Introduction: Transform an Oak Log Into a Buddha Head
I built a rotary axis indexer for my CRP pro CNC router. I was anxious to try it out. After a rare rainstorm last year my wife and went on a mission to find windfall in the hills above the San Francisco bay. What we found was a downed large California live oak. We brought a few pieces home and set it aside in my workshop.
I use Vcarve pro for most of my work. But it doesn't do 3d. so after a lot of trial and error with other various complicated programs. I downloaded a trial of DeskProto It can create code to carve or print 3d objects, it's an awesome program, fairly simple to use. I found an .stl 3d Buddha file, an .stl is simply a file that contains 3d vectors, and imported that into DeskProto it comes with a post processor for Mach3 which is the program that runs my CNC machine.
My rotary axis can turn work up to 15 inches by about 30 inches in length in diameter. That was about the diameter of the log.
Step 1: Mount the Work in the CNC Machine
I used a faceplate and a live center for most of the carve. The bit was a 1/2" x 4.5" bottom cleaning router bit. The finished head is about 19" high by about 10" in diameter that's how I was able to get decent resolution, with a 1/2 inch bit. You may notice from the photo, I'm taking very aggressive 1" deep passes. That came about from my not completely understanding the DeskProto program. The general rule of thumb is the depth your passes should be about half the diameter of the bit. Again I got lucky, the moisture content of the oak was about 40% so that combined with my stepover being about 5% had the bit sailing through the oak. The plunge cuts were scary though! I've attached the 3d toolpath (gcode) for Mach3. This gcode will only run on a Mach3 controller.
Stepover: Stepover essentially measures the distance the tool will travel with each pass. Let's say for example you are cutting a 2" wide pocket and using a .25" end mill. If you set the stepover at .125" or 50% then you would take 16 passes to clear the entire area. The reason for changing the stepover is to either reduce machining time (higher stepover) or for more fine machining (lower stepover).
Plunge Cut: The're 2 kinds of ways a router bit can enter the workpiece a ramp where the bit enters the piece gradually and a plunge straight in.
Gcode: G-code (also RS-274), which has many variants, is the common name for the most widely used numerical control (NC) programming language.
Attachments
Step 2: Start Cutting
Of course this being my first rotary project it was not without mistakes.
Early in the cutting I ran the spindle smack through Buddha's nose. I used a little west system epoxy with 404 high density filler and turquoise tint, to try my interpretation of a nose job. I'm crossing out plastic surgery on my resume.
The log was not quite big enough to carve the back of the head due to the natural curve of the tree. I decided just to live with that. I managed to run the spindle through the back of the head as well. I was able to erase that scar with a 4" disk grinder and a rubber backed 36 grit sanding disk
The carving process to about 16 hours start to finish.
Step 3: Dry the Sculpture and Fill the Cracks
My drying technique was not stellar. Buddha tried to split itself apart durning the drying process. By the time it was down to 11 % moisture content, I should have just left it in a heavy paper bag. After 6 months It had a lot of checks (cracks) through the face. I filled these as best I could with epoxy resin and then finished off with a brown epoxy gype (paste). Epoxy is really hard to get off an uneven surface. I had to spend a few hours blasting with aluminum oxide and then blast a lot more with baking soda in my home brewed sandblasting cabinet (pictured). I know, the blast cabinet looks like a bathysphere, the porthole is from a WWII Victory ship that was broken up at Hunters Point years ago. The blue thing is a Harbor Freight soda blaster
Step 4: Finish the Sculpture
I used 3 coats of dewaxed shellac to seal the piece. and then Brown gel stain, some people call this technique glazing. I finished it with 3 coats of satin oil based polyurethane.
I have a 10" in diameter x 9' Honduras mahogany peeler pole that begging to be carved into something sitting on the floor of my shop. I hear "carve me" every time I walk into the shop now it tries to trip me.
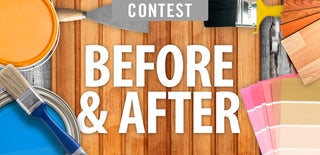
Participated in the
Before and After Contest 2016