Introduction: Creating Decorative Inlay
This instructable describes the process of making a small decorative inlay for adding something special to a woodworking project.
Step 1: Selecting Materials & a Design
For making small inlay I always save nice scraps of wood from other projects. The woods I use are usually between 1/16" and 1/8" thick because if they're too thin you may risk sanding through it. I draw out my design on a piece of paper, and depending on the complexity of it, I'll sometimes cut out the individual components of the drawing and glue them to the wooden pieces as a guide. Try to use the colour and grain to your advantage, much like painting a picture. When using these thin woods, grain direction isn't important.
Step 2: The Tools
The hand tools you need are quite basic. A small fret saw or jewellers saw is used in conjunction with a V-board for cutting out the pieces. A sharp knife is a must for tracing the outline of the pieces. Small files help to clean up the shapes after cutting, and small chisels can be really handy for cleaning out the edges of a cavity.
The only power tool needed is a small router with a 1/16" bit. I like to use a camping style headlamp strapped onto the router to light up the area around the bit.
Step 3: Getting Started
My first inlay piece is round, so I used a plug cutter for the centre part, then I wrapped it in purfling for the other colours. Purflings are the decorative veneer strips that surround guitars and violins. I carefully use CA glue, otherwise known as superglue, to stick them together.
To make the hole for the first bit of inlay to sit it, tack the components together with a single small dot of CA glue, then carefully trace the perimeter with a razor knife. I trace very gently at first because the grain, or fibres of the wood can often pull the blade off course. Carefully snap the pieces apart, then deepen the scribed line a little more with your knife.
Using your coping saw, cut very close to the line while supporting the piece in the notch of the V-board. Then use small files to get the shape just right until the parts fit.
Glue the components together with CA glue. I often use a spray product called accelerator to speed up the curing process. Sand the surfaces flush with 220 grit paper.
Step 4: Other Materials
Decorative inlay isn't limited to wood, soft metals life aluminum, brass, silver and gold can also be added to enhance the look of the inlay.
If you're inlaying something into a dark wood like Ebony, the cut line can often be difficult to see. Use a white pencil crayon or a piece of chalk to fill the cavity of the cut, making it very visible.
The V-board is very handy for cutting out and shaping even the smallest parts. Additional parts don't have to go all the way through the inlay, but should be deep enough that they won't get sanded off later when the finished piece is inlaid.
Step 5: Other Colours
If natural woods and metals don't yield the colours you want, then experiment with stains and dyes to achieve the right look. Shells are also a commonly inlaid material, and you can cut and file them with the same tools. Just keep in mind with any of these operations that protecting your lungs from fine dust is important, so always wear a dust mask.
Step 6: Inlaying the Finished Design
Once you have constructed your finished inlay picture, inlay it into your project using the same procedure previously described. Tack it in place with a dot of CA glue, scribe its perimeter, then make the recess with the router. Glue it in place with CA, then sand it flush with sanding blocks. I like to use 220 grit paper because it doesn't leave deep scratches like coarser grits can.
Step 7: Finished Product
After everything is sanded to your liking, it can be finished just as you would any other project. Some inlays are structural joinery as well, like this butterfly, to keep cracks from spreading in large slabs. I've imbedded a YouTube video from my channel if you'd like to see how I inlay those. Thanks for taking the time to read through this instructable, I'm happy to clarify any questions you have.
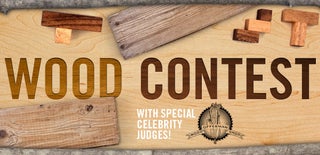
Participated in the
Wood Contest