Introduction: Build a Motorized Barn Door Tracker...
...shoot stars, planets and other nebulae, with a camera that is.
No Arduino, no stepper motors, no gears, just a simple motor turning a threaded rod, this barn door tracker rotates your camera at the exact same rate as the rotation of our planet, a requirement for taking long exposure photos.
The concept isnt new, its been around since the 70's, back in the days of 35mm film, my version updates it to motor drive and adds a corrective cam to remove the inherent error in the original version.
Briefly, the common ways of doing this are the single hinge 2 boards with a straight threaded rod, the single hinge 2 boards with a curved threaded rod and the doubled hinged 3 boards version.
All versions can be motorised, but the 2nd version with the curved rod has the motor driving a nut through gearing and the curved rod is held stationary.
An example here of Dennis Harper's curved rod tracker.https://sites.google.com/site/distar97/
Gary Seronik's fine curved rod tracker here http://www.garyseronik.com/?q=node/52
Finally Dave Trott who invented the double-arm tracker. http://davetrott.com/inventions/double-arm-barn-door-drive/
Step 1: Parts and Tools
Parts
- A decent hinge with very little play, I went with a solid brass 63mm one seeing as the plank width was 69mm.
- The main part of the tracker, 500mm pine 22m X 69mm.
- The camera mount, approx 300mm of 22mm X 44mm meranti (a hard wood, well harder than pine anyway)
- A brass 1/4" 20 modified machine screw for mounting the camera.
- M8 nut and bolt for mounting the cam mount to the main body.
- M6 rod ~ 90mm with wingnuts and washers for the tilt axis in the camera mount.
- M6 nut and bolt 50mm long for attaching the tracker to the tripod.
- 16 wood screws, 6 for the hinge and 10 for reinforcements in the camera mount.
- A 70mm X 50mm section of plastic cutting board for the corrective cam.
- A 230V AC synchronous 1 rpm motor.
- 2 x steel rods to fit the motor mounts, 4mm in this case.
- M6x1mm threaded rod 135mm long out of which I get a usable length of 90mm, @ 1mm pitch that translates to 90min
- M6 coupling nut to connect the motor shaft to the drive rod with split pins to fit.
- M6 Tee nut for the bottom board's drive rod.
- An existing sturdy mount like a camera tripod or a diy contraption to suit, bear in mind some tripods have a plastic pan tilt head assembly and wobble a fair amount.
Lastly, a camera is also a requirement, preferably a DSLR with remote in order to use the "bulb" setting for long exposures. On my Nikon D70S I use an infrared remote because the camera wont allow bulb setting with the timer, it just overrides with 1/5 sec exposure.
That said, it might be theoretically possible to use a Canon PowerShot (point n shoot range) and load it with the CHDK software to utilise the intervalometer scripts.
Step 2: Some Calculations
So, 360°/23.9344696 = 15.041068635170423830908707498578° per hr = 0.25068447725284039718181179164296° per min to match the diurnal rate.
The M6 drive rod has a pitch rate of 1mm in 1 min, so we need to calculate the length needed to achieve that diurnal rate, ie 0.25068447725284039718181179164296° per min.
1/(tan 0.25068447725284039718181179164296°)=228.55589mm
Nice to know:
- M8 x 1.25 rod would need a rod to hinge distance of 285.69486mm
- M5 x 0.8 rod would need a rod to hinge distance of 182.8447mm
Step 3: Construction Begins
Make sure everything is square and moves freely, clap the 2 hinged boards together and shout "action" a few times like they do when making movies, if it makes a nice clack sound it should work well for a star tracker.
- Now measure 228.55mm from the center of the hinge pin down the middle of the board and mark the drive rod holes, do this on both boards.
- Only drill the hole in the bottom stationary board and hammer in the M6 Tee nut.
- On the top board make the 228.55mm mark which will be needed to line up the plastic correction cam.
- Fit the motor shaft in the drive rod hole and mark the positions for the 2 sliding mounts. These need to be parallel to each other as well as perpendicular to the board to prevent the motor from binding. These were a tight fit in 4mm holes and I forced a M4 nut on top of each one to stop them from dropping out the bottom.
- At this point I made the pan/tilt hardwood attachment for the camera, also known as AltAz in astro circles.(altitude/ azimuth)
Step 4: The Motor
The motor used is a 230v ac synchronous 1 rpm which is very accurate as it relies on the 50 Hz frequency of the main ac supply.
Using a suitable 12v battery with a small inverter, 100w coke can shaped inverters are more than adequate, allows the whole mechanism a degree of mobility for outdoors use too.
The motor was connected to the drive rod with a M6 coupling nut which had one side drilled out to take the 7mm dia motor shaft, seeing as I will be using this in a clockwise rotation, I pinned the threaded part of the drive rod as well to stop the shaft from unscrewing.
Once power is switched on you need to check which way the motor is turning because it can do clockwise or anti-clockwise too. In use it slides freely down the 2 rails which flex a bit, but with no rotational slack. Where the top of the drive rod will ride on the cam was rounded over sanded smooth and polished.
Step 5: The Case of the Growing Hypotenuse and the Corrective Cam
Due to the fact that the boards are moving apart with the drive rod in a 90° fixed position, it is a given that the top board acting as the hypotenuse in this triangle configuration must get longer with time, which causes the boards to open slower as time progresses and is the source of the inherent error in this device.
The last 2 pics of the top board riding on the drive rod illustrate this well.
One of the easiest corrective solutions was discovered by Frederic Michaud and he goes into a nice writeup here. http://www.astrosurf.com/fred76/planche-tan-corrigee-en.html
He proposes a cam which is the involute of a circle, the radius of the hinge pin to drive rod distance of the tracker, and provides a printable jpg here. http://www.astrosurf.com/fred76/images/tan-sans-derive.zip
He also stresses that the jpg must be printed to the scale according to the drive rod thread pitch which in my case was 65mm square.
EDIT 2019: due to dead hyperlinks I've decided to attach the "sans derive" jpg to this step.
There are individuals that have reduced the error by using pivoting points where the drive rod meets the boards to form an isosceles triangle, however these solutions involve a lot more engineering.
My cam was made out of a small section of plastic cutting board, roughly cut to size with a hacksaw and then finished to the curve with a small drum sander bit that would fit in a dremmel tool. I used my drill press to ensure that the curve would be perpendicular to the sides so that the drive rod would track true and not slip off the side.
Step 6: Using and Setting Up
Here in the southern hemisphere finding the southern polar star is a small mission in itself, maybe better luck once my spotting scope arrives, so my work around uses a protractor and a compass.
The compass indicates true south once I've added in the magnetic declination for my location, and taking my latitude (33°52"), converting to degrees (33.867°) gives me the tilt or altitude I need to aim the trackers hinge to. This I printed out using 2D cad and added a nut and thread for a diy inclinometer to hold against the hinge pin.
In use I set the boards open at the maximum angle, I then sight along the hinge pin to the south and tilt it up at the required angle for my latitude, the hinge will be on my left in the east with the motor on the right hand side to the west. Then when switching on the motor I make sure its running in a clockwise direction with the boards closing. Once the device is fully closed, I switch off the power and remove the splitpin from the shaft and twirl the drive rod back up by hand.
In the Orions Belt closeup,(1st pic) a F11 shot @ 100 sec @ iso 200 would have been enough to show some elongation of the star if not a definite trail, the tracker was aligned with a compass and protractor so quite happy even though I havent found the southern polar star yet.
Two examples of tracking on and off over a 5 min exposure.
Last pic of Orions belt is from my Canon PowerSHot A480 using CHDK, 161secs @ iso 200 F4 which the camera saved as a *.DNG raw file fortunately, I was then able to process it in Adobe and saved the result as a jpg.
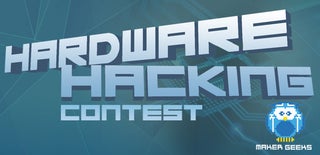
Participated in the
Hardware Hacking