Introduction: Algae - Arthropod Culture System
This is a simple, modular shrimp culturing system. It is designed to minimise the shear forces in the shrimp growing chamber, and to operate at low voltage (9-12v). This makes it safe to mix electricity and salt water, should an accident occur, and also allows a micro controller such as an Arduino to be used to control day/night cycle, dosing and measurements in future refinements of the project. It also can be cleaned in a dishwasher when it is finished. The design strategy of powering the culture system from a low voltage, sealed and certified/tagged power pack makes this system very suitable for classroom experimentation.
The idea is that it uses two chambers that are connected by two tubes with filters attached. On one chamber, there is illumination supplied by a hydroponic LED illuminator (with constant current driver) and intense aeration. The aeration means that the water level on that side is higher than on the other side, so water flows from the aerated side to the non aerated side. The non-lit side is where the shrimp are cultured, and they feed on the algae grown on the lit side and that travel through the filters on the tubes.
If you have students who want to safely culture living organisms, watch the life cycle of an invertebrate, or just keep a fresh and ready supply of brine shrimp then just read on !
Step 1: Gather Your Equipment
You will need
2x acrylic drinking chambers
1x aquarium pump or 6v aerator pump
1x sheet wiping cloth. (Wash this in the washing machine, then rinse repeatedly in fresh water to eliminate any chemicals such as surfactants or anti-microbials)
2x 3cm lengths of glass or plastic pipe. I cut up an old 20ml pipette that I raided from the broken glass bin. Clear pen barrels, washed very well, would also do.
digital calipers or ruler
2x tube of "2 minute epoxy resin"
4x plastic tub (cleaned cap from a milk bottle) to mix epoxy in
4x cotton buds for mixing and applying epoxy
7mm drill bit and drill or drill press
1x small file to smooth edges of the holes/ score the glass pipe
1x bastard file to even up aluminium
1x Dremel with cutting disk (or hacksaw and lots of patience)
1x aquarium air pump, or 6v air pump (eg from a live bait aerator)
1x airstone and silicone tubing (you can autoclave these).
1x 50cm "stick" or piece of wood for o-ring applicator
1x plastic cap the size of o-ring (could use 10mm pvc)
1x ball of cotton wool to make vent filter
Blue or other bright colour food dye
Measuring jug (1 to 2l)
Electronics
- 10k Ohm resistor
- 2.7 Ohm, 5 Watt resistor
- Small signal NPN transistor - anything in silicon will do ! 2n2222, BC548, I used a C185 (desoldered from a TV obtained from the kerb)
- Power NMOSFET, 3A-6A rating, eg 3055VL, anything of reasonable power (30 Watts, and low on resistance. I used PO903BDG mosfets from old computer motherboards rated at 30W, see http://www.cheertech.com.tw/Niko-sem/Data%20sheet...
- 1-3 Watt LED grow lamp. These emit red and blue light, and so stimulate both Photosystem 1 and 2 in plants, leading to good growth. I got mine from http://www.ebay.com/itm/10pc-3W-High-Power-Mixed-C...
- GPU heatsink, 50mm x 50mm
- Aluminium box section, 50x50mm
- 2.1mm power pack plug
- "Wall wart" style power pack, 9v to 12v, capable of 500mA. I bought mine from a thrift shop, 50cents each for a box of 10
- Hook up wire
Soldering iron, solder, clippers etc for electronic work.
To run the culture unit:
- Sea salt (approximately 40g)
- Bicarbonate of soda (1g)
- Soluble plant fertiliser (0.2g)
- Electronic balance
- Algae (eg Dunaliella salina, or freshwater variety if cultivating freshwater arthropods)
Once you have collected all the materials, you can start to assemble the chambers.
Step 2: Cut Your Connecting Tubes
First you need two lengths of connecting pipe.
Measure 3cm of your pipe.
If it is glass, scratch a single line around it with a file.
Lick your fingers, and rub the line you have just scratched. (There is enough OH- ions in the "high" pH of your saliva, 7.8'ish to catalyse the breaking of the Si - O bonds in the glass. This makes it significantly easier to snap, especially if you use freshly scratched glass)
Grasp the tube at either end of the scratch, pull it apart so that there is tension on the glass, and then just slightly bend. The glass tube should break cleanly at the place that you have scratched it.You can see how to cut glass pipe in this video
or
Measure 3cm along a plastic tube such as a round pen barrel. Mark the barrel then cut it with a hack saw. Repeat to get the other tube.
Step 3: Mark Out the Chambers and Glue in the Connecting Tubes
Mark out 4cm from the top and 4cm from the bottom of each container. Place them together on a flat surface so that you can see the two marks. On the top mark, raise one mark by 2-3 mm. The lower side will become your aerated side. When you bubble air through this chamber, the level of the water will rise. This small head of water is what pushes water from one side to the other. The lower tube allows the water to flow back from the non-aerated side, ensuring that there is a continuous flow.
Drill out the marks in each container. As my glass tubing was 7mm, I used a 7mm drill bit. Use a file to clean up and adjust for the slight angle on the top connecting tube.
Choose one container, lay it on its side with the holes you have just drilled straight up and place the connecting tubes into the holes that you have just drilled. Make sure that you have 0.5cm or more tube poking into the container so that the o-ring and filter can fit. Check that you have a snug fit. If necessary, temporarily position the glass tube in place so that you can epoxy them in place.
Mix your two part epoxy well, and then glue the tubes into one container. Leave half a centimeter or more of tube exposed into the chamber so that the filters can fit over it. Let it set. It should look like the last picture above.
Step 4: Add the Second Chamber and Epoxy Together
Now take the second container and push the tubes from the one that you have just epoxied into it. You might want to support the containers on their sides, so that epoxy doesn't run down the sides of the container. I didn't photograph this, but a pair of such as those shown here will help, if you attach the clip to the opening of the already set container.
Mix another 2-5ml of epoxy. I waited a minute or two to let it thicken before applying it around the base of the tube where it connected to the acrylic container. The philosophy with the epoxy is to use it to seal the glass to plastic connection. You want as little epoxy as is possible to be in contact with the culture (any plasticisers in that brand of epoxy that we don't even know about can't leach out if they are not in contact!).
Let the whole thing set for a couple of hours.
Then mix some more epoxy and totally cover the connecting tubes with it. This is to give extra support, and to prevent the system from snapping at the connecting tubes when you handle it, or if it is dropped. You can think of this as thickening the joints between the two chambers.
Leave the whole system to set for 24-48 hours. "5 Minute" epoxy doesn't reach its full strength for that long.
Step 5: Drill the Vent and Airhose Holes in the Lids
You need to drill 3 holes in the lids of the chambers.
For the illuminated lid, drill two holes near each other and just off the edge. One is for the 7mm air hose, and one is for the vent.
For the non-illuminated lid, you just need a 7mm hole for the vent. Remember to file the edges smoothly, so that you don't have to worry about catching the cotton wool filter that will stop dust and microbes from contaminating your culture.
Step 6: Installing the Filters
Next you will need to install your filters. I made an o-ring installer by hot-gluing a piece of plastic tubing the diameter of the o-ring onto a long piece of wood (well chipboard off cut). I held the chamber on its side and laid a square of filter over the connecting tube. I gently stuck the o-ring to the plastic o-ring installer with the smallest, flimsiest piece of tape. I grasped the stick and manoeuvred the o-ring over the connecting tube and pushed down. This places the o-ring over the filter and holds it in place.
Step 7: Test the Chambers to With Dye to Show That the Chambers Are Working
Now the time has come to test your system.
Measure the volume of water it takes to cover the inlet of the lowest chamber. As you measure out volumes (eg in lots of 250ml), it is useful to mark the levels on the side of your chambers.
Add blue dye to the lower chamber, and switch on the air hose into that chamber.
After 30 seconds to a minute, you should see the dye spread between the two chambers, as shown above.
If so, your system works!
Now on to build the light.
(NB. Oops, in this photo I have swapped the chambers around, so I put the
air hose onto the non-illuminated side. That was just for the photo, the colour distribution was caused by the system working properly)
Step 8: The LED Driver: How It Works
The LED driver is a simple, constant current regulator. You can run
it from 9-12 volts, but the higher the voltage, the more heat it will have to dissipate. Lower voltage means less disturbance to the heating of your culture system (but hey, your shrimp might appreciate a bit more warmth!).
The circuit works like this: When power is applied, the transistor Q1 is off (has a high resistance compared to R1), and so nearly a full voltage (9v) is supplied to the gate of the mosfet. This turns it on. Current then flows through the LED, mosfet Q2 and current-sensing resistor R2. The more current that flows through R2, the bigger the voltage drop across it. When the voltage drop reaches nearly 0.7v, the transistor Q1 starts to conduct and its resistance drops. This means that the ratio of resistance of R1 to resistance of the transistor changes, and the voltage at the gate of the mosfet Q2 falls. This partly turns it off, thus regulating the current through the LED. It doesn't matter what voltage you supply, the current flowing through the LED is set by the current required to reach a 0.7v drop across R2. So the current the LED sees is set by the formula R2=0.7v/Current through LED (amps). For a 9v grow lamp LED, rated at 3W and running at 300mA, a 2.3 ohm resistor is needed. The grow lamp LEDs consist of a string of LEDs wired in series, hence the strange running voltage (9v) for a LED.
Step 9: Build the LED Driver
Get a 50x50mm heatsink. I got mine from, you guessed it, the kerb!. There are plenty of suitable heatsinks in old computers, especially on GPU chips. CPU heatsinks are generally much larger, and overkill but there is no reason you can't use them.
Attach the LED, the mosfet, and the current sensing resistor to the heatsink by painting their backs with a thin smear of heatsink compound. Double sided heatsink tape will also do.
Once you have placed these components on the heatsink, you will need to mix up some more epoxy glue to attach them securely. Cover the components, but not their terminals with epoxy glue and leave to set. At the same time, epoxy in the 2.1mm power socket to the edge of the heatsink as shown.
Once the epoxy is dry, place the remainder of the components, and solder them together with insulated hookup wire.
Plug the LED module into the 9-12v plug pack and confirm that it works.
Step 10: Build the LED Housing, and Assemble the LED Module
Take the 50x50mm aluminium stock tubing and cut a 5cm length of it.
Mark out the position that the power socket will fit into by lining up the heatsink unit on top.
Cut with hacksaw or dremel out the required shape, then file it smooth with a bastard file.
Check that there are no problems with short circuits by powering it up. If there are, adjust the leads into position.
Once you see that it all works ok, place it heatsink side down, and fill with epoxy resin. Take care not to get any on the lens of the LED.
Allow this to set for 24 hours.
Step 11: Assemble the Chamber, LED, and Pump
Assembly is straight forward but there are a couple of points to note.
I use ordinary sticky tape to hold the LED module onto the top of the culture chamber. This is disposable, and allows the chamber to be washed between cultures.
Run the air stone and tubing to the bottom of the filter chamber. Tape the LED unit to the lid of the illuminated chamber, taking care to not crush the air tube or block the vent hole.
Place a wad of sterile or at least clean cotton in the vent hole to stop aerosols of the culture medium escaping, but to allow excess air to pass through.
Place another wad of cotton in the vent hole of the non-illuminated chamber.
Add culture medium. I used 40g/l of sea salt, 0.2g of thrive garden fertiliser, and 1g of bicarbonate of soda, made to a final volume of 1.25l or just so the higher tube was uncovered.
Time to pitch the algae!
Step 12: Innoculate With Algae
I wanted some salt-tolerant photosynthetic algae/ organisms so I visited my local very salty rock pool on the limestone cliffs at Cape Peron, Rockingham.
You can see a photo and a video of what I found, which looks to my untrained eye like one of the Dunaliellas. As I don't have access to named and identified cultures of algae (eg Dunaliella salina), this seemed a good way to go. Always be careful with unidentified microorganisms - having said that there isn't much that is toxic in the extremely saline dying rock pools that I could tell.
I pitched 20ml of that liquid into the culture, and waited 4 days before adding brine shrimp eggs to the non-illuminated slide. After 2 days I got very noticeable Tyndall scattering when I passed a laser pointer through the chamber.
Step 13: Concluding Remarks
There is a lot of potential in this little device and a number of experiments that I would like to try.
I haven't really worked out the optimum angle for the top connector tube, and some experiments on this would be helpful.
I am quite interested on working with Arduinos to control this. I have in mind using a mosfet (3055vl are good for switching little motors) to control both the light and the aerator (I'd use one from an old bait aerator, or one of these
http://www.ebay.com/itm/DC-3V-6V-370-Air-Pump-High... I'd like to use a DS18B20 to monitor temperature, and maybe a green laser module and a green-filtered bpw20 or other photodiode to do light scattering and turbidity so that real-time growth can be monitored. Maybe also I might look at making these chambers aseptic (eg put a 0.22uM filter on the air line and seal the inlets better).
A peristaltic pump for dosing could also be used - however I don't think that would be good for pumping shrimp!
Mostly though, I'd like to explore growing some of the clam shrimp-like creatures (I think they are Conchostraca) that used to live in the seasonal ponds alongside the railway in Gosnells, Western Australia when I was a kid. I don't think it has ever been done before!
This is my first ever Instructable, so I am interested in any comments on how to improve the next one. I hope that it has been of some use to someone. Enjoy your low-shear shrimp culture system!
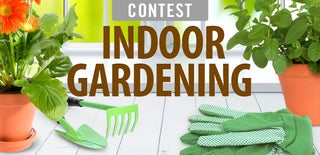
Participated in the
Indoor Gardening Contest 2015