Introduction: Wine-Splash Lamp
The project constitutes the design and assembly of a desk lamp featuring the visual appearance of wine dropping from a broken bottle.
Supplies
Material Supplies
- Stereolithography 3D printer - No model specification necessary.
- Photopolymer Resin Material - Red Colour - Black Colour
- Isopropyl Alcohol - 99% desirable
- Curing Machine - Not necessary.
- E12 lamp socket
- E12 LED light bulb
- Electrical Wires - Less or equal to 18 AWG Gauge is desirable
- Power cord with switch - No model specification necessary.
- Furniture Felt Pads - No model specification necessary.
Assembly Tools
- Glue
- M2.5 x 6mm screws - Screw kit
- M2.5 screw threading - Not necessary
- Wood screws
- Soldering station - No model specification necessary.
- Solder - No model specification necessary.
- Heat Shrink - Not necessary.
- Acrylic Plastic sheet - Not necessary.
Painting Supplies
Step 1: Design
The overall design is broken down into a total of 11 components. Only components As resulted in a modified version of an already published design. All other components were custom designed using Fusion 360. The first 4 parts being A1-A2-A3-A4 are the bottom parts making a visual representation of a wine splash. Components B-C-D-E form the frame of the lamp in the form of wine dripping from the bottle. Components F-G-H form the lamp in the form of a broken wine bottle with a bulb socket inside to screw a light bulb. A visual representation of the overall assembly of each component can be found above. Further specification regarding the dimensions of each part is provided below.
Component A
Component A was broken down into a total of 4 parts which were originally gathered from a Thingiverse project. The dimension to take into consideration is the resulting trunk diameters since part B must be firmly attached to maximize strength. Although the exact trunk diameters can vary based on the type of printer used, the assembly of components A1-A2-A3-A4 was found to form an ellipse circular shape with diameters of 1.8 inches and 1.5 inches.
Component B - C - D - E
As component A must be inserted firmly within B, the lower diameter of component B is of great importance. It is recommended to first complete the printing process of components As and adjust the design of component B in accordance with the produced diameter of As. Also, component B-C-D was first designed as one component and broken down into three based on the maximum print volume of the 3D printer used. As demonstrated in the visual, a difference in diameter of 0.02 inches allowed to insert each component B - C - D - E within one another tightly. A hole with a diameter dimension of 0.03 inches was made within each component to pass the electrical wire.
Component F
Component F being the wine bottle was designed using the reference dimension of a "real" wine bottle. A written note was added on the bottle, but can easily be removed or personalized if one wished to reproduce the project. The bottom diameter of the bottle was left at 2.9 inches to allow component H to be joined firmly.
Component G
The dimensions of component G were selected based on the dimension of the E12 lamp socket utilized. As there are wide varieties of lamp sockets, one can easily modify the component to appropriately mount the socket-based on its given geometry.
Component H
The design of component H was produced with the aim of creating a visual effect of broken glass. The inner diameter was set to 3 inches to insert firmly onto component F. A diameter difference of 0.1 inches between components H and F allowed to easily insert the two-component into one another without losing too much structural integrity.
The main design file can be downloaded from --> Fusion 360 Project Gallery if one wishes to reproduce the project. Feel free to modify and improve the design of each component. Productive iteration is key to improving design accuracy.
Step 2: 3D Printing
Printing Parameters
The size of each component is limited by the maximum printing size of the 3D printer used. The Creality LD-002H printer was used for the project having printing dimensions of 130 x 82 x 160 mm. As represented in the visual documentation above, components A1-A2-A3-A4-F were printed individually whereas components B-C-D-E, as well as components H-G, were printed as a combination of parts to minimize print time. Important printing parameters for each component are elaborated below.
Components A1-A2-A3-A4
The STL files for components A1-A2-A3-A4 were gathered from --> Thingiverse Project . To maximize the size of each component without losing visual accuracy, the scale of each component was set to 18%. It is important to keep consistency in the location of the components onto the bed to ensure perfect similarity between parts. As result, the X-axis location was set to 18.00. The selection of the scale and location parameters provided can easily be modified as long as it remains consistent from one part to the other.
Components B-C-D-E
The frame components represented by parts B-C-D-E were printed together. As observed within the provided visual, a small portion of the upper diameter of components B-C was left unprinted to maximize the size of the exterior frame. Doing so did not affect the structural integrity of the components as the remaining lengths of the inner tubes were high enough to be inserted deeply within the following component. Component E was mounted on the bed from the upper portion of the component to create a small flat area enhancing the visual illusion of wine coming out of the bottle.
Components H-G
Component H was mounted onto the printer bed from the non-broken area to maximize adhesion. Component G could have potentially been printed with components B-C-D-E to minimize printing time. When space remains on the printing bed, I recommend printing components in duplicate as parts can be slightly damaged in the unmounting process from the bed.
Components F
Component F was printed as a stand-alone part. After experimenting with printing the component from the top edge of the bottle rather than the bottom, printing the components from bottom to top as seen in the visual representation was found to produce a smoother surface.
The STL file of components B-D-C-E-F-G-H can be downloaded below. STL files of components A1-A2-A3-A4 can be downloaded from --> Thingiverse Project
Step 3: Assembly
Assembling Wood Frame
By providing structural strength to the overall frame, the 3D printed components were mounted onto a wood structure. To induce appropriate horizontal levelling, 4x furniture paddings composed of wood screws were screwed at the bottom. To pass the electrical wire within the wood structure, two holes were created. One hole was drilled vertically at the center of the structure allowing the wire to pass through the 3D printed components and reach the lamp socket. Another hole was drilled on the horizontal axis of the wood structure allowing the wire to exit from the side and reach a power outlet. Standard 18 AWG gauge electrical wires were used to bring power to the lamp socket from within the frame. A cord composed of a switch was soldered to the wire exiting from the side of the wooden structure and consequently allowing a power connection to an outlet. Although any power cord can work, the cord utilized was gathered from an E26 socket assembly kit. The E26 socket was cut and replaced by a lower dimension E12 socket as further explained below.
Assembling Components A1-A2-A3-A4
To facilitate and enhance the structural assembly of components A1-A2-A3-A4, each part was glued together onto a transparent acrylic sheet cut with the same circular geometry as the wood structure. Glue was applied at the bottom and onto the side surface area of each component. It is important to leave the glue fully solidify for at least 24h before proceeding with doing any further assembly. Following the curing period of the glue, a hole was drilled in the middle of the trunk portion of the components to allow the passage of the electrical wire. I recommend using rubber bands to hold the assembly together tightly while drilling the hole as demonstrated in the picture provided. Although not demonstrated in the visual provided, the assembled components A1-A2-A3-A4 glued onto the acrylic sheet were mounted on the wooden surface using standard wood screws and a washer. Although providing a working solution, the mounting method can easily be improved.
Assembling Components B-C-D-E
As demonstrated in the provided visuals, the electrical wires were first passed through each component. Glue was applied onto the bottom and upper surface of each part and inserted into one another. Glue was also applied onto the upper trunk surface of component A1-A2-A3-A4 allowing it to firmly insert within component B. As before, leave the glued assembly for at least 24h to ensure proper adhesion of the glue before proceeding with any further assembly procedures.
Assembling Components F-G-H
Four holes with dimensions matching with the diameter of M2.5 screws were drilled at the inner bottom of component H (bottle). Zinc metallic M2.5 screw threadings gathered from McMaster-Carr were inserted within each hole. The lamp socket was inserted within component G before being screwed with 4x M2.5 x 6 mm screws within component F. Glue was applied onto the inner surface of component H before being inserted tightly onto component F (bottle). The overall assembly was left curing for 24h to ensure optimal adhesion of the glue. The electrical wires from the lamp socket were soldered with the wires originating from the inner frame to terminate the electrical connection at the socket. Lastly, completing the assembly, glue was applied to the inner surface of the bottle exit area and inserted onto component E.
Step 4: Painting
Modelling Clay
To eliminate the visual appearance of small inaccuracy between components, modelling clay was applied as shown in the visual representation. Clay was also applied at the junction of components H and F. After 24h of drying, the clay was lightly sanded with sandpaper to smooth the surface.
Painting
Acrylic paint was lastly applied to all components. A Crimson Red colour numbered A604 from Fantastory was applied to the wine dropping structure and a Lamp Black colour numbered A602 was used for the bottle portion. A total of 3 layers of paint was applied, each layer was left to dry before the application of the subsequent layer. Although providing realistic colour combinations, other colours can easily be explored.
Step 5: Result & Improvements
Potential Improvements
After several design iterations, here's below a list of potential improvements to consider if one wishes to reproduce and improve the results:
- Different post-curing techniques could be experimented with to induce a glossy finish to the 3D printed components. *
- Instead of relying on glue for the assembly of each component which minimizes portability, threading can be implemented allowing each component to screw into one another. Doing so could allow easy de-assembly to either modify or relocate the lamp.
- Instead of relying on an acrylic sheet to mount components A, the design can be modified by adding screw thread allowing to screw each component firmly onto the wooden component.
- The utilization of a real broken wine bottle could be explored instead of using a 3D printed model. The difficulty comes from breaking the bottle at the desired location with the desired patterns. Glass often breaks following unpredictable patterns.
- The wooden structure could easily be further modelled allowing it to house further electronic circuits providing features such as a USB connection acting as a phone charger.
Overall, the project was a success and the lamp was given as a gift. Feel free to improve the design by adding additional features. Ensure to share your improvements with the community!
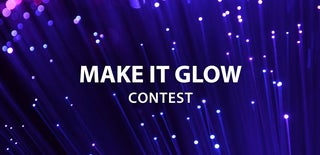
Runner Up in the
Make it Glow Contest