Introduction: Toy Train Advent Calendar
For those of you that have seen my other instructables, I love Christmas, my family, and recycling old wood. My wife also loves trains at Christmas, and wanted an advent calendar. I tried to integrate the two, and made a toy train advent calendar. Thus i came up with this fun little project. The entire project required only dowels, old pieces of two by four, and glue.
As you can see from the project picture, I designed it to look as if it is coming out of a tunnel from the wall--each day one new train car coming out with a new treat. Ultimately the train would wrap around the base of the Christmas tree. However, it works just as well having the entire train out from the beginning.
Step 1: Supplies
This project used only 3 ingredients in the making process, left over wooden 2 by 4 cuttings, variously sized dowels, and glue.
In terms of tools, I used a travel table saw, a drill press, a jig saw, a miter box, a pull saw, files, rasps, and sandpaper.
Step 2: Preparation
The first step, which is not depicted in the instructable, was that I ransacked my old excess wood cuttings in my workshop. I had stored multiple pieces of old 2 by 4s that I received for free. I was in Home Depot, talking to a vendor who was unloading molding onto the floor. The strips of molding were separated by pieces of 2 by 4. The vendor let me take them for free.
Step one for this project was that I "milled" these strips of wood into thin strips of wood, approximately from 1/8" to 1/2". I "milled" these by running them through my table saw with a guide close to the blade. If you intend to do this as well, be very careful when working close the table saw blade. I used these various sized milled strips to make all parts of the train other than the wheels, and a few pieces of engine.
Step 3: Step One: Train Car Bodies
Once I milled enough of my wood into appropriate thicknesses, I cut the 1/2" strips into the body pieces for the cars. These are the thickest pieces as I planned to drill into them for the wheels. Other than the body of the train engine and the lumber cars, the blocks were all about 4 inches in length. The engine block was 5 inches in length, and the two lumber cars were 6 inches in length.
Once I cut 21 4 inch sections, 2 6 inch section, and 1 5 inch section, I cut a template out of paper to mark the ends of the blocks for the connecting sections of the car. I used the template at both ends of each block (except the front of the engine block).
Step 4: Molding the Car Bodies
I then used a jig saw to cut off the marked areas on each block.
Step 5: Shaping, Smoothing, and Evening
I always like to break out my hand tools when working on wood projects. I use a rasp to make sure that the ends were even and removed excess wood and splinters. I then used a finer file to smooth and round the top edges, and then sanded the whole body car with increasingly fine sand papers as you can see in the pictures.
Step 6: Shaping the Engine and Lumber Cars
To finish shaping the Engine car, I used my table saw to cut two approximately 30 degree angles to a point at the front of the engine. I then cut a shallow slant on the angle as well. As you can see from the picture, I cut the back of the engine piece with the same template as every other piece.
For the lumber cars, I make a cut on each side of each block in the middle to give the illusion that it was two connected cars. I then cut both ends according to the template.
Step 7: Connecting Holes
As you will see later, I designed a connecting piece that will fall into the end holes of each piece. To make the holes consistent I placed the template back on each body piece and marked each car on the same spot.
I then made a small pilot hole with a very thin drill bit, and then drilled into the pilot hole with a 1/4" inch drill bit. As all of the wood pieces in this project were thin to very thin, I made sure to make a pilot drill hole in everything I drilled, and I pressed the drill in slowly to reduce the risk of cracking the wood. I also always place a piece of scrap wood under the piece I was drilling (as you an see in the pictures) to reduce tearing and splinting as the drill bit exited the base of the wood.
Step 8: Making the Engine
To make the engine I cut a length of 1.5 inch dowel at about 2.5 inches. I then cut the piece of dowel on one end at about 20 degrees on each side and along the top (as you can see in the picture). I also trimmed the bottom of the dowel so that it sat flat on the engine body.
I then took a few strips of the 1/4" thick wood, and cut it into small pieces for the walls and roof of the engine compartment.
Step 9: Making the Engine Compartment
The picture here show Mach 1 of the engine house. I took this one apart and put a 45 degree slant on each piece so that they hide the ends of the wood. You can see this in the picture. I used a 3/4" drill to put a window on each side wall of the engine house, and glued all of the walls together. There is no picture for this, but I then cut the rear piece of wood so that it looks like there is a back door. Lastly I took some slim wood cutting from my table saw and glued a window frame in the front of the engine house.
I did not glue the roof on, as I intended it to be removable to claim the treat for that day.
Step 10: The Smoke Stack
To Make a smoke stack for the engine I took two different sized dowels, 5/8" and 3/8". I drilled into the 5/8" section with a 3/8" drill bit.
I then inserted the 3/8" dowel into the 5/8" dowel with glue, and cut each end at the length I wanted. I sanded the 5/8" top section to round and smooth it.
I also drilled into the top of the 1.5 inch dowel of the engine, and slipped the 3/8" end of the dowel into the engine with a little glue.
Step 11: The Roof
I then took the roof piece and put a 45 degree around the top for visual affect. I placed the roof piece on the engine body and marked the underside around the wall pieces.
I cut thin sections of scrap wood, and glued them along the lines marking the inside and outside of the wall so that the roof sat snugly on the body but still came off without a struggle.
Step 12: Front "Light"
As an added detail I took a 1/4" dowel, round the end, and cut off the last 1/8". I glued this to the front of the train to look like a headlight.
Step 13: Trim
Lastly I added a few strips of 1/8" dowel along the sides of the engine for look.
I will discuss the wheel assembly at the end, as the process was the same for all body sections.
Step 14: Open Cars: 3 Styles
I wanted to have a variety of train cars for visual effect and as variety allowed for different sized treats. After reviewing the designs for numerous trains, I decided to include 3 open car designs. These car were not closed compartments, and thus allowed for larger treats to be included in the advent calendar.
For all of these designs I used I/8" to 3/16" thick wood slices.
Step 15: Stationary Open Compartment
For the first design, I created a template as in the picture. I made two of these cars. I cut two side panels at 30 degrees angles int triangle and then cut off the tip each triangle. These are the end pieces. I then cut the side walls and put a 30 degree slant at the top and bottom of each wall piece so that it would line up with the end pieces evenly.
Step 16: Glue
I then glued the side and end pieces together. I let this sit overnight, and then glued the compartment to the car body. Other than some sanding, these compartments were complete.
Step 17: Swinging Compartment
For the second open container design, I made a swinging compartment. It moved freely side to side. I first cut two end cap pieces of wood as shown in the pictures.
Step 18: Drilling
I then drilled in the top each end cap first with a pilot hole, and then with a 1/4" drill bit.
Step 19: Compartment Body
For the compartment body, I took think strips of wood, approximately 1/2" and cut them at 45 degree angles at the ends. I glued them together into a rectangle shape. I then cut the two base pieces and put a 45 decree angle at the top and bottom so that they sat evenly on the frame.
Step 20: Filling the Sides
To fill the hole in the sides, I made a template and used it to cut two filler triangles.
Step 21: Glue
I Glued the side triangles to the bottom pieces, and then glued the completed bottom to the frame piece.
Step 22: Drill
I then drilled a hole into each side of the compartment first with a pilot drill and then with a 3/8" inch drill bit. These holes were larger that the one in the end pieces as I wanted the compartment to be able to move side to side.
Step 23: Putting It Together
I then glued the end pieces to the body block, and let it sit overnight. The next day I took a 1/4" dowel and passed it from the end pieces in the body compartment. The end pieces held it firm but the compartment pieces larger holes allowed for some motion.
Step 24: Trim
I used a pull saw to cut off the excess dowel and make it flush to the outside of the end pieces.
Step 25: Finished
I make two of these open compartment cars.
Step 26: Open Compartment 3: Coal Car
The last open compartment was the coal car following the engine compartment. There was only one of these cars, and he process was similar so I did not break it down. I cut out the front, back, and side pieces as they look in the picture. I put a 45 degree angle at the joints, and glued it all together.
Step 27: Cage Cars
I designed two cage cars to be part of the train. First I took a 1/4" square dowel and make a frame out of it the size of the body block.
Step 28: Marking the Location for the Bars
I then laid the frame on the body block and outlined the dimensions. I then used a rules to mark the location of the bars on the body block and in the underside of the frame.
Step 29: Drill the Bar Holes
I used a 1/8" drill bit to drill the bar holes into the body block, and into the underside of the frame.
Step 30: Make the Bars
I took a 1/8" dowel and cut 14 2" bars for each of the two cage cars. I rounded both ends of the bars with sandpaper so that they would go into the drilled holes more easily.
Step 31: Putting in the Bars
I used a hammer to gently push the bars into the body blocks. I then put the frame on top and tapped it down on the bars with some glue on each bar tip. You can see the finish product in the last picture.
Step 32: Lumber Trailers: 2 Styles
I made two lumber trailers, each with different types of lumber. One had a single thick log, and the other had many stacked logs.
For both designs I want to put a "fence" on the sides of the lumber. To do so, I first marked the body plates at measured intervals for the fence posts, and drilled the post holes with a 1/8" drill bit.
Step 33: First Design: Stacked Lumber
For the stacked lumber I cut 12 5 inch sections of 1/4" dowels. I glued 4 together side by side for the base, and three pieces together for each of the sides. I then glued the 3 section side pieces to the end pieces of the base.
I then cut half inch sections of the same size dowel and glued four together in a square pattern for each end of the lumber. I glued the square at the front and rear of the lumber.
lastly I glued two of the 5 inch sections together for the "top." I did not glue this to the rest as it is designed to be removable so that a treat can be hidden inside of the lumber.
Step 34: Glue
I then glued the stacked lumber "box" to the body block equidistant from the fence posts at each side.
Step 35: Fencing
Lastly I cut fence planks from thin scrap wood, and glued three planks to the two fence posts in each section. The stacked wood was just tight enough to hold the planks in place until the glue dried.
Step 36: Single Log Style
For the other design I cut a 5" section of 1.25" dowel. I then drilled about an inch into the center of one end with my thinnest drill bit.
Step 37: Tube
I then cut off a little less than half an inch from the end I just drilled into. Both the half inch section and the remaining section still showed the drilled pilot hole. I then took a 3/4" forstner drill bit and drilled into the top half inch section using the pilot hole as a guide. I made sure to drill into the face that was cut directly from the larger section. This way when I place them two pieces together, they fit nice and snug.
I then drilled as far as I could into the longer section using the pilot drilled hole as a guide.
Lastly, I cut a 3/8" section of a 3/4" dowel and glued it into the hole I drilled into the smaller end piece. I then put the two pieces together flush and let the glue dry. Thus the end cap piece slips into the larger section as a cap.
Step 38: Gate
I also wanted to fence this lumber car. The process was the same as for the stacked lumber car, except that I only used two fence planks and did not glue the larger lumber piece to the body block. Once dry the fence holds the large lumber in place.
Step 39: Done
Here are the completed cars.
Step 40: Container Cars
I made 5 container cars with sliding doors for the train. To start I cut side and back walls for the containers about 2" high. I then cut a thin (about 1/3" wide) of wood for the top of the face wall. I glued everything together with 45 degree joints.
Step 41: Face Walls
I then cut two pieces of wood for the front wall, but leaving an big enough opening for a the treat to be put inside and taken out afterwards.
Step 42: Sand and Smooth
I sanded the corners round and smooth for looks
Step 43: Slider Guides
I then two some 1/16" thick by 1/8" wide wood slivers, and put two section per compartment (one for the body plate, one for the roof). I glued the pieces to the body plate and to the underside of the roof, equidistant from the outer edge and sides.
Step 44: The Door
I then took some 1/8" thick wood and cut two doors per compartment. I then drilled 1/8" holes in inside middle of each door, and slipped a half inch section of 1/8" down into the door. I left the bigger part on the inside to hit the walls and stop the doors from opening to far and falling off.
Step 45: Glue
I then glued the compartment frame to the body block, and the roof to the top of the frame. I put the doors in place before gluing. The doors slid easily open on each side.
Step 46: Passenger Cars: 2 Styles
I made two designs for the passenger cars, 4 of regular passenger cases, 4 of the trolley design, and one slightly modified trolley design for the trailer.
To start off I did the same thing as every other stage, i cut the walls and roof.
Step 47: Windows
For windows I used a 5/8" drill bit (after the pilot hole) three times on each side, and once on the face and rear pieces.
Step 48: Doors
I then took the face and rear panels and cut down the mitre box to create a door space in the front and rear.
Step 49: Roof
In order to give myself additional room in the passenger compartment I made the roof pieces by gluing together a frame with open space in the center. I then glued a smaller cut square piece over the hole and weighed it down with a hand weight.
Step 50: Lip
I then Marked the underside of the completed roof piece where the lip would be. I glued small strips of thin wood around the marking to keep the roof piece in place when on the body.
Step 51: Glue
I then glued the compartment body together, then attached it the body block. I did not glue on the roof as It is intended to come off if necessary.
Step 52: Passenger Cars: Trolley Car
The trolley cars were made in a very similar way. The body is slightly smaller to give me room to add handle rails to the ends of each compartment. I again used 1/8" dowels for this.
Step 53: Handrails
At the end of car I drilled two small holes on each side, and then inserted the 1/8" sections. I then cut small sections for the handrails. The caboose car ends with a handrail that blocks the rider from exiting from the rear.
Step 54: Glue
I then did everything as described for the other passenger cars. I glued the walls together, drilled out windows and doors, and marked the underside of the roof plate with the outline of the walls.
The only difference with this design is really the roof. This design includes a small cupola on the roof.
Step 55: End Product
Here is the finished product for each design. Both designs include a removable roof for access for treats.
Step 56: Wheels
For the wheels I took a 3/4" dowel and a 1/2" dowel, and cut thin (about 3/16") slices out of both. I also cut some slices from a 1.25" dowel for big wheels for the engine car.
I then marked each, as well as possible, in the dead center.
Step 57: Drilling
I then drilled slowly into each. For the smaller wheels, these are to hold he wheels on, I used a 3/16" drill bit, and for the larger wheels I used a 1/4" drill bit. I used a 3/16" dowel to hold the wheels one. This allowed for a tighter fit for the outside smaller circle, and a loose fit for the larger actual wheel to spin.
Note: Drill very slowly into each wheel to reduce the risk of cracking and to avoid the drill catching hold of the wheel and spinning it.
Step 58: Wheel Pegs
I then cut a half inch section of the 3/16" dowel for each wheel and ran it through both wheels.
Step 59: Drilling Wheel Holes
I then took each body block and marked where the wheels would go. I drilled into the body block with a 3/16" drill bit. I put a little glue in each hole and pushed the wheel peg in.
Step 60: Viola...Wheels
There you go. The wheels were designed to be aesthetic rather than functional. They turn but are not perfectly aligned and even.
Step 61: Compartment Links
Lastly, for the train, I created links to connect all of the body blocks. I cut 2/3" wide strips of 3/16" thick wood. The strips were about 1.5 inches in length.
I then drilled first a pilot hole and then a 3/16" hole at each end of each piece. I marked then so that they are uniform.
Step 62: Connecting Peg
I then cut 1/3" pieces of 3/16" dowels and gently hammered them into the holes.
Step 63: Flush and Smooth
I then sanded the tops flush and smooth.
Step 64: Rounding
I took each piece and trimmed off all four corners at a 30 degree angle on the mitre box.
Step 65: Sanding
And sanded the ends into a smooth flowing rounded edge. The pieces fell easily into the 1/4" holes I drilled in the body blocks.
Step 66: Train Tunnel
The last thing I made was a Tunnel house to mark the days and have the train emerge from. I wanted it to look old fashioned so I cut half inch wide, 3/16" thick planks of wood for the face and sides. I glued 4 planks together for each side and cut the tops to a 30 degree pivot to follow the roof angle.
Step 67: The Face
For the face I glued pieces together and then trimmed the bottom flush with the side. I brought the planks together at a 30 degree angle in the middle as you can see in the picture.
Step 68: The Roof
For the roof, I took some of the weathered looking excess wood left over from the milling process and made roof planks. I cut each one to fit and glued them along the face and walls.
Step 69: The Count Down Plates
Lastly I drilled two 1/8" holes in the face to mark the days.
Step 70: Pegs
I cut two 3 inch long sections of 1/8" dowels and ran them through the holes. They protruded from the front about 1/3" and out the back about 2.5".
Step 71: Number Plates
I cut 1/8" thick, 3/4" wide, 1" Long sections of wood for the number plates.
Step 72: Number Plates
I cut a total of 12 of them as I will need a plate for 0, 2 for 1, 2 for 2, and 1 for 3 through 9
Step 73: Peg Holes
I drilled a 3/16" hole at the top of each plate after a pilot hole to hang them with.
Step 74: Numbering
I then wrote the numbers on each plate. NOTE: I bought a set of number stamps and intend to redo them with the stamps on the back. I hung all of the plate inside the Tunnel until they are needed.
Step 75: Emerging Advent Calendar
As I originally stated, this calendar was designed to emerge from the tunnel one new section each day of advent. The number of the day would reflect the day of advent as in the picture above. Eventually the train could wrap around the Christmas Tree.
However, it could just as easily be placed out in full and opened one day at a time.
Step 76: Candy
Finally, I bought a bunch of candy and treats and filled the section of the train as illustrated in the picture above.
Step 77: End Product
Here is the end result. I hope you found this a fun project. Happy Making, and Happy Holidays!
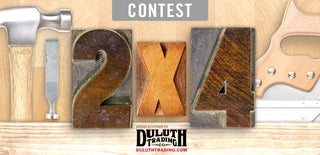
Runner Up in the
2x4 Contest
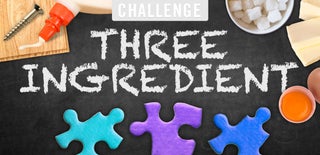
Participated in the
Three Ingredient Challenge
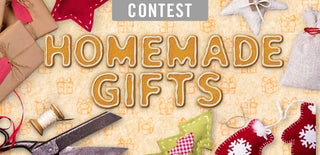
Participated in the
Homemade Gifts Contest 2015