Introduction: Folded-horn High Accuracy Full-range Speaker System
Had been browsing the web for good speaker designs and was intrigued by the concept of horn speakers. Thought I would go ahead and make one just to see if the claims on the web were true or not (very high efficiency, no cross over distortion, great sound in th mid range, and bass up to 30-50 Hz without woofers) . The designs on frugal-horn.com seemed well thought out and the Spawn family seemed to be good performers especially after the glowing reviews on equivalent speakers. I was planning on recycling drivers (3 inch or 4 inch speakers) that I already had so therefore selected the least wide Spawn speakers.
The picture shows how the speakers turned out. Wife likes em! Will post a video later on.
Printed the plans out. I needed 18 inch wide panels for the sides and 5 1/8th inch wides for the baffles and dividers etc. Closest were 16 inch wide and 5.5 inch wide. So decided to get enough of the 5.5 inch white MDF panels to make one speaker. Also bought some nice plywood and Lowes cut it for me to 18 inches wide. Was simpler to stick to the original 18 inch dimensions otherwise I would have to recalculate the internal baffle dimensions.
Step 1: Cutting the Wooden Pieces for the Speaker
I cut the 18 inch wide panels to a height of 6 feet from it's original height of 8 feet. I then drew the locations of the internal baffles onto the plywood panel. Then drilled 1 mm dia. holes though the panel so that I could attach nails to hold the baffles.
Got busy with the glue bottle and clamps and screws to assemble the the back, top, bottom and front panels (baffled) onto one 18 inch by 72 inch side panel. Used biscuits to hook the panels together which makes the final assembly quite a bit easier. You can see the biscuit slots in the left most speaker. Even with biscuits is is important that the panels are perpendicular otherwise the final large panel will not fit on top.
While the glue was curing, I cut the 5.5 inch wide panels into 38 pieces based on the handy table included in the plans. This was a bit of a work as only had a handheld circular saw.
Glued the internal labyrinth of baffles in. And painted exposed surfaces with black paint. Let everything dry and cure overnight.
Step 2: Connecting the Speaker Driver
Could not wait to see if these speakers actually performed as stated so wired an RCA socket on one end and a 3 inch speaker that I removed from a Creative Labs D80 bluetooth speaker box. The original speaker output on the amplified Creative bluetooth D80 unit was extended with a longer wire to which I soldered an RCA plug. Know this is not the ideal speaker driver but it was good enough for a test.
Without the second side panel, the sound was not too bad! And not that different from the second speaker still in the creative box. This got me a bit worried. Anyway clamped the other panel on temporarily to see if the sound was different, and yes, it was, there was more bass and more 'presence", more gravitas! So even with mediocre speaker drivers there was a bit of an improvement. Ok, this might be worth putting more effort into.
Based on the above informal test, I decided to use speakers that I had removed from a Fostex SPA11 powered speaker unit. Expanded the hole in the front panel to fit the speaker (used a jigsaw to cut the hole). Stuffed the speaker chamber only with polyester stuffing to minimize sound reflections. And permanently attached the side panel with expanding polyurethane glue and tons of clamps, weights etc. to really push the side panel onto the baffles. Also applied a few strategic screws to hold and clamp the side panel in place.
I did something stupid, directly attached the speaker to the iPhone head phone output. Yes, without an amplifier, and the sound was nice and loud. Did a bit of testing using an oscillator app on the iPhone. Could hear from about 40Hz to about 16KHz.
The picture shows my crude cutting set up. The baffles with the trial speaker attached. Close ups of the stuffing behind the speaker. Temporarily placing the side panel for testing!
Step 3: Finishing the Speaker ...
After the speaker bodies were assembled I attached black velvet across the fronts of the speakers covering up the horn openings. As was using scrap velvet left from a previous project that was not big enough had to use two pieces for each speaker, one piece covering the top half of the speaker and the other piece covering the bottom half, with the seam in the middle. Attached the velvet with glue and staples.
I then attached standard-of-the-shelf 0.75 in x 1.5 inch wooden strips to the top, to the sides (to hide the velvet edge), and the bottom of the box for additional support. I used standard 6 feet long strips from Lowes. These projected out below the bottom of the speaker box forming support feet.
The diagram will make a bit more sense. The left three boxes show how I added the velvet fabric. The right three boxes, how the wooden strips were added.
Finally, added molding on the top and bottom, stained, soldered the speaker clips to one end of lamp wire and an RCA jack to the other after confirming continuity with a multimeter. Added the driver.
Step 4: Conclusion ...
They do sound pretty good. Was it the worth the effort of constructing these? Am not sure. Am glad that I did make them but most likely would not make these again.
Do now like listening to music again (the sound is different and somehow more connected) but the speakers are pretty massive (6 feet tall and nearly 2 feet deep).
Will add a bit more info later on once I get used to them.
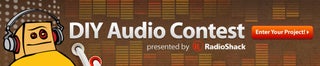
Participated in the
DIY Audio