Introduction: All-Terrain Electric Scooter
At the beginning of the 2011/2012 school year, my school's robotics team decided to finally dismantle some old FRC robots that had been collecting dust for six or seven years. We had no use for all the parts we stripped off the robots, so I generously relieved the team of some of these parts, including six Victor 884's, six CIM motors (4x 2.5", 2x 3"), 2 AndyMark Toughbox gearboxes, some #35 roller chain, and assortment of sprockets, some steel shafts and shaft collars, a 1/4" by 4" by 3' aluminum plate, 1" aluminum U channel, 1/8" polycarbonate sheet.... Anyways, while looking up the CIM motor curves, and trying to figure out by how much I could over-volt them, I ran into this, which at one point used a pair of CIM motors. That vehicle then led me to these. By an interesting coincidence, only a few weeks after I discovered those vehicles, I went to the Atlanta Mini Maker Faire, and guess what I saw there. After seeing the vehicles in action, I decided to build my own electric vehicle, and so the idea for my scooter was born.
The scooter is geared for a top speed of about 25 mph, has around 3 horsepower, and can go 8-12 miles per charge.
Step 1: Parts and Tools
- Donor kick scooter frame - mine was a Royce Union Transit
- Wheels - I used 12.5" low-speed pneumatic wheels from Northern Tool
- Motor(s) - 3x CIM motors, which are generally used in FIRST robots
- Gearbox - CIM motors are fairly high speed/low torque motors, so a gearbox was required in addition to the reduction from the chain drive. My franken-gearbox is a mashup of two Andy Mark Toughboxes from 2005.
- Motor Controller + throttle- I went a bit overkill, and chose a Kelly KDS72200E, 72V, 120 A continuous, 200A peak controller.
- Batteries - 8 x Turnigy 5000 mAh 4s LiPo packs
- Aluminum - angle channel and flat bar in a variety of sizesd
- Shock absorbers - 2x mountain bike rear shocks, 2x mountain bike fork shocks
- Nuts and bolts - too many and of too many different varieties to list here
- 1/2" threaded rod with matching nuts
- 1/2" and 8mm stainless steel rods + shaft collars- for the pivot points in the suspension
- Large power switch
- Fuse/Fuse holder
- High current terminal connectors
- Drill - with lots of large bits, up to at least 1/2"
- Hack Saw - if you have a bandsaw with metal cutting blades, please save yourself and use that
- Drill Press - Not strictly necessary, but it makes drilling precisely aligned holes much easier than with a hand drill
- File - for smoothing sharp corners and enlarging holes
- Propane torch and aluminum-zinc brazing rods
- An assortment of clamps
- Bench vice - mine was literally a workbench that was a vice, but the kind that bolts onto a bench would be even better
- Soldering iron + solder - one with a very heavy tip for soldering large power connectors and battery leads
- Lithium Polymer battery charger with power supply
- At least two adjustable wrenches
Step 2: Donor Scooter Teardown and Layout
The scooter started out as my old kick scooter, a Royce Union Transit, which was a small step above the classic Razor scooters in terms of quality - for instance, it has front and rear wheel suspension that uses actual springs and shock absorbers rather than rubber blocks, and it has a more elegant folding mechanism.
I started out by stripping the scooter of its original wheels and suspension, so that I could figure out an approximate layout of the final scooter.
For use on softer and less regular terrains than asphalt, the original wheels needed to go. I got new ones from Norther Tool. They sell a version with a 60t sprocket included, but I managed to scavenge a 60t sprocket with the same bolt hole pattern from my school. The best part of these wheels is that I can later upgrade the tires to these snowblower tires if I want to use the scooter in snow.
To keep room for suspension travel and keep a good steering geometry, the wheels had to be placed completely under the deck of the scooter. This means that the rider's platform is well over a foot above the ground, and the clearance under the scooter is around 7 inches.
Step 3: Rear Suspension Assembly
To accommodate the larger wheels, I built a completely new rear suspension assembly out of aluminum. I found some cheap mountain bike shock absorbers on ebay, and bought two with 1500 lb/in springs that I used for the rear suspension. The main frame of the assembly was made from 1/4" x 4" lengths of aluminum bar, which, like most of the other parts used in the scooter, were scavenged from my old school. Supports for the shock absorbers were made from 1/4" x 2" and 1" U channel aluminum.
Since the original scooter had suspension, designed the new suspension system to use the same pivot points as the old one. The original used 8mm bolts, and I had some lengths of 8mm stainless rod pulled form old printers that became the new pivots. I found that one of the 8mm rods was flexing significantly under load, so I drilled out those holes to 1/2", and replaced the 8mm rod with a 1/2" steel rod taken from a large flat bed scanner.
I made the left arm of the suspension assembly about two inches longer than the right arm, because I later would need to bend the aluminum around the rear sprocket. To bend the massive aluminum bar without a heavy duty bending brake, I heated the area I needed to bend with a pair of propane torches, and then used a vice, clamps, and brute force to bend the metal.
Step 4: Fork
Like the rear suspension, the fork and front suspension needed significant resizing to fit the new wheels.
For the new fork, I started out by tearing apart the fork from an old mountain bike. Fortunately, the scooter used a 1" threaded headset, which I was easily able to replace with the mountain bike's 1" threadless headset.
I pulled the springs and dampers out of the mountain bike fork, and used them to create a new pair of shock absorbers with pivots at each end. The pivots allowed me to build a leading-link style suspension arm, which is much easier to build than a telescoping fork.
I reused the fork crown and the top of the fork legs form the mountain bike, and bolted the 1/4" x 2" aluminum bars that made up the new fork to the tops of the old fork legs.
In my original fork design, the front wheel was was centered in front of the axis of the steering column. While this design did work, I did a few human-powered test rides of this configuration and found the handling to be poor. The wheel's forward position made it impossible to lean while turning, because if you lean into a turn, the wheel naturally wants to swivel away from the turning direction. Additionally, at higher speeds I realized that there would be the risk of the front wheel "castering" - trying to swivel around 180 degrees.
I rebuilt the fork, using only the parts from the original iteration, so that the front wheel was properly positioned for good handling. This did raise the front end of the scooter a couple inches, but it was a worth while tradeoff.
Step 5: Wheels
To get the wheels to interface with the rest of the scooter, I built my own axles our of 1/2" threaded rods and corresponding nuts. The wheel bearings' inner diameter was 5/8", so to get the 1/2" axle to fit snugly through the bearings, I made spacers by filing down the corners of two 1/2" nuts. The nuts are screwed towards each other until their flanges press against the outside of the wheel bearings. To lock the spacers in place, a second nut was threaded on for each one. FInally, to lock each wheel to the frame of the scooter, four more nuts were used, in pairs that pressed against opposite sides of the aluminum frame pieces.
Step 6: Gearbox
Because the CIM motors I used are relatively high-speed low-torque motors, a gearbox was needed to reduce the motors' output speed to a useable level. I started out with two AndyMark Toughboxes, scavenged from my school. These are two-motor, two-stage gearboxes, so I had to cut them apart and recombine them to make them useful. First I removed one stage from each of the gearboxes, for a gear ratio of 14:50. I cut down the gearboxes to get rid of as much wasted space as possible, and aluminum-zinc brazed the pieces back together to get a 3-motor gearbox with one output shaft.
The gearbox was mounted to the scooter using the original bolt holes built into the gearbox and some aluminum angle bolted to the scooter's frame. Finally, a 21 tooth sprocket for #35 chain was fixed to the output shaft.
Step 7: Chain Tensioner and Idler Configuration
By far the hardest part of the scooter to get working well was the chain tensioner. Because of the location I had to mount the gearbox, as the scooter's suspension is compressed the effective chain length between the sprocket on the gearbox and the sprocket on the rear wheel increases. The chain tensioner had to store enough extra chain to accomodate the movement of the rear suspension.
In addition to a chain tensioner, the scooter required an idler sprocket to rout the chain under the aluminum frame of the rear suspension arm.
In version 1 of the tensioner/idler configuration, both the idler and tensioner were fixed relative to the rear suspension arm. The chain tensioner was very simple, made of one idler in a pivoting arm attached to a spring, that pulled the chain tight.
This design worked okay on roads, but I found that riding over big bumps, especially on trails, caused the chain to slip off the drive sprocket. I was able to rationalize two reasons why this happened. When riding over a bump, the movement of the suspension puts additional tension on the top of the chain. Since the mounting of the idler sprocket was only made from 1/8" aluminum, the extra tension could have caused the idler to deflect to one side, causing the chain to slip off the drive sprocket. Additionally, the first chain tensioner design actually could not store enough extra chain to allow for full suspension travel, so over large bumps the suspension may have bottomed out and overstretched the chain, causing even more tension and idler-bending. At least that kind of makes sense. I couldn't actually see what was happening, so I don't really know if it's true.
Tensioner V1.5 added a chain guard around the drive sprocket, to prevent the chain from slipping off it. The guard was made by cutting small angled sections out of one side of some angle aluminum at regular intervals, and then bending the aluminum at these points to form a roughly circular guard. The seams were then brazed over and sanded down. This worked well at first, until the chain pulled so hard against the guard that it cracked one of the brazed joints and bent the chain guard out of the way.
Tensioner V2 failed so miserably it isn't worth posting pictures of or mentioning andy further.
V3 had the idler sprocket fixed relative to the gearbox, rather than relative to the rear wheel, so it completely prevented the chain from coming off the drive sprocket. The chain tensioner was fixed relative to the rear sprocket, so when it pivoted to lengthen the chain, it could not come out of alignment with the rear sprocket. Also, the tensioner used two sprockets to direct the chain in an "S" shape, similar to the rear derailleur on a bicycle, in order to store more extra chain. It was constructed from entirely 1/4" thick aluminum, making it extremely solid, and used actual shielded ball bearings for a pivot, rather than a bolt.
Step 8: Brake
Motors and drivechains are nice, but being able to stop is nice too. Since the rotors of disk brakes are simply large rotating metal disks bolted to a wheel, I decided to simply use the wheel's drive sprocket as the rotor for a disk brake. I built a caliper to grip the sprocket out of an aluminum block that used to support the scooter's original suspension, some aluminum U channel, two road bike brake pads, a spring, and some bolts.
The right brake pad is fixed to a rod that passes through the caliper, springs, and aluminum frame of the suspension, and the pad and rod can slide through all those bits. Since the spring is split in the middle, the brake is applied, and the brake cable pulls the two halves of the caliper towards eachother, both halves move equally in opposite directions, so that they both move towards the sprocket.
Normally on kick scooters, you brake by pushing down a lever above the back wheel with your foot. The lever rubs against the wheel, slowing the scooter down. I wanted the disk brake to be actuated the same way, so I built a brake pedal out of some 1" U and angle aluminum. Two pivoting segments are attached to the brake pedal, which, when fixed to the scooter frame, form a kite shape with hinged joints. When pressure is applied to the pedal, the kite is deformed, which lengthens its long diagonal. Since the brake cable is attached across the long diagonal, the cable's housing is pushed up the cable when the pedal is actuated
Step 9: Handelbars
For more control, I added wider handlebars, pulled from the same mountain bike as the fork and shock absorbers. Since the scooter's steering column did not have a mechanism for attaching the new handlebars, I also reused the stem from the mountain bike, and fixed it to the steering column by shimming its clamp with aluminum flashing.
The hall-effect throttle grips I ordered with the motor controller fit exactly on the handlebars, and the cable was routed down the steering column.
Step 10: Deck
The kick scooter's original was much too small for the scooter to be practical, especially when going over rough terrain, so I built a new deck that approximately tripled the width of the original. In addition to providing more standing area, the new deck added more space to hang components like batteries underneath.
In the spirit of building as much of the scooter as possible from parts I had on hand, I made a new deck out of some carbon fiber left over from my bamboo bicycle. Since the carbon fiber was in the form of 12K tow, I had to form it into cloth myself. I built a wooden frame with nails spaced every 1/2" around its edges, and used it to wrap two orthogonal layers of carbon fiber at a time. Once I applied epoxy to the fiber, I clamped the frame to another piece of wood to squeeze out excess epoxy and create a smooth, flat sheet. After 5 or 6 repetitions, I cut the deck to shape. I glued a layer of 1/8" polycarbonate on top of the carbon fiber, because carbon fiber is not very impact or abrasion resistant. The new deck was screwed on top of the old one with countersunk stainless steel screws.
Step 11: Electronics Mounting and Wiring
The motor controller was mounted to the face of the gearbox by a length of angle aluminum, to leave as much space as possible for batteries. The master power switch was bolted directly to the deck of the scooter, while a fuse holder and fuse were bolted to the bottom of the deck using more angle aluminum. I ended up using a 200A fuse, as 200A is the peak motor controller current. All the fuse will really do is help to prevent a catastrophe if the controller or battery pack short out. In most circumstances however, the solder connections on the power leads would probably just melt before the fuse blew. And as I've found out, the fuse does nothing to save the motors, which have a much lower current tolerance than any of the scooter's other components.
All electrical connections were wired with heavy duty bolt-through terminal connectors soldered to two parallel lengths of 14 ga wire. Because the motor controller was mounted with its contacts close to the underneath of the deck, its connectors had to be attached at right angles to the top of the controller. Because of this, the middle connection had to be raised, which I did with a small copper block soldered to the bottom of the connector.
The three motors were wired in series, using 5mm bullet connectors between each motor, so that individual motors could be easily removed if they got damaged.
Step 12: Battery Pack
For light weight and maximum energy storage per cost, I chose to use lithium polymer batteries from HobbyKing. I ordered 9 4S 5 Ah hardcase LiPo packs from HobbyKing, which happen to be the best value in terms of Wh/$ you can find on the site. The 9th battery was an extra, since HK's quality control is not highly regarded. I used 8 of them to make a 16S2P pack, at a nominal 59.2V 10 Ah pack, for about 600 Watt hours.
I paired off the battery packs, and wired the pairs in parallel, including the balance connectors, so I had four battery modules. To charge the pack easily, I made an attachment for my charger that connects all the packs in parallel so they can be charged simultaneously. When charging is done, the packs can easily be reconnected to each other in series.
Step 13: Battery Holder
To mount the batteries to the frame of the scooter, I built an enclosure out of angle aluminum and some polycarbonate scraps left over from making the deck. So that the inside of the enclosure would not have any protruding corners or edges, I made cutouts in the corners of the angle aluminum, so that no faces overlapped. I then brazed the assembly together. So that the batteries would be easily accessible, I made a cover for the front of the battery case out of more angle aluminum and polycarbonate, that was fixed in place by four thumbscrews. The bottom of the enclosure was also covered in polycarbonate, to hold up the batteries. At some point in the future, I plan on completely enclosing the batteries.
Step 14: Final Pictures and Videos
Step 15: Thoughts and Improvements
While the scooter is a blast to ride, there are a number of improvements that could be made.
The biggest issue with the scooter is the motors. CIM motors are designed to be 12V motors. With about a 60V battery pack and 3 motors in a series, each of the motors is getting around 20V. While the extra voltage in and of itself is not especially a problem, the extra current that the extra voltage entails is. ~1.7 times the voltage means ~1.7 times the current through the motors, which means ~2.9 times the power lost through heat in the motor's windings. Since CIM motors are not very efficient motors in the first place, the risk of overheating and damaging the motors is very serious. Going up a long, fairly steep hill, I managed to burn out two of the motors simultaneously. Fortunately, the motors are really cheap and I had an extra (a second spare came from HammockBoy), so it wasn't too much of a problem.
One way to solve the motor-burning-out problem would be to use the motor controller's programmable current limiting to reduce the current available to the motors. However, less current = less torque = less acceleration = less fun. The ideal solution would be to just buy a much nicer motor, like a short magmotor, which would be more powerful, more efficient, and lighter than the three CIMs.
For using the scooter in anything but completely dry conditions, it would need fenders around the wheels to prevent water and grime form being sprayed into the electronics and mechanical bits and onto the backs of my legs. Also, the connections for the electronics would probably need additional (mechanical, not electrical) shielding.
Finally, the bearings in the Norther Tool wheels are meant for low speed use, and are generally pretty terrible. Pulling them out and replacing them with proper sealed bearings would be a good upgrade.
If you like this project please vote for it in the Hurricane Laser Contest. If I won a laser cutter I would set it up at MITERS, MIT's student-run shop/hackerspace, so that any student, regardless of department, could have free, easy access to a laser cutter.
This is also entered in the Back to School contest. I was able to ship the scooter from Atlanta to Cambridge(due to it's folding ability), and I plan on using it as my method of transportation around campus and grocery-getting vehicle.
Finally, it is also entered in the Fix and Improve It contest, as I certainly regard this as an improvement on a boring old kick scooter
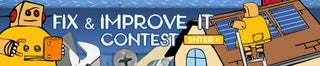
Grand Prize in the
Fix & Improve It Contest
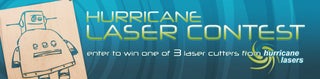
Runner Up in the
Hurricane Lasers Contest
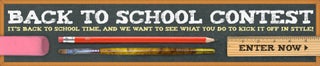
Participated in the
Back to School Contest