Introduction: Build a Simple Shed: a Complete Guide
Here's a solid little shed I built in my backyard.
It's essentially an 8-foot cube, which is just the right size to store a bunch of bikes, a lawnmower, wheelbarrow, and all my lawn and garden tools.
The design is relatively simple and I was able to complete it for about $1200 (this is 2015 . . lumber prices will likely skyrocket in coming years if we have some kind of pandemic or something).
If you're interested in building a similar shed, this instructable documents every detail of my process from the ground up. If you happen to have a slightly sloped lawn like I do, I'll show you how I worked around that too.
Step 1: Some Considerations
Local Regulations
Before you get too serious about building a shed, be sure to check with your local government to make sure you will be in compliance with any regulations regarding the building of a structure like this.
In the city where I live, my 8x8x8-foot shed is considered an "accessory structure" and did not require a permit to build because it is 120 square feet or less, 8 feet tall or less, and not wired for power.
If you plan to do any digging you need to call the applicable buried utilities hotline in your area and have the various companies come out and mark where their lines run. It's free, painless, and required in most locations.
Design and Budget
My goal was to build a shed that would be rock-solid and long-lasting, with a design that fully maximized my dollars-spent by taking advantage of common dimensions in building supplies . . . hence the 8-foot sizing. (As a side benefit, this design yields very little waste.)
I wanted to keep this around $1000. However, due to the additional supplies needed to build on my sloped lawn and because of a few upgrades, I ended up spending a little over $1200 on the materials for this.
Step 2: Supplies & Tools
This is a brief look at the supplies that were needed to build this. Not everything is listed here (full details are contained in the individual steps) but this will give you a basic idea of what was used:
- Fourteen 2x6 pressure treated 8-foot boards
- About 50 8-foot 2x4s
- Two sheets 23/32" tongue and groove OSB
- Four sheets 7/16" OSB
- One 4x6 pressure treated post (I needed this for my sloped lawn)
- Ten 2x6 joist hangers
- Eight SmartSide siding panels
- Landscaping garden blocks and anchor pier blocks
- One cartridge of landscaping adhesive
- Several cartridges of Dynaflex 230 caulking
- Three packages of shingles
- Roll of roofing paper
- Four 10-foot drip edges
- One cartridge of roofing cement
- Paint: one gallon of main color, one gallon of trim color
- One gallon of Deck Restore paint for interior floor
- Hinges and door hardware
- Large variety of fasteners (screws, nails, bolts, etc.)
Here are the basic tools required to build a shed like this:
- Circular saw (make sure it has a tilting base plate)
- Corded drill
- Cordless drill/driver
- Framing square
- Sawhorses
- Large level
- Hammer and apron/tool belt
- Painting supplies
- Tape measure
- Rubber mallet
- Pick mattock and shovel
Useful tools to have, but not necessary:
- Hammer stapler for roofing paper
- Reciprocating saw or jigsaw
- Air compressor with small brad nailer or stapler (very helpful for trim work)
- Table saw
- Power miter saw
Step 3: Mini Instructable: How to Screw Stuff Together
I used primarily screws for the entire assembly of my shed (even for framing the walls), and I highly recommend the average weekend builder do likewise. Here's why:
For the average DIY-er, way up on the list of must-have tools are a decent corded drill (for drilling holes) and a decent cordless drill/driver (for driving screws).
These two tools are almost universally needed for any type of project, and are more than sufficient for building a small shed like this.
Using screws may take longer when framing versus using a hammer and nails or a nail gun, but you'll make up the difference in how forgiving they are once you make your first mistake and have to take something apart!
So . . .
Before we get started, let's take short detour to briefly go over how to properly fasten things together with screws.
See diagram above for the basics of fastening with screws.
See photo for the style of bits you should get if you don't already have some. This type of bit is a little pricey, and I don't recommend them general purpose drilling--only drilling holes for fastening screws.
Step 4: Lay Foundation Blocks
A small shed like this can just rest on the ground, but it is wise to first create level, firm contact points made from concrete pavers or landscaping blocks.
For an 8x8-foot layout, I recommend placing solid contact points at the corners and at the midpoints along each wall.
I have about a 12-inch slope where I wanted my shed, so I put the upper half directly on blocks buried just slightly in the ground, and the other half up on elevated risers bolted to concrete pier blocks, similar to how a low deck would be built. (There are region-specific regulations on these things, so your needs/requirements may vary.)
This step covers the installation of my upper level blocks, but if you have a fairly even area to begin with the method shown here can be used to lay out all of your ground blocks.
The blocks I used for this are 12" by 8" "Olde Manor" garden blocks from Home Depot. These looked the most beefy and substantial, so these are what I chose to use.
The photos and photo notes cover the details of placing these blocks. The trick is to make sure they are all precisely located as needed, perfectly level with each other, and firmly set on compacted material.
This is a backbreaking step, but should not be rushed or done halfheartedly.
Step 5: Pier Blocks and Risers
For the half of my shed that would be elevated, I needed to carefully position the pier blocks that would hold the wooden risers. To do this I built a temporary frame that was the exact size needed to act as a placement guide.
Making a similar temporary frame may be useful if you are building a shed on relatively flat ground, however, carefully measuring corner-to-corner to check for squareness of the layout of your ground blocks should be sufficient.
Step 6: Floor Frame: Interior Boards
The floor frame and internal joists were all made from pressure treated 8-foot 2x6 boards (trimmed as needed). I doubled up the external boards for added strength and rigidity.
I consciously chose to make this floor very beefy and substantial. You do not want a saggy floor in your shed!
The first layer of boards were fastened as shown here. Where boards were attached directly to the risers I used 3" galvanized 5/16" diameter lag bolts, fastened into pre-drilled holes that were slightly counterbored (so the bolt heads would sit just below the surface of the outer boards).
Everywhere else I used 3" exterior grade screws, fastened into pre-drilled holes.
Where the upper portion of the frame rests directly on blocks I used landscaping adhesive to hold them in place. This same adhesive was used to secure the two blocks on each side that support the frame midway along the slope.
At this point it is critical that the frame is square. Be sure to measure corner-to-corner and adjust the frame as needed until both dimensions are exactly the same.
Step 7: Floor Frame: Exterior Boards
Exterior boards were added to double up the floor frame, lapped at the corners as shown.
Where my frame was attached to the riser blocks I actually fastened this second layer internally so the boards tied in directly to the riser blocks.
This required a bit of pre-planning to ensure that the finished frame was exactly 8 feet by 8 feet, but it all came together nicely.
Step 8: Floor Joists
Galvanized joist hangers were fastened to the frame with galvanized nails every 16 inches.
The joist boards were fastened in place with 3" exterior screws through the joist brackets.
Blocks of 2x6 were then added to the mid section between the joists to provide support to the edges of the floor boards that would meet there. These sections were fastened in between the joists with toe-nailed screws (or would that be "toe-screwed"?)
Step 9: Floor Boards
Two sheets of 4' by 8' tongue and groove 23/32" OSB were used for the floor boards. These were fastened to the floor frame and joists with 1 1/2" exterior screws placed every 8 inches or so.
The "tongue" of the board that was sticking out over the edge of the frame was carefully trimmed off with a circular saw.
Okay . . .
Some of you may be thinking "Hey man, aren't you concerned about your shed racking (shifting laterally) on those risers?"
Frankly, no, I am not.
Because of the relatively short height of the risers and the way they are bolted to the frame, I'm very comfortable with this setup.
That said, if I was dealing with a more dramatic slope and needed risers substantially taller than this, I would not be as comfortable with this simple of a solution.
If I was building a shed on a very steep slope (and was not going the route of building a retaining wall and back-filling it to create level spot), I would cement 4x6 posts deeply in the ground, and create a framework of angled supports fastened from the risers to the floor frame.
That would be kind of fun to figure out, but fortunately that is not needed here!
Step 10: Trusses and the Magic Number
When it comes to framing trusses for a simple structure like this, 22.5 really is a magic number.
If you cut something at 22.5 degrees and want to cut a mating piece to go with it? 22.5 as well. Boom, easy!
That oversimplifies things, but let's just go with it.
The building of the roof trusses as well as the walls is done right on the floor platform. It's basically a large, perfectly-sized work table that acts as a sizing guide as you assembly the components that will ultimately be fastened to it.
For the roof I went with five trusses laid out 24 inches apart. See diagrams for dimensions and details on building the trusses.
Step 11: Framing the End Walls
I framed my all my walls with 2x4 studs set 24 inches apart. You could do the studs at 16 inches apart, but I feel 24" is generally adequate for a shed. (I wanted a super strong and "never-ever-gonna-sag" floor, so that's why I went with 16" centers there.)
I chose to attach the exterior panels to the wall frames prior to putting each wall section up. This requires some planning and careful laying out of things along the way, but when it's time to put up the walls they go up in a breeze!
I began by building the two peaked end walls. These two are built the full width of the floor, so exactly 8 feet wide.
For the height, I wanted to use every inch of the exterior siding panels I bought, so the height of the end walls plus the height of the floor platform together needed to be exactly 8 feet.
The exterior panels will be attached to the wall frames with the bottom edge extending past the bottom of the walls, so the panels will cover the deck sides once the walls are put in place.
On paper the height of the deck should be 5 1/2" plus 23/32", or just a 32nd under 6 1/4".
In real life however, it was closer to 6 3/8". In a situation like this always go with actual real-life measurement rather than what it should be on paper.
See diagram and photos for details and measurements. All of these boards were fastened with 3" screws through pre-drilled holes.
I'll briefly cover framing doors and windows in a later step.
Step 12: Framing the Side Walls
The side walls are framed with 3 1/2" subtracted from the width on either end so they butt up nicely against the insides of peaked end walls.
The exterior panels will be left the full eight feet wide however, so they cover up the end wall frames once all the walls are put up.
Step 13: Framing Windows and Doors
You have a lot of options when it comes to windows and doors on a simple shed like this.
I got an old window from my local Habitat for Humanity ReStore, which I built into one of my side walls. For the door, I needed it in a very specific location, which also dictated the max size I could build it (the building of the actual door is covered later on).
See the photo notes for how I framed mine and for the basics on framing in windows and doors.
Step 14: Install Side Wall Panels
The installation of the wall panels requires precision and a very specific order of steps.
Since the factory-cut panels are perfectly square we can use this to our advantage to pull the frames into perfect squareness as well. The panels are attached with exterior galvanized nails according to the order and directions in the diagrams I've shared here.
If you want the shed to come together nicely, your walls have got to be perfectly square. Take your time and do it right.
Step 15: Install End Wall Panels
The end wall panels are installed in essentially the same manner as the side walls except there is no side overhang to plan for.
Mark and trim off the top corners of the panels as shown.
Step 16: Side Wall Window
The side wall where I put my window required quite a bit of measuring and marking to know where to put all the exterior nails to fasten the panels to the frame.
With the panels in place I removed the material where the window was to go, and installed the window.
Note: Don't remove the paneling where the door is framed in yet. The wall will be too weak without it at this point.
Step 17: Vents
You will want a couple of vents placed somewhere along your walls to maintain some airflow in and out of your shed.
I placed mine on either ends of the the non-windowed side wall (which faces away from my house, so I don't have to look at them).
Step 18: Put Up the Walls!
This is where things get really exciting!
You get to see if all your careful measuring and building was done correctly.
I started by lifting the back end wall into place. I used 4" exterior screws to fasten the wall through the floor board into the floor frame boards. Be sure to use screws that can be fastened into treated lumber.
The side walls were then lifted into place, butted firmly against the back wall frame, and then screwed down through the floor boards into the floor frame.
The corners where the frames meet were screwed together from inside the side wall frames to the end wall frame.
Shorter exterior screws were added all along the outside bottom edges of the panels where they cover the floor frame.
Step 19: Last Wall
The last wall was lifted up and held in place by a couple of people. I climbed in and screwed it in place just as the other walls had been.
The paneling that was covering the door frame was then carefully cut free using a reciprocating saw. This panel will be used to build the door so care was taken to trim it carefully and not ruin it.
The section of the wall frame at the bottom of the door was also removed with the reciprocating saw.
Step 20: Build Roof
The three remaining trusses were screwed to the tops of the wall frames directly inline with the wall studs.
Two sheets of 7/16" OSB were fastened to the trusses with screws (about every 8 inches) making sure the trusses were vertical.
7-inch strips of OSB were added along the lower edges to complete the roof. The amount of overhang was dictated by how I wanted to do the roof trim boards, which is covered in a later step.
Step 21: Intermission
You know, you wait all week for the weekend so you can work on your big project.
. . . And then you wake up to this nonsense.
Step 22: Paint Walls
Once the snow melted I painted the walls.
I used Behr exterior paint, color: Boston Brick.
Step 23: Roof Trim
With the walls painted I added the roof trim pieces.
I decided to use actual 2x4s for this to give the roof a more substantial look.
Step 24: Trim Window and Corners
Trim was added around the window and along the corners. These trim pieces were painted ahead of time and fastened with 1" pneumatic staples.
I used exterior putty to fill the staple holes, and the window and corner trim was then caulked to seal the edges.
Then I went back and quickly did some touch up painting.
Step 25: Miscellaneous Stuff
Here are some miscellaneous items that were taken care of at this point.
Step 26: Roofing
For the roof, I installed architectural shingles to match the ones on my house (mostly) according to the instructions provided by the manufacturer, which are available here.
For a simple shed like this you can either overhang your shingles a couple of inches all around, or install an aluminum drip edge as I did.
Step 27: The Door
There are so many details involved with the building and installation of the door.
See photos and photo notes for specifics.
Step 28: Build Some Shelves
I deliberated for a while on how to include some shelves that would be useful, not waste any floor space, and still provide access to the window. These are what I came up with.
Step 29: Lawn Tool Storage
This is the solution I came up with for some tidy lawn tool storage.
These little hangers were made from 2" PVC.
Step 30: Paint the Floor
I painted my floor with Rustoleum 4x Deck Cover paint so it would be waterproof and durable. One gallon allowed for two heavy coats.
Step 31: Fill It Full of Stuff
My new shed fits all the stuff I've put in it so far!
Step 32: Thoughts
Whew!
Thanks for sticking around till the end. I think this is the most detailed documentation I've ever done for a project of mine. I sincerely hope it will be useful to many people.
This was a fun project and very rewarding!
I hope you'll build a similar shed. If you do, be sure to share some photos in the comments. As always, thoughtful feedback is appreciated. Thanks for taking a look!
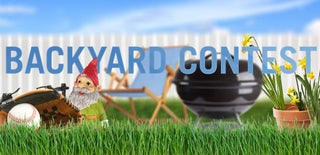
Participated in the
Backyard Contest