Introduction: 40W Bluetooth Portable Speaker (Improved Version!)
Hey everyone! Today I'm going to show you how I built this portable speaker! After nearly 2 years of research, designing and testing, I have come up with this design. It puts out 40W of power from it's 2 tweeters, woofers and passives, has the latest Bluetooth 4.0 with smart features, long lasting lithium ion batteries, all wrapped up in a stylish plywood body. In this Instructable I have made links to all the parts, and in depth instructions on how to wire and assemble it all.
Specs:
- 2*20W Yamaha Amplifier
- Bluetooth 4.0 with onboard battery indicator and ground loop isolation
- 3S Lithium Ion battery with protection and easy charging
- 20W Woofers with tweeters + passive radiators
- 4 hour battery life @ high volume, 8 hours medium volume
How does it sound? It trumps most high end factory made speakers like the Bose Soundlink Mini, see the video below for proof!
So what makes this speaker stand out from other DIY speakers?
- This speaker has built in ground loop isolation, which eliminates interference noises coming from the Bluetooth module, which most other DIY speakers suffer from. This speaker has 100% clean sound.
- Smart monitoring; so you can see the battery charge of the speaker from your phone.
- Uncompromising Bass; this speaker has been cleverly designed to put out a very impressive sound, which puts it ahead of a lot of high end shop speakers
- The parts used can be found cheaply and reliably
- The speaker is fully disassemble-able, it can be taken apart just from unscrewing the components.
- Long lasting battery life and convenient charging options
Step 1: Parts List
UPDATE: Unfortunately several parts that I used in this build have been discontinued! I've redesigned the speaker to use different drivers (it now uses much more compact high quality full range drivers), but everything else like the amp, batteries and so on haven't changed. Here's a link to the parts for the new redesigned, simpler, and cheaper version (It has the same sort of sound quality and same power output). I've made a kit for the parts to make things simpler if anybody's interested, there's more info on the changed parts over here:
https://www.etsy.com/ie/listing/467986351/new-spea...
- 18mm Plywood
- 3mm Plywood
- If you're laser cutting, you can download the laser cutting files here. If you want the parts laser cut, but don't have access to a laser cutter, you can send me a message, and I'll do what I can to help out.
Step 2: Designing the Front and Back Panels
The design for this enclosure was inspired by layers of stacked wood. From the outside, the speaker looks like it has been built by stacking 10's of layers of wood together, but in fact, it was built using 3 pieces of 18mm plywood glued together, followed by two 3mm plywood panels on the outside. I designed this enclosure so that it's about 2.25 liters in capacity, which is perfect for this driver/passive radiator configuration.
Making the front panels:
The quickest way to make the front panels is by laser cutting them. Here's a link to the laser cutting files. The laser cutter I used couldn't take wood thicker than 3mm, so I had to layer 2 pieces on top of each other for strength, followed by strips of MDF for extra reinforcement. All the wood in this project is glued together only using wood glue. The front panels have holes for the tweeters and woofers, as well as a service hole to access the electronics. The back panel has holes for the passive radiators, and small holes for charging and a switch.
If you're designing your own front panels.. I would recommend including a service hole like in my designing, as being able to have easy access to the electronics is crucial in case something goes wrong/needs adjusting.
Step 3: Making the Side Panels
Next up we're going to make the side panels. These are made out of high quality 18mm plywood. Each layer on the plywood is about 3 mm thick, with a thin veneer on the top and bottom. I would recommend using a very high quality plywood, as the inner sandwiched layers are more likely to be solid and tightly packed. On cheaper plywoods, when you cut them thinly the layers split/fall apart. For these pieces we will only be using a jigsaw and a drill with a hole saw drill bit and a wood drill bit.
- We'll start by taking our front panel pieces and tracing the shape on to the plywood. We will then draw an inner shape, about 8 mm in, possibly more or less, depending on skill level and quality of the plywood (you'll get an understanding of it quickly)
- Next up, use the holes aw drill bit on your drill to create 4 holes on the inside of the shape, so that the edge of the hole saw cut lines up with the inner drawing on the wood. This gives us a sharp inner curve, and a hole to stick the jigsaw into.
- Use the jigsaw to cut the inner shape out.
- Lastly cut the outer layer, and round the curves at the side.
Step 4: Gluing the Side Panels
The side panels are simply glued together using wood glue. Use plenty of glue. Sandwich them together and put a large weight on them/clamp them to keep them tightly together while they dry.
After the piece is fully dry, we can use a jigsaw or a table saw to shave down the sides to get them to perfectly align with each other. You can also do this by sanding it down, but it will take significantly longer.
Once they dry, coat the inside with a thick coat of wood glue. This is essential to prevent air leaks once the speaker is assembled.
Step 5: Preparing the Back Panel
Now it's time to glue the passive radiators on to the back panel. Passive radiators are an alternative to a bass reflex port. They allow us to extend the frequency range of our speakers, in a more compact enclosure. They require no power to operate, as they simply work off the air pressure within the enclosure (ie. when the driver moves outwards, the passive moves inwards). Therefore it's extremely important to make sure your enclosure is 100% airtight when complete.
We will glue the passive radiators in place using a super glue gel.Super glue gel is better than super glue for this application, as it's not as rigid, and allows minimal movement, unlike normal super glue.
While we're at it, we will also add several strips of MDF to the back using the same glue, in order to make it harder to bend. Any vibrations within the enclosure will spoil the sound.
Step 6: Positioning the Electronics
As you can see in the pictures above, there are a lot of electronics to fit inside this enclosure. It's important to plan out your positions for the electronics before you start making anything. Make sure everything will fit! It's also important to select the best positions of components that may need to be serviced/inspected later on down the line.
In this design I decided to place the components so that I have very easy access to boards like the amplifier and bluetooth module. Other components like the crossovers may never need to be inspected, so I have placed them further away from the servicing hole. The crossovers are positioned directly underneath the cutout for the right woofer, so if I need to access it I can unscrew the woofer and access it. The other components are directly underneath the service hole, which also gives me easy access.
Step 7: Electronics Schematic
Here's a schematic for the electronics used in this project. If you use the parts linked on the parts list step, it's pretty simple. All you'll need is a soldering iron and solder (and maybe some cable ties to clean things up afterwards). Measure out the lengths of cable you need in relation to how you're positioning your components. The less excess cables the better.
If you're new to speaker building, or would like a better understanding of how the components work, read on. Otherwise you can skip the electronics steps.
Step 8: Understanding the Battery Pack
Safely using lithium ion batteries confuses a lot of people. But in reality it's quite simple. There are 3 things that you need for a lithium ion battery pack:
- Lithium Ion battery cells
- Battery protection board
- Lithium Ion Charger/charger board
Buying good lithium ion cells is important.There are plenty of fake cells online for sale in both China, America and Europe. The easiest thing to do is to find a reliable genuine battery type that sells quite cheaply. A great example of this would be Samsung's pink 18650 batteries. Since they're so cheap, Chinese companies don't bother creating replicas because the original ones simply cost to little for it to be worth their while to design something cheaper. As a result, you end up with genuine battery cells by Samsung at a cheap price.
The next thing you need is a battery protection board. These circuit boards will protect your batteries from over charging, over discharging, short circuiting and more. The exact safety features vary a bit from board to board. Battery protection boards are an essential item, as lithium ion batteries are very sensitive, and need specific conditions to work under, or else you may run the risk of the batteries dying/catching fire/exploding.
Lastly, a lithium ion battery charger is important. These chargers send power to the batteries to charge them, but will also cut off/reduce power depending on the battery pack's voltage. It's important to make sure that your lithium ion battery charger IS a charger, and NOT just a power adapter. A lot of the 'chargers' listed on eBay are in fact just power adapters. It's important to check the reviews and the item descriptions, as you definitely don't want to get the two mixed up.
If you would like to understand more about charging/managing lithium ion batteries, I've written more about them here. See steps 3 and 4.
Step 9: Wiring the Battery Pack
Before we start assembling anything, it's important to make sure that the battery voltages for each cell are exactly the same. Any difference in voltage will confuse the protection board and potentially kill the batteries when charging. If the voltages are slightly off, you can use one of these circuits to charge each battery individually, so you can get them all to exactly the same voltage.
Once the voltages are balanced, we can start work on the battery pack. This battery holder is worth getting, as it keeps the batteries neatly one place. I would recommend replacing the wires on them though, as they're too thin to transport the power that we need.
Follow the schematic from earlier to wire up the battery protection board, as well as the switch and charger. Make sure you wire the charging jack the right way around!! See the image above as reference. The right pin (bent) can be removed. The middle pin is for positive power, and the left pin is for ground. Plug the jack into your charger and check voltages with a multi-meter before connecting it to the protection circuit to make sure you have it wired correctly.
Slot in the batteries and make sure that everything works. If it does, you can clean up the wires a bit by tucking them on the underside of the battery holder using tape.
We will now also add in the voltage step up converter. Once the inputs are connected, using a multi-meter, measure the output connectors to see the voltage output. We want to adjust the voltage output to 14v. We do this by getting a small screwdrivers, and twisting the copper screw on the PCB, until we reach 14v. It's exactly the same operation as this, except on a slightly different board.
Step 10: Wiring the Bluetooth Module and Amplifier
To save space and keep everything in one place, the Bluetooth module has been stacked on top of the amp. If you plan on doing the same, make sure to leave a decent gap between the amp's PCB and the BT Module's PCB, as they both need airflow to cool down, and you run the risk of short circuiting if they're touching each other. I glued the BT module on top of the amp's capacitors using hot glue. If you already have a Bluetooth Module that you would like to reuse from a previous build, that runs off 5V, I would highly recommend attaching this Ground Loop Isolator to the power inputs of the Bluetooth module, as it will eliminate unwanted ground loop noises created by the Bluetooth chip.
The Output from the BT module can be connected to the Input of the amplifier. If you would like to connect function buttons to the Bluetooth module, now is the time to do so. Simple push to make switches, wired as shown in the photo is perfect.
Connect the amplifier to the output of the step up module. That means it will receive 14v. Connect the BT module to the input of the step up module, which will result in an output between 10v and 12.6v, depending on the battery voltage. The ranging voltage means that the BT module can monitor it. If you one of the newer android versions, you will get a notification next to the BT symbol on your phone, showing the battery life left in the speaker. The Bluetooth module will work down to about 10.5v, which works quite well with the 3S battery configuration. Do not connect the BT module to the 14v power supply, as the maximum voltage that the BT module can take is 12.7v.
Step 11: Wiring the Crossovers
Now it's time to connect the crossovers. Crossovers split the audio into high and low frequencies for the woofers and tweeters. Once they're connected we can glue them in using hot glue, along with the other components. We can also glue in the switch and charging jack. Pay special attention to these, as it's important to get them 100% airtight. Use your hot glue smartly!
Step 12: Gluing the Side Panel
Now it's time to glue on the side panel. Put a line of wood glue around the edge of the back panel, and then clamp the side panel on.
After it has been left to dry for a few hours, add a layer of hot glue on the inside of the joint. This is to ensure that it's airtight, and to add more structural rigidity.
Step 13: Making the Front Panel
We can add small bits of MDF wood to the back to add more structural rigidity. Now we can glue in the tweeters. Since they won't be moving, we can just use hot glue. Solder on wires for connecting it to the crossovers, since this won't be possible once the panel is glued on. We won't screw in the woofers just yet. We can do that last, after everything is glued and wired.
Add a bead of glue along the front panel, and clamp it tight and leave it to dry.
Step 14: Closing Up the Enclosure
Now that the glue has dried. we can wire up the remaining woofers. Once wired we can screw them in. Give it one final test, and if everything works, then you can screw on the final plate over the servicing hole.
Lastly, we can sand the outside, and add a clear coat stain over it to keep the natural look of the wood.
And just like that, the speaker is finished! If you would like to, you can add a cloth and plywood speaker grille to the front by layering up a few more pieces of 3mm plywood, and then gluing a cloth to the underside of the top layer.
Step 15: Further Reading/inspiration for Speakers
- I have written several other Instructables that you can check out, which may give you more ideas.
- My Facebook design page is a great place for inspiration. Recently I added a special section where people can add their designs to the page for everybody else to see, ask questions, and make new friends.
- Sites like Etsy may give you some interesting ideas. Etsy focuses on handmade/vintage items, which means that they have a nice lineup of crafty items.
- Youtube is also a great source for inspiration.
Thanks for reading this Instructable, and I hope that it will help inspire you to create something amazing. If you have built any speakers, feel free to comment below and show them off. I'd love to see them! :)
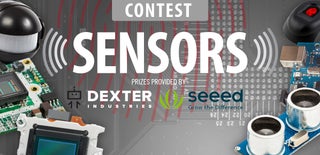
Runner Up in the
Sensors Contest 2016
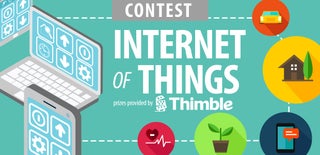
Participated in the
Internet of Things Contest 2016