Introduction: Viking Helm
Ok so this is one thats been on my wish list for a while..... This ible is the second part of a two ible story, check out my previous ible for the helmet padding
I've made a helm before using armourkris his How to Build a Spangen Helm. ible, but because I didn't have any real experience with metalworking it kinda got lumpy:\ So in an attempt to improve my collection and add to this site I made this:
Step 1: Tools & Materials
Tools:
Scissors
Straight edge / square
Tape measure
Marker / pencil
Arming cap / padding
Jigsaw / tinsnips
Clamps
Files
Dishing stump / leather sandbag
Powerdrill / drillpress (with drills matching your rivets / nails 4mm for big rivets, 2mm for the chainmaille holes and <1mm for the riveted chainmaille)
Bolts & wingnuts(same diameter as your rivets / nails)
Regular hammer
Dishing hammer
Planishing hammer
Metalworking stake / stone chisel
Ball stake(I made mine by putting liquid bottlecaps in half a ballpit ball and halfway through I got one from a friend)
Bench vice
Center punch
Hacksaw / boltcutters
Anvil (I use a cobblers last)
Sander (or a lot more patience than me) + sandpaper (up to at least 600 grit)
Ring making jig (chainmail)
Overlap ring cutting snips (will explain how to make these)
Pliers
Materials:
Sheetmetal (I used an old washing machine outer plating, wich is 1.2mm)
Cardboard
Tape
Large 4mm nails(to be structural rivets)
Metal wire, I used 1.3mm wire for the rings and 1mm for the rivets. (1.3 mm is really the thinnest you can use)
Tea lights / candles
Step 2: Measuring & Design
Start by figuring out what style you want, google around to find one you like, just one thing: NO HORNS!!
My chosen design has a faceplate / eyeguard and 6 in 1 riveted chainmail all around the bottom including the front. As for the padding, I made an arming cap for this ible. If you dont want / need / have an arming cap but you want to make sure that there's room for padding add about 5 - 10 cm to the circumference and front to back measurements.
Now to make a prototype of the bands you need to get your measurements (with padding). So start out by measuring the circumference of your head just above the ear and over your eyebrows. Transfer this measurement onto some cardboard with a width of about 4cm. The band width is up to you, however if you make it slimmer you will need to dish the panels more.
When you have this band drawn out, cut it and tape it to itself so you can wear it! Now put your tapemeasure on the lowest point on the back and pull it over your head to about the tip of your nose (I overshot it quite a bit). Transfer this measurement onto cardboard, again at 4cm width, cut it out and tape these two bands together.
Next use the tapemeasure to get the length of the middle band, this band goes from the top of one ear to the other. To get the correct position I wore the whole thing and had a friend mark the correct spot, next I used a tapemeasure to asure it would be symetrical. Turns out the best place for me was the center on each side + about 1cm to the back.
My measurements were (about)
70 cm circumference
50cm back to front
38cm left to right
each at 4cm width
The eyeguard will be designed when the helm structure is completed so you can fit it to the already finished helm.
Step 3: Making the Bands - Circumference
Now take the cardboard prototype apart and trace it onto your metal sheet. Make sure that you lay the parts out so your will have the least amount of scrap material. Check if the tracings are straight using a straightedge and cut out the bands using your tinsnips / jigsaw.
After cutting you might want to use a file to get the edges straight and smooth, remember to use a straight edge to make sure its all straight. I actually use a doorframe(one of the premade plastic ones) for the parts that were too long for my straight edge.
Bending the bands is done by simply placing it on your knee and slowly bending it. When you have the circumference band bent use your permanent marker to mark, centerpunch and drill a hole 1cm from both edges(picture 6). Next I took a piece of scrap metal and drilled a hole in it and bolted it onto the band. Then while pressing the band together, I marked and drilled a second hole in the scrap piece. This allowed me to connect the circumference band to itself(pictures 8, 9, 10, 11 and 12).
Next mark the center of the band on the back side and mark two points, just like before, 1cm from each edge and drill these (pictures 13, 14 and 15).
Step 4: Making the Bands - Back to Front
Take your back to front band, mark and drill 2 holes, again 1cm from the edges. Now you can bolt the two bands together, this allows you to put on the bands and shape the back to front one to fit your head just right. To get the back to front band to curve with the circumference band I placed it in my dishing stump and gave it a few good hits, this removes the gap between the bands(pictures 20 and 21). When the band is correctly shaped, take your marker and just mark the height of the circumference band on the back to front band(picture 22). Use your square to ensure the line is square to the edges, then mark and drill two holes, again 1cm from the edges(pictures 23 and 24). Mark and drill two more holes this time 1cm from the bottom edges of the circumference band (picture 25). Bolt the two bands together to mark and drill the holes on the front to back band(pictures 26, 27 and 28).
Step 5: Making the Bands - Left to Right
Looking back on it I think the next part should be considered optional, at the time it seemed to be usfull but it does hinder sanding a bit and I don't think it really adds a lot to the finished piece.
Start out by cutting a small strip, at least as long as the left to right band is wide, at 4cm width (same as the band width, pictures 29 and 30). Next draw a line in the center of the left to right band widthwise and lengthwise on the small strip(pictures 31, 32 and 33). Now take a small clamp and secure these two together so the lines match up(pictures 33 and 34). The next part takes a bit of patience, a bit of controlled violence and a lot of fiddling to keep the lines aligned. Put the band on your anvil with the small strip on the bottom and start pounding along its edge so the band gets a crease in the shape of the strip (pictures 34, 35, 36, 37, 38, 39 and 40).
Step 6: Making the Bands - Putting It Together
Place the left to right band inside the other two at the right position, I just placed it inside and placed it by sight, it turned out to be nearly perfectly centered(check with a measuring tape). Mark the position on the back to front band and draw a square line(pictures 40 and 41). Mark and drill some holes in the back to front band 1cm from the edges and markings(pictures 41 and 42). Clamp the left to right band onto the back to front and square it up, mark the holes onto the left to right one, drill these and bolt the bands together. Square up the bands at the side and mark the edges onto the circumference band (pictures 45 and 46). Mark and drill some holes again 1 cm from the edges and the markings (picture 47). Clamp the bands together and transfer the holes onto the left to right band and drill these (pictures 47 and 48). Finally the bands are done and you can go onto making the panels!
Step 7: Making the Panels
This step takes a bit of controlled violence and a lot of patience, time to make the panels!
Start out by taking out the bolts + wingnuts and place them back with the wingnuts on the inside(picture 1). This allows you to place the frame on a piece of cardboard and trace the hole, to get the corners rock the frame toward each side(pictures 2 and 3). Trace the front two panels and cut one out, place it on the other one upside down and trace it, this makes sure the panels will be symmetrical(pictures 3, 4 and 5). If your cardboard panels are too different you need to check if your frame is square. Be sure to make a mark that tells you wich way is up.
Now transfer your panel onto some sheetmetal with about 1.5cm to spare on each side. Add another line at about 1.5cm distance (the first panel I did 2cm but it turned out to be to much (pictures 25 and 26). I did so by just marking some dots at 1.5cm and then I just connected the dots. Cut this panel out and lets start dishing!
Take your freshly cut panel to your dishing stump and start wacking away at it with your dishing hammer, starting from the center and work your way out towards the edges. When you start to get a little bit of a dish shape (picture 15) take the nuts and bolts out of your frame and place them back with the wingnuts on the outside again. Place the dished panel inside your frame and check wich sides need more dishing(pictures 16 and 17). Keep doing this untill the inside of the frame is flush with the panel(picture 18). Don't worry if the outside of the frame matches up perfectly as long as its not more than a few mm, it will be coldsmithed down later on.
When you feel the panel is curved to fit your frame correctly, you need to drill some holes. Take out the bolts from the panel hole and clamp the panel onto the frame on one corner (picture 19). Push the panel down as much as you can and mark the hole in the frame onto the panel (picture 21). Centerpunch and drill the hole, now you can bolt the panel onto the frame and make some small adjustments if needed (pictures 22 and 23). The other holes are made in a similar way, bolt in the panel, clamp another corner and push the panel down to transfer the holes.
The second front panel should be cut by transfering the same cardboard cutout to ensure its symmetrical(it just needs to be upside down). Now for the back panels, these will most likely be a different shape so repeat the process from the start to create the two back panels.
Now you can choose to leave the panels as is if you want the rough finish, if not you (like me) have some planishing to do! Removing the paint helps to discover any bumps left, I just took everything apart and threw it on a fire to strip the paint.
Step 8: Drilling the Panels
After the (nearly) endless hours of planeshing, you'll want to get the panels truly fastened, so lets make some more holes! The goal here is to devide up the space between the corners of each panel, the main point is to make the helmet stronger and a lesser point is to make it look a bit better.
First I marked the center of the space between the circumference and the front to back bands (pictures 1 and 2) onto the front to back band. Then devided the remaining space in 3 to mark 2 more points (pictures 3 and 4). Add some squared lines at these points and place some marks at 1cm from both edges at each line (pictures 5 and 6). To get the marks onto the circumference band I took the same steps only I didn't place the lines because you only need the top side of the band to have holes (for now). Use these methods to place marks on all the bands and drill these.
Bolt the whole thing together again and make sure every bolt is as tight as it can be. Mark the panels through the holes you just drilled take the whole thing apart again and drill all the marks. Some of the holes(like mine) are really close to the edge, if you want your helm to be functional you need to redo it, but since mine is too thin to really be used it was ok to use the panels anyway.
Now you can bolt in all the panels and you'll start to notice the bands bending at the bolts when you tighten everything up. When you have all the bolts in you can take a small hammer and tap down all the bumps in the bands, make sure the bands are as flush to the panels as you can get them.
Step 9: Making the Faceguard Part 1
Time to make your helm strike fear in your enemies! To get the faceguard started have your frame and panels bolted together and place some carboard ontop to get a rough estimate of the width. Fold this piece of carboard in half to get the center, mark this and place another mark at 2cm from the edge (pictures 1, 2 and 3). Now place marks allong the edge at 2cm distance (picture 4). Take out the lower front two bolts and place the cardboard so the center mark falls in between the two ends of the circumference band and all the 2cm marks are at the edge of the band. Puncture the carboard through the holes and bolt it onto the helm in between the back to front and the circumference band (pictures 5, 6 and 7), you can keep the carboad in place by using some magnets to keep the corners down.
Draw out a rough shape on the cardboard, adjust it or make a new faceguard untill it looks the way you want, you only need to draw out 1 side. I actually made 2 before settling on this design. Just remember it is designed to deflect blows from the nose, brow and cheeks as well as scare your enemies. Once you settle on a design fold it double, cut it out, bolt it on and you can wear it! (pictures 8, 9, 10, 11,12, 13 and 14)
Transfer the carboard prototype onto your metal and cut it out, to cut out the eyes just drill a big hole in the center and work your way around with a jigsaw (pictures 15, 16, 17, 18, 19, 20, 21 and 22). Make sure to transfer the holes from the cardboard, these give you a good guideline for placing the faceguard. Now you can bend the faceguard and place it, for me it goes in between the front to band band and the circumference band just like the carboard.
Line up the marks and the holes (picture 23), make sure the entire thing is lined up by sight and mark the holes from the front (picture 24). Drill the holes and bolt it onto the helm, to get the guard on securely I chose to add one structural rivet to each corner of guard. While the guard is bolted on push down the corners and look where the closest panel hole is (picture 27). Place a squared line at this hole, place a mark at 1cm from the edge, centerpunch and drill it (Pictures 28 and 29). Now you can put everything back together and transfer the holes you just drilled onto the faceguard and drill them (remember to push down the corners when placing the mark).
If you used painted metal like me burn it off like the other parts, file the edges and bolt everything together!
Step 10: Making the Faceguard Part 2
Now you need to figure out what you want the distance between the faceguard rivets to be, I put a mark in the center at 1 cm from the bottom of the guard. Next I put a mark in the center at the top (just below the holes that connect it to the circumference band) and the last one I put in between the first two. To get the rivet holes marked on the brow side of the guard I devided the space between the top center hole and the one on the outer corners of the guard. These marks need to be at 1cm from the edge of the guard, so keep in mind that your measurement needs to follow this and not just go straight across. When all the marks are placed, centerpunch and drill each of them and bolt it onto the helm.
Transfer all the holes in the faceguard onto the circumference band and the back to front band, centerpunch and drill these!
Now comes a short step wich is somewhat optional, it isn't really necessarry but it is pretty easy and looks much better! Take a scrap piece of wood and secure it in your benchvise, my scrap piece had a hole in the center, you can make one by glueing 2 bigger pieces onto a smaller piece. Take a stone chisel and hit the inside center of the back to front band, in between the holes for the faceguard, a few times. This creates a crease wich makes the back to front band sit flush with the faceguard. Now do the same to the faceguard, only make the crease a little more shallow so the edges of the back to front band and the faceguard are forced flush.
Step 11: Making the Chainmail
At this step you need to ask yourself if you want chainmaille. If so what kind? I chose to make 6 in 1 riveted maille, wich simply put is a horrible and slow task..... So if you are ok with no chainmaille / lighter weave / non riveted find an ible or skip this step! However, if you want it to look awesome and be one of the strongest forms of medieval body armour, you should go for riveted. Since there are loads of ibles / tutorials online about making chainmaille (riveted or not) I wont go into much detail, but I put this step in because it explains a few crucial actions. If you really cant figure it out I will make a short image reel on how to make it. To make the overlap ring cutting snips I just used a file to create a small void a few mm from the tip, make the void the same size as the diameter of your wire.
Start out by making a piece of chainmaille, you don't need to make the entire thing yet. Take a piece of paper and lay the chainmaille ontop. Make sure the maille is in "resting" position, meaning it isn't stretched. Take a pen / pencil and put some marks at the top of each ring. Measure these marks and calculate what the average distance between the marks is.
Take this average and the radius of your rings (diameter / 2) and place marks on a piece of cardboard at 1x the radius from the edge and 1x the average apart. Now you have a good template to mark where the holes for the chainmaille need to go.
I started by doing the back to front band first, placing the template so the outer holes were no less than the average from the edges. After drilling these marks I bolted on the faceguard and marked where the edge of the back to front band was onto the faceguard. Take the faceguard off and use your cardboard template to place new marks starting from the line you just drew.
Before you reach the rivet hole at the top of the faceguard you need to make sure the maille holes arent too high onto the circumference band, remember the maille holes need to be 1x the radius of your rings away from the edge. When done with placing the marks drill all the holes and bolt the faceguard back into place. Now you can transfer the holes that overlap onto the circumference band, if you did the last part correctly the holes should be at 1x the radius from the edge. Drill the first hole so you can use this as a starting point for your template later on. Do this for the other side of the faceguard and use your template to work your way around placing marks. When everything checks out drill all the holes and clean off any burrs.
Step 12: Sanding
Alright this is pretty easy it just takes a while, I highly recommend wearing (latex) gloves to keep your sweat from corroding / staining the metal.
Start out by doing some rough sanding, this will probably reveal a few bumps missed during planeshing. Use your planeshing gear to get the last bumps out and continue to sand all the pieces.
When you have a piece sanded take some tealights and rub the entire piece (inside and outside), take a torch and melt the wax so it gets into all the corners / holes. Give the piece another coating of wax and go on to the next part.
Step 13: Riveting
Now that you have a fully shaped, sanded and waxed helm its time to replace those bolts with rivets! But lets do a test piece first, take 2 pieces of scrap metal (same thickness) and drill some holes (same width as your large nails).
To make the rivets I just took a nail, cut off the head, cut off the point and cut the nail in half, all using a boltcutter. Then I placed it on my anvil and hammered the top into a mushroom. To get the correct length I put it through the holes in the testpieces and figured out by eye how long they needed to be, for me it turned out to be about 6mm. Remember there are places where 3 layers of metal lay ontop of each other so those rivets need to be longer. There should be about 2mm protruding to make the rivet head.
For the width I set a goal of making each rivet head at least 1mm more than the width of the nail. Be carefull as some of these rivets will develop sharp edges (one drew some blood even!).
When you have a rivet done, take your scrap pieces and push the rivet through, take it over to your anvil and mushroom out the rivet with your ballpeenhammer untill the testpieces are stuck together! When you are satisfied with the result you can go on to riveting the helm. Make sure the rivet doesn't exert to much sideways pressure on the metal, meaning that the rivet shouldn't become too wide in the middle.
On the helm I started at the top and secured each piece. After that I chose to do the "worst" fitting holes first, meaning the holes that weren't aligned perfectly, to get them in place I used a nail to "guide" the pieces into place by putting a nail in and wiggle it around to get everything aligned
Step 14: Putting on the Chainmaille
Alright so I changed my mind about the chainmaille, at least for now due to getting it finished for the fair. Instead of going with the 6 in 1 riveted, I went with 4 in 1 butted maille. If I change it out I'll update the ible! To get the butted maille on I just made a rectangle large enough to wrap around the helm and by putting a ring through a hole and close it onto the rectangle.
Step 15: Storage and Use
OFF TO BATTLE!!!
seriously, don't. This helm is NOT designed to be used in reenactment or competitive fighting.
Firstly, the materials I used are too thin, 2mm mild steel is mostly used.
Secondly, the eye openings are to big, they should be small enough to prevent a one inch rod from being pushed through
Thirdly, the neck isn't protected properly, there should be, at the very least, steel braces to protect the neck / throat.
The rules can be found at http://www.sca.org/officers/marshal/docs/marshal_h... for the sca rules and at http://botn.info/rule/en-rules-for-buhurt-category... for buhurt.
Alright, now that the warning label is done, to keep this piece of kit nice and shiny it needs some maintenance. To get it ready for use just heat up the helm to slightly melt the parafin wax and rub it off with a clean rag. Keep melting and removing the wax untill it is nice and shiny.
*WARNING* Do this outside or you might ruin your floor *WARNING*
When you are done wearing it, use some tealights / candles and rub the ENTIRE helm with it, get in between the chainmaill too! Now give it a quick blast of heat to get it into all the corners. Any spots left uncovered might develop rust in time, however there should be a fine layer of parafin on all the parts so rust might not set in for a while.

Participated in the
Metal Contest
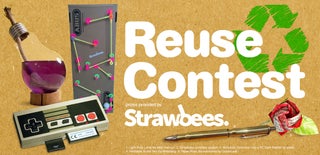
Participated in the
Reuse Contest
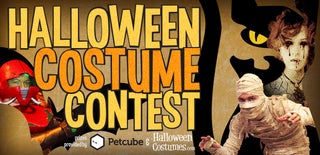
Participated in the
Halloween Costume Contest 2015