Introduction: 10 Woodworking Tricks the Pros Use
I'm always looking for shortcuts in my work, either to save time or make my life easier. Over time, I've come across a new way to do something I've done a hundred times before and wonder why it never occurred to me to find an easier way.
In an effort to share some of my experiences in the shop, here are 10 woodworking tips that I've learned from professionals or on my own. These tips are simple yet effective ways to stay organized and efficient when working with wood. If you have any of your own tricks, share a picture of them in the comments below and help out others. Be sure to check out the second part I made based on some of the responses in the comments, 10 MORE Woodworking Tricks the Pros Use.
I hope these woodworking tips help you in your next project!
Step 1: Wood Layout - Triangle Registration
When laying out wood pieces it's easy to get them mixed up, especially when you've got multiple cuts of a similar length. Numbering the pieces and where they join is fine, but an even easier way is to use a triangular shape. When the pieces are moved, you can quickly visualize their position relative to each other since there will only be one way that triangle shape can be made when together.
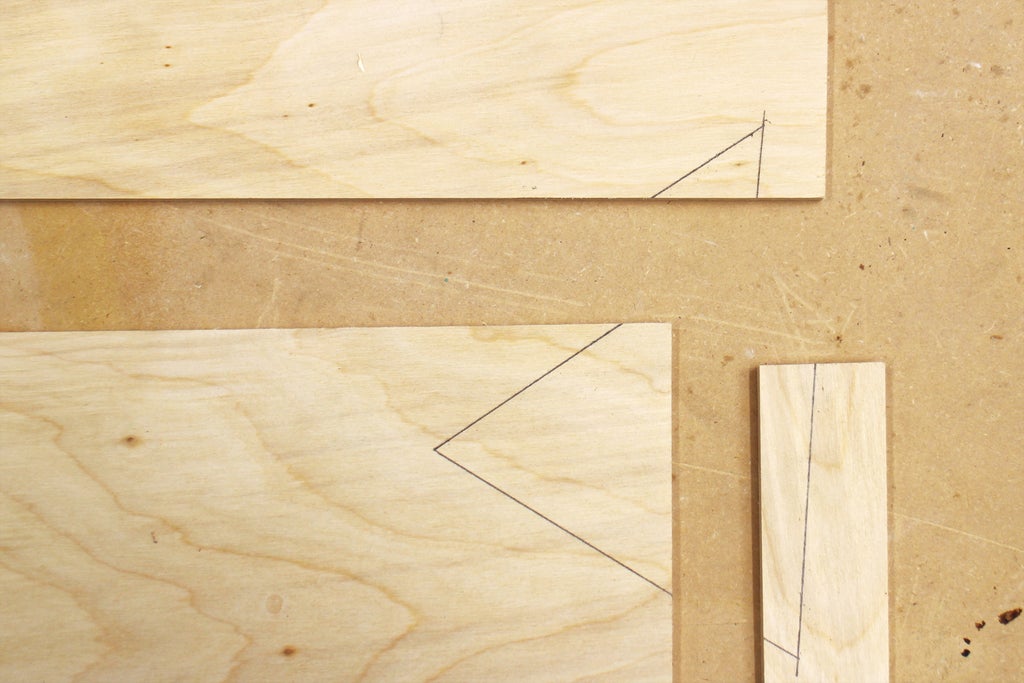
Scribe a triangle onto your wood when they are laying in the correct position, ensuring some part of the triangle hits all the pieces you want to register with each other. Using a straight edge makes this a quick and easy method to keep even the most complex glue-ups properly references.
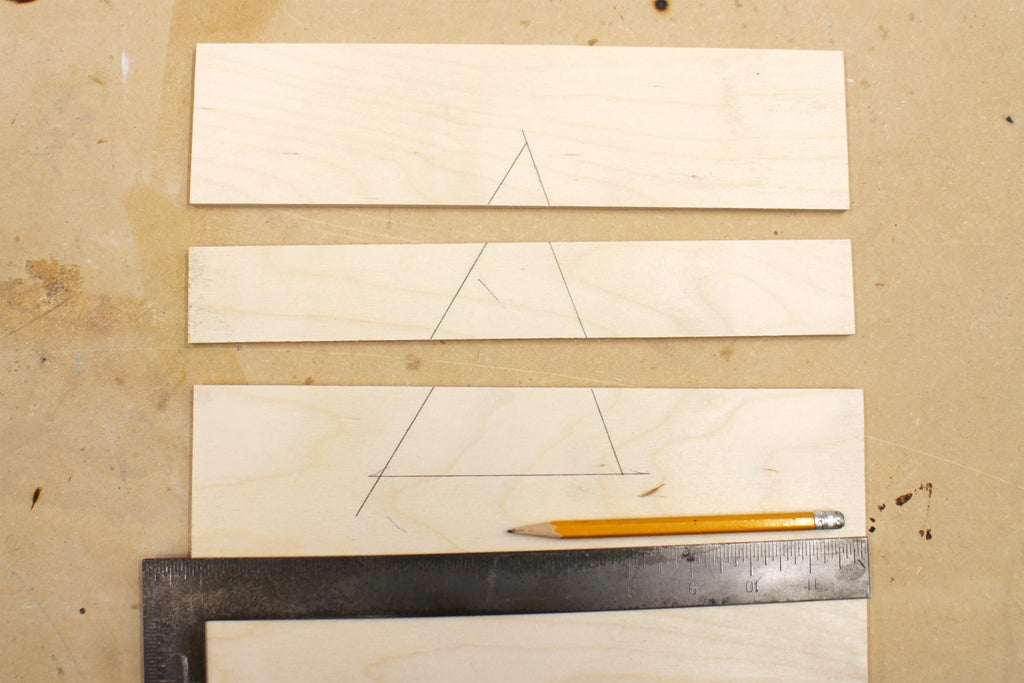
Whether you've got boards laminated together in a particular orientation, or just multiple pieces that need to be in a specific place, the triangle registration mark is a great tool to use.
Step 2: Marking Cut Lines
When measuring material to be cut I find it helpful to put a little tick mark of the side to cut on. This simple action saves countless time remeasuring and helps me account for kerf, the thickness of the blade you are cutting with.
Kerf is the divergence between the left and right sides of the saw teeth, and any cutting will result in some loss of wood that is turned into sawdust. If you just cut directly on the marked line the blade kerf would eat into your measured piece, causing your cut to be inaccurate. This may not seem like a big deal, but if you've ever had a project be a 1/8" out of measurement you know how frustrating this can be.
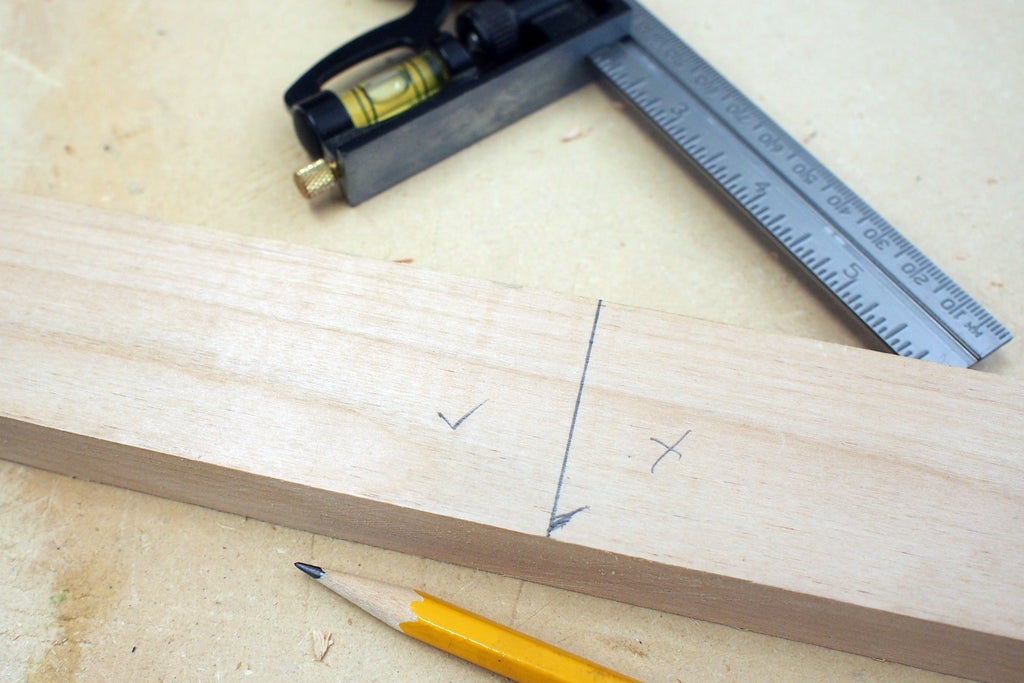
The solution is to measure your piece and make a small tick to one side of the measured line, indicated which side to cut on. Once measured, line your blade up to the line with the blade on the ticked side, so that the kerf will be on one side of the line and not into your measured area. If you ever work with a buddy and are dividing labor this is a great trick to keep each other informed of the areas to cut.
I use this every time I mark cut lines, and it's a great habit to fall into.
Step 3: Straight Lines on Dowels
Making a straight line on a dowel is something that comes up every so often and can appear to be a tough task, despite all the fancy measuring tools you may have at your disposal. However, the solution is simple: just place the dowel into any straight slotted surface. In the workshop, that can be the track of your table saw and laying a pencil against the track and dowel to create a line.
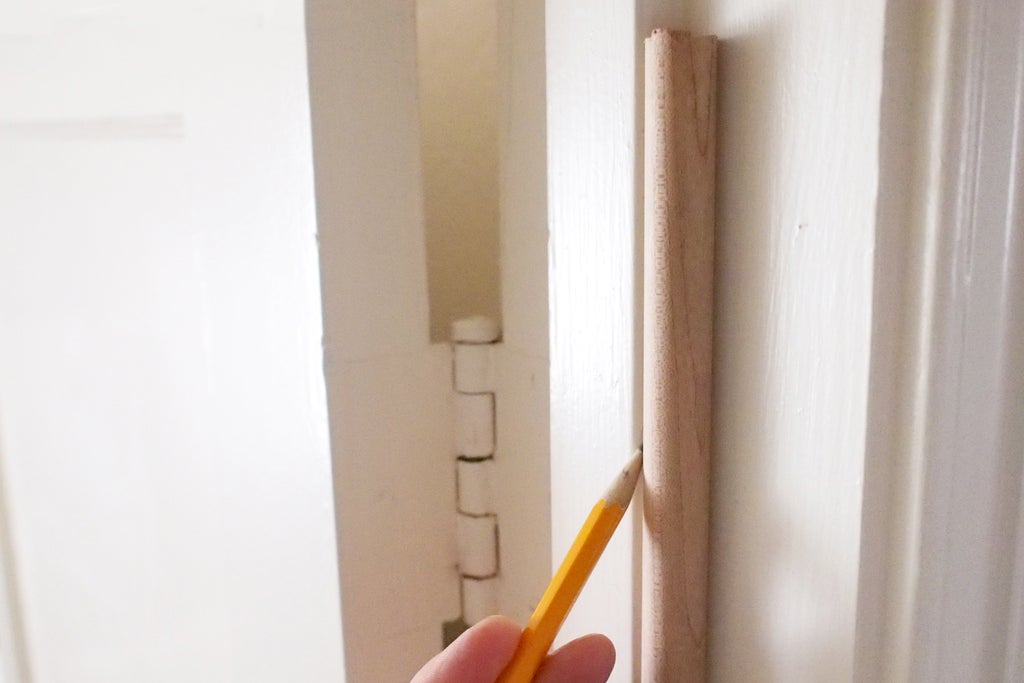
Don't have a table saw? Just use any door jamb or casing. This trick can work on all kinds of cylindrical objects you need a bisecting line on.
Step 4: Story Stick
Making accurate measurements is important but there's an easy way to cut down on repetitive measurements by making a story stick, a measured reference that can be easily made out of any squared scrap laying around.
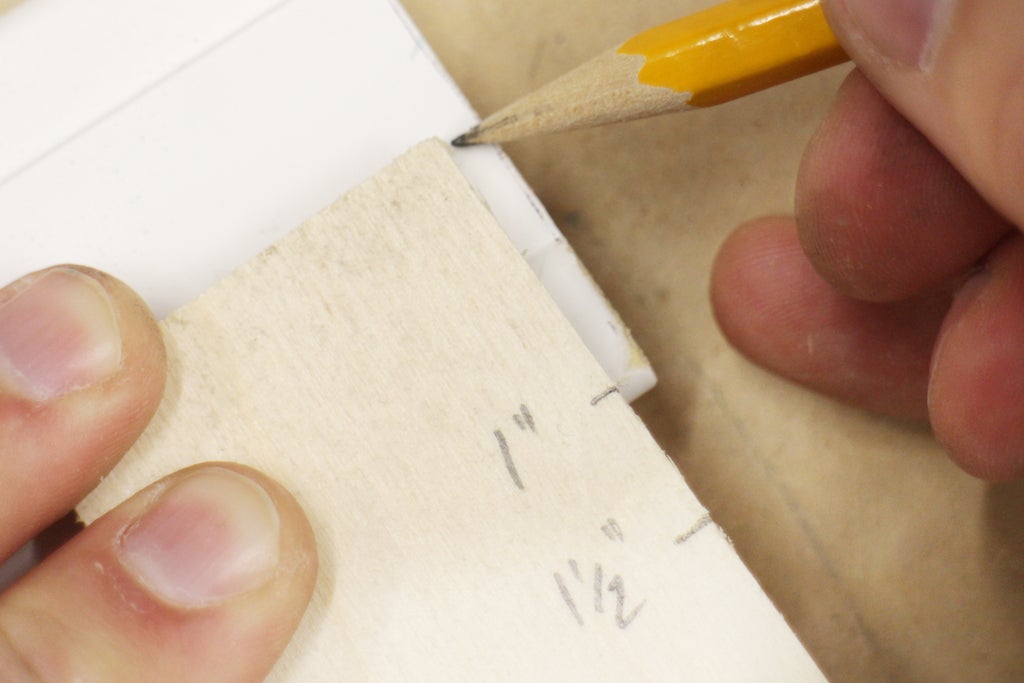
Story sticks are great because they can be as specific as you need, are less cumbersome than a tape measure, and once you have the measurement marked there's no chance of a misread measurement.
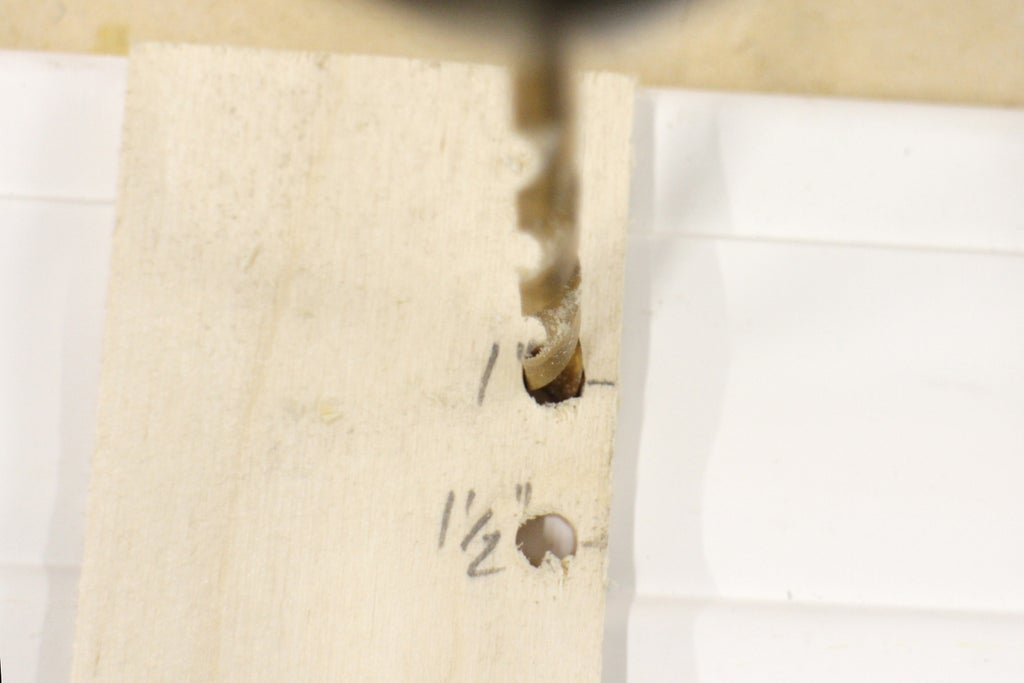
Taking this concept further a story stick can also be used from drilling holes a consistent distance from an edge. Make a story stick as usual, but this time drill an opening at the measured mark. Now your story stick can be used as a drill guide.
Step 5: Drill Depth
Not every hole that's drilled needs to be completely though the material. Though setting up stops on a drill press is easy enough, there are plenty of times when using the press isn't the best tool for the job (portability, size of material, etc.). Making a depth marker for a handheld power drill is as easy as using a piece of tape to mark the intended depth of that bit.
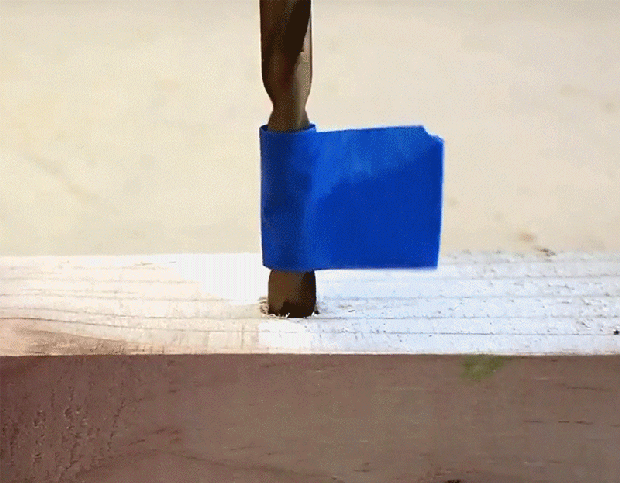
This is the same tip discussed in the Drilling Perfect Holes lesson in the Woodworking Class.
Step 6: Glue Cleanup
Glue is a great tool for lots of woodworking projects. Applying glue is simple enough, but sometimes there can be a bit of a mess. While the glue is still wet, cleanup of glue squeeze-out is as simple as applying sawdust to the glue and rubbing it around to absorb the excess glue. This is a preferable method for glue removal over a damp cloth or sponge, as moisture can cause wood to swell.
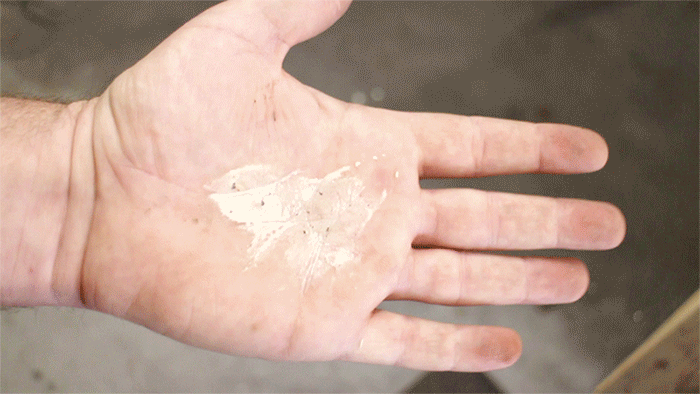
Glue cleanup from your hands is even easier. If you get any glue on your hands after your piece is secure you can easily remove it by just rubbing your hands together. Wet or still damp glue should just flake off.
Step 7: Keep Slippery Glue-Ups Steady
Not every glue job going smoothly, and sometimes wood pieces are want to slip apart when being clamped together. This is especially true if you have multiple pieces that are being glued together and secured in a single clamp. An easy fix for this is sprinkling a small amount of salt onto the glue before clamping.
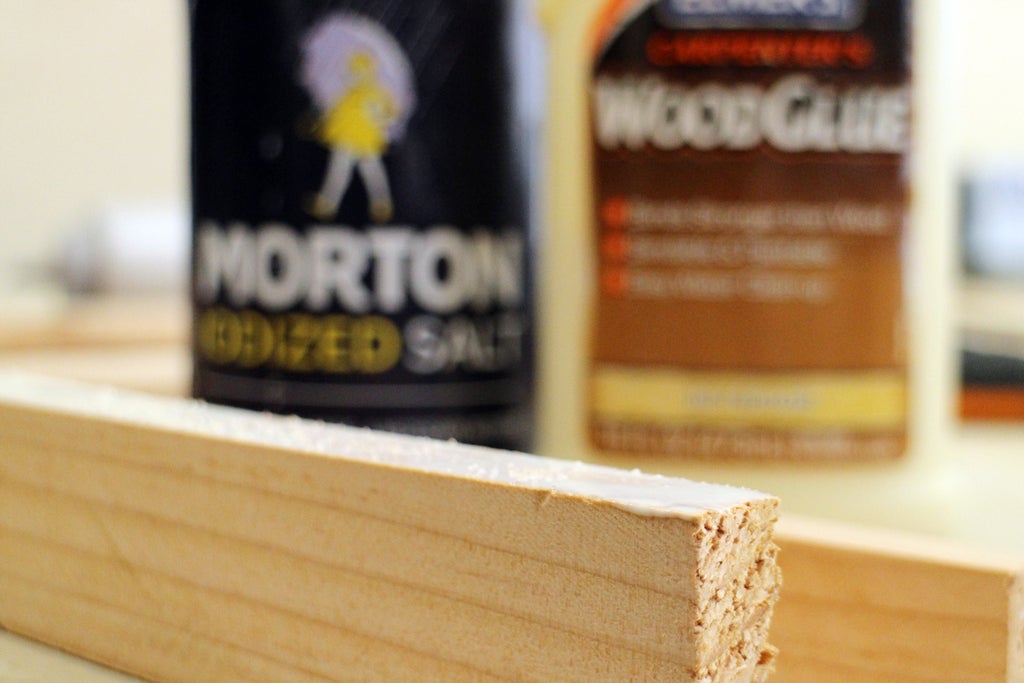
The salt crystal shape act like square wheels on a car, preventing the pieces from sliding around. In the above image I used too much salt for illustrative purposes.
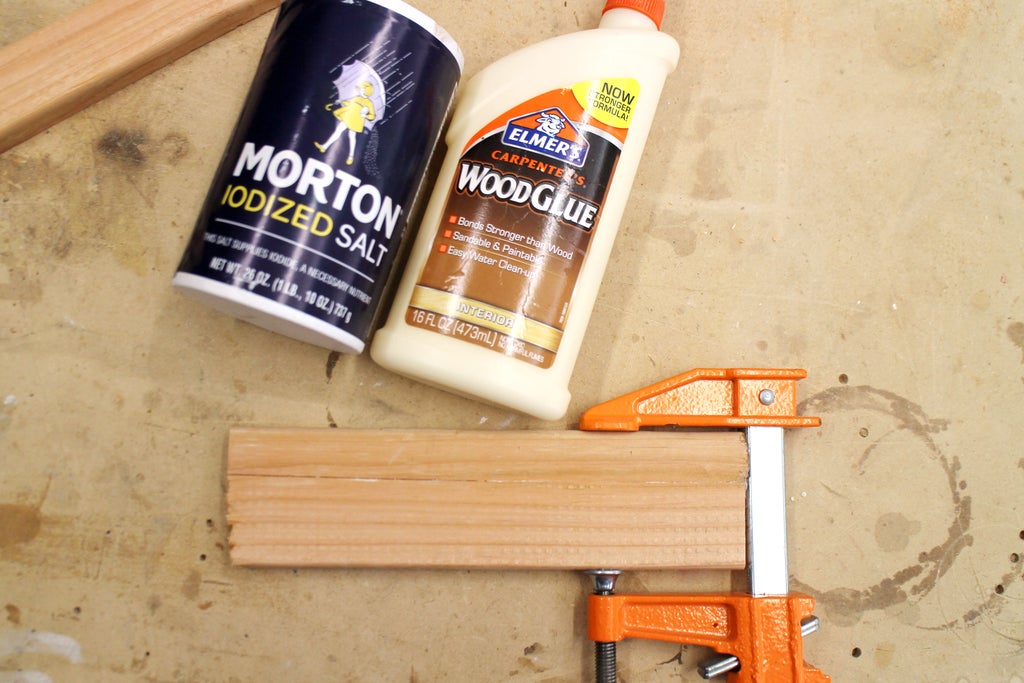
When clamping the salt is embedded into the wood and is untraceable from the outside.
Step 8: Wax Paper Cover
Accidentally gluing your work to the bench is a mistake that usually only happens once. Keeping a roll of wax or parchment paper under your glue-up will not only keep your workbench clean by catching glue drips, but will also prevent your work from sticking to the bench while it's drying
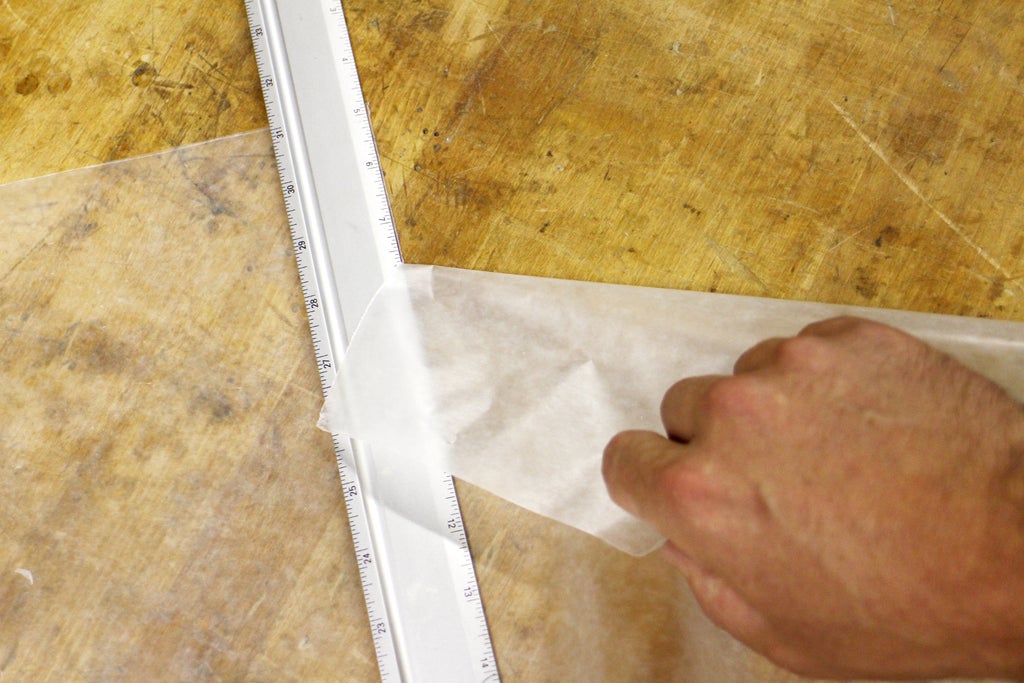
Rather than use the serrated edge on the roll, I find it easiest to unroll more wax paper than I think I'll need and trim it to the specific shape once it's under the work. A shop ruler works great for ripping a clean edge on the wax paper.
Step 9: Hold Glue-Ups Instantly
Sometimes a clamp just won't fit into where I need to hold a piece during a glue-up, and sometimes I'm too impatient to wait for the wood glue to set before needing to move on to the next part of the build. In cases like this, hot glue is a great crutch to use with wood glue and hold the glue-up instantly.
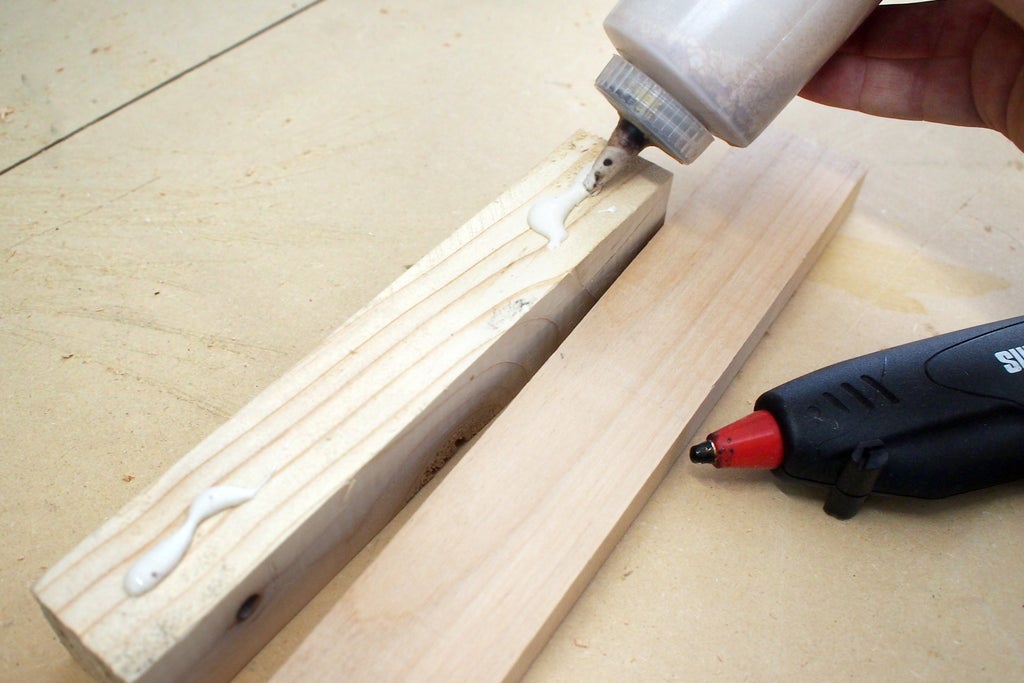
Plug in your hot glue gun and let it come to temperature before applying any wood glue. Once your hot glue is ready, apply wood glue as usual but leave small gaps every so often in the piece to be glued.
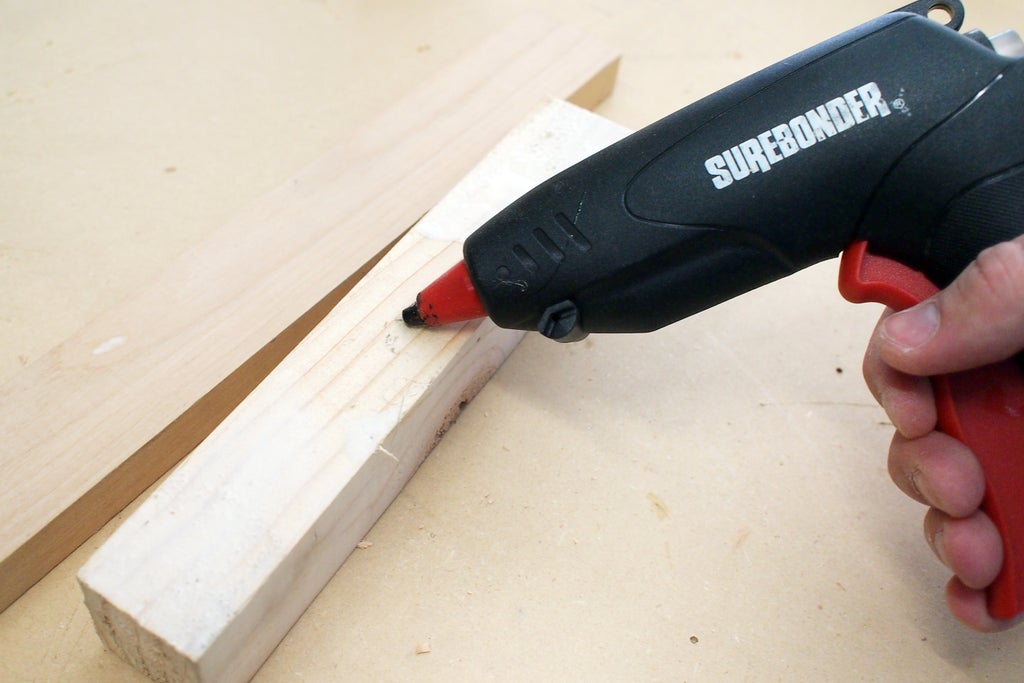
Once your wood glue is applied add a squirt of hot glue in the gaps of wood glue. Before the hot glue has a chance to set, join the wood pieces together and hold in place for a few seconds. The hot glue bonds the two pieces together with enough strength to keep working, and holding the wood in place until the wood glue can take hold and make a stronger bond.
Step 10: Sandpaper Organization
I have all kinds of abrasive paper on hand, just in case I need a specific grit or type. As such, my sandpaper storage was a mess. Since almost all sandpaper is the same size as printer paper, I keep it all neatly organized in an inexpensive accordion-style file folder.
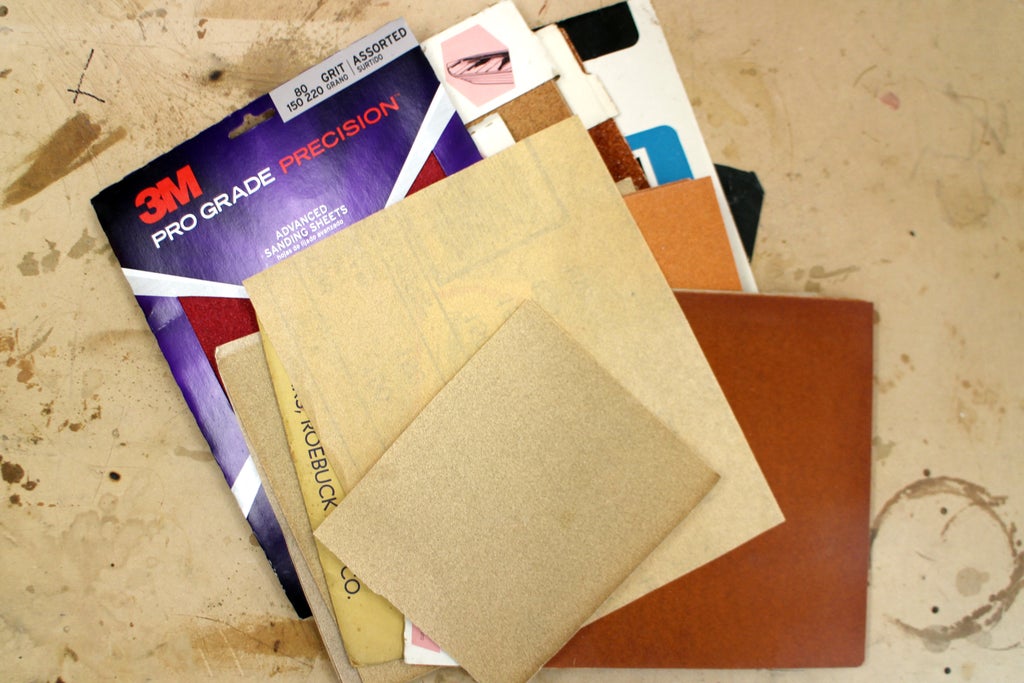
I pulled all of my sandpaper out of it's packaging and sorted it by grit. Each grit has it's own slot in the folder, with the front pouch reserved for smaller scraps of sandpaper.
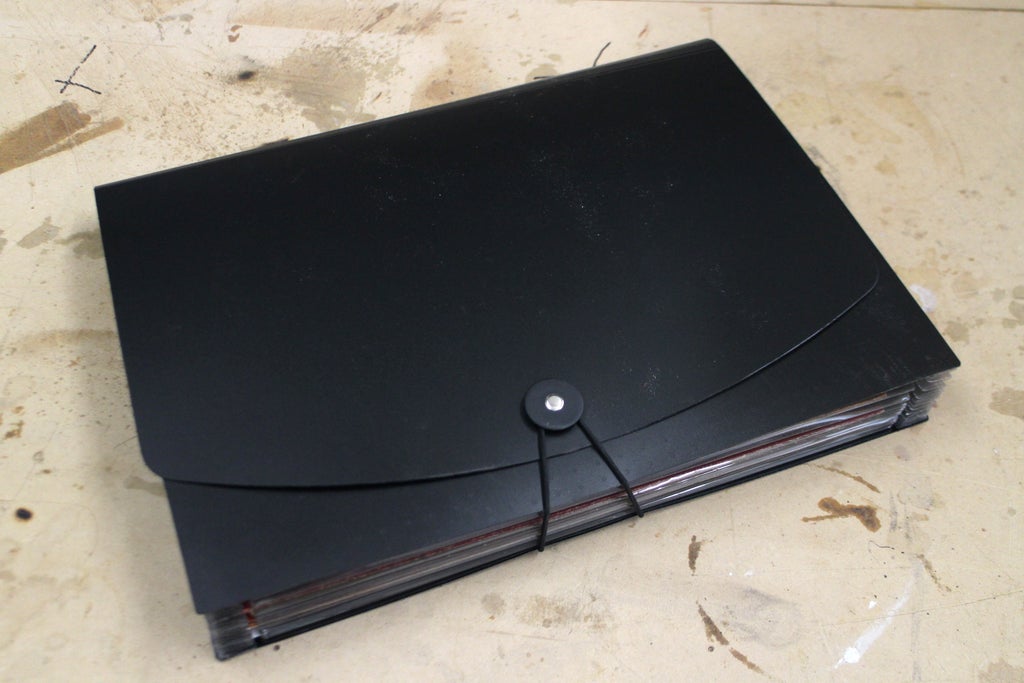
Now my sandpaper is all in one place, and I can just grab the folder and bring it to my work and have all the sandpaper I could ever want.
Happy making! :)

Do you have your own woodworking tips that keep you productive or organized? I want to see them!
Happy making :)