Introduction: 2x4 Work Bench With Nested Rolling Assembly Table
This ible shows my creation of my new workbench for my shop. I wanted to replace the old bench that was built by my grandpa after he built tbe building.
The old bench was 10 ft long, 23 inches wide and 34 inches tall. It was pretty solid and worked fine but I wanted something bigger and custom built for my purposes.
My new bench is 12ft long, 32 inches wide, and 38 inches tall. it has a large span between the legs to hold a rolling assembly table that is 32 inches wide and 6'6" long and 35 inches tall. The assembly table also has retractable caster wheels so it can be moved easily and stay put when I want it.
Step 1: Plans and Materials
I get a lot of inspiration from pinterist and lumber jocks. I have seen a few nesting table designs that really appeal to me for both function and space saving design.
I wanted the assembly table to be 34.5 inches tall to use as an out feed table for my table saw. My shop has a row of outlets approximately 38 inches off the floor. To make the assembly table fit under the workbench I had to use 2x4s for the frame. I would have preferred 2x6s but 2x4 work great.
Step 2: Workbench Legs
I started by making both ends legs. I waited to make the center leg until the top of framed.
To make sure all peices are cut to the same length I measure the first peice then use it as a guide to cut all remaining peices. I lay the guide on top of the peice I'm cutting and slide it flush to the saw.
I like to make 90 degree L shape legs. They have as much area as 4x4 post legs but I feel the L shape is more stiff on 2 axis.
You can see I made the vertical supports stick up past the horizontal cross member to attach the horizontal table top supports too. Also on the back vertical support you will notice a cleat (small peice of wood to help support vertical load) to hold up the back horizontal table support.
Step 3: Horizontal Table Top Joists
I laid the legs on their side and attached the 12ft. boards to the raised portions on the legs. I also ran a 12 ft board across the bottom to help hold the legs from spreading apart.
Step 4: Finish Table Top Frame
Next I flipped the table back upright. Then I cut and installed blocks in between the edges of the horizontal members.
Next I added the final horizontal members. In total there are 4 12ft. 2x4s each spaced about 7.5 inches apart.
Finally I added blocking across the entire length of the table. Blocking is just peices of wood set perpinducular to the main horizontal members. I offset them slightly to be able to screw into each side easily.
The blocking makes the entire top more solid by transferring load to multiple horizontal members. Making and installing blocking is a long boring step but I feel it really pays off.
Step 5: Middle Leg and Shelf Support
These photos show the design for thr middle leg. It basically follows the same design as the outer legs using L shaped concept.
You can also see the horizontal cross members that create the lower shelf. The L shaped legs lend easily to making a shelf by just running support boards each direction of the L.
The shelf is set just high enough to fit some old wood drawers underneath that I will attach small casters too so they roll in and out easily.
Step 6: Assembly Table Frame
I used the same L shaped leg design for my assembly table. I kept this design KISS keep it stupid simple. An L shaped leg at each corner then horizontal peices at top and bottom.
Then a horizontal member spanning the length of the table on the top and bottom.
Step 7: Retractable Caster Wheels
I like caster wheels to move things around in my shop but I also need things to stay put when in use. I really don't like most brakes on caster wheels as they don't always work great. I found a few different people using this design and I cannot take any credit for it nor could I find anything stating who originally made it but it's pretty great and easy to use.
The design uses 3 hinges to create moving caster blocks and a stop block. The caster blocks move down when the table is lifted up and once they are down far enough the stop block swings down and holds the caster blocks in place. Pull the stop block out and the caster blocks move upwards dropping the table onto its legs.
I used a story block to mark the exact same height line on each corner. I also was out of lag bolts so I just used double screws on each corner of the caster screws. I know it's not right but it works.
Step 8: Assembly Table Top
We had a 36 inch wide solid core oak veneer door from a restroom break at work. Fun story a kid locked himself in the bathroom and a female employee who weighed a whole 120 pounds soaking wet broke the door down instead of calling me for help opening it. She cracked it where the door knob hole was. I ripped it down on the table saw to 32 inches and that removed all the damaged bits.
I laid the door down and set the table frame on top. Then I squared it up and set the edges where I wanted them. I made the frame smaller than the top so there would be a couple inches overhang to make clamping things to the table easier.
Once I had the frame positioned I used leftover 2x4 peices to outline the inside of the frame. I then screwed them to the face of the door, then screwed the frame to the faced attached 2x4s.
Step 9: Attach the Plywood to the Top of the Workbench
I had already test fit the 3/4" plywood top but I had not screwed it down fully yet. To make sure I didn't miss a horizontal member I used chalk lines. Also at this point I installed the lower shelf.
Step 10: Finished
Here are some photos of thr finished product.
Some fun math lol
The old table had 120"x23" = 2760 square inches surface or 19.1 square feet area VS 144"X32" = 4608 square inches or 32 square feet table surface. That's 13 square feet more working space on just the workbench.
The old bench did have shelves underneath. The shelves were a little smaller than the table top but my new one has shelves as well. So I have close to 13 square feet more shelf storage as well.
The old bench also let me store some stuff on the floor but the only things on the floor were the 2 drawers I put casters on for this project so I didn't really lose or gain anything there with the exception of the wheel assembly table that creates and other 6'6"x32" = 2496 square inches or 17 square feet of table top working area. The assembly table is almost as much area as the original bench.
So total new working area 17+13 = 30 square feet more working area totaling 49 square feet working area and 32 square feet storage area plus the area on the floor under the shelf.
I worried before I started that replacing my grandpa's simple small bench may not have been worthwhile, but now I know redoing it my way makes it much better and more useful. I hope he is proud of the upgrade.
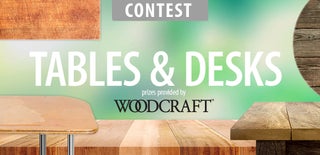
Participated in the
Tables and Desks Contest 2016
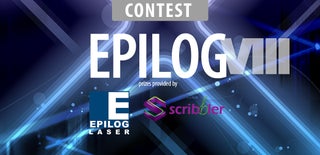
Participated in the
Epilog Contest 8