Introduction: Tinkercad Robotics for School: Create TWO Walking Machines!
Hello! My name is Mario. I'm a Maker and STEAM Educator, and THIS IS MY INSTRUCTABLE NUMBER 100! :-)
Thanks to all the people who, during all these years, have followed my projects, supported them, commented them and voted for them; and thanks to all the awesome team of Instructables and Autodesk for making this possible.
OK, let's celebrate with... 3D printing and robots!!!
One of the greatest satisfactions of my career as a professional maker and STEAM educator has been training in Tinkercad and 3D printing the first wave of public school teachers of Azerbaijan. At the beginning, they were full of doubts, not very sure if this knowledge was useful or if they would be able to design something by themselves.
Now, one year later, I see that most of them have become mentors, not only for their students, but also for other public school teachers! They exhibit with pride their own creations and the ones from their students; some of them have their own YouTube channels where they explain how to design cars, tanks, mice and fighter jets; and even I can see some of them leading the new training sessions for the next generation of public school teachers. Way to go, guys!
Ready to take your skills to the next level? Let's design walking robots with Tinkercad!
This project was executed in three stages:
- First, I created a physical prototype (Mark 1).
- After that, I designed a basic mechanical walker with one crank (Mark 2).
- After testing the previous design, I took its useful parts and created a more efficient design (Mark 3)
This project has the following constraints:
- Small Printing Area: my 3D printer is a Biqu Magician (small but faithful), and its printing area is only Φ100 x 150mm; so no piece of this project could exceed this area. This was an important limitation, considering I had to print the pieces at 105% scale, with a raft.
- Simplicity in design: the target is to teach design of a basic mechanism for a simple walking robot; so I wanted to keep the number and complexity of pieces at minimum. Also, the pieces may be reused or easily replaceable.
- Simplicity in materials: no screws, no nuts, no glue (with one little exception: traction). Except for the gearbox, the power source and one zip-tie, everything had to be 3D printed.
Students will require to have some prior knowledge of Tinkercad in intermediate level (workplane navigation, basic Boolean operations, group, ungroup, mirror and align, how to improve their own design).
Supplies
- 1 Computer with access to Tinkercad
- 1 3D printer. Material: PLA
- 1 Gearbox "I" shape (like this one)
- 1 Battery holder for 9V battery, with switch (like this one).
- 1 9V battery. NOTE: at the beginning, I worked with 2 AAA batteries and their respective holder. However, tests demonstrated the robots worked far better with 9V. So, don't be surprised if you see that my initial designs use a AAA battery box as a reference.
- Zip-ties
- Hot glue gun
- Pliers (for removing support material)
- Scissors (to cut the remaining zip-tie)
- Flat screwdriver (in case you need to separate the pieces.)
Step 1: Simple Walker Mark 1: Upcycled Prototype
Before creating any design with Tinkercad, I started doing some sketches and building a prototype using some broken toys and other pieces I had in my workshop.
It's a great to give to the students a bunch of e-waste and a gearbox, so they can explore other approaches for building simple walking machines. For more ideas, you can check some of my previous walking prototypes made with plastic junk:
https://www.instructables.com/id/Chopsticks-the-Ro...
https://www.instructables.com/id/Heartcrab-a-Lamba...
Step 2: Simple Walker Mark 2: Body
Let's start with the first CAD walker. The Mark 2 only requires one end of the gearbox's axle, and for that reason, only one crank.
Bring the "Hobby Gearmotor" from the "Circuits/Components" menu from the shapes library. One of the shafts must be pointing up. Then, create a half case, using a long box (where the gearbox will be attached) and two small boxes; one in front of the gearbox, one in the back. When you are happy with the result, group them.
Step 3: Simple Walker Mark 2: Axles
The legs will be connected to the body through two axles. Each one will be made from two cylinders: a thick one (to reduce contact surface with the body), and a thinner one, that will pass through the leg's hole.
The thinner cylinder must have a bevel for an important reason: do you remember we are not using screws? Legs and other components will be attached using 3D printed pressure lock washers, with a hole of more or less the same diameter of the axles; so the bevel will be useful for an easy insertion.
When you finish creating the axle, duplicate it and place it in the opposite box.
In this case, the diameter of the axle is 6 mm.
Step 4: Simple Walker Mark 2: Long Legs
Bring a box from the shapes library, make it flat and add a cylindrical hole in the middle. That will be the "hips" of the robot. Then, on each end, place two more boxes to create a leg. You can add some radius to the boxes and modify their angles, giving to the legs a more organic shape.
Axle's diameter is 6 mm. The cylindrical hole's diameter is 8 mm, to give it more tolerance and free spinning.
Step 5: Simple Walker Mark 2: Short Legs
Duplicate the Long Legs design, and bring it to the other end of the body. Reduce the height of the legs, so they are shorter that the original.
Also, you can play with the knees position and angle. Consider that the long legs will be forward, so investigate on internet your favorite quadruped (a bull, a horse, a jaguar, a Boston Dynamics robot) and polish the design according to it.
Step 6: Simple Walker Mark 2: Legs Articulation
To each pair of legs, add a 5 mm mini-axle (it will be connected to the crank). Don't forget to add some bevel. Group it with the rest of the leg kit.
Now, place each leg kit in its respective axle. If you see the leg kit is too close to the body, make the axle higher.
Step 7: Simple Walker Mark 2: Crank
Bring the workplane over the gearmotor. Now, place a cylinder and manually align it with the gearbox's shaft. Then, place over it an axle similar to the ones you already created for the legs kits (diameter: 5 mm), but place it off center, more or less aligned to the axle in the large legs kit.
Step 8: Simple Walker Mark 2: Long Transmission Rod
Create four discs of 12 mm diameter, with a hole that allows the mini-axles to turn freely (NOTE: originally the holes were 7 mm diameter, but during the tests they proven to be to loose, so I changed them to diameter 5.5 mm.)
Then, place the discs this way:
- One inserted in the mini-axle of the short legs kit, over the main box of the kit.
- One inserted in the crank's mini-axle, at the same level of the previous disc.
- One inserted in the crank's mini-axle, over the previous disc.
- One inserted in the mini-axle of the long legs kit, at the same level of the previous disc.
Now, bring a box from the shapes library, change its angle and position, and place it in a way that joins the first two discs. When you are happy with the result, group the two discs with the box. This rod will transmit the power from the crank to the short legs kit.
Step 9: Simple Walker Mark 2: Short Transmission Rod
In the same fashion, bring another box to join discs 3 and 4 from the previous step. When you are OK with the result, group the two discs with the box. This rod will transmit the motion from the crank to the long legs kit.
Before continuing, dedicate some time to check that the transmission rods are placed in a good position. Analyze if the movement will work in a proper way, or if the mechanism will get jammed with the main axles or another part of the body.
Step 10: Simple Walker Mark 2: Lock Washers
Create three discs of diameter 10 mm, with a hole of diameter 5.5 mm (NOTE: after test, this measurement was modified to 5 mm, and later, to 5.2 mm). Now, fit them on each mini-axle. They need to have a tight grip, but allowing the transmission rods to rotate fluently.
Then, create two discs with a cylindrical hole, diameter 6 mm. They will be placed on the main axles of the body.
Step 11: Simple Walker Mark 2: Gearbox Attachment Holes
The gearmotor from Tinkercad library is great, but it have something that may be improved: it doesn't have the holes for screws. We will use these holes to attach the real gearbox to the body using a zip-tie, so we need to create them.
When you measure the real gearmotor with a caliper, you realize its holes are diameter 4.5 mm, and they are placed 5 mm away of the rectangular border of the gearbox.
Bring a box and change it to 5 mm. It will help you to calculate where to place the cylindrical holes of 4.5 mm each. Hide the gearmotor and group the holes with the body.
Step 12: Simple Walker Mark 2: Battery Holder's Case
Now, turn the robot upside down. Time to create the case for the battery holder!
As I mentioned in the Supplies section, originally I used the AAA battery box from the components library of Tinkercad. In this case, I transformed the battery box into a hole and group it with a bigger solid box. However, the robot worked better with a 9V battery, so I took the dimensions of the 9V battery holder, created a hole box of those dimensions and grouped it with with a bigger box.
Whatever power source you choose, don't forget to create a hole to allow the wires to pass through it.
Step 13: Simple Walker Mark 2: Making Holes to Adapt the (real) Gearbox
Create a duplicate of the Hobby Gearmotor and transform it into a hole. This hole gearbox must be located in the same position of the solid one. Hide the solid gearbox and group the hole one with the crank, so the printed one will have an available socket to insert the shaft from the gearbox.
Also, don't forget to open a cylindrical hole into the body of the robot, in the same spot where the available motor shaft is located, so it can spin freely.
Step 14: Simple Walker Mark 2: Attaching the Battery Case to the Body
Place the battery case over the top of the body. However, don't do it directly. You need to leave some empty space to allow the zip-tie to run and the available motor shaft to spin. Place two boxes over the body, and then, place the battery case over them.
Step 15: Simple Walker Mark 2: Holes for Fun Accessories And... Smile for the Screenshot!
Our design is almost finished. However, let's place some cylindrical holes of diameter 6 mm in the front, available part on top, and back of the body. This is just for aesthetic and fun reasons, because kids can create their own accessories and plug them there to customize their robots, Mr. Potato Head Style.
Now, let's place our basic Walker Mark 2 with all legs touching the workplane, for a nice photo! CLICK!
Great. Now bring back the Walker to its original position, body parallel to the workplane. We are not done yet.
Step 16: Simple Walker Mark 2: Preparing the Pieces for Printing
Duplicate your Tinkercad design and leave the previous one as a demonstration of how the final product will look. Now take this duplicate and disassemble the robot, placing all the pieces over the workplane. Export them and send them to the slicer.
I printed the pieces with 20% infill and raft. The body was the only part that needed supports. It was too long for my small Biqu Magician, so I had to print it in vertical position. All pieces were printed in a 105% scale, to allow the crank to fit perfectly into the gearbox's shaft.
Here you can find the STL files for this Walker Mark 2.
Attachments
Step 17: Simple Walker Mark 2: Assembling and Test
The assembling is very straight-forward, if you already know the design:
- Attach the gearbox to the body, passing a zip-tie through their available holes. After the gearbox is firmly attached, cut the remaining end of the zip-tie.
- Attach the crank to the gearbox.
- Place the battery holder in its case, and pass the wires through the hole.
- Connect each cable to each pin of the motor.
- Insert the legs kits into their respective axles. Fasten them with their lock washers. Check that the legs kits can turn without issues.
- Connect the crank to the legs kits using the transmission rods. Keep them in place with their lock washers. Check that they can move without issue.
- Insert the battery and turn on the switch.
OK. It's working, but it's incredibly slow. Time for some improvements!
Step 18: Simple Walker Mark 2: Improvements
Now, nothing is perfect at the first try; so after some pieces were broken and the robot was so annoyingly slow, so I had to do the following corrections:
- A bigger battery case to keep a 9V battery holder instead the AAA one.
- Addition of fillets in the union between the mini-axles and the rest of the component. (crank and legs kits.)
- First, the lock washers were too loose. The second time, they were too tight. I solved it removing some material using a pair of scissors.
- I added hot glue in the feet, to give more traction to the robot.
Now the robot works far better!
Step 19: (For Both Versions) Fun Accessories!
You can create some interesting accessories to customize your Walker! You have three holes of diameter 6 mm in your robot, so you can use a cylindrical plug of diameter 5.4 mm to connect extra parts.
I started with a skull and a plasma gun (Why? Well, let's say I am addicted to a video game named Valfaris). The skull from the library was scale-locked, so I exported as an STL file and imported it again to the workplane, to make it bigger. I also created a dinosaur's head and tail, and some eyes.
Step 20: Simple Walker Mark 3: Taking the Best Parts of Mark 2 and Changing the Orientation
Time to build a more efficient machine. Nevertheless, it's not necessary to start from scratch, considering the Mark 2 design has several pieces that can be optimized for this new idea.
For starters, you need to rotate the gearmotor 90 degrees, so the shafts are at the sides of the robot. For that reason, the axle for the back legs must be rotated 90 degrees. This time you will use both shafts and for that reason, two cranks; so duplicate and mirror that axle. You can erase the front one, considering the previous operation is easier than bringing the front axle to the bag.
Also, its good idea to reduce the length of the body, considering there is a lot of empty space between the gearbox and the front and back boxes.
Last but not least, duplicate the gearmotor, make it a hole and group it with the rest of the body, so the real gearbox will perfectly fit there.
Step 21: Simple Walker Mark 3: Adapting the Cranks
Duplicate and mirror the crank, and place them on each shaft of the gearmotor. Inspect the body, and check that it doesn't touch the cranks. If that's the case, remove the contact parts using a hole box, so the cranks can spin freely.
When you finish, select all this construction and turn it 180 degrees (upside down.)
Step 22: Simple Walker Mark 3: Transforming Mark 2 Legs Into the New Back Legs
The long legs kit and the long transmission rod from the Mark 2 will be transformed into a single leg. Remove the legs and the mini-axle, and place the rod in an angle of more or less 15 degrees. Don't forget to add some metafillets between the rod and the leg. Group.
Step 23: Simple Walker Mark 3: Front Legs and Adaptation to the Back Legs
Transform the front legs kit into a single leg in a similar way of the previous step. However, keep the mini-axle and the fillet. Make the leg longer and place the mini-axle in the top end.
This part depends more of you eye: Insert the front leg into the crank's axle, and the back leg into the big axle. Start tinkering with both of the legs until you can insert the rod's hole of the back leg into the mini-axle of the front leg.
Also, add some round roofs as feet for the legs. They will look cool and add more surface for traction.
Step 24: Simple Walker Mark 3: Lock Washers
After you get a satisfactory result, lock the legs to the body, crank and between them, using the lock washers designed for the Mark 2.
Step 25: Simple Walker Mark 3: Mirroring the Left Side Components And... Another Final Screenshot!
Duplicate the full legs assembly created for the left side, and take it to the right side. Mirror it. Now, another nice screenshot for the presentation!
Step 26: Simple Walker Mark 3: Preparing for Printing
Like the Mark 2, duplicate your Tinkercad design and leave the previous one as a demonstration of how the final product will look. Now take this duplicate and disassemble the robot, placing all the pieces over the workplane. Export them and send them to the slicer.
I printed the pieces with 20% infill and raft. The body was the only part that needed supports. It was too long for my small Biqu Magician, so I had to print it in vertical position. All pieces were printed in a 105% scale, to allow the crank to fit perfectly into the gearbox's shaft. Here you can find the STL files for this Walker Mark 3.
Attachments
Step 27: MARK 3: Assembling and Test
The assembling is very straight-forward, if you already know the design:
- Attach the gearbox to the body, passing a zip-tie through their available holes. After the gearbox is firmly attached, cut the remaining end of the zip-tie.
- Attach the cranks to the gearbox shafts. If you want the Walker to... walk, the cranks must be in alternated position (left crank with its mini-axle facing forward; right crank with the mini-axle facing back). If you place the cranks with both axles aligned, probably your robot will walk like hopping
- Place the battery holder in its case, and pass the wires through the hole.
- Connect each cable to each pin of the motor.
- Insert the legs into their respective axles (front legs to the cranks, back legs to the body) Fasten them with their lock washers. Check that the legs can rotate without issues.
- Connect the back legs to the front legs using their fixed transmission rods. Keep them in place with their lock washers. Check that they can move without issue.
- Insert the battery and turn on the switch.
- Test how it moves. After that, feel free to spread some hot glue on the soles of its feet. Does it improve the traction?
And your Mark 3 is ready! Have fun with your walking robots!
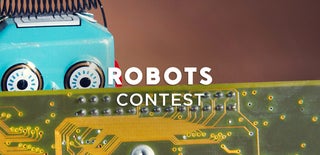
Grand Prize in the
Robots Contest