it didn't fit) as a template to simply cut out and fit sections which would become the ends of the hammer.
Step 6: Laser Cut Out the Ends
After measuring the base again, I designed an SVG file with the individual pieces for the ends of the hammer. I used Corel Draw to create the pieces. This was easier to adjust for mistakes and did not take up a lot of filament (or cause me to wait hours while the 3D printer prints a piece) and I could tweak as necessary to get the right parts. After using the 3D printed end as a template, I hot glued the individual pieces to create the ends of the hammer.
Step 7: Putting on the Ends
Next I hot glued the ends to the hammer. I then took my rotary tool and sanded down all of the edges so everything is more flush.
Step 8: Handle
I contemplated various ways to create the handle (i.e. PVC only with paint, leather with straps, etc.). I finally decided on 3D printing individual handle guards and running PVC through the center. The PVC was not large enough in diameter so I hot glued some craft foam onto the handle, which made the individual pieces snug. The STL files with the individual handle pieces can be found on Thingiverse here.
Step 9: Paint the Handle Pieces
I then used some acrylic paint to alternate dark leather brown and silver.
Step 10: Periodic Measurements
It is a good idea to take periodic measurements and put the pieces together to make sure they are fitting properly.
Step 11: Second Skin
Putting individual panels together has a tenancy to show the seams of where you put the individual panels together. Thor's hammer has no such seams. I wanted to eliminate as many of them as I could. So, I measured out the width of the base part of the hammer (excluding the attached ends) and the length around the base. I cut a long 0.20 Polystyrene sheet. I hot glued one end to the under part of the base. Then, using a heat gun, heated each panel, stretching the polystyrene around the hammer, hot gluing along the way. It formed a second skin with no seams. Once cooled it formed around the hammer nicely. I then re-cut the top and bottom hold for the handle.
Step 12:
Next I needed the recessed sections of the hammer. My objection was to cut into the outer skin while heaving the inner skin intact to give the proper impression. I measured and laser cut a piece of 0.60 polystyrene with the recessed section cut out and used it as a template. I then used my rotary tool to cut through the outer skin. I then cut out some rectangle sections, and hot glued to the under part of the hammer.
Step 13: Symbols
On the long panels on the ends of the hammer are a bunch of squiggly symbols. I measured and laser cut out panels for each of the ends. I then used a hot glue gun and just drew squiggly marks similar to what I pulled from comics or production images. I then glued the panels onto the hammer. Technically, the panels in Thor's hammer with the symbols is recessed, not raised. But since I did not think about that when constructing the ends and did not want to have to redo everything, I just went with having the panel's raised.
Step 14: Topper
On the top of Thor's hammer is a circular topper. I laser cut out two identical circles then cut a hole in the bottom circle. When stacked on each other it creates a recessed section which will hold the PVC for the handle and prevent it from sliding off the hammer. Once the two circles are hot glued together, I glued the handle in place. It is important to get your measurements of the length of the handle correct since it has to be long enough to extend through the bottom and create the handle but not too long so that the 3D printed handle guards do not fit up against the hammer.
Step 15: Paint
OK, time to pain the hammer. I drilled a small hole in the tip of the handle (which will be covered up with a 3D printed piece anyway later), ran a wire through it and hung the hammer from a tree. I then primed then spray painted the hammer.
Step 16: Handle End
After creating the topper I needed to finish up the bottom end of the handle. This section contains a leather strap. The final 3D printed section which goes on the end of the handle has a section for the strap. I measured the width of the opening and cut some leather to the appropriate size. I fed it through the hole on both ends. With both ends of the leather sticking up through the 3D printed piece, I placed a rivet connecting the strap ends. The rivet will lay inside the 3D printed section so it is not visible. The pictures above show me measuring while the 3D piece is unpainted. This was to ensure proper measurements. Do not attach the rivet until after the 3D printed section is painted and dry.
Step 17: Affixing the Handle Sections
As mentioned earlier, to make sure the 3D printed handle pieces are snug, I cut then ran a piece of craft foam up the length of the handle. I then put the pieces on one at a time and hot glued them in place. Finally I glued the end piece with the leather strap onto the end of the PVC.
Step 18: Accent and Weathering
The symbols on the ends are weathered and accented to stand out. So I took some dark metal grey, watered it down and brushed it across the symbols. I then used a cloth and dabbed away the paint causing it to give a weathered look.
Technically, the hammer also has an engraved symbol as well as wording which I originally intended to include. However, I realized after cutting out the recessed section that trying to cut out the lettering work probably do more damage to the hammer than add to it. So I opted to forgo the wording and will try adding it a different way if I ever do a version 2.
Step 19: All Finished
An finally, it is done. I then created and painted gold a hanger and placed Mjolnir up on the wall next to Captain America's shield. [Note: some of you may notice from one or two pictures there is a dent or waved section from a certain angle. That was not part of the construction process. That was my testing to see if the topper was properly attached by giving the hammer a swing, only to discover it was not properly attached. The top flew off, the hammer flew across the yard and . ...well it now has a dent. But you cannot tell from where it its on the wall)
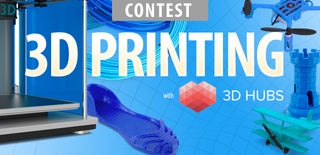
Participated in the
3D Printing Contest 2016