Introduction: Abraham Lincoln Head Mold
having moved from south east Texas to central Michigan i got to experience a my first true winter .everyone here takes the snow fall for granted but to me its still just amazing and absolutely beautiful .it also became the inspiration for my tenth instructable. i wanted to make a snow ball mold. me being me .i couldn't just settle for a simple round snow ball
the day after my wife and i made it to Michigan we went to the Henry Ford Museum (i recommend going if you have the chance) where i got a plastic injection molded Abraham Lincoln head from a souvenir which i put in the window ledge and pretty much didn't pay any more attention too .until one night while getting into bed i had a flash .why not make a snow ball maker that would make the snow balls shaped like Abraham Lincoln's head
sadly i wasn't able to finish the mold in time to make a snow ball with it .however there is a slight chance of a late snow .if the stars aline i will add photos
Step 1: Materials
warning: polycaprolactone has not been proven to be food safe .but its also not been proven to be food unsafe
-polycaprolactone (polymorph, shapelock, etc)
-lincoln's head (a small bust will do)
-heat source (i use a small blow torch, boiling or water at 160 degrees is recommended)
-needle nose pliers
-wire
Step 2: Getting Started
the first bust i tried using was the souvenir i got while at the henry ford museum .i liked it because there was only one parting line .it turned out to be harder than i thought to use due to the fact i shaved off the parting line soon after i got it home
so that bust being a .well a bust .i got on ebay and searched for "metal abraham lincoln bust" i got lucky and found one for about $15 .i could see from the photos that the parting lines were still clearly visible .from the photos the seller posted i could only see three parting lines .once the bust arrived i found that there were in fact four .but i was determined to make it work
taking the bust and a sharpie marker i traced over the parting lines to make them more easily visible .i molding the back of the head first since it was the smallest of the pieces .i got over zealous and tried to make it all at once .heating a large piece and then trying to push it all in place and to its final shape .turns out thats not the best way to use the polycaprolactone .its hot to begin and will burn your fingers and cools to quickly to mold to its final shape
my solution was to heat and mold small sections at a time and i went to working on the face
Step 3: Making It More Mold Like
for this to work as a mold for more than just snow .which i saw the need for as time and winter passed .side pieces are needed to not only aline the mold but to also give greater surface area for holding in water or what have you .building the edge molding is much like building the face part itself .heating up small pieces of plastic and building it slowly and shaping so the side pieces have a place to fit up against without getting trapped on its matting piece
Step 4: Addition of Pegs
the building (what i am calling pegs) are to hold all the pieces together .the greater need for these is that with most materials polycaprolactone expands when heated and then contracts when cooling .this caused misalignments to occur and the need for these pegs to pull the mold back into shape
i modeled them kinda like little plateaus only wider at the top then at the bottom so any binding method used would not slip off prematurely .after completely making the face piece of the mold i new it no longer fit snugly i was unsure as to why .i thought maybe since i made it in small pieces it became warped heating only one side at a time .so to test this i heated the entire face piece up and and let it cool and it still did not fit snugly .so the conclusion was then drawn that it was due to expansion and contraction causing the piece to loose shape after cooling down .had this not been the issue i would have not needed any pegs to align the final mold and i was going to build a hinge system to fold the side pieces in from the back and then incorporate a pliers type hinge to bring the face piece in making a full mold
Step 5: Right and Back
this step is more just for pictures since its pretty mush the same process as the first two pieces
Step 6: Testing It Out
like i said in the beginning this was intended for snow but as its now march and i'm just finished with the complete mold .snow isnt likely. halfway threw the project i thought i felt at this might be the case so i decided that it should be able to mold other things too .so anything that could be poured or packed into the mold and solidify that i had access to was tested
first up is -ice cream
i decided that plain vanilla would be the ice cream i would try .not because it was my favorite (cause its not) but because i thought that a plain ice cream would give me the best chance of pulling it out of the mold in one piece .rather than filling the entire mold with the ice cream i decided to test it and only fill the face portion .it was a failure .eating the failure was good .tasted like freedom .it had a funny after taste of assassination though
second in line -ice
after wiring the mold together all nice and tight .i proceeded to fill it with water .and it proceeded to leak right out .so i emptied the mold of all the water .and placed it into the freezer with the hope any water remaining in the cracks would freeze and thus form a seal to hold in the next bit of water i put in the mold .but it didnt .instead it only slowed the water leaking out .the next morning morning when i discovered this i filled it with water again since there was about a fourth of an inch of water frozen in the bottom of the mold .after a few hours the water had frozen solid and i took the wires off .then i placed it back in the freezer as it tool me 3-4 minutes to undo all the wire .warming the mold and melting the outer layer of ice .i waited another hour or so then i started to remove the mold pieces .and then again places it into the freezer to re harden any melting that had occurred .then i took it out a final time to take picture you can see below
third in line -jello
mango jello to be precise .mixed up by my lovely assistant and wife .she made a nice thick mix and i left the spoons in the bowl to test to see when the jello had fully set .after having the water leak right threw and having no butter in the house i decided to try to use chapstick to seal the edges and also lube the inside of the mold .my wife then spooned in the jello mix into the mold .when i was able to pick up the bowl filled with jello with one of the spoons left in the jello i figured that the jello not only had set but it was firm enough to hold its shape when the mold was removed .but i was wrong the jello stuck to the mold and ripped apart
Step 7: Conclusions
so now that youve seen my fun its time to make your own .it doesnt have to be of lincoln .it could be of daniel day lewis .or wasington .or of yourself if you have the proper technology
a few tips for working with polycaprolactone
if you dont care about it turning brown you can use frire to melt and shape it .it will only turn brown if youre impatient and burn the stuff .it also gets the polycaprolactone hotter then it needs to be and you can easily burn your fingers when trying to work with it
adding cooler is pretty simple .if you make a thin piece of polycaprolactone then color it with a sharpie marker remelt it and then mix it all together it will color the stuff .if you want black .crushed up charcoal is excellent colorant .i have also found that eye shadow will color it .make sure that the shadow is only pressed powder and not a creme additive
and on a final note a little teaser .i did have the face part of the mold made when we received a light snow .so i decided to test it
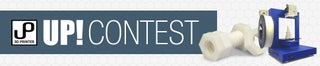
Participated in the
UP! Contest