Introduction: A Better Vacuum Chamber
If you look back upon my previous work you will find that I have been experimenting with vacuum metal deposition.
I have been attempting to vaporize metal and have it coat glass under a vacuum. There will be more on this once I get the process working flawlessly.
Ideally this is done under a very deep vacuum using a diffusion vacuum pump.
I am attempting to do this without the use of a diffusion pump.
The vacuum chamber that I have been using is showing signs of melting and burning which to say the least is less than ideal for the task at hand.
The first problem is the type of material used for the chamber base. The second is in dealing with the heat generated and the third is the vacuum seal.
I have come up with a solution to all three in the most unlikeliest of places...
Step 1: SAFETY!
This experiment has some risks that you should be aware of!
The first is that it is not electrically grounded. It is best to not touch the chamber assembly while it is operating. This experiment uses a variable transformer connected to a step up transformer(240V 15A).( these are not shown here but will be discussed in another Instructable)
The second is that the glass jar shown is not safety rated for a vacuum. It is a very thick wall preserving jar. If you want to try these experiments it is best to have a vacuum shield while running under a vacuum. Mine was removed for the pictures.
The third is that the first time you see metal actually bonded to glass you may become addicted!
Step 2: Out With the Old
The original base was constructed from a thick piece of ABS plastic that was drilled and sealed with 2-ton epoxy resin.
The electrical components were brass rod and brass screws.
The element shown is a 3 wire tungsten pre-formed piece from Lithuania (eBay)
As you can see after several heating cycles the base is charred and melted. The epoxy shows signs of cracking.
Not to mention that the .190 Torr vacuum took over 30 minutes to achieve, despite using a 6CFM 2 stage vane type pump.
The electrical connections are clamps to the brass rods protruding from the side.
All that this base now produces is a pre-layer of soot thereby preventing the adhesion of metal to the glass.
Step 3: The IDEA!
I have to admit it took me quite a while to sort out how to achieve an electrically insulated vacuum seal through a metal plate.
Then it hit me! A non resistive automotive spark plug!
The plug needed slight modification to be able to connect the electrics to both ends.
I chose to braze a 10-24 brass nut to the business end of the plug and use the plug wire connector end as a raised connection for the chamber element.
First carefully cut some if the threaded end off to expose the ceramic core jacket. This will allow for the space to braze a nut to the copper core.
place the nut and plug in a vise as shown the braze the nut to the core as shown.
It might be a good idea to make sure that the plug and nut combination still has 0 resistance with a multimeter.
Step 4: Get the Materials
I chose to rummage through the scrap bin the the local metal recyclers.
For a vacuum chamber, the ideal material is stainless steel.
I found various pre cut shapes and flanges.
The main plate is a 6 inch square plate the riser is an exhaust pipe reducer and the flange is a SCH 40 pipe flange. Total cost $1 per pound.
Step 5: Plan and Drill
I needed to make room for the electrical connections and possible future connection to a diffusion pump. (should I choose to).
The center hole needs to be large enough for rapid vacuum and small enough to provide a stable working surface. I chose a half inch drill for this.
The spark plug holes need to be 9/16 inch for a frictionless fit. make sure to leave enough room between the spark plugs and riser pipe for electrical insulation.
Use a small bit first and relatively slow speed. gradually increase bit size, this will greatly decrease drilling time. I used 3 different bits in this step. Once drilled the holes need to be de-burred and cleaned.
Any areas to be brazed may need to be cleaned with a wire brush.
Step 6: Assemble
First braze the flange to the riser pipe.
Set aside to cool.
Next braze the spark plugs to the top of the vacuum plate. Be sure to have the plugs aligned for ease of electrical connection.
Turn the plate over then braze the plugs to the bottom sise of the plate. This will ensure an air tight seal. Remove any glass left over from the brazing operation. This can be done with a wire wheel.
Next braze the riser pipe in place at the center of the vacuum plate on the underside of the plate.
Again remove any glass with a wire wheel.
Step 7: Enjoy
Make the electrical connections.
I placed the vacuum plate and riser assembly on my standard vacuum base which is connected to a 6CFM Ritchie 2 stage vacuum pump.
I am using the same tungsten element from eBay.
The metal being vaporized is copper from an old wire.
The transformer connections are 8GA wire with crimped eyelets. These are held in place with 10/24 brass screws.
Using the same jar as before, it took less than 4 minutes to achieve less than .100 TORR!
The glass shows minor copper deposits which are bonded!
More experiments to follow!
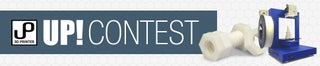
Participated in the
UP! Contest
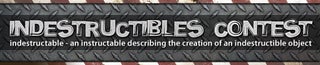
Participated in the
Indestructibles Contest