Introduction: Wooden Thumb Plane
This instructable focuses on the making of a small wooden hand plane of the sort that is used by luthiers and carvers known as a thumb plane or hollowing out plane. These types of planes are used to carve the intricate interiors of violins, and the curved bracing of guitars. They are a very useful tool, but easily damaged in a bag full of tools, so it's smart to make a little carrying case to protect them and keep the blade sharp. We'll be making one of those too. Let's get started.
Step 1: Deciding on the Size to Make
There are many different sizes of thumb plane, the smaller they are the tighter the interior curve they are capable of planing. The Ibex plane here has an 11/16" wide blade, and I love it's performance, so I will attempt to emulate its size in my design. The radius of the grind at the bevel is 1 1/2".
Step 2: Making the Blade
A standard mill bastard file provides the perfect size steel for a blade of this type so I measure how much I need, then heat up the steel red hot using MAP gas in a standard plumbing torch. Let the steel cool slowly, and at this point it has been softened sufficiently to be able to cut through with a standard hack saw.
Grind and sand your blade blank down to 11/16" wide by 2 3/8" long. I flatten the surfaces on a belt sander first, then a grinder and finally on stones. The radius on the business end of the blade is 1 1/2", or roughly the same as the inside of a role of duct tape.
Grind the radius onto the end at 90 degrees first, then hollow grind up to it at approximately 30 degrees. Leave a small square section at the edge so that it won't crumble when it's heated and quenched afterward.
Polish the back of the blade flat on your sharpening stones now, while the steel is soft. I like to leave just a shadow of the pattern of the file on the blade, I think it looks cool, and shows its handmade.
Re-harden the steel by heating it back up to cherry red, then quenching it quickly into peanut oil or water. At this point the steel is now too hard and brittle, so soften it just a little by putting it in the oven at 200 degrees for 1 hour.
Apart from cleaning it up and sharpening it, you now have a finished blade, so don't burn it, and grind slowly. Of course you could skip all this and just buy a replacement Ibex blade, but that's no fun. For a little extra information on sharpening I've embedded a YouTube video about sharpening from my channel.
Step 3: Selecting Wood, and Laying Out
When choosing wood for this little plane, hardness and and feel in the hand should be top of mind. Rosewoods, Cocobolo, Ebony or Jatoba come to mind, but any good hardwood will do.
The plane is made from two pieces 5" long 5/8" wide by 1 1/8" tall. These two were sawn from a single piece so that when they're glued together again the glue line nearly disappears.
Measure 3 1/4" forward from the back, and mark the location of the mouth of the plane, this is where the blade exits the bottom. Right now the mouth should be too small, so it's 1/16" wide, and the ramp on the back side is marked at 45 degrees. The forward cut is angled forward 15 degrees from square. Take your time here to lay things out on both pieces really accurately because the more care you take now, the better the results later. I find I can achieve really accurate results by laying out one side, then holding the pieces together and transferring the marks to the other side. Also mark 3/8" deep on both the top and sole of the plane to guide the depth of cut.
The blade is 1/16" narrower than the opening so that the blade can be adjusted laterally in use. Double check all your layout marks again before cutting.
Step 4: Roughing Out the Ramp
To guide the handsaw perfectly down the layout lines it's very useful to cut a small shoulder for the teeth of the handsaw to ride against when starting the cut. To make this shoulder, cut down the layout line carefully with a sharp knife and a ruler. Cut gently at first, then deepen the cut line with additional passes and more pressure. Then use a chisel to remove wood from the waste side of the cut. Saw both cuts carefully and slowly all the way down to the full 3/8" depth trying your best to stay square. This is infinitely easier with the pieces held in a vise.
I then remove 1/4" of depth from both sides using a small router and a straight cutter. DON'T try to take 1/4" in one pass with the router, take just 1/16" at a time, being careful not to touch the the sides. Always wear a dust mask when working with exotic woods.
Step 5: Making and Setting the Wedge
Now a wedge must be made that will hold the blade tightly into position. Numbers don't really matter here, the wedge should have a long gentle taper, because a short sharp taper tends to pop out during use. This wedge is about 1/16" thick at its narrow end.
Once you've made a wedge that's uniform, flat and at least 3/4" longer than the blade, place both the wedge and blade into each half of the plane in their proper orientation and with the wedge all the way forward. Hold them carefully in position with one hand and trace the profile of the wedge with a sharp knife onto each side.
Using this cut line as a guide, remove the wood all the way down to the full 3/8" depth (where the blade and wedge will sit) using a sharp knife and chisel. Forward of the cut line, the wood needs to be carved down like a ramp to open up the cavity enough to allow shavings to exit the plane. I like to leave the carved surface left by a gouge to give it the hand made look.
Step 6: Glueing the Body
At this point you should be able to dry fit all the parts together, but the blade shouldn't exit the bottom of the plane yet. Wrap a piece of tape around the blade to prevent it from rusting when the plane is glued up, and assemble the parts with the wedge pushed tightly into position. If it won't tighten cut a little off the narrow end.
Clamp it down on its side on the edge of your bench, then drill out two 1/4" holes for locator pins on either end that will help keep things lined up during the glue up. These will be cut off later.
Disassemble everything, wipe the surface to be glued with a little acetone if you're using an oily wood, and apply glue. Reassemble all the parts, with the locator pins, and clamp it together for as long as the glue you are using recommends. Any quality wood glue will work great.
Step 7: Prepare the Body for Shaping
Once the glue has dried, sand off all the squeeze out, take the tape off the blade, and cut off the ends where the locator pins are. Make sure that the ramp is flat and the blade sits evenly, adjust with files, chisels or sanding sticks to get it right. The plane at this point is still too long compared to the Ibex plane, but first the sole needs to be curved to match the profile of the blade.
Step 8: Shaping the Sole
File or chisel away the leading edge of the mouth of the plane until the blade barely exits the bottom. I remove this material at the same angle as the blade (45 degrees) so that I can trace the curve of the blade onto the wood as a guide. Remove the majority of the wood with a block plane, then with a piece of 220 sandpaper laid out on a flat surface, finish refining the curve by planing the sole on the sandpaper. When the two match perfectly, you're done.
Step 9: Setting Up
At this point the mouth should be opened up at least 1/32" and shaped to allow shavings to not get jammed into the body. The wedge should be carved to your liking but should let you adjust the blade with your fingers. The tip should also be cut back and shaped to allow shavings through unobstructed. Your little plane in now a coopering plane and will take great shavings in a straight line, but still needs more work to become a luthier's plane.
Step 10: Final Shaping
The body can now be cut down and shaped to your liking. I like to leave the knife facets from the carving because it makes the plane a little easier to grip, and it looks cool. Dome the sole by carefully carving and sanding away the wood in front of and behind the mouth opening. Don't disturb the curved edges of the mouth opening to preserve the proper radius. Use the plane often while you are doing this final setup, and you will get a clear sense of where to remove more wood to get the right feel.
Step 11: Roughing Out a Case
To make a simple carrying case, find a block of wood slightly larger than your finished plane and saw out an 1/8" bottom, a main body deep enough to fit the plane, and a lid 3/8" to 1/2" thick. Trace out the silhouette of the plane onto the body piece.
Step 12: Finishing the Box
Cut out the profile of the plane on the scroll saw slightly large so it doesn't get stuck, glue on the bottom, and locate a screw in one corner of the lid so it will spin open. The hole in the lid should be slightly larger than the screw so that it can pivot freely. Tighten the screw just enough to keep the lid from spinning. Now you're all set, so go make a guitar!
If you're interested in more about making planes, I've imbedded a video from my YouTube channel about making your own Krenovian style wooden plane. Thanks for taking the time to read this tutorial, and I'm happy to clarify any doubts you may have.
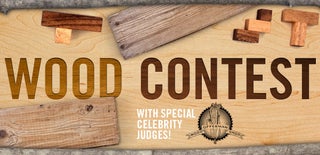
Participated in the
Wood Contest