Introduction: Build an Awesome Sewing Box
I decided that I wanted to build my girlfriend a new sewing box for her birthday, and instantly knew that I wanted to make one that cantilevered, just like tackle boxes and traditional sewing boxes. Searching the internet for mathematical help, I discovered that none exists. As a result, I have decided to just figure it out the hard way and share my results.
Step 1: How My Box Works
My box will be 300mm long by 200mm deep, and have 2 tiers, plus a lid. I want there to be approximately 30mm of overhang between the top and bottom tiers when the box is open. The lid will be opened with the same movement as the rest of the box. The top tier will be about 60mm deep inside, which is the approximate length of a spool of thread, and will be divided into compartments. The bottom will be about 100mm deep, and will be a spot to keep larger things. If you want the same dimensions, carry on with the instructable. If not, now is the time to sit down and think about what you want. If your dimensions differ from mine, you'll have to alter the instructions to suit, obviously.
Step 2: Think About Your Boxes.
To make this box, you essentially need to build two boxes with identical footprints. I've chosen to use finger joints for the corners, and locked rabbet joints to secure the lid and base. Because the timber that I bought is 66mm wide, I've had to think about joining the boards along their length to make panels big enough. I decided to make tongue and groove joints for this.
Note that the finished box will have 2 bases and one top. Many people make a box by assembling 6 panels together into one sealed box, then sawing it into two. You can do that for both halves of this box if you like, but I decided to make one open box for the bottom, and one sealed then split for the top box + lid. If you do it the way I chose, you'll need 11 panels in total, if you do it the other way, you'll need 12.
Step 3: Making Your Panels.
As I mentioned, my stock is only 66mm wide, but every single dimension in my box is wider than this. Why did I buy the wood then? It was the best I could find, and isn't too hard to make panels up anyway. Let's call it practice, yeah? Anyway, onto the joining:
The stock I'm using is 12mm thick, which is good, because the first slot cutting router bit I could lay my hands on was a 4mm one. So, to edge join these boards into larger panels, first set your router up on a router table. Mine is a homemade one, just a large sheet of MDF with my router strapped to the bottom as in the photo.
First of all, set your slot cutter so that the top edge of the cutter is exactly 4mm above the surface of the table. Run some scraps over the router, doing one face, then flipping to the other side and repeating. Once you have a tongue cut on your scrap, measure it with calipers to make sure that it is, in fact, 4mm thick, and centred. mark this piece of scrap with the measurements and save it as a tool to help you set up faster in the future.
Once the router bit is set correctly to cut the tongue, cut all the tongues you will need. I did this panel by panel, but if you prefer you can do them all at once, or even along the whole length of un-cut stock.
Step 4: Cutting the Grooves.
Once all your tongues are cut, raise the router bit by exactly 4mm. I found that the easiest way to do this was to take my set up block, which was made in the previous step, and lay it on the table against the router bit. Carefully raise the router bit until it lines up perfectly with the tongue on the block.
Run a test piece over the router bit, and make sure the test block and the newly grooved piece of scrap mate properly: you're looking for a flush joint at the shoulders, and as little variance between the two surfaces as possible. If the fit is perfect, mark the scrap as you did in the previous step and save it. If not, keep adjusting until it is perfect.
Cut all the grooves in whatever order you feel appropriate, as before.
You should now have a collection of boards with a tongue on one side and a groove on the other, and they should all fit into each other perfectly.
Step 5: Evil Wooden Panels, Assemble!
The next step is to glue the panels up. I only have enough clamps to do one panel at a time, but if you have more, do them all simultaneously.
The first step is to get your gluing area clean and tidy with enough room to work in. Lay some long clamps out. I use long quick clamps, but you can also use sash clamps, or whatever suits you/you have. Lay your boards tongue to groove along the clamps in the order you want them to be glued.
Then, starting from one end of the row of boards and working toward the other, pick a board up and run a bead of glue into the groove. You may want to put some glue where the shoulders of the groove-half will be, or you may be able to rely on squeeze-out.
Once the glue is on there, put the tongue of he next board up line into the groove, press as tight at you can. You may need to use a mallet. Don't worry if there's a tiny gap, and don't worry too much about squeeze-out at the moment.
Repeat this until all of your boards are glued together.
Now, raise one end of the panel so that it comes between the pads on one of your clamps and close the clamp tight. Repeat on the other end of the board. Wipe any squeeze-out away now.
Place a piece of wood long enough to cover the entire width of the panel (i.e. perpendicular to the joints) under each end. Put a scrap of paper over each one, and a scrap on the top of the panel, directly above the wood that is underneath. Put another scrap of wood at each end of the panel so that it lines up roughly with the scrap below. Then with one clamp at each end, clamp the bits of wood around the panel. You should have one on each side, each with a piece of paper separating it from the panel. Each pair should have a clamp at each end. This clamping procedure is to ensure that the panel comes out straight.
Make sure the long clamps are as tight as possible, and leave overnight to dry.
Step 6: All the Panels
Once you've finished making panels, you should have 11 panels: 3 top/bottom pieces (see step 2) , 4 end pieces, and 4 front/back pieces. The next step is to turn them into boxes.
Step 7: Corner Joints.
I decided to do the corner joints first, because I felt it would be easier to make the top and bottom fit the sides than the other way. If you want to do it the other way around, that's cool too.
I picked finger joints, A.K.A box joints because they're easier to do than dovetails, and there are a lot of joint to do on this box. So, I made a box joint jig for my router table. Instead of telling you how I made it, I'll link you to the guy who designed the one I made. Here .
So, that's basically enough said about finger joints I think. Essentially, follow that guy's instructions and build yourself a fine set of box-jointed corners. Make absolutely certain, however, that your two boxes will end up being exactly the same size (the footprint, that is, height isn't important at the moment).
You should now have a pair of boxes without tops or bottoms, that is, four walls connected by finger joints. DO NOT glue the walls together at this point, and do not sand the ends of the fingers down flush just yet. Now it's time to get measuring for the top and bottom panels.
Step 8: Too Many Bottoms, Not Enough Tops.
The next piece of joinery attaches the lids and bases to the boxes you have made. Measure the thickness of the stock that you're using for both the lid and the wall. In my case, they're the same - 12mm.
The crucial figures are these ones:
A - half of the WALL stock's thickness (6mm)
B - half of the LID stock's thickness (6mm)
C - the WALL thickness (12mm)
D - one third of the LID thickness (4mm)
On each wall piece that will receive a side of a lid/base, rout a groove (A) wide and (D) away from the top edge of the wall. Repeat this on every wall piece, then do a test fit to make sure that all the grooves line up. If they don't, slowly adjust the router and re-rout until they do match up.
The next step is to rout the lid channels. Route a groove (C) deep, (D) away from each edge of the lid (i.e. in the very middle).
Do this to all four edges of each panel that you're mounting. Once that is done, select which side of each panel will be the bottom. Mark this side clearly. To do this, I had to remove the bearing from my piloted slot cutter bit, I used the remaining bearing stub as the pilot instead.
The next step is to remove the BOTTOM edge of each of these grooves. You want to take (A) off the bottom lip the entire way around the panels. This will leave you, in essence, with three differently sized rectangles of wood, one on top of the other. The smallest in the middle, the largest on the top, and the medium sized one on the bottom. The attractive paint image should clarify the route I took to remove this lip.
If none of that made sense, the pictures should help a bit.
Step 9: Don't Sniff the Glue
Now it's time to glue up. Before you go any further, do one last test fit. Put every single piece together - you're looking for a snug fit, not too tight, but not loose either. Once you're happy with the fit, get the clamps and glue back out. I found that the best way to glue up was to glue one corner first, then put glue into the grooves for the lid and fit one lid in. Fit the second lid (if there are two on your box) next. Add another wall piece, then the final wall piece. Now put the clamps on. Make sure you have scrap wood between the clamps and the box, and preferably a piece of paper too. Slowly tighten up the clamps, making sure each of the three dimensions of the box are under roughly equal pressure. Make sure the box is square, and once you're satisfied, go and have a cup of tea.
You can glue both boxes up at once, or just one - I don't mind.
Step 10: Time to Cut Fingers Off.
Once your glue has set, it's time to trim everything up. Take a small back saw and very carefully trim the excess off each finger. Once the bulk of the excess is gone, sand everything flush - do not use a handheld random orbital sander, it will not help you! Use either a stationary belt sander, or a piece of coarse sandpaper wrapped around a scrap block of wood - you want to maintain those beautiful square sides that you have.
Now that your fingers are smoothed over, see if you have any little voids around the joints. If you do, take some of the fine sawdust that you have no doubt been producing, mix some with wood glue, and smear the mix into the voids, pressing hard. While you're at it, you'll notice some rectangular holes at the bottom edge on the long sides, these were caused by the cutting of the groove that keep the lid on. You'll want to cut some small strips out of a piece of scrap and glue them into these holes. Let all the glue dry, and sand smooth. Once the surfaces are all flush and flat, it's time to separate the boxes.
On your tablesaw, you want to saw precisely around the edge of the boxes - this will split your unusable wooden brick into two open wooden trays. The size of each is up to you, but mine were 120mm and 50mm.
I suggest cutting the long sides first, then putting some shims the same thickness as your saw blade in the kerfs, then cutting the short sides. Give the cut surfaces a quick sand, don't worry too much about a perfect finish at this point though.
Step 11: It All Hinges on This Moment
Now is the time to cut all your slots for any fittings and gadgets that you're including, things like hinges, locks, spool/bobbin holders, and inlays. These details are very dependent on the items you have yourself, so I can't tell you how to do these. Mostly it's just hole drilling or chisel work, or a combination of the two.
Don't permanently install any of these fittings, as they'll get in the way later on. If your hinges will allow removal at a later date, install them now. If not, you may want to mock some hinges up with electrical tape.
Step 12: Chords
N.B. Before you begin making your box, do this exercise with pieces of cardboard that correspond to your IDEAL dimensions. Once you have your boxes ready to go, however, repeat the exercise using the EXACT MEASUREMENTS of your real boxes.
The hard part in designing these boxes is getting the opening mechanism right. My first approach was to decide how far I wanted the top tier to travel in relation to the bottom, and then use chord maths to figure the rest out. Unfortunately, I wasn't good enough at maths to make this actually work. If someone knows a formula or something, post it in the comments please.
Instead, I took the tried and true method of trial and error. I cut out some pieces of paper on a 1:1 scale with the side of my boxes, cut some thin strips, and got out the thumbtacks. The trick to this step is to decide where you want the pins on which the arms rotate, and then to figure out the ideal length of those arms. Here's how I did it:
1. Pick a line on which the pins will sit. These two lines (one per box) have to be parallel to each other, and to the edge of the box. I chose to put the lines 30mm from the edge of the box, so they were 60mm apart in total.
2. Pick a starting point on one of the lines. I started at the bottom line, 40mm from the back edge of the box. This point is now called A. Get a pair of dividers and set them to a convenient size, making sure that size is greater than the distance between the two lines. I chose 100mm. Place one leg of the dividers on A and, with the two pieces of cardboard lined up perfectly flush and even, place the other leg of the dividers on the only point that they will reach to ON THE TOP LINE.
3. Now, making sure not to slip, swing the top piece backwards using the dividers to simulate the arm. If the overlap that you see between the front of the top tier and the back of the bottom tier is too small, then reduce t he distance between the divider points. If it is too big, increase the distance.
Keep adjusting the distance between the divider points until you're happy, but make sure that one leg of the dividers is always on the point you first selected. By some freak of luck, 100mm was perfect for this setup.
4. Once you've determined the length of the arm, measure the distance between the divider legs and record it. Also make sure you mark the final point on which the legs of the dividers rested. This point is B.
5. Take 2 strips of cardboard and draw 2 points on each, with the distance you recorded between them. These will be your cardboard arms.
6. Pick a nice number, I used 40mm. Measure this distance along the lines from A and B. mark those points. The points are now C and D, as in the pictures.
7. Put a thumbtack through A,B,C and D from behind. Then put the two arms onto the thumbtacks, one between A and B, the other between C and D.
8. Give it a test-run. Make sure the overlap is still fine, and that the boxes are parallel when completely open. My mock up had a gap of about 2mm at the front edge, which means that the front arm was a touch too long.
You can now transfer these measurements to some scrap to make sure they still work on wood, or if you trust yourself more than I do, you can put them straight onto your final piece.
Step 13: Transfer Your Measurements.
Now that you have all your measurements and a working cardboard model, you need to very carefully transfer all the box-end measurements onto each end of your boxes. make sure you get this right!
The other thing you need to do is make your arms up.
Find some appropriately sized stock and cut it into lengths that correspond to the length of each arm. Allow an extra inch or so for good measure. measure and mark the centre (lengthways) of each arm.
Take your cardboard arms, still with thumb tacks in them. Gently press one thumb tack into the centre line on an arm-piece, towards one end. Carefully line the other thumb tack up with the centre line at the opposite end, making sure that the cardboard is taut. Press it in. Now take both thumb tacks off. You now have the exact measurements transferred! If you have multiple arms of the same length, the best thing to do is clamp them all together, with the marked one on top, and drill holes though them all at the same time on a drill press. Drill a very small hole first, and slowly work up to the right sized hole for the screws you choose to use as the pivots. (You want these screw to have smooth shanks, rather than being threaded all the way to the end.)
Once this hole is drilled, decide how far from the screw you want the rounded ends of the arms to be. Find a scrap piece of wood, and put a screw exactly that distance from its edge. Now remove the screw, put it through and arm, and screw it back onto the scrap. Using a combination of backsaw and file, round the end over by pivoting the arm and using the straight edge of the scrap as a guide. This will result in a round end. Repeat on each arm.
If, like me, you have chosen to make the lid open automatically, you will need an arm with a joint in the middle capable of bending. to do this, you will need to cut some material away. See the picture.
Step 14: The Tipping Point.
It quickly became obvious that the box would tip over when open, unless heavily weighted in the bottom tier. To counter this, I decided to add some legs. This was quite a simple affair.
You'll need two bits of wood, mine were 12mm wide by 6mm thick. They need to be long enough to reach from the bottom edge of the bottom box to the midpoint of the top box.
Once your arms are attached (don't bother with the lid) firmly clamp the top and bottom box together, and to a bench. Get your router out and rout a groove the same size as the bits of wood you prepared earlier. My grooves were 6mm deep by 12mm wide. You will want to use a fence of some sort to guide the router and ensure a straight groove, mine was a piece of wood clamped across the box.
Clean up the rounded edges of the grooves and test fit the pieces of wood. Pre-drill and countersink two holes in each leg, we will screw the legs to the top box.
Now, when they are attached, if the box is closed, the legs will be flush with the surface of the box. When you open the box, the legs will swing backwards along with the top box, which will then rest on them.
Balance!
Step 15: Finishing Touches.
This is an optional, though recommended step. I put a light cedar stain on the box, as meranti is likely to silver over time, followed by two coats of wax. this left the box looking quite nice, and I buffed the wax for a matte finish, which I prefer to glossy, as does the young lady.
Step 16: Put It Together!
If you want to line your box, like I did, I leave that up to you. I glued the paper I chose to light carboard boxes that I made to fit the boxes, then glued the boxes in.
Install any fittings you have, I put in magnetic bobbin holders (x12), brass spool holders (x12), a lock, 2 hinges, and an inlaid brass etching of a cat.
To learn how to etch brass, visit http://frazer-makingstuffup.blogspot.com/
Once everything is assembled, put the arms on!
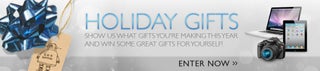
Finalist in the
Holiday Gifts Challenge