Introduction: 20' Geodesic Dome Greenhouse
Geodesic Domes are awesome. This Instructable will show you how I built a 20' dome for about $250, with the majority of that cost being the greenhouse plastic ($167 with shipping.) That's right, the structure itself cost less than $100! I will also write about what is wrong with this design, how it came about, what I learned from it, and what you might want to do if you're building your own.
Buckminster Fuller wanted his dome houses to be cheap, quickly constructed, and portable. Yes, your house was supposed to be able to be picked up with a helicopter and dropped off somewhere else! The Marines experimented with it in the 60's. There are pictures of domes being flown around.
My purpose for building domes is the same as Bucky's: to save humanity from extinction. We are currently building houses the same way as we did thousands of years ago. Bucky said we would adopt his new technologies only when it was absolutely necessary. Well, the time has arrived. Here is why YOU should be living in a dome:
1) They use far less material than a square building
2) They are much stronger, domes have withstood hurricanes and tornadoes, even a nuclear blast
3) They use less energy, the oft quoted amount is 30% less, but it goes up as the dome gets bigger
I am submitting this as part of the "Win A Home Fabricator" contest. If I had had one when this started, it would have shaved days off of construction and lots of frustration. My next dome will be made out of bamboo, and hopefully use home fabricated vertices (the connectors between the wooden struts.) So if you like this Instructable, please rate it highly so I can make a better dome next time, and work toward that goal of saving humanity from itself.
Step 1: What Type of Dome
There are many choices in dome construction. I chose to build a 3/8 3v dome to keep the complexity low. This is where the 'designed on a computer" part came into play.
First, I used a program called Dome Designer to play with raw material lengths. It is very useful in calculating the amount of scrap that will be produced, and letting the user experiment with different dome frequencies and sizes. Unfortunately, it has a tendency to stop working, and then needs to be reinstalled in order to start again. Part way through the project, it stopped accepting my license key, and the creator never returned my emails. I wasn't about to spend another $100 on a program that doesn't work, so it was back to the web. In the end, everything I needed was online. The scrap length didn't matter on a dome this size anyway, so it was no loss.
The design tutorial that comes with Dome Designer was actually one of the most useful things I got out of my $100. In it, they point out that most domes are overbuilt. People making a house are used to using 2x12" boards, and think that it should naturally be the same with domes.
This is not the case. The stress that is put on dome struts is actually tension, instead of compression. Picture a drinking straw, standing vertically. Now put a stack of books on the straw. It immediately bends over and drops the load, breaking if it were something like wood. But what if you were to suspend the books from the straw? It could hold them until the end of time. This principle applies to domes, all of the force exerted on the struts is pulling, not squishing.
That's why I built this dome out of 1" (which is actually 3/4" in the real world) sticks, weak and many cracked. I wanted to see if they could hold up. More on the results of that later.
These are the most useful online tools I used:
Desert Domes has a number of great resources, the Dome Calculator and Reverse Dome Calculator being my most used. It is helpful for figuring out the length and number of struts, and number of vertices needed for different frequencies of domes.
Then I used this diagram during assembly.
Dome frequency is basically the number of triangles that exist in the dome. The higher the frequency, the stronger the dome, and the more complicated and more materials you will need. The one pictured is a 3v (frequency 3) 3/8 dome. The 3/8 means it is 3/8 of a sphere, so you can imagine just cutting the top 3/8 off a baseball, and that's what it will look like.
Step 2: Parts List
Dome's need struts and vertices. The struts are the "bones" of the structure, the vertices are the connectors between the struts.
Strut raw materials:
25 1"x6"x4' scrap boards I got from the lumber mill at pulp prices: $5.00
(I actually bought 50, and didn't use half of it)
Strut construction tools:
Table saw
Chop saw or similar for cutting them all to the correct lengths
Drill (press preferable, the press you see here takes a hand drill)*
7/8" hole drill bit * ($12)
Vertex raw materials:*
20' of 3/4" (inner diameter) hose (I got this as scrap)
46 2-1/2" machine screws and corresponding washers and nuts (about $30)
Vertex construction tools:*
Hose cutters (I got cheap ones, and they were dull by the end) ($14)
Hose smashing press (we made it, see pictures)
Drill & bit for making the hole for the machine screws to go through
Covering
Greenhouse plastic from GreenhouseMegastore I bought 32' x 75', which is enough for 2 domes. Total cost per dome $167
32' is just enough to go all the way over and have a tiny bit hanging on each side.
Other
1" Wood screws and a cordless drill* ($15)
Props - At least 8' long, for propping up the dome during construction
2 Rolls of duct tape ($15)
*All starred items could be eliminated using printed vertices, as well as saving a lot of time. So vote me up so I can Make better faster stronger!
Step 3: Make the Vertices
Please vote up my Instructable so the next one I make can have this whole step replaced by one that uses a home fabricator!
Originally I planned on ordering parts from these guys, but they emailed me and suggested using hose instead. It was a fine experiment, and it worked on the cheap, but next time I want:
Less time spent on vertex construction
Not to have to dowel the strut ends
To be able to snap struts in and out of vertices at will, thus allowing me to disassemble the whole thing easily.
But that's for next time, here's what to do if you're making it out of hose:
I made the hose lengths 8". With the struts only going in 2", this was too much. Make them 6" and your whole construction process will be a lot less floppy. (You can try 5" too, but I don't know if it will be too short.)
Now to make them.
There are three different types of vertices to make, 4 connector, 5, and 6. For 5 and 6, use 3 hoses. You'll just ignore one end on the 5's. For 4 connectors, these will be on the ground. You will either need to cut two ends off, or make two of the hoses "one sided" from the start.
First, cut your hoses to length. For 2" doweled ends (which is determined by the length of your hole bit,) I recommend trying 6", but you might be able to get away with 5" lengths.
Next, use a press to smash the hoses, 3 on top of each other, and drill a hole through them big enough for your machine screws to fit through. Drive the screws through with a hammer.
Flip, press again so the screw comes out on the top, and apply your washer and nut. Tighten some, but not so much that you can't adjust the angle of the hoses.
These are now complete. Load them up and get them to your construction site!
Step 4: Make the Struts
First, we took the boards and ripped them to be 3/4" x 3/4" x 4'. This took several hours with two of us, but we also did twice as much as was necessary. Stick with 25 boards.
Next we'll need to determine strut length. We'll work with 4' boards and you can adjust if your doing a different size dome. Add the length of hose in the middle of the vertices, the part that doesn't have any wood in it. If you are doing a 6" hose, and have a 2" hole bit, each end of the strut is in 2", and that leaves you with 2 inches to add to your strut length.
So our 4" strut will actually be 4' 2" with the extra empty hose.
Go to the reverse dome calculator and enter 4.166 (4' 2") and choose strut C (the longest one.) It will give you the length of all the 3 different strut lengths, and how many of each are necessary. Now subtract those 2" of hose to arrive at your strut lengths.
A 3.521 = 3' 6 1/4" - 2" = 3' 4 1/4"
B 4.067 = 4' 13/16" - 2" = 3 10 13/16"
C 4.166 = 4' 2" -2" = 4"
As the chart says, you need 30 of A, 40 of B, and 50 of C.
The number of struts will always be the same for a 3v 3/8 dome, the only difference is length. So if you make a smaller dome, you'll use the same number of struts, they will all just be shorter.
I chose for longest one to be 4' because that was the length of the boards I bought. As you can see, only strut length A had very much waste, and I was able to make some of those out of boards that had ends break off while ripping them.
Make sure to clearly mark the different lengths, this will save you later!
The following could be eliminated by using home fabricated vertices that can take square struts.
Next we have to dowel off the ends of all the struts.
First use the drill press to round the ends of the struts. Be careful, the stick will be wobbly, and the drill bit will hurt if you get yourself!
After that you have to trim of the corners that are still on the struts. We used the chop saw in a way that is probably not recommended by the manufacturer. If you're doing this, be careful!
Step 5: Begin Building Your Dome!
This took us three tries. Hopefully you'll get it in one. See the last sections for more on disaster.
First, print out a diagram. It may be confusing, so I've also uploaded some pictures to help.
In the pictures
A = Red
B = Blue
C = Yellow
Notice that B is the edge of pentagons and hexagons. A is always the inside of pentagons, and C is always the inside of hexagons. That's it!
Lay out the bottom ring first. It's going to be in a pattern of CCBCCB all the way around. It will be 15 pieces. Connect them with your 4-way connectors, leaving them pointing up and a little in, toward the middle of your dome. Make sure the top of the machine screw, the rounded end, is on the outside of the dome to prevent your plastic from tearing later. Attach each strut to it's vertices with duct tape.
From here on, it will be useful to have at least 3 people.
Start building the lower ring of triangles. As you can see from the photos, what you are really building is the tops of a hexagon, then the bottom of a pentagon, then the top of a hexagon, etc. Use props to keep it upright. You won't know how far in they are supposed to tip until you are getting close to connecting the last piece with the first. At that point, the ring of triangles will probably be stable. Now screw the vertices to the struts, trying to keep all sharp edges on the inside.
Step 6: Finish Your New Dome!
This can be the hardest part, it certainly was for us. The first two failed attempts at raising the dome took place at this stage, and were a result of using duct tape without screws, and not having enough props. Make sure you have those props!
At this point, you're just going to keep working around the dome, building each ring of pieces. Prop up behind you as you go. Have one person running the drill while the others assemble.
At the top, you'll need chairs or stepladders to reach. What we found to be very easy was to make the top pentagon on the ground as just the center vertex with five loose struts sticking out (only A's, no B's around the edge, these were already up top.) Then we lifted the "star" up and just popped all the struts in place. Suddenly everything was very stable, and we were done!
You should go back and check your machine screws. Make sure the heads are on the outside, so the plastic won't tear. Tighten up any that have loosened.
Step 7: The Greenhouse Part
It's pretty easy to slide the plastic over if all of the machine screw heads are on the outside.
Once the plastic is on, it shouldn't take long before your dome is a sauna. I had water running down the sides in under an hour. This is probably out of optimal for plant growth, so you'll have to add some ventilation.
There are several options. You could simply remove the plastic in the morning and let the plants be outside during the day, replacing it toward the evening.
Another option is to make large windows on the sides, maybe adding a fan.
Buckminster Fuller had domes on the equator of Africa that were cooled only through airflow. They have vents with small holes, like a screen, at the top, and large open vents at the bottom. Air is drawn out through the bottom and forms a twisting column of rising air, that forces a smaller, inner column to be rapidly drawn in through the small openings at the top, cooling the air through the Bernoulli effect. The picture is from Bucky's book Critical Path, which is... well, critical to our survival.
I like this last option because it uses no electricity. To keep it lightweight, you could poke holes in the top, and make an extra flap that velcros over them when you want to close it. How you'll reach it without taking it down, I don't know.
Let me know what you come up with. The reason I haven't done it yet is revealed in the next step.
Step 8: Lessons Learned
Don't Rely on Duct Tape
I would have had wood screws holding it all together a long time ago, but the cordless electric drill I was expecting still hasn't show up. This has caused no end of duct tape failure, even though I splurged and bought Gorilla tape, extra wide. One or two a day go out, and I am regularly repairing it. When I put the plastic on, the inside got hot and wet fast, and tape was failing all over the place. Which brings me to:
A Catastrophic Failure Isn't Catastrophic
When enough pieces are pulled out of the vertices, the whole thing slowly folds in on itself. Usually pieces don't break, although they have at times. The nice thing is I can usually put the whole thing back up in half an hour, even though it looks so bad my neighbor was certain I would have to take it down completely and start from scratch. The way it collapses, once the edge of a triangle gets to the ground, that triangle becomes another base holding the whole thing up.
If you are having to fix some problems like this, start at the bottom, replace and re secure one by one, and you should be fine. Although once it's screwed together I doubt many of you have these problems.
Strut Strength
I'm happy with the performance I have gotten out of these 3/4" boards. Lots were destined to break right from the start, and we broke them before even getting to construction phase. Some broke during construction, usually because someone was moving it from the middle, and it had a lot of weight on both ends. The interesting this is that once they are in place and secure, they are very strong. It's only when force is applied in the middle, perpendicularly, and the dome isn't in a position to shift with it (like when it's already part way collapsed thanks to the duct tape!) that they break. It will be interesting to see what happens when I've got the plastic on, the pieces screwed together, and a high wind shows up. I'll let you know.
Tensegrity
I wouldn't have found out so much about this if I hadn't had to deal with a half dozen collapses. When putting it back up, I noticed that the force is all pulling, and there is quite a bit. It's no wonder that the duct tape is failing, because the dome really seems to want to explode outward! It's pretty cool, and I think it will make it really strong once I have it secured.
Don't Splint Struts
The part above the door sags a little, and my friend and I wanted to correct it for aesthetic purposes. We duct taped an unused strut between two others to give them both some lift. This was a bad idea, it seems to have stopped those struts from being able to move around and flex the way they are supposed to. During a high wind, one of them broke, and since it was near the door I now had a huge hole, causing the whole thing to slowly implode. Fortunately, I had a spare half hour to fix it.
Build on a Level Surface
Seems obvious, but evidently it wasn't for me. I wanted to put it in it's eventual destination right from the start. The unevenness is tolerable, and maybe I could build their next time, but on a first run it just added enough complications that it wasn't worth it.
90% of Build Time Can Be Eliminated
With a home fabricator, or prefabricated vertices, I could have eliminated all of step 2 and half of step 3. These supposed super pieces would have also eliminate any duct tape and screwing from steps 5 and 6. Finally, they would allow individual pieces to be easily removed and replaced. The whole process would have consisted of ripping the boards (actually we're using bamboo next time) and construction. It will go from a week long project, to several hours. So the lesson is, once again, I need a home fabricator, so please rate this Instructable!
Thanks for digesting:)
Step 9: Epilogue
After the dome sat near my hillside garden for some time, I decided to move it over the garden in order to protect from cows.
Over time, the dome shifted a little down the hill, putting stress on some of the struts, and snapping them. Slowly, over the course of a few days, the upper part of the structure folded in on itself. It started to look more like a bunch of pyramids. I wanted to see the full course of destruction, so I let it keep going. It basically just broke into smaller pyramids over the course of a month, until finally, it become a bunch of triangles on the ground.
I learned that these small struts will work until they receive pressure on the middle of the piece. My next dome is going to be a lot bigger. It will be using 2x6's anyway, and that won't be a problem.
I also learned not to let my dome slide down a mountain :)
And finally, all future domes (including this one when I repair it) will be built from the top down, as Buckminster did. We will build the top layer, then hoist it into the air so we can work on the next. Each layer is hoisted as it is completed, allowing us to always work on the ground and also not deal with floppy walls. Buckminster was able to make huge, 200+ domes in two days with this method.
Thanks for reading!
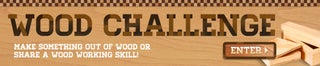
Finalist in the
Woodworking Challenge
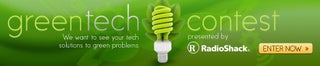
Participated in the
Green Tech Contest
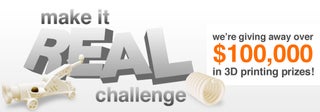
Participated in the
Make It Real Challenge