Introduction: Build Lifesize Space Marine Armor in 352 Terribly Complicated Steps
When I was a kid I happened past a hobby store in Petaluma, California that carried rulebooks and miniatures for Warhammer 40,000, a tabletop wargame from Games Workshop. I immediately fell in love with the rich, dark universe and the heavy, brutal designs of the characters, vehicles, and weapons. I ended up getting a job at that same store and spending nearly every penny I earned collecting, building, and painting the models.
Years later I've developed a bit of skill collected some helpful tools that allow me to make some reasonably impressive costumes. I've taken on project after project, but no matter what else I've built, I've always found myself thinking back to those beloved characters from my youth.
After trying to talk myself out of it for years, I've finally accepted the fact that I must build Space Marines in all their glory or I would never be satisfied with any of my lesser projects. To do it right, the finished characters would have to be about eight feet tall and four feet wide. Given that requirement, the main challenge was to make all of the pieces lightweight enough to still be a wearable costume.
With that goal in mind, most of the components were vacuum-formed in thin sheet styrene or ABS plastic. Some of the more intricately detailed parts were sculpted in Magic Sculpt epoxy putty or molded and cast in urethane resin. The whole project ended up taking about three or four months worth of actual work spread out over about ten months worth of the calendar.
While I suppose I've got a bit of experience with this kind of project, I will admit that this tutorial is not the end-all-be-all resource for this sort of build. The intent is to inspire other people to take on similar projects. I encourage you to do more research and spend some time gathering additional references before you begin. I may have done everything the hard way.
It's also important to point out that Space Marines are the copyrighted intellectual property of Games Workshop and I have used the design without permission. I'm a fan and these suits are a tribute to a rich universe that I have always loved. This project is in no way endorsed by Games Workshop. Instead, I decided that there just wasn't enough Warhammer stuff walking around in the world, so I took it upon myself to help.
In describing this project I tried to be as brief as possible, but there's simply no way to describe all of the hours and days and weeks and months worth of work that went into this project in 50 words or less. Since it is a bit on the long side, I've at least tried to keep it entertaining. So pour yourself a beverage of your choice, get comfy, and let's begin...
Step 1: Building Forms in Pepakura
To download the program, go to http://www.tamasoft.co.jp/pepakura-en/
Once you've downloaded it, register your copy. It's a good idea to keep encouraging the developers to continue improving the program. Besides, at the time of this writing, it only costs $38 you cheap bastard.
After installing Pepakura you need to get your digital 3D models. With a bit of Googling, you can find models available for all sorts of things. I found the models I used while looking around on Obscurus Crusade, a Warhammer 40,000 costuming forum.
Now that you have your digital files squared away, here's what you'll need to build them in paper:
Cardstock paper. At least a ream. Possibly two. The heaviest thickness you can get at your local office supply store.
Cyanoacrylate adhesive (brand names include Insta-cure or Zap-a-Gap)
CA accelerator (aka "Zip Kicker" or "Insta-Set")
Scissors (don't run with them)
A sharp hobby knife (don't run with that either)
A cutting board (this you can run with. Run your little heart out.)
Music or movies to play while you're working so you don't go insane from the tedium of cutting and gluing.
Print out the pep models. Make sure to turn on the edge ID settings so you'll have little numbers along each edge to match up with their counterparts along the way.
Use the scissors to cut out each piece as you need it. This will make it easier to keep track of the pieces so you don't have to go sifting through a pile of parts to find the one you need like some sort of jigsaw puzzle turned into a psychological torture device. If you have your computer nearby, it's a good idea to keep the program open so you can use the "check corresponding face" function to identify and locate each piece as you're building them rather than just poring over the printed sheets looking for matching edge ID numbers.
Once the pieces are cut out, use the hobby knife to score the lines where the creases will be. Then pre-fold each crease.
Use the CA glue and accelerator to bond the parts together. Make sure to keep everything properly aligned while you are working. The numbers on each seam should line up opposite each other. If you get the edges a bit off, each mistake will compound and make each following mistake a bigger problem. It's a good idea to start with some of the smaller pieces to get the hang of how the process works before you waste a bunch of time and materials by learning on a large piece.
If you can shanghai a friend into helping, you can set up a workflow that will really speed up the process. When I have help, I do the folding and gluing and leave the cutting and scoring to the other guy. Here's a quick timelapse video showing the construction of an arm model as well as a kneecap:
Step 2: Reinforcing the Forms
Once you've assembled the paper models, you need to toughen them up so they'll withstand the crushing power of the vacuum forming process. This is a job for fiberglass.
Fiberglass is a composite structure comprised of glass fibers saturated with a plastic resin. By themselves, either of these materials have very poor strength characteristics (the resin has no tensile strength and the glass has no shear strength) but when you combine them you get the best of both worlds.
For this step you'll need the following:
Fiberglass resin and hardener
Fiberglass mat
A graduated mixing cup
Mixing sticks
Disposable brushes
Rubber gloves
A respirator with an organic vapor filter (chicks dig scars, but it's hard to show them the ones on your lung tissues)
There are lots of resources that can help you out when it comes to learning to lay up fiberglass, so do some reading of your own before you tackle this part of the project. Also bear in mind that pretty much all of the ingredients are bad for you, it will make a mess, and the fumes probably kill kittens. Be sure to read all of the manufacturer's warning labels and instructions before you begin.
Once you've done your research, go ahead and mix up a batch of resin. I usually work in batches of 8-12 fl.oz. so I've got plenty of time to use up the material before it begins to harden. Using a disposable brush, spread a thin coat of resin over the inside of the paper model. Let this initial coat harden to stiffen the paper and keep it from warping under the weight of the fiberglass mat.
Once the first coat has cured, tear off patches of fiberglass mat and set next to the resin-coated paper model. Mix another batch of resin and coat the inside of the model again. Place the patches of mat into the resin one at a time, then use the brush to work the resin into the fibers of the mat and to massage out any bubbles that may have been trapped in the process.
Experience will give you a good idea of how thick you need to build up your fiberglass composite. Until you get a good handle on that, just go with the brute force concept and make it heavier than you think it should be.
Fun fact: atmospheric pressure is 14.7 pounds per square inch. When you place these pieces on the vacforming table, all of that pressure will bear down on them. The chest parts will be roughly 14 inches by 25 inches, for a total of 350 square inches. That means it'll have to withstand a total force of 5,145 pounds during the forming process. This is about the same as parking a Ford F-250 pickup truck on top of it. So when you think you're done, go ahead and build up another layer of fiberglass inside each piece.
Step 3: From Polygons to Smooth Curved Surfaces
Once you've built up enough layers of fiberglass to make your pieces nice and strong, the next thing you need to do is smooth out the faceted surface of the pieces so they'll stop looking like low-poly computer models and start looking like heavy pieces of armor.
Here's what you'll need:
A grinder with a sanding flapwheel
Automotive body filler (commonly known by the brand-name "Bondo" and available at your local hardware store)
A smooth surface and putty knife to mix your Bondo
A flexible plastic spreader (probably for sale on the shelf right next to the Bondo)
80-grit sandpaper
100-grit sandpaper
150-grit sandpaper
Eye, ear, nose, and throat protection so you don't fill your delicate parts with nasty, nasty glassfibers.
Use the grinder to take down the corners on the paper model. An 80-grit flapwheel will make quick work of the fiberglass and paper, but it will also make a huge mess of nasty, toxic dust. It's best to work in an outdoor area and you'll still want to wear eye, hearing, and respiratory protection.
Once you've knocked down the high parts, you'll want to build up the low, flat spots with some Bondo. Use a flexible spatula to spread the material out over the surface and build up a smooth curved surface.
When working with Bondo, make sure that you only mix up as much as you can use in about ten or fifteen minutes. After that it'll turn solid and you'll end up wasting a lot of material. If you add too much, you can always sand or grind it off after it hardens. If you add too little, you can simply add more after it hardens as well.
Once you're satisfied with the smooth surface you've created, it's a good idea to spray on a coat of primer to get a uniform color to get a better impression of how smooth the actual surface really is. Chances are you'll discover that you're not as done as you thought you were and you'll want to add more Bondo and do more sanding.
You'll repeat all these repetitive steps repeatedly for all of the individual armor components. It's going to make a mess wherever you're working as well as quite a ways downwind. Consider this when choosing your workspace.
If you're like me, you never make one of anything. To make these forms into the basis of an army, proceed to the next step.
If you're a rational, sane person, you can skip ahead to step 8 and use the smoothed, reinforced paper models as one wearable costume.
Step 4: Turning the Reinforced, Smoothed Paper Models Into Vacforming Bucks
Vacforming is the process of heating a sheet of plastic, stretching it over a form, and then sucking the air out from underneath. When the plastic cools, it stays in the same shape it was stretched over. As long as there are no undercuts where the plastic will be locked onto the form, the sheet will pop back off and you can use the form to make another copy of the same shape.
In order to turn these pieces into usable forming bucks, they'll have to be cut apart. Since they all have compound curves, the best way to mark a cutting line is with a laser level and a marker. Using the laser level I was able to identify a slicing plane which I could mark on the pieces with a pen and then I could follow the cutting line with a jigsaw.
Most of the pieces just have to be cut in half to make front and back pieces. The most complex shape is the chest armor. To avoid undercuts it had to be cut into three pieces: top, front, and back.
Once the pieces were cut apart, the next step was to add a border around the new open end. Using scraps of MDF, a border was built around the edge, making only the slightest offset. When you form the plastic over it, this offset will become the cutting guide you follow when you do the final trimming on the pieces. Once the border is built up, fill in the open ends by gluing more cardstock over the holes and reinforce this new cardstock with more fiberglass. While I was at it I went ahead and laid up yet another layer or two of glass mat over the entire interior of each piece.
In one of the attached pictures you'll see that the fiberglass is laid up to roughly 1/4" thickness. If yours is thinner, you may want to add another layer. Remember, you'll need to park a pickup truck on top of these things.
Step 5: Vacuum Forming
Now it's time to start melting plastic. If you don't have a vacuum former, and you don't want to spend thousands of dollars on a professional machine, you can build your own. In this case, I'm using the 2'x4' table I built a year or so ago which you can read about on my blog here: http://protagonist4hire.blogspot.com/2011/05/homemade-vacuum-forming-machine.html
You should also check out studiocreations.com, stormtrooperguy.com, Volpin Props' recent vacformer build, and the very helpful Prop Builder's Molding and Casting Handbook by Thurston James for some great insights into building your own vacforming machine. Once you have one, you'll wonder how you ever managed to build anything without it.
The principles of operation for these machines are pretty simple. First, you lay out your forming bucks on the forming surface (called a "platen" if you're the kind of person who gets off on technical jargon). Then you clamp a sheet of plastic into a frame that holds it by the edges. The sheet is then heated until it becomes soft and stretchy. The frame is then pressed down over the forming bucks and a vacuum system sucks the air out from under the sheet through the platen. When the plastic sheet cools, it stays the same shape as whatever forming bucks you placed under it.
Here's what you'll need for this step:
A vacuum forming machine
A metric butt-ton of plastic sheets cut to size for your frame (I used both black .040" ABS sheets and white 1/16" styrene sheets)
A nice, warm day
Plenty of ventilation
Utility knife (also called a "drywall knife")
Tin snips or shears to do some rough trimming
Gloves (the oven, frame, and plastic get really frakkin' hot)
A small amount of real estate to stack up lots of pieces of armor
I've never really quite finished building my vacforming machine. I've got a great plan for a lifting mechanism that will move the plastic clamping frame up to the overhead oven and down to the forming platen. Until I finally get around to making that last mechanism, I'm still stuck begging friends and family members for help with moving the frame from the oven to the platen when it comes time to use the machine.
When laying out the forms on the platen, you want to put them close enough together to minimize the amount of plastic you'll waste between parts. You also need to place them far enough apart to avoid any "webbing" that occurs when the plastic creases and forms a ridge between two high points during the forming process. Practice and experimentation will make this make more sense.
As each piece is formed, it's a good idea to alternate between forming bucks rather than use the same ones over and over again. This is because the fiberglass will begin to soften slightly as it gets warm. If you don't give it time to cool down between uses, you may well end up crushing some of your forms and have to go back and re-do much of your hard work with toxic substances.
As the plastic cools, you can use a utility knife to score the surface between the parts so you can snap or tear them apart. Then use the shears to rough cut the pieces so they can be stacked up and take up slightly less space.
At this point, you'll start to notice a lot of plastic scraps piling up. You'll want to separate them into two classes: nice, smooth, flat pieces that will be useful later, and misshapen, twisted, formed wierdness that needs to go to the recycling center to be made into toilet seat covers or whatever.
NOTE: Heating up sheets of plastic like this will release all sorts of noxious fumes. I'm not a doctor, but I'm sure these fumes are probably the leading cause of nostril cancer or some such thing. Be sure to work in a well-ventilated area. Respirators are still a good idea.
ADDITIONAL NOTE: Do not leave a fuel source and a heat source in close proximity to each other unattended at all. Ever. I wish I didn't have to point that out.
Step 6: Other Forms
While the Pepakura-built forming bucks are great for some of the more complex curved shapes, there are other parts of the build that don't really lend themselves to the same process. Specifically, the weapons and the backpack. These are mostly simple geometries with large flat surfaces.
Rather than try to build a pep model and keep the large flat surfaces flat during the reinforcing process, it's easier to just make them out of large flat pieces of material that will already be strong enough to use for vacuum forming.
For the backpack I printed out a couple of photos of the miniature and blew them up to fill an entire sheet of paper. Using these pictures as a sort of blueprint, I cut pieces of 3/4" MDF to make the shapes I needed to build the backpack.
The forms for the guns and the chainsword were made in pretty much the same manner. I also used random little blocks of MDF with the corners routered down as forms for various patches and inserts. That'll make sense later.
Step 7: Trimming and Assembly
Now that you've formed all of the parts, the next step is to do the fine trimming on all of the parts. This is where you'll spend a lot of time trimming and test fitting pieces. I use a pair of tin snips and/or a hobby knife to do the cutting.
To glue the parts together you'll use a solvent cement to chemically weld the parts together. For the styrene I used Weld-On #4 adhesive. For the ABS parts I used hardware store ABS pipe cement. For the rare places where I needed to bond ABS to styrene, I used Weld-On #16.
This is where you'll need those nice, flat scraps you set aside when you did the rough trimming. To bond the separate parts together, you'll glue a piece of scrap behind one of the edges so it hangs out about 1/2". Then butt the edges against each other, gluing the scrap to the second half. Use pairs of rare-earth magnets to clamp the parts together while everything is drying.
At this point, this project will start taking up a heck of a lot more space. Apologize to your neighbors, roommates, and family members in advance.
Step 8: Parts That Don't Lend Themselves to Vacuum-Forming
When this happens, it's time to invest in some silicone RTV moldmaking rubber and learn a whole new set of skills. I'll refer you once again to Thurston James' excellent opus: the Prop Builder's Molding and Casting Handbook. I own three copies of it because they keep getting abused and the pages are all stuck together.* If you're going to tackle a project like this, I'd recommend getting at least one.
For this particular project, I used methods detailed in that book and made one-sided silicone rubber block molds for pieces like the charging handles on the bolters, and the teeth for the chainsword. I made two-part molds for the pistol grip and some of the other small widgets. But the most interesting molds were the rotocasting molds for the helmets and the ball vents on the backpack.
The process of making a block mold is pretty simple. You build a watertight box big enough to fit your original into with at least 1/2" clearance all around. Then you pour silicone in to fill it up and cover the original. When the silicone cures, you remove the original and it leaves a hole with the same shape behind. Now you fill that hole with a 2-part urethane resin which will cure and become an exact copy of the original piece.
For larger pieces, this starts to get expensive. Instead, you can create a "glove mold" by brushing the liquid silicone onto the original, then adding layers until it's thick enough to hold up to being pulled and pried at. Once that sets up, you create a rigid "mother mold" to help the flexible rubber retain its shape when the original is removed.
After the mold is made, you can make hollow "rotocast" or "slush cast" copies by pouring a bit of mixed resin into the mold, then rolling the mold around so the resin coats the interior. When the resin cures, it forms a hard shell in the same shape as the original. By adding more and more coats to the inside, you can make the shell as thick/strong/heavy as you like.
There are countless tutorials available online that will tell you everything you need to make silicone molds. I've read dozens of them and even written a few. Here's one of them in my blog: http://protagonist4hire.blogspot.com/2011/07/star-wars-republic-commando-helmet-part_22.html If that's not your speed, here's another one: http://protagonist4hire.blogspot.com/2011/02/warhammer-40000-space-marine-chaplain.html
My favorite video detailing the rotocasting or slush casting process is this one from Volpin Props:
Step 9: Boots and Stilts
Option 1: Get yourself surgically enhanced to increase your height to seven feet or more. This might be expensive.
Option 2: Take the vacformed boot parts, fill them with expanding foam, and wear them like platform shoes. Simple but awkward.
Option 3: Integrate a pair of homemade drywall stilts into the boots. This gives you most of the mobility of option one and will result in less weight than option two.
For me, I decided I only needed to gain around 16 inches in height to look the part. One inch would come from the thickness of the soles on the costume boots. Another inch would come from whatever boots I was wearing on my feet. The remaining fourteen inches would be in the stilts.
The stilts were made out of steel. There's not too much reason for this other than it's what happened to be on hand when I emailed my sketch to Ryan Kertz of Kertz Fabrication. He made pretty quick work of the stilts and all I needed to do was attach the velcro straps (called "onestrap" from strapworks.com) which would wrap around the wearer's foot and leg to keep everything stable.
Once I had a functional pair of legs, the next step was to take them for a test drive:
Step 10: Arm Extensions
Making a person look bigger in costume is a challenge in maintaining proportions. If you make someone's legs longer, you'll also have to make their arms longer.
In this case, I needed to make giant hands and add an extra foot or so to the wearer's reach. To achieve this, I sculpted out a pair of palms using oil-based clay. Then I went ahead and sculpted individual knuckles for each of the hands using more clay as well as some wooden balls and scraps of PVC pipe I had laying around. Then I made a mold of each of the parts and rotocast them in urethane resin to make them hollow and lightweight.
Once I had castings lined up, it was just a matter of choosing a gesture* and gluing the finger pieces into place on the palms. For the hands that would be holding weapons, I had to build the fingers around the grips. The assembled hands were then glued onto the end of a piece of 4" ABS drain pipe with a handle inside. The pipe would slide over the wearer's arm inside the costume's forearm and act as a sort of brace to help the wearer wield the weapons and whatnot.
*It was very hard to maintain an adult level of maturity in this stage. If you ever stumble across photos of Space Marines flipping peace signs, giving people rabbit ears, or poking each other in the eyes 3 Stooges style, know that I faltered in a future build.
Step 11: Trimmings
Now that all of the main pieces are made, it's time to get into the details. At this stage, they're huge, but the suits still look pretty naked. This will not do.
The reference artwork from Warhammer 40,000 has all sorts of amazing little details on these suits of armor. Each and every suit is customized with all sort of badges and trim. To keep things simple and relatively quick, I settled on only the very basic bits of trim. Each suit ended up getting a winged icon of some sort on the chest and a handful of purity seals.
Since I didn't want to sculpt wings over and over again, once I had a pair I was happy with I went ahead and made a mold so I could cast copies and simply glue them onto the armor. To differentiate one suit from the next, I made different icons in the middle of each chest after attaching the wings. Using an epoxy putty product called "Magic-Sculpt" I was able to create a unique sculpture for each one which later hardened and became at least as strong as the resin and vacformed plastic pieces. The first one I sculpted was a skull, then the imperial double-headed eagle, and finally a winged sword.
For the purity seals, I started with a few lumps of clay and pushed a cylindrical object into them to give the impression of wax seals. In the center of each one, I stuck a found item to make them more interesting (things from a small skull sculpture to one of my rank devices from the Navy). Then I went ahead and made a mold so I could cast copies of them in resin.
The ribbons hanging off of the seals are supposed to be inscribed with various litanies and incantations about victory and bravery and devotion to the Emperor of all Mankind. Rather than simultaneously developing my calligraphy skills and carpal tunnel syndrome, I opted for printing out the text using an inkjet printer and a few sheets of Printed Treasures printable fabric, This stuff is a lightweight cotton fabric with a paper backing adhered to it so you can run it through your printer. Once it's printed, you peel off the paper backing and you've got a piece of fabric printed however you like. Pretty nifty.
For the actual text, I found a few things I liked here and there, but after a while I realized that nobody's really going to read them. That's when I started really having fun with them. I started by feeding long strings of text to the Google Latin translator. The text in question included things like the lyrics to the Mr. Ed them song and Ke$ha's "Tick Tock." For some reason I get a chuckle out of the idea of the Saviors of all Humanity waking up in the morning and brushing their teeth with a bottle of Jack.
I also made it a point to include at least one on each suit which detailed Games Workshop's copyright policy with regard to fan-made costumes and a disclaimer stating that these costumes are in no way officially endorsed. These are the largest fo the purity seals and can be seen on the left shoulder of every one of these guys. It's important to make that clear.
After I'd cut each of the strips of text out, the next step was to age them by soaking them in a cup of tea overnight, then singe the edges lightly to give them the look of old paper. The strips were then glued to the back of the resin seal.
The last little touches were some small vent and patch details I made using rounded rectangular scraps of MDF and cast blocks of resin here and there. These mostly show up on the legs, but I'll attach some to the arms and chest at some point.
Sometime later I'll go back and sculpt out a few more random icons to attach to these suits. As any Warhammer fan knows, your character becomes 12.6% more badass with each additional skull icon you attach to him.
Step 12: Rubber
In between the heavy armored parts of the costume are rubber parts that allow the character to have freedom of movement while still protecting him from whatever harsh, alien operating environments he might be campaigning in.
To simulate these I've chosen to make slipcast latex pieces. The process of slipcasting latex is pretty straighforward. I learned everything about it from the tutorials available at monstermakers.com which, incidentally, is also where I buy all of my latex slipcasting materials. This is essentially the same process used to make latex Halloween masks.
The short version: sculpt whatever shape you need using oil-based clay, make a mold using Ultracal-30 or an equivalent gypsum moldmaking compound, remove the clay original, fill the mold with liquid mask making latex, drain the latex back out of the mold, and wait for the remaining residue to dry inside the mold. When the latex is dry, you can peel it out of the mold and you've got a skin shaped just like the original clay sculpture. If you need a thicker skin, you just repeat the pouring and draining process after each layer has dried.
I used this same process to create the rubber bits for the inside of the elbow, the back of the knee, the hip joints, and the neck.
Step 13: Painting
According to Warhammer 40,000 lore, there are 1,000 different chapters of Space Marines, each with their own heraldry, livery, traditions, and so forth. WH40K fans have very deep feelings with regard to choosing a chapter when building their Space Marines. After some measure of soul searching, I was able to decide on a chapter color scheme. These will be Dark Angels. Deal with it.
The first step in turning all of the big plastic pieces into members of the fifth tactical squad of the fifth company of Dark Angels chapter of the Adeptus Astartes was spraypaint. In this case I gave everything a base coat of "Hunt Club Green" by Rustoleum, then went back over it all with their much richer, slightly lighter "Hunter Green." This gave some added depth to the color and started the aging process.
Once everything was a proper shade of Dark Angels green, the next step was to pick out all of the details. For the badges on the chest, this was a simple matter of masking off the not gold parts and using a spray can to put a coat of metallic gold on the gold parts.
For the shoulders I decided that I needed stencils in order to maintain uniformity from one suit to the next. Using unsatisfactory copies of the shoulder pieces which I'd set aside during the vacforming process. Once I'd sketched out the designs on these pieces, all I had to do was cut them out using a plastic cutoff wheel in my Dremel rotary tool and voila: I had a stencil which would conform perfectly to the compound curved surface of the shoulder pad.
I made three such stencils: the chapter logo for the left shoulder, the red double arrow for the right shoulder, and the white numeral 5 for the right shoulder. The red was a combination of "Colonial Red" and "Paprika" in different sheens to make it look a bit old and faded. The white was "Shell White" which should be called "Bone White" but some marketing group probably decided that was too scary for people to buy it. After the stencils were sprayed with their respective colors, I decided that they still needed quite a bit of touch-up with a small artist's brush.
Once all of the details were picked out, the next step was to add some aging and damage. According to the in-game mythology, these suits would be passed down from warrior to warrior for hundreds and hundreds of years. They absolutely cannot be left all shiny and new-looking.
To add a bit of wear and tear, I took a cheap brush, dipped the very tip of the bristles into a can of oil-based "Aluminum" colored paint. Then I wiped most of it off on a rag and used the nearly dry brush to simulate scuffs and scratches on the pieces. During this process, I focused heavily on the edges where the parts would be most likely to wear and show abuse.
When the scratches and scuff marks had dried, the last step in the painting process was to apply a blackwash over the whole thing. A blackwash is basically a coat of watered-down black acrylic paint that seeps into all of the nooks and crannies and helps make the details stand out better. I learned this technique from painting Space Marine models as a kid.
At this stage, much like all of the others, it's important to resist the urge to try on all of the pieces and waste precious hours doing silly things in front of a camera.
Step 14: Making Puny Humans Into Superhuman Space Warriors
Fun.
Since my plan was to debut these suits at a crowded event, I told the other guys that were helping me with the project that the only way I'd be willing to let them wear one of the suits in public is if they first spent some quality time walking around in and near the workshop wearing at least the stilts. That turned out to be a good idea:
Later, after a near-fainting incident, we also decided that nobody would be allowed into a suit without first swallowing at least 10 ounces of water.
As the guys got more proficient and comfortable with the stilts, we started adding more and more of the parts until they were eventually strolling around in all of the parts.
Dressing each wearer in a suit required at least two people. One to lean against while standing on a stool or bucket, and one to reach in through the kneecap and fasten the velcro straps around the wearer's shins and feet.
You can see some of the dressing process in this video from Tested.com when they interviewed me at the 2012 Bay Area Maker Faire:
Step 15: Show Off
Now that you've got some serious-looking ginormous battle armor, the only thing left to do is to take it out in public and amaze the heck out of everyone you meet.
It's also a good idea to find a few followers of some lesser emperor and make them feel inferior.
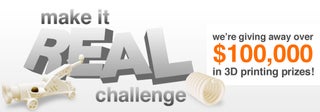
Grand Prize in the
Make It Real Challenge
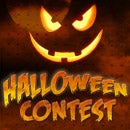
Third Prize in the
Halloween Epic Costumes Contest