Introduction: Air-Powered Soft Robotic Gripper
Update (11/22/2013): MUCH cheaper option added to the materials list to replace the squeeze bulbs. Thanks to the education staff at the Franklin Institute in Philadelphia, PA for pointing that out!
Update (4/23/2013): smaller, cheaper "mini" gripper STL file has been added. This gripper will cost less to order from a 3D printing service and won't require as much air to inflate (easier to inflate with a single pump from a squeeze bulb).
Credits: The soft robot technology in this project was originally developed in the Whitesides Group at Harvard University. For more details about the development of the technology and its uses, see the papers Soft Robotics for Chemists and Multi-Gait Soft Robot, and check their publications page for new work. These instructions, which modified the Whitesides Group's original process to be cheaper and more kid-friendly, were developed by a postdoctoral researcher (Dr. Ben Finio) in the Creative Machines Lab at Cornell University (PI: Prof. Hod Lipson), with the assistance of Prof. Robert Shepherd. The work at Cornell was sponsored by the National Science Foundation (DRL-1030865) and the Motorola Foundation.Special thanks to the Ithaca Generator and Ithaca Sciencenter for providing audiences to help us test this project.
"Soft robots" are all the rage in the robotics research community right now. Forget what you usually think about robots and machines - gears, pulleys, circuit boards, aluminum and steel. These robots are made out of soft, stretchable rubbers and plastics, and driven by things ranging from compressed air to chemical reactions and materials that change shape due to electrical current or voltage. Existing robots include a robot worm that can survive being hit with a hammer, a rolling soccer-ball shaped robot, a gripper filled with coffee beans, and even an artificial octopus tentacle.
This project will describe how to make simple, air-powered soft robots that are made from silicone rubber, and shaped using a 3D printed mold. The project is based on a soft robotic gripper and a walking soft robot originally developed by the Whitesides Group at Harvard University:
The project requires access to a 3D printer, or you can order a 3D printed mold from an online printing service like Shapeways, Sculpteo or iMaterialise.
IMPORTANT NOTE ABOUT 3D PRINTER MATERIALS: I can only guarantee that this project should work with an ABS mold. I think PLA should work but have been unable to test that yet. I have also tested both laser-sintered nylon and UV photopolymer molds ("strong & flexible polished" and "detail plastic" respectively on Shapeways), with mixed results. Even with a "polished" finish, the laser sintered nylon has a somewhat porous surface, which can make it very difficult or impossible to remove the silicone rubber from the mold without breaking it. The UV photopolymers can prevent the silicone rubber from curing fully, leaving it with a tacky or even slimy surface. Point being - order these materials at your own risk! A representative from Smooth-On (manufacturer of the Ecoflex silicone rubber) suggested spraying incompatible mold materials with a clear acrylic lacquer, but I haven't been able to try that yet. He specifically recommended Krylon Crystal Clear.
Required Materials
- Ecoflex 00-30 (one "trial kit" is enough to make 5-10 robots depending on size).
- (Optional): Ecoflex 00-50, which is stiffer than Ecoflex 00-30. Using both materials (00-30 for the top layer and 00-50 for the bottom layer) can help the robot bend more easily when inflated, but this isn't required and will drive up the cost of your project. Only recommended if you plan on making a large number of robots (e.g. for an after-school program or summer camp), and need to purchase two or more Ecoflex kits anyway.
- (Optional): Food coloring. The default color of cured Ecoflex is off-white, but you can use food coloring to customize your robots.
- 1/16" ID, 1/8" OD polyethylene tubing* (part number 5181K15 at McMaster-Carr), about one foot per robot
- 1/8" ID, 1/4" OD silicone rubber tubing* (part number 5236K832 at McMaster-Carr), about one inch per robot
- Squeeze bulb: we recommend the "Polaroid Super Blower with Hi Performance Silicon Squeeze Bulb", available at Amazon.com and ritzcamera.com.
- UPDATE: these syringes work just as well and are much cheaper than the squeeze bulbs. If anything, they work better - they don't leak air as much, allowing the gripper to hold its shape better. Much more economical if you are doing this for a large group of students.
- 3D printed mold. The STL file for a basic four-leg gripper is available as an attachment to this page, and is also available on Shapeways and Thingiverse. If you have access to a CAD program (there are some free ones like Google Sketchup and 123D by Autodesk), you can also design your own molds. UPDATE 4/23/2013: I've also added a "mini" gripper STL file - smaller, cheaper to print, and easier to inflate with a single squeeze from a squeeze bulb. This file is also available on this page, Shapeways and Thingiverse. Make sure you read the warning above about materials!
- Plastic cafeteria tray or metal baking tray (metal tray only required if you plan to use an oven, see below)
- Disposable rubber gloves
- Scissors
- Plastic cups
- Coffee stirrers or popsicle sticks
- Paper towels for clean-up
- (Optional) toaster oven. Do not use an oven that you also use for food.
*Note: all of the materials for this project are re-usable except for the silicone rubber. The tubing is very cheap (less than a dollar per foot) so it is not very economical to ship in small quantities - it can't hurt to purchase a few feet of both polyethylene and silicone tubing, in order to make multiple robots.
Step 1: 3D Printed Mold
Download the file 4-leg-gripper.stl or MiniGripper.stl from the links on introduction page (note: the units for the files are in millimeters). If you own or have access to a 3D printer, print your own mold. There are many low-cost "desktop" 3D printers available on the market, such as the Makerbot, Cube, and UP.*
If you do not have access to a 3D printer, you can order a mold from an online vendor like Shapeways, Sculpteo or iMaterialise.* Be sure to choose a material with a smooth surface finish - otherwise it will be difficult (or impossible) to remove the cured silicone rubber from your mold. Disclaimer: I tested the directions for this project printing in ABS with an UP 3D printer. I cannot guarantee that other printers or material types will work well with the silicone molding process. It might be a good idea to print a very small test container and do a test cure (follow the steps in the rest of the procedure to mix and cure the silicone rubber), to make sure you'll be able to get your robot out of the mold.
Advanced users: if you have access to CAD software, you can certainly design your own mold instead of using the files supplied here. The paper Soft Robotics for Chemists and its associated supplementary material provide a great introduction to different types and shapes of molds (and the resulting robot motion).
*Note: the 3D printing market is evolving rapidly. This project was originally posted in March 2013, and we can't predict what new 3D printers, companies and services will emerge in the future. You can always do a Google search (for example "3D printing", "3D printing service", etc) to check out what's currently available, and shop around for the best option.
Step 2: Prepare Silicone Rubber Mixture
Safety note: Ecoflex is a brand of silicone rubber used for molding made by Smooth-On Inc. Ecoflex comes in two bottles, containing Part A and Part B. Parts A and B are liquids - when mixed together, they will solidify and form silicone rubber (in 4 hours at room temperature, or 10 minutes at 150º F). The materials are non-toxic, and harmless once cured. However, according to the Material Safety Data Sheet (MSDS), "repeated or prolonged" exposure to the unmixed materials (Part A and Part B) can cause mild skin irritation. We recommend wearing disposable gloves when handling unmixed material. If you do get Part A or B on your skin, just wash it off with soap and water.
Mix parts A and B of the Ecoflex in a 50/50 ratio by volume, using a paper or plastic cup. You do not need to use all of your Ecoflex - fill one cup (the one pictured here is a 9oz cup), put the lids back on your Ecoflex jars, and save the rest of the material to make more robots later. Stir the mixture for about two minutes.
Optional: if you have food coloring, mix a few drops in with the Ecoflex. The food coloring will tend to bead up and form droplets instead of evenly mixing in to the Ecoflex, so you need to stir pretty vigorously to break up the beads.
Step 3: Pour Mixture Into Mold
Slowly pour the mixed Ecoflex into your 3D-printed mold. The material is very viscous so it will flow slowly - do not pour too fast! Fill the mold to the top edge. Once filled, wait about five minutes for air bubbles to rise out of the mixture. You can "pop" air bubbles with a coffee stirrer, pencil or pen to speed the process along.
Step 4: Pour Mixture Onto Tray
Optional: If you purchased Ecoflex 00-50, mix parts A and B in a new cup (do not mix with 00-30) and use it for this step.
Pour your remaining Ecoflex onto your baking tray or cafeteria tray. Make sure you form a puddle large enough to completely surround the outer perimeter of your plastic mold (if you didn't mix enough in Step 2, you can mix more). If you are making multiple robots, you can fill the entire tray. The layer should be several millimeters thick.
Step 5: Let Rubber Solidify
You should now have uncured Ecoflex poured into your plastic mold and your tray. Let the material sit for 4 hours, and it will cure (solidify) at room temperature.
Optional: if you have an oven available, and are using a metal tray, you can bake the material for 10 minutes at 150 degrees Fahrenheit. Safety notes:
1) Do not use an oven that is also used for food.
2) Do not put a plastic cafeteria tray in the oven.
3) Double-check the melting temperature of the material of your 3D-printed mold. The plastic pictured here is ABS, which will not melt at 150ºF, but your material may be different.
Step 6: Check That Rubber Has Solidified
After 4 hours at room temperature (or 10 minutes in the oven at 150º F), your Ecoflex should be solid. Poke the material with your finger - it should have a rubbery feel, but no longer be gooey. It should also become slightly more opaque (compare the picture in this step to the one in the previous step). If the material is still liquidy and sticks to your finger, it needs more time to cure.
Warning: if you used an oven, your metal tray and mold will be hot. Use oven mitts to remove them from the oven, and let them cool before handling directly.
Step 7: Remove Rubber From Mold
Carefully peel the cured silicone rubber out of the mold, starting with the outer edges. Be careful and peel slowly - if you peel too quickly, the material might rip. Do not remove the sheet of cured rubber from the tray yet.
Step 8: Mix a Fresh Batch of Silicone Rubber
Using a new cup, mix a new batch of Ecoflex in a 50/50 ratio of Parts A and B. You only need a small amount for this step - enough to apply a thin, even coating about 1mm thick over the flat sheet on your baking tray.
Step 9: Spread Thin Layer of New Silicone Rubber on Top of Cured Layer
Spread a thin, even layer (about 1mm thick) of freshly-mixed silicone rubber on top of your cured sheet. This forms a "glue" layer to bond the top and bottom halves of your robot together. Using a paper towel to smear the material around can be helpful. This step is crucial - if you use too much silicone rubber, it will clog the air channels in your robot. If you don't use enough, the two layers will not bond together.
After you have poured the material on and spread it around, give it about two minutes to settle before moving to the next step.
Step 10: Place Top Half of Robot Face-down on New Layer of Silicone Rubber
Take the piece of cured rubber that you removed from your mold in Step 7. This is the top half of your robot. One side of it should be smooth, and one side should have exposed ridges that will form the interior air channels of your robot. Carefully place the top half onto the fresh layer of new silicone with the air channels facing down.
Step 11: Seal the Outer Perimeter of the Robot
Using a coffee stirrer or popsicle stick, apply an additional layer of fresh silicone rubber (you can mix some more if you don't have any left over from Step 8) around the outer perimeter of the robot (the bottom edge, that is in contact with the layer on the tray). This will help prevent air leaks.
Examine the top of the robot for embedded air bubbles. You can apply a small blob of silicone directly above these bubbles - this will strengthen that area, and prevent your robot from popping. You should also add some reinforcing silicone directly above the large, circular central chamber in the robot
Step 12: Let "glue Layer" Solidify
Wait 4 hours at room temperature (or 10 minutes in an oven at 150ºF - follow the safety notes from Step 5) for the "glue layer" to solidify, bonding the top and bottom layers of the robot together. Check that the new layer and seal around the outer perimeter of the robot are solid and rubbery (no longer gooey/liquidy) before proceeding to the next step.
Step 13: Remove Sheet From Tray
Carefully peel the entire sheet up from your tray. Be careful to peel slowly so you do not tear the rubber.
If you used an oven, wait for the tray to cool before touching it.
Step 14: Cut Out Robot With Scissors
Use scissors to cut around the outer perimeter of the robot, removing excess material. Be careful not to cut into the robot and puncture the air channels. It is OK to leave a little extra material around the edges just to be safe.
Step 15: Puncture Robot With Air Tube
Cut roughly a one-foot section of the polyethylene tubing. Cut one end of the tubing at a 45 degree angle so it is pointy - this will make it easier to insert the tubing into the robot.
Puncture the robot from the side, at a 45 degree angle in between two of the "legs". Aim for the circular central chamber that connects the four air channels. It may help to use something sharp, like the tip of a pencil or a paper clip, to make the hole before you insert the tubing. Make sure that the end of the tube winds up in the central air chamber.
Step 16: Connect Squeeze Bulb
Cut a one-inch segment of rubber tubing. Use this piece as an adapter to connect your polyethylene tubing to the squeeze bulb.
Note: if you are using the Polaroid Super Blower, remove the small rubber piece at the end of the plastic nozzle, and 1/8" ID rubber tubing should fit directly onto the plastic nozzle. If you are using a different brand squeeze bulb, you may need to use an additional piece of rubber tubing with a different diameter as an adapter (such as the one pictured here).
Step 17: Inflate!
Inflate your brand-new robotic gripper! It may take more than one squeeze of the squeeze bulb to fully inflate your robot. Can you use it to lift different objects?
Be careful not to over-inflate your gripper - the material is very durable but it will pop eventually. If your gripper doesn't work on the first try, go to the next step for troubleshooting tips.
If you've completed this project, please leave a comment with a link to pictures or videos of your work!
Step 18: Troubleshooting
Gripper not working? Here are some troubleshooting tips you can try.
Check for air leaks. If your gripper doesn't inflate at all, listen and feel for air leaks when you squeeze the bulb. If you do have air leaks, you can patch them up with a fresh layer of silicone rubber, let the material cure, then try again.
Check for clogged channels. Hold your gripper up to a bright light and look at the interior air channels. Can you see them in all four legs? If you can only see parts of the channels, or can't see them at all, they are probably clogged, which means you used too much "glue" in Step 9. Unfortunately there is no way to repair this - you will have to start from the beginning. Luckily, you should have plenty of Ecoflex left over, and your mold, squeeze bulb and tubing are all re-usable.
Make sure the tip of the air tube is in the central chamber. Hold your gripper up to a light and look for the tip of the air tube. Did it make it all the way in to the central chamber? If you didn't fully puncture the outer wall of the robot, or pushed the tube too far and into the opposite wall, then the end will be sealed shut by rubber, and prevent air from getting into the channels. Wiggle the air tube until the tip is free in the central chamber.
Some legs inflate better than others. If all four of your legs don't inflate symmetrically, first check each individual leg for clogged air channels, as described above. If none of the channels are clogged but the legs still don't inflate symmetrically, you can layer some extra silicone on the legs that are inflating the most - this should make it harder for them to inflate, allowing more air pressure to divert to the other legs. The material has "nonlinear" behavior - this means that, instead of always inflating gradually with air pressure, it could not inflate at all and then suddenly "jump" and inflate. So, if one leg is slightly weaker than the others (maybe due to some slight differences in wall thickness from the molding process), it might inflate first while the others don't inflate at all. Strengthening this leg with additional silicone may prevent this.
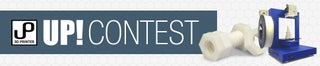
Grand Prize in the
UP! Contest