Introduction: Vintage School Desk Restoration Conversion to Bench (Decades to Make)
Hi all, I’ve had these vintage school desk wrought iron pieces for, well over a, decade. My mom & dad had converted it into a bench. It was passed on to my daughter but it had deteriorated over the years. When I got it, it was pretty much falling apart. So I stripped it of all the old rotten wood and set it aside with the intention I’ll remake it. Well I did sorta. I cleaned and painted the hardware. Then painted them and well it sat for another 5 years LOL. At any rate this details how I did, Sorry for not having any earlier pics of my progress.
This set of legs are from and old school desk, the hardware is actually the last seat that would appear in a row of desks which would typically all be mounted to two long stringer boards to keep the desks in a row. The other desks would have the actual desk over hang for the person sitting on the next seat behind it and so on until the last seat which would have no desk portion off its back.
Supplies
For Wrought Iron:
- Vintage School Desk Hardware
- Wire Brush (for cleaning wrought iron)
- Rustoleum Paint
For Wood work:
- Various 1" boards by 39"
- Circular Saw
- Hand Trim Router with Roman Bit
- Palm Sander
- Polyurethane
- Steel Wool
- Cordless Drill
- Cordless Impact Drill
- Pencil
- Square
- Tape Measure
For Monogram:
- Wood Burning Tool
- Laser Printer
For Assembly:
- Screws
- Concrete Anchors
- Mason Drill bit
- Cordless Impact Drill
Step 1: Clean & Paint Wrought Iron
Before removing all the rotted wood I took some basic measurements to make it a bench. I made note of the number screws needed and the size as well. In hind sight I could have made my measurements notes a little more understandable. I actually measure the top and bottom of each board, since there is a curve to the board placement on the legs. After 5 years I had a hard time understanding my own notes since I no longer had the original boards as reference. But I finally figured it out.
I took a course wire brush and removed all the old green paint along with any rust that had build up on the legs. After the wire brush I took a course 80 Grit sand paper to smooth out as much as possible.
I used a dark brown Rustoleum paint. Gave it two coats and let it dry for say about 5 years (lol).
Step 2: Mount Feet
I found two appropriate lengths of 2x4s to mount the the legs. I polyurethaned each after sanding them down. I screwed the feet of the legs to the finished boards and let them rest again for about 5 years.
Step 3: Measure, Cut, Route, & Sand
OK 5 years gone by, I think it is safe to go to the next step. Taking my almost undecipherable measurements I set about pulling boards from my stock. I had initially wanted to make the bench wider than but my boards set the limit for me as I was short one board to go to a full 42”. So I downsized to 38” lengths. Using my circular saw I cut apart my existing boards down to the narrower strips I needed to be able to attach to the curved hardware.
Once I had the boards all cut down to the proper widths I sanded all down to remove any marks or blemishes that were existing in them. I temporarily mounted the boards to the legs to make sure they would fit properly.
Holding in position I drilled small pilot holes via the screw mount holes on the hard ware. With this test assembly I was able to make sure the seat folds up with no interference from the back.
This is where I figured out my cryptic measurements from years gone by. The bottoms of the boards needed to be slightly smaller than the tops so that as they attach to the curve of the hardware they don’t bind up against the other board in the sequence.
To achieve this I took my hand trim router and used the smallest round edge bit I had to remove the edge so they wouldn’t be touching when assembled. I then switched my router bit to a roman edge and did the ends of each board. For the top board on the back and the front board on the seat I angled the corners about 3” face to the corners. I then routed the top edge of the back and the bottom front edge of each board to finish the roman look.
Step 4: Add Monogram
Before moving on to Polyurethaning it all I decided to add a bit of flourish to the top center board by wood burning a monogram “F” to personalize it. An after thought (only took me 5 years to come up with that).
Now about the letter itself... I have no clue what font it is. I actually found it in my Cricut Software in the new Monogram feature. Its under the Handwritten Styles. It doesn't give it an actual font name. I placed it in my software then did a screen grab and redrew it in Abobe Illustrator.
I printed out my letter design to size in reverse or mirrored on my laser printer. Then attached with some tape in position face down.
Using Acetone on a shop cloth I rubbed the paper from the back. The acetone loosens the toner an apples it to the wood. Depending on the wood you are using it works really well. You may have to rub it a couple of times with more acetone. Avoid peeling up. You can lift a corner to take a peek but, removing and trying to line back up hardly ever works. You’ll end up with a double image.
Using my trusty wood burner and the smallest point nib I have I set about wood burning the areas where toner was applied. Take your time. Detailed work can be very tedious. No reason to rush at this point I mean it shouldn’t take another 5 years. So somewhere in between.
Here is a link to my other Instructable on Pyrography/Wood Burning.
https://www.instructables.com/Decorative-Wood-Burning-Pyrography/
Step 5: Polyurethane, Steel Wool, Cure
I coated each board with Polyurethane both fronts and backs. This took some time as it was very humid here at the time (at least it wasn’t 5 years). I gave each board 3 coats allowing to dry a full day between coats. Before applying subsequent coats I made sure to remove any brush hairs that might have come off along with any bubbles or beads that may have formed on the edges.
Then I extra fine steel wool the entire board smoothing any blemishes that might have appeared from the previous coat. If any beads of varnish I take a razor blade and cut the bead down to be level with the top coat. Wipe down with a clean cloth to remove any of the loose steel wool. Or if you have a hair dryer with a cool setting will work to blow any of it away before applying the next coat.
Step 6: Assemble
After a couple days I assemble the boards to the legs with the screws. I worked from the center out. So for the seat I did the smaller boards first working outward. Then for the back, start at the bottom and then work up towards the top. It help having done a test assembly earlier as the pilot holes help make it and easier assembly. Once assembled I gave the entire piece a 4 coat of Poly. And left it sitting in my time machine to cure for another 5 years, No!!! just a week. The final step was moving it into place.
OK technically its not my back yard but I think it looks great sitting in front of my house. Its under the over hang of the front quad level and the huge Hickory tree, so it won’t get much direct weather as its in the shade 80% of the day. It’ll be great to sit out front and watch the neighborhood and yell at those kids to “HEY, get off my lawn". (Joking). Plus it’ll be the perfect spot to sit and pass out candy at Halloween.
Step 7: Placement
For added security I drilled holes in the concrete pavers it sits on and added screw anchors. Counter sunk drill holes through the feet and then screwed heavy gauge mason screws into the anchors. Hopefully deterring anyone from just walking away with it.
Its nice to finally complete a project I had plan on doing so many years ago.
Thanks for your viewing.
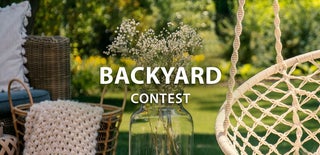
Runner Up in the
Backyard Contest