Introduction: 3D Router: When a CNC Machine Is Overkill.
The idea arose after dealing with the difficulties and loss of time in preparing for certain CNC jobs. Sometimes I spent more time preparing for the CNC than the work itself. With this manual router, you can make holes or mill very fast. A 43mm Clamping Collar makes it very versatile and you can change the milling tool to drill very fast.
There are certainly lots of wooden router table and CNC router plans floating around in cyberspace. What makes this project noteworthy are the feature set and the cleverness of how it’s all put together and designed for maximum versatility. This router table can be used as a 3-axis drill press, sanding station, a 2D router, and you can do simple shapes 3D milling via a reference model. Using a series of accessories, you can also cut circles, straight-cut squares, and cut to a 2D reference model.
The uses of this tool are varied. I am a guitar maker and my plan consists of devising several templates of guitar bodies and necks to be made with the 3D Router, without switching on my CNC. Besides, it can also be used for other woodwork tasks. I have tried to make a design which can be easily built, with rather simple and cheap. Check out the Youtube video.
- Overall dimensions: 800mm high, 740mm width and 700mm depth.
Useful dimensions: 425mm in X Axis, 535mm in Y axis and 185mm in Z axis.
What You'll Need:
- Woodworking tools
- A sheet of 18mm thikness plywood (2500x1250mm)
- 32 ball bearings (608)
- 5 Lineal meters L perfil of steel (1mm thikness)
- 500mm steel piper, 10mm exterior diameter and 8mm inner
- A lot of M8 and M6mm metric screw
- A lot of M8 and M6mm Washers
- A lot of wood screw
Number 23 Metal spring 140 x 22mm
You can also check out my website! www.paoson.com
Epilog Challenge:
This tool would be very useful for Luthier jobs, to engrave truss rod covers, pickguards, picks and other guitar parts, even to engrave my logo.
Step 1: Designing the Project.
I have designed the project in Autocad, a 3D model which I made several construction layouts for. Plans are available on my website. Parts of the layout can be life-size printed; you can paste them on the plywood and cut, or just use the plans as a reference and then measure, as I usually do it.
Step 2: Starting the Project.
Using my homemade Router & Saw table to start this project. Making this tool requires great precision and considerable experience in woodworking. Cuts should be perfectly straight and square. They must be axis parallel and well aligned, to avoid bumps on bearings, otherwise, the tool will start vibrating.
Step 3: Assembling Table and X Axis.
Finish cutting, sanding and prepare all the pieces according to plans. Then, start assembling the axis metal profiles (L-shaped). They must be made of iron or steel. I've used aluminum, but, as it is softer than the bearings, a groove can be made on the metal profiles, which after long term use may cause width . You can glue it or screw it preventing the screws from touching the bearings. Use a rule to leave them paralell and straight.
Step 4: Finishing X Axis and Beginning Y Axis.
Once the X-Axis bench is assembled, start with the bearings of this Axis, as you can see on minute 2.45, we must enlarge the 8mm hole in the direction and areas that are marked on the plans to adjust bearings to the metal profile, to prevent width. Use dowels to reinforce some parts that require more strength.
Step 5: Continue Assembling Y Axis.
When the Y axis frame is assembled, before starting with the Z axis, needless to say that this frame should be perfectly square so as to faultlessly slide along the arms of the X axis. So far, we have done most of the work!
Step 6: Finishing Y Axis.
Assemble the bearings that go along the Y axis frame and test the Z-axis bearings before mounting this part on the machine. Cut and test the Z axis spring.
Step 7: Starting Z Axis.
Continue with the Z axis, assembling all parts. The 43mm Clamping Collar should be very exact, do it with the right drill bit or a CNC. Make sure the milling machine is well fastened because it might come off with the vibration.
Step 8: Assembling Z Axis and Accessories.
End the Z axis with the actuating lever and other accessories such us the elevator control, fast clamping sleeves and the axis brakes, whish are also made from 18mm plywood. We must also finish the guideway and the worktable.
Step 9: Ending Z Axis, 2-3D Followers and Circles Follower.
This is the end of the 3D Router project. Finish the Z axis and the 2 and 3D followers. The parts that fasten these followers must be very firm and secure. Use glue and screws.
Step 10: Electric Guitar Body on the 3D Router (part1)
Before starting this project, I install a block on the Z axis in order to mill from the rear, without having to pull the lever, which is very useful for certain pieces of work with the 2D Follower. I made the templates in a CNC for the 2D contours y for the 3D top of the guitar. If you do not have a CNC, I recommend that you order them from someone who has them. They could also be made by hand but, if it is done accurately, some good templates may be used to duplicate a job at any time! In this situation, we could also use a real guitar as a template. I made two bases of 700x350x10mm on MDF in order to hold and locate the pieces to be worked on.
Step 11: Electric Guitar Body on the 3D Router (part2)
The bearing of the 2D Follower must have the same diameter as the router bit, or install a smaller bearing if you are looking for a bigger milling cutter than the one in the template itself. The depth of each pass on Z axis depends on the material and the work tool. As you can see in the video at 2'50 min, the 2D Follower can be used from ahead or from the back. Personally, I prefer from the back because I feel more at ease with the template.
Step 12: Electric Guitar Body on the 3D Router (part3)
I lower all the elements of the Y axis, bringing the milling cutter close to the piece to be worked on. Then, I adjust the height of the touch probe in order to use the 3D Follower. As I am going to lower the cover by passing several times on Z, I first leave the milling cutter at a slightly higher level than the touch probe. In the last pass, these heights must be identical. As with the 2D Follower, I prefer milling from the back because I feel more at ease with the template and it is less dangerous.
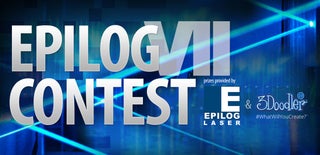
Runner Up in the
Epilog Contest VII