Introduction: 3D Printable Designer Sunglasses
To find the right sunglasses that fit your face is not easy. So I set myself the challenge to, using a consumer-level 3D printer, create a custom pair of sunglasses. My goal was to have a model that is customizable, very low-cost, with an original design, and can be created in a single print. After a week of development, the results were successful so here is a step-by-step guideline for making your own pair, using 3D software of your choice. I have used Solidworks for 3D modeling, and an Ultimaker Original for creating the 3D print.
Step 1: Design Approach
The glasses can be fully 3D printed if you use a louver design. I chose to create custom lenses by applying a special window film to a thin transparent plastic sheet. The window film is Opal film supplied by Haverkamp GmbH, and the plastic is an ultraclear polypropylene (PP) of 0.6 mm thickness supplied by Milliken. You can also have your lenses laser cut by Ponoko– they have a polarizing sheet material of 0.030” thickness and 38% light transmission, which works great for sunglasses. Because I am using a sheet as a lens, the design of the lens frame will need a groove that the lens can snap into.
To minimize overhanging areas that result in inaccuracies in the 3D print, the model is entirely built up flat from the print bed. I created a specific bridge element that connects to the frames with lap joints that need some reinforcement with superglue (cyanoacrylate). The separate parts allow you to print the entire model in a single run, as well as paint them in different colors. The hinge for connecting the temple to the frame is fully integrated and requires a specific design which I will explain later.
Step 2: The Spectacle Frame
First we sketch an outline of the frame incorporating the general dimensions. For the top and outer curve I use arcs, for the bottom and inner curve I use splines. Arcs make it easier to constrain the sketch, though it is also a design choice.
Then to round the frame, I create a different sketch and import the previously created base sketch with the ‘Convert Entities’ command in the sketch toolbar. Then I add the roundings. The reason why I create a new sketch is to maintain the base design for easy modification, since adding roundings in the original sketch may remove some of the constraints.
We extrude this frame drawings to a thickness with a minimum of 2 mm. Add at least 0.8 mm on each side of the lens material you will be using.
To create the groove to snap the lens into, we create a plane with an offset at least 0.8 mm from the base plane, a sketch offset 0.5 mm outwards from the last created sketch, and Cut-Extrude this up to a depth equal to the thickness of your lens material plus an added clearance of at least 0.2 mm to account for inaccuracies in the 3D print. I also added a fillet to the edge where the lens snaps into the frame to make for an easier fit.
Step 3: The Joints
The joints we use are lap joints – in a cut through view one part will partially overlap the other. The overlap can be strengthened with glue. We will be creating square shaped laps and not for example dovetails because this way we can slide the joints together and use the compressibility of the plastic, so we get a better fit even though there will be inaccuracies due to the 3D printing process.
First let’s set up a basis for the squares. We offset the outer contour of the frame where the bridge will connect to 4 mm, and the horizontal lines with a linear sketch pattern. Then in a new sketch, we use the Trim Entities tool with setting ‘Trim to Closest’ to create the squares that will be cut out of the frame with the Cut-Extrude tool, halfway into the thickness of the material.
Then to create the positive side of the lap joints we create a new sketch on the top surface of the frame, offset the previously created squares to a clearance of 0.10 to 0.15 mm (see what works best for the material you are using), and extrude this with setting ‘Offset from Surface’ into the square cavities of the frame using the same clearance value.
Step 4: The Bridge
With the top of the frame as a basis, we draw the sketch for the bridge. Using Convert Entities, we copy the outline of the frame into the current sketch. Then draw the centerline of the glasses – there should be about 12 mm space where the bridge rests on the nose so the centerline is 6 mm away from the outside of the frame. Connect the converted sketch to the centerline with arcs that are tangent to the frame, and have their center vertically aligned with the centerline. Trimming away the excess entities will result in the outline for half of the bridge. It is a good idea to now use the Mirror feature to check your design.
We can create nosepads for more wearing comfort by starting a sketch on the top of the bridge. Offset a part of the inner curve of the bridge to at least 2 mm and make it about 10 mm tall. Then connect it to the bridge and extrude it to 8 mm.
You can finish the bridge shape with fillets and chamfers to your liking.
Step 5: Hinges
The hinges will simply be thin parts that connect to the temples. This is called a ‘live’, ‘film’ or ‘integral’ hinge and design parameters are very specific to each material. Usually only PP is a suitable plastic for such a hinge. I found through my research that it is possible to create a durable hinge through 3D printing PLA because 1. There are quite supple yet strong PLA filaments available, the best one being Biome3D from 3DOM and 2. Because of the composite structure of 3D printed plastic it is possible to align the filament strands in a way that creates a workable hinge. The best hinge is created with 3 layers of filament, the first and the last layer being printed in the horizontal direction and a layer thickness of 0.15 mm.
Step 6: Temples
The overall dimensions for the temples are given above.
Other than that, you can create a design to your liking. Extrude the temple to at least 2 mm. You can add a logo and a chamfered edge all around will give a nice finish to your 3D print – better than a fillet because the stepping lines created by the layering of the print will be equally spaced. You can add a 3D embossed or debossed logo as well using the Combine feature.
Step 7: Make It!
Add all parts to your print bed, but instead of one include two bridge parts. The nose pads are small features that require proper cooling, and printing multiple simultaneously allows them to alternately cool down enough. In addition, set your fan to turn on just above the height of your frame – if your slicer software allows - to cool the nose pads further.
When the 3D prints are done you can opt to reheat them a bit above a flame to bend them into shape. Then you can finish them with spray filler, spray paint and varnish. Snap in the lenses and you have created your first unique pair of 3D printed designer sunglasses!
Using flexible PLA such as Ninjaflex you can create thin pads to glue onto the bridge as well for extra wearing comfort.
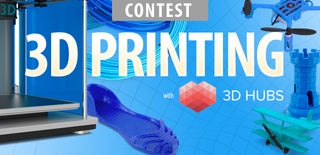
Participated in the
3D Printing Contest 2016
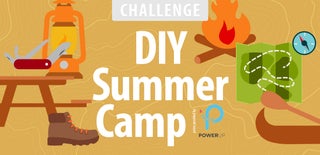
Participated in the
DIY Summer Camp Challenge