Introduction: Battery Powered Motorcycle
I have a lifetime love of motorcycles and we have a garage full of them to prove it. Big and Small, Fast and Slow I love them all. That said the little bike in this build is one of my favorite motorcycles of all time.
Back story for this Instructable is that we have a few of the Razor E Bikes in the garage and as a large man I have always been limited where I can ride them when we are camping. This has not been a huge problem though since I ride a Yamaha YZ426f most of the time. I do enjoy the silent little electric bikes though as a nice change of pace from my very load and obnoxiously powerful dirt bike.
The idea of tweaking a Razor also grew in my mind because we have a cabin on an island that is located at the top of a steep hill. The island only allows electric vehicles on the roads to keep the noise to a minimum. Unfortunately a golf cart for the cabin costs a lot of money, and although it is good exercise to climb the hill on foot there are times when we just need to run down to retrieve something from the boat or wish to go for a ride.
I started to envision a Razor with a two-motor set up and with added voltage and amperage. After my build was completed I found a couple of others who have built similar projects.
That original build was three years ago and it was so much fun that my wife asked me to make one for her. Our project list is large so it took me a long time to get around to ordering the parts and building her motorcycle. I also have ordered up parts to rework my original bike based off of what I learned from build number two.
Doner Bikes
Razor makes a number of styles of electronic dirt bikes. My family has experience with the MX500 and MX650 bikes. They are great little toy dirt bikes that require little maintenance. At least little maintenance in comparison to our gas driven bikes. Before my original build we had 1 MX500 and 2 MX650s. For the first build I found a MX500 for $150, bringing our Razor count up to four bikes. This became the "bones" for build number one and gave the project a start. Batteries where not in the bike at the time of purchase and it needed brake cables and work.
A little more about the doner bike for the first build: It had a single 500 Watt motor set up for a 36 volt system. It had an inferior shock absorber for the scope of my project and for my physical size, and the controller was not giving it enough power (amperage).
The Vision
My plan even before I began was to build a bike that had a two-motor set up, 48 volts, more amperage, a larger rear sprocket, and larger motor sprockets. My goal was to be able to carry my 240 pounds up the steep hill at the cabin. These bikes stock will fail to climb even a fairly moderate grade with someone my size on them.
That is a brief history of how this journey began. Up until now I have been referring mostly to the original build (MX500), and how and why it was built, but I will now change focus to tell you how I built bike number two, my wife’s bike (MX650). We worked hard to get this one done in time for Mother’s Day. I enlisted the help of a friend who also tweaks Razors to get it done in time.
Step 1: Parts List, Tool List, Safety List
I am describing a one-off custom build in this Instructable.
I will do my best to call out every aspect of the build to the best of my ability, but even if you go with the exact parts list provided keep in mind that wire colors change, parts and distributors change or go out of business, and that individual parts must be aligned and fit to size. Check photos for tips and key components. I have added notes to most of the photos. You do need to click on a photo to be able to read these notes. Generally the upper left corner of the box points to what part I am referring to. Try it on this photo to see what I mean. Click on the pencil Icon on the photo to show drop down notes.
Safety Notice: This project requires the use of lots of tools both powered and unpowered. Precaution should always be used when working with tools of any kind. Proper gloves, hearing and eye protection are a must. Also keep in mind that with this project you will be working with enough DC power to be respected. In other words do not attempt this project if you do not have a basic understanding of electricity. You can easily burn yourself, cut yourself, stab yourself, or put an eye out if you are not careful. Do not proceed without the proper knowledge and skills needed.
In taking the Large Motor class from Randofo I stole the following additional safety warning: "In fact, if the motor can take off your finger, there is no reason that the thing the motor is attached to couldn't crush or run you over in all kinds of dangerous or potentially lethal ways. This is not even to mention the danger of high-speed crashes." I feel this is a valid and important addition to this safety notice. Thank you Randofo.
Tools needed:
Soldering station (or iron), flux, solder, drill and/or drill press, hack saw or cut off grinder, screw drivers, wrenches, grinder, box knife, marker, tap/die, tape measure, metal drill bits and a vice. These are minimum tools used.
Supplies: This is an extensive list and I have done my best to tell you what part numbers I used. This is was not an easy task as I robbed a bunch of parts from my work space and started accumulating parts two years ago.
MX500 or MX650 - Used from Craigslist $150 to $250. I have four (two of each MX500 & MX650) that I have bought at $150 apiece, but I have not cared about condition of most of the components. One even came without batteries or a charger.
1x Controller - 48 Volt Controller 65A (Model: YK42-4) Item# CTL-101215 from TNC Scooter. I believe this is the correct one that I used, but verify before you buy. (I switched to Speed Controller SPD-SD1000-6 from electricscooterparts.com after burning up the 65 A controller in a couple of rides.)
2x Motors – 750W Razor motors
Rear Sprocket - 50 Tooth Sprocket Item# FH-SPROCKET-50, Bikeberry.com
Motor Sprockets – 11 Tooth Dual D-bore Sprocket for ½”x1/8”Bike Chain SPK-106022, tncscooters.com
Batteries – Turnigy Multistar 6S 12000mAh 10C Lipo
Amp Meter – Water proof DC, small digital volt meter .56” LED green
On off switch - Battery Power Disconnect Rotary Isolator Kill ON OFF Switch A802
Bike chain – 410 chain, Same as BMX chain at a bike shop
Mountain bike shock – DNM AO42AR Mountain Bike Shock w/lockout 200x57mm
XT 90 connectors - SummitLink 10 Pairs XT90 Male Female Connector for High-Amp Lipo Batteries
200 A Fuse - Baomain ANL-200A Electrical Protection ANL Fuse 200 Amp with fuse holder
Bullet or Spade connectors – 12-10AWG insulated Male and Female, Can use smaller gauge for this step.
Ring connectors – Big enough to fit the posts on the switch
Misc. nuts and bolts
10 or 12 gauge wire
3 each hose clamps – From Ace Hardware I do not have the part numbers. I believe that it is two of the largest that they stock and one of the next size down. Some clues in the photos might help select the right ones.
1/8” x 1” x 3’ flat bar iron stock
Step 2: Strip Down the Donor Bike
My donor bike for this project was a Razor MX650. They come stock with a 650W motor, 36 V system and a 30 Amp controller.
In the words of Razor’s marketing materials:
Here are the specifications and features that make the MX650 a truly top-of-the-line electric motor bike:
The chain-driven 650W electric motor can offer variable speeds of up to 17 mph. When assembled, it measures 56″ x 24.5″ x 36″ and weighs 98 pounds. The power comes from three 12V sealed lead acid rechargeable batteries. The charge time is 12 hours. It comes with a battery charger, along with other tools needed for assembly and maintenance. The MX650 Razor can run up to 40 minutes or for 10 miles (although this can be longer if the rider is smaller and lighter). It comes with some similar features found in the less powerful MX500: Twist-grip acceleration control, hand-operated dual disc brakes, Dual suspension and adjustable riser handlebars, large 16-inch front and 14-inch rear pneumatic tires, double crown fork, folding metal foot pegs, and a retractable kickstand. The super-cross inspired scaled down dirt bike design can carry up to 220 pounds.
If this stock bike description sounds good enough for you and your friends then you can stop here.……, but I am replacing everything; LET'S GO!
So I started by stripping down the bike. I took everything off the bike, including all plastics, batteries, motor, and cables. Leaving only the brake levers and tires on.
It may seem quit a task to even begin, but it takes mere minutes to clear the bike down to the frame. Something like 15 minutes if you have done it before. Donor bikes usually have stripped out bolts, rusted parts and the like as they have been worked on by others without proper tools somewhere along the line so it may take just a little longer to remove stripped out hardware.
As you can see it is a robust little bike that Razor makes. In this picture the bike is stock except for the mountain bike shock is already installed and the rear sprocket installed. (I did end up turning the sprocket around from where it is shown here to line up better with the motor sprockets.) The weak links in stock Razors for a build of this kind are the front shocks and the small disk brakes. Both work, but could be better for the monster we are about to create.
Step 3: Starting to Put It All Together. Sprockets and Shock Absorber.
The build needs to begin somewhere so let’s start with the sprockets. The easy two are the ones located on the motors. I am replacing the stock chain and sprockets so that it can stand up to the abuse I will be throwing at it. Remove the stock sprockets from the motor using a socket and a wrench to hold the shaft. Install the larger sprockets.
I use large sprockets designed for custom bicycle builds for the rear and have tried two different sizes. The first build I took it to a machine shop along with the stock sprocket and asked them to cut the center hole larger to fit and to cut in the bolt holes to match up for mounting. My second build, which is this one, I cut the hole with a drill press and a hole saw. I recommend going with the machine shop option. My results were good, but it is a difficult process for sure. I then bolted the stock sprocket to the custom sprocket for added support though probably not a necessary step.
The mountain bike shock fits right in where the stock shock was located without any modifications. It even uses the same bolts. You can add some thread locker to these for peace of mind. This will lift the bike up and look much cooler in addition to giving support enough for larger riders. The shocks are adjustable to different riders as well using a quality bike pump that is capable of high pressure.
Step 4: Getting Tougher Now. Let’s Install the Motors.
I removed the stock 650 W motor and I am replacing it with two 750 W motors. You can change this step up. You can go with the stock 650 W motor by itself and save some money. It may or may not hold up to the abuse that is to come. You can also put in a single 750 W motor that will bolt right into place, but it too may or may not survive very long with the rest of the changes. I believe that the motors with two of them are going to hold up to the abuse of a 40 A or 65 A controller and 50 Volts just fine.
I am going to explain most of this section with photos. I bolt the rear frame bolt to the top motor and twist the motor up as high as it will go and tighten the bolt a little bit to hold it in place. I then cut a piece off of my bar stock and drill holes in it to mount up the front frame hole to the motor. Some of the brackets need some minor bending to fit flush on the motors and/or frame. I will try to call attention to these in the photos.
There are some important notes here. If you remove both bolts the motor will come apart and it can be difficult to put it back together in the right position and to push the brushes in to close the case. To avoid this just work with one bolt at a time. If you over tighten the motor bolt you will break the housing and shrapnel will get into your motor and you will need to take it apart to remove the pieces. Don’t be that guy. On this built I also used slightly longer bolts to give me an attachment point on the other side of the motor and to avoid cracking the cast case. I had these longer bolts in my garage, but they could be purchased from Ace Hardware or anywhere with a decent bolt selection.
So far we have the left side of the top motor attached to the frame in two spots. Now take the second motor and attach it below the first motor and to the front of the swing arm with the smaller hose clamp. Tighten firmly, but not too tight yet. Add the other two larger hose clamps at this time to tie the motors together and tighten a little. The motors should still be adjustable to align all the sprockets. The bracing can now be added to the right side as seen in the photos. Make sure that the sprockets are all in a straight line with each other and then tighten your bracket bolts and clamps.
Step 5: Installing the Batteries and Controller
First a little bit about the batteries I chose for this special build. I went with 22.2V 6S 15C Graphene because I was dying to try them. Go back to the stock specs and you will see 12 hour charging times for the sealed lead acid batteries that come stock from Razor. The Graphene shortens this to something like an hour at complete discharge. The down side of course is cost. Graphene is expensive, but oh so very cool. I built the first bike with four sealed lead acid batteries so I just ordered Lipo batteries for the rework of the MX500. I am going to share the part numbers for the Lipo batteries as they are more cost effective and still have excellent performance. There is also a 20 Ah battery pack for the same Lipo batteries that I listed. It costs a bit more, but would be worth it if you want longer run time.
I have two battery packs wired in series to create 44.4 volts. These batteries are 12 Ah batteries. Ideally I would like to add two more batteries wired the same as the first set and then wired in parallel so that I can get up to 24 Ah and 44.4 V. Unfortunately the batteries are expensive and the added range comes with a large price tag.
Another nice benefit is that the replacement batteries are a fraction of the weight of SLA batteries, and they fit side by side in the same tray that the stock batteries came out of. I just cut and bent the bracket that locked the original batteries in place and used it for the new batteries. See photo.
Zip tie or bolt your controller somewhere near the batteries.
Step 6: Adding a Power Switch and Volt Meter to the Stock Plastic Tank.
This is the last step before wiring it all up. Measure your parts and cut holes out the plastic to fit them. This creates a really clean look.
Step 7: Wiring
Please use some common sense and caution as you are working with some decent voltage here. First I solder the positive wires from each motor together then to a 10 or 12 gauge jumper wire. Then do the same with the negative motor wires. To the end of the Positive and the Negative motor wires I solder on a XT90 fitting. The other end of this is connecting to the Controller Wires labeled for the motor. They too get an XT90 fitting to mate up to the motor wires connector.
Install the Throttle and add spade connectors to the three wires. Colors vary by manufacturer, but one will be 5 volts, one will be 1-4 volts, and one will be your ground/negative on your Hall-Effect throttle. I used 10/12 connectors for the throttle to controller connection so they will need to be crimped and soldered as these leads use smaller wire. You can use smaller connectors yourself, that just happened to be what I had available.
Add XT 90 connectors to the controller for the power in. Power to the controller comes from two wires. The negative wire goes directly to the battery negative the positive wire gets routed to the fuse, switch, and a jumper wire goes to the volt meter. I will show this in picture format with notes.
A plug needs to be added that connects the charger to the batteries before the switch. I used XT60 connectors for this so that it can only be connected to the charger as it is the only one in the build. We took apart the charger I bought and changed the voltage output to 50.4 which we deemed ideal for the batteries I used. You can call the distributor and request that they set the charger to a given voltage at the time of purchase. This is probably better as I would hate for you to destroy your charger or get shocked.
Step 8: Finishing Up the Build
You can now connect everything up and reinstall your tank, seat, and if you desire engine covers. I left mine off. You may bolt your controller to the frame or simply attach with zip ties. Also cut the #410 chain to length and install.
Accessorize. Add custom paint, lights, mirrors, or whatever makes it unique to you.
Before you set off on an initial test run there are a few things you should do. Make sure that there is air in the tires. Make sure the brakes work well, make sure all of the bolts are tight and all systems look right. Set your shock pressure to your weight. This can be done by bouncing on the seat and watching how far the ring goes down the shaft. If the shock bottoms out add some air and if it barely moves down the shaft then remove some air.
Step 9: First Ride
If you have never ridden electric vehicles before be aware that they are all torque. This bike will put you on your butt in the street if you just hit the throttle full. Start slow and gain confidence. Always wear a helmet.
I told my wife and kids not to let anyone ride the first build. My wife being experienced with motorcycles did not think it was a big deal until she put her friend on it who had never driven a motorcycle before. Unfortunately she immediately rode it full throttle right into the back of my Explorer.
This bike in this set up will do over 30 miles per hour with someone my size on it. Even faster with smaller riders. Keep in mind that the frame, tires, brakes and front shocks where not designed for this stress so build and ride at your own risk. If you find that it is too much of an animal then tame it by changing out for a 40 A controller.
I should note also that I did not use the brake cancel switches to cut power to the motors when the brakes are applied, but many controllers will accommodate this feature and it REALLY SHOULD BE INSTALLED. UPDATE: WE FRIED THE 65 A CONTROLLER IN JUST ABOUT 20 MINUTES OF TOTAL RIDING. WHEN IT FRIED IT PEGGED THE THROTTLE FULL ON AND TOOK OFF IN A WHEELIE. MY DAUGHTER GRABBED BRAKES AND SHUT DOWN THE POWER SWITCH WITHOUT INCIDENCE, BUT USING THE BRAKE CUT OFF SWITCH WOULD HAVE CUT POWER TOO.
I still need to work out a chain tensioner that works and that is not too loud when driving, because part of the charm is how quiet these bikes ride. It is like a stealth bike; they do not hear you coming.
Step 10: Conclusion:
I am not an electrical engineer. I am not an expert in electric vehicles. If you do build one of these be aware that there are serious risks involved. Your build is dangerous to ride (A helmet and protective clothing should always be worn). Parts are expensive and you could fry components at any time. Let me say that again,"Parts are expensive and you may/will burn them up." I am reasonably confident that this build is going to hold up for a while, but it is not time tested for durability yet. With roughly 10 miles on it, it is too soon to know how it will hold up to extended running. UPDATE: BURNED UP THE 65 A CONTROLLER AND MOVED DOWN TO 35 A. AFTER TRYING A FEW CONTROLLERS WE DECIDED THAT 35 A WAS PERFECT FOR MY WIFE AND SHOULD GIVE A DECENT RUN TIME AND EXTENDED RANGE. JUST SO YOU KNOW, THE 100 AMP CONTROLLER WAS COMPLETELY UNRIDABLE FOR HER.
This is an expensive project and it does take some time and skill. I believe that I could complete a total build of one now in about 12-15 hours, but your first one will take more time by far.
I did a speed test with my Daughter tonight. It tops out at 30 MPH which is plenty fast for a bike this small. It was moving around a bit at speed which I do not feel much when I ride. Best guess is that it has a range of close to 5 miles at around half throttle.
I had so much fun and was so happy with the results that I will now rework my first build, the MX500, and I will share some photos and insight to this Instructable when I complete the changes.
I am always open to questions and comments and will do my best to answer any questions you might have.
Step 11: The MX500 - First Build
I referenced the MX500 first build so many times in this write up that I thought maybe I should show it and outline some of the differences. It is a 48V SLA system powering twin 500W motors with a 100A controller. It is heavy with the four SLA batteries, but it really gets up and goes with the 100A controller. Initially I was burning up wires and had all kinds of issues. I am going to rework it so that it is set up closer to what this build is and hopefully put an update to this Instructalble when done.
UPDATE: FINALLY REWORKED THE MX500 IN AUGUST 2019. I PUT THE GRAPHINE BATTERIES ON THIS BIKE (AND REPOWERED THE MX650 WITH THREE 20Ah LIPO BATTERIES). I LEFT THE 100A CONTROLLER ON THE MX500 AND THE TWIN 500W MOTORS. I TRY TO DRIVE MOSTLY AT POSITION ONE OR TWO ON THE HALL EFFECT THROTTLE USING ONLY SHORT BURSTS OF POSITION 3 OR 4 TO AVOID OVER HEATING THE MOTORS. BOTH BIKES SEEM TO BE HOLDING UP TO THEIR ELECTRONIC SETUP SO FAR, BUT I THINK FULL OUT RUNNING OF THE THROTTLE FOR ANY LENGTH OF TIME WOULD OVERHEAT THE MOTORS. BOTH BIKES ARE A BLAST TO RIDE. I FLIPPED THE MX500 ONTO MY BUTT RECENTLY SO AS PREVIOUSLY WARNED IF YOU BUILD ONE OF THESE PLEASE EXERCISE CAUTION WHEN RIDING.
See the photos for some notes and possible ideas for changes you can make to your build.
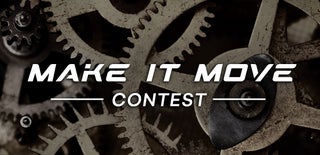
Participated in the
Make it Move Contest