Introduction: Building a Small Format Vacuumformer From an Old Toaster Oven
This instructable will guide you to creating your own hobby-level vacuum forming machine using fairly inexpensive tools, readily accessible secondhand appliances, and hardware available at nearly any big box retailer. Thermoforming is a very quick way to get lightweight hollow shapes from thin plastic and the possibilities are near endless once you've got a rig like this in your workshop!
It's worth noting that this isn't intended to be used as a set of strict dimensional plans toward building your own machine. This is meant to be more of a guideline that can be adapted to your particular needs for your machine.
Vacuum forming is the process of heating a sheet of plastic, placing that heated sheet over a form (called a "buck") then removing the air between the hot plastic and the buck to create a hollow copy. Many items can be vacuum formed and many different plastics can be used, but for the purposes of this tutorial I'll be focusing on the machine itself.
Project cost will vary somewhat based on your own specific needs and any alterations made to the following steps, but a machine like this can easily be had for under $200. Build time is approximately two to three days if you're pretty handy around the shop, maybe a week if you're a beginner.
Recommended Skills:
- Basic knowledge of AC electrical systems and home wiring
- Hand and power tool experience
- General DIY problem solving/troubleshooting
At the end I'll also be going over a couple of additional items and accessories that will make the machine a little more robust and capable if you're after something a bit stronger than the shop vac set-up shown here.
Recommended Tools:
- Drill press (laser guides will make your life way easier!)
- Saw; radial arm saw is best for the lumber and a jigsaw will work well for the oven in step 4. A circular, table, hand miter or bandsaw will work as well.
- Wood blade & tile blade for your particular saw(s)
- Power drill & assorted drill bits
- Caulking gun
- Disposable brushes
- PVC pipe cutter
- Generic hand tools, i.e. hammer, pliers, screwdriver, wire cutter, etc.
- Clamps
- Respirator
- Safety goggles
Step 1: Thrift Store Scrounging -or- Sourcing Appliances
There are two main forces at work in a vacuum forming machine: Heat and Vacuum. Heat is needed to make the plastic malleable and vacuum is needed to keep it in shape as it cools.
For heat, you're going to need an old toaster oven. These exist in abundance at various thrift stores and second hand shops for as little as $5. They will be gross (pic 1, ew) but luckily the days of preparing food in such a machine will be over for our purposes.
Most of these appliances are stamped steel or aluminum held together with a myriad of screws. The item to be salvaged here is the heating elements. Look for a machine that has at least four of these installed. (pic 2)
Keep the elements, their mounting hardware and any wiring or ceramic standoffs they may be supplied with. The wire will be helpful as well since it's usually shielded with a high temperature material. If you want specific temperature control feel free to keep the ceramic resistor knob as well. The timer and bake setting knobs can go in the trash.
For a hobby-level vacuum former, a small shop vac is typically more than sufficient. I used the machine in this tutorial for years with an ancient 5hp machine and it worked brilliantly. (pic 3)
All of this heat and vacuum will need a chassis, and luckily I had a turnkey solution available at the time I made my vacformer. On a visit to my parent's house one Thanksgiving, I came home with this small mobile kitchen table. It has caster wheels and a large open base and was perfect for housing this project. A shape like this is fairly simple to achieve from scratch, but as long as you're out and about in thrift stores hunting for a toaster oven keep an eye out for something like this too.
Step 2: Sourcing Materials
Materials for this project will vary slightly depending on several factors. The size of the heating elements mentioned in step 1 will determine the general scale of your project and, in turn, the amount of materials needed to finish your machine. Generally, the following materials will be necessary:
- Wood, in various sizes - I used a combination of 1x6, 1x4, and 1x2 poplar along with 3/8" and 1/4" MDF.
- 16ga grounded home electrical wire, approx 20ft
- Wire nuts, approx 10
- Wood finish, shellac, sealer or paint
- Screws
- 4x bolts w/ nuts & washers. I used 3x3/8" carriage bolts
- Fireplace or High-temp silicone caulk
- Silicone caulk or similar sealant
- PVC fittings, these will vary depending on your shop vac setup
- Wood glue
- Cement board (also called HardieBacker)
- Electrical conduit box & necessary cover
- Electrical switches (15a) and outlet (if desired)
- Foam insulation tape, 1" width
- Non-skid tape
- Binder clips
- 2x stamped metal handles
- Aluminum L-channel stock, 1/8 x 3/4 x 3/4"
- 4x drawer slider assemblies, 18" long minimum.
- 3 prong grounded 20A plug
Step 3: Terminology
There are a few terms I'll be using in the rest of this instructable, and knowing what they are now might make things just a bit easier to understand! Referring to the photo, here are the four main elements of the machine:
- Oven Box: As the name implies, this houses the elements from the toaster oven and generates the heat necessary to give the plastic its desired elasticity.
- Plastic Frame: a mobile piece that transfers the hot plastic from the oven to the forming surface. This is necessary to ensure the plastic keeps its perimeter shape and aligns properly to the surface below every time the machine is used.
- Platen: Essentially a shallow box with holes in it. Air is evacuated through these holes to create a vacuum between the hot plastic and the part being thermoformed.
- Frame Guides: The plastic frame rides up and down along these rails from the oven to the platen.
Step 4: Creating the Oven Box
There are many factors which will influence how large your machine will be, but a few things to consider during the planning process are the following:
- Size of your heating elements - mine were roughly 12" long, and since both sides needed room for their mounting hardware and wire connections, this dictated a 14x14" ID for the oven box (pic 3). The machine was built with this spec as the foundation, and it takes 15x15" sheets of plastic as a result.
- Plastic is typically sold in 6" increments, most sheet plastic comes in increments of 24", and large sheets are almost exclusively sold in 4x8' - if you follow my example here you may end up with some scrap material.
- Different configurations of the heating elements may allow for a larger oven size with the same units, but be wary of hot spots - you want to make sure your machine heats the plastic evenly.
The oven box is a fairly simple piece. I chose to make mine out of 1x6" sheets of poplar with a 1/4" MDF top. I installed some 3x3/8" carriage bolts on the interior of the oven in order to mount it to the chassis using 1x6" boards. Wood screws would probably have been fine, but over-engineering never hurts. (pic 4)
This wooden box needs to be lined in concrete board to insulate it against the heat from the coils. You want all the heat directed downward toward your plastic, not out toward your wooden enclosure. I double-walled the interior with 1/4" HardieBacker board and secured it in place with fireplace caulk. (pic 1 & 2) HardieBacker generates a lot of dust when you cut it, so a respirator is mandatory when doing so. Use a ceramic tile blade to avoid chipping and tearing the material.
Salvage as much of the mounting hardware from the toaster oven as possible. In pic 3 you can see the ceramic mounting posts, wire, and metal brackets which hold mine in place. Route the wires for the elements out of the top of your oven box and fill the through holes with more fireplace caulk.
I went with a simple approach when mounting the oven to the chassis - L-brackets screwed directly into the 1x6 boards (pic 5). Once everything was installed I painted the wood with shellac to seal it.
Step 5: Add a Frame to Hold Your Plastic
With the oven box created, you can work backward to determine the size of your plastic frame. The previous step noted that my oven box was a 14x14" ID, and after adding the HardieBacker concrete board and wood for the oven enclosure, this became 15.5x15.5" OD. Your plastic frame should match the outer dimension of the oven in order to ensure the plastic is properly heated. Any smaller and you risk heating the frame itself, any larger and it won't properly heat the edges of the plastic.
The frame is built from 3/4x1.5" poplar boards, held together at the corners with steel L-brackets. You'll need to build two of these frames to identical dimensions. (pic 2)
The idea here is to hold the plastic rigidly in place while it is being heated, and continue to hold it once it is stretched over the buck later on. It then needs to be able to be removed from the frame so a new sheet can be loaded and the process repeated.
After assembling both frames, apply non-skid tape to the interior facing edges. This will help grip the plastic in place. (pic 3)
To hold the two frames together, I used small pieces of aluminum L-channel screwed into the upper and lower frame. These are pinched together with a binder clip to hold the plastic in place. A pair of handles on either side of the upper frame makes moving this up and down on the machine much easier. (pic 5)
Step 6: Frame Guides
Frame guides are an integral part to a machine like this. They ensure the plastic frame moves smoothly and accurately from the heating oven above to the platen below. It is possible to have a vacuum former without this element, but aligning the plastic frame to the platen by hand takes time and that gives the plastic a chance to cool off and harden.
For my budget build I chose to use four drawer sliders. These were 20" models purchased at a big box home improvement store. These can be had in numerous lengths, but keep in mind the height of the bucks you'll use for forming, and also any length you'll lose from the additional height of things like the platen, oven, and frame. I recommend anything between an 18" and a 24" rail.
The rails are situated so that the part which would normally mount to the back of a cabinet (the gold part in pic 2) serves as the base, while the piece that would mount to the front is now mounted to a set of stand off blocks on the side of the oven box (pic 3).
Four sliders with small nylon wheels were included in the drawer rail kit, and these were attached to the top of the plastic frame. This is because adding this piece to the bottom frame will lift it off the platen and in between the frames would interfere with the frame holding the plastic in place.
The plastic frame was put in place, then the sliders were inserted into their rails and lowered onto the top of the frame before screwing them into place (pic 4). Once these are attached the upper plastic frame cannot be removed from the machine without unscrewing the sliders again.
This set up worked well for heating thin plastic, with the friction of the sliders against the rail enough to keep the plastic frame in place next to the oven. Thicker plastic proved somewhat heavier, and eventually I added a set of springs and S-hooks, mounted to the oven box, which hold the plastic frame in place during the heating process (pic 5).
Step 7: Building the Platen
The platen is a thin hollow box which distributes vacuum across a wide surface area. It needs to be built robust in order to withstand the vacuum that will be applied to it. I chose to build mine out of MDF.
The platen itself is a sandwich of three elements:
- The base, a 3/8" thick MDF board with a hole in the center.
- The cavity frame, a 1/2" wide square of MDF which makes up the inner cavity
- The top, another 3/8" thick piece of MDF with a few hundred holes drilled into it.
All three components should have the same perimeter dimensions.
First, you'll need to determine what your eventual source of vacuum will be. A trip to the local big box home improvement store should provide you with a selection of pipe fittings that can be coupled to your vacuum hose (pic 3). I chose a large threaded PVC fitting so I could change out the vacuum source later on if desired. Cut a hole in the center of your base and glue your desired pipe fitting in place with an airtight adhesive. (pic 2)
After this, trim out your cavity frame from 1/4" MDF. This should be about 1/2" wide and look like a thin picture frame when placed on top of the base. Glue it in place with wood glue and allow it to cure. (pic 4, shown with plastic frame. pic 5 shows a larger frame I made for another vac former)
The top will take a while. A grid needs to be created across the surface, taking into account where the cavity frame will block off the open area inside the platen. For my machine I drilled 1/16" holes on a 1cm grid. In retrospect this could probably have been expanded to a 2cm grid with no loss in fidelity. Drilling the holes is much easier with a laser guided drill press! (pic 6 & 7)
Don't glue the top to the platen base & frame before drilling these holes. MDF has a tendency to chip out and you should turn the top over after drilling to clean up any holes which may be blocked.
Once complete, glue the top to the assembled base and frame with wood glue and allow to cure overnight. (pic 8)
I found it's also beneficial to have a strip of foam weatherstrip tape around the base of the platen where the frame will land. This helps make a seal between the bade and the frame, ensuring that the vacuum will pull air out from around the mold, not from outside.
Step 8: Wiring Configuration
With the construction complete, it's time to wire up the heating elements. These are no different than any other powered electrical component, and supplying one side with live current and the other with neutral will result in heat. If anything in this section is vague or confusing, please consult other instructables to learn about AC wiring before proceeding.
Depending on the resistance of your specific element you may choose to wire it up in a variety of configurations. Series, Parallel, or a combination of both. The last, series/parallel (pic 2), is how my machine is configured. Running all 4 heating elements in parallel provided a lot of heat, but the combined amperage draw was too high and ended up tripping a circuit breaker on testing.
On the other hand, a fully series-wired circuit proved too cold as the provided 110V wasn't high enough to fully heat up the coils inside the elements.
I'm providing the graphics above as an explanation of possible configurations, as I only know what worked best for my personal junked toaster oven. It's quite likely that other makes and models will need other wiring to suit them.
Keep in mind: parallel circuits operate with additive amperage draw and series circuits operate with additive voltage requirements. Test this safely or clone the wiring set up in your toaster oven before junking it.
Your oven should be wired to a 20A switch housed in an electrical box, easy to reach during operation. I also added a 15A socket to this area for my shop vac and a heat gun in case some areas of the plastic required more heating during the process (pic 5). Don't laugh at the switch plate, I was penny-pinching.
Step 9: Fitting a Dedicated Vacuum Pump
After a while with this machine, I decided an upgrade to the vacuum system was in order. A shop vac will only be able to provide about 5inHg of vacuum, while a dedicated pump/tank set up will be able to pull 25inHg or more. This results in more detailed pulls on your machine, since the suction of the plastic against your form becomes much stronger.
The information below is intended to replace the shop vac as a source of vacuum in the system. Generally this is more reliable and stronger, but not 100% necessary for hobby applications.
The basic operation goes like this: With the air valve shut, the pump is turned on and air is evacuated from the tank. A gauge is hooked up to this vacuum circuit which displays how much vacuum the tank is currently holding. When the desired amount is reached, the pump is shut off, the plastic frame is lowered onto the buck, and the air valve is open. This lets air into the tank through the holes in the platen, pulling the plastic down around the buck. Cool! Pic 1 shows a diagram of the plumbing for clarity.
A mod like this will run an additional $200-$250 on top of the rest of the project, but it does make for a stronger and more capable machine.
Materials/supplies needed:
- Vacuum pump (pic 3)
- Air tank (pic 3)
- Vacuum gauge
- Ball valve
- 2x U-bolts for mounting ball valve to machine
- 2x 90º fittings for ball valve
- Barbed hose fittings; 2x for valve, 1x for pump, 1x for gauge, 2x for tank
- Large ID (3/4" to 1") vacuum hose; connection from tank to valve and valve to platen
- Medium ID (3/8") vacuum hose; connection from pump to tank and T-connection from this line to vacuum gauge
- Additional switch to activate air pump (pic 5) I chose switches with status indicator lights so I'd know when the heater was on.
- One-way valve for medium ID hose
Fittings such as the valve and barbed adapters can be picked up at big box home improvement stores. The specifics of which ones to buy will depend on the threading on your air tank, pump, platen and gauge. It's a bit of a jigsaw puzzle and you can expect to pay somewhere around $70-85 just for the adapters and hoses.
If you decided to add the threaded fitting to your platen when building it, this upgrade becomes much easier.
Step 10: How to Use Your New Vacformer
The video here is me working on my larger machine which I built a couple of years ago to make larger parts. In practice though, the process of making vacformed pulls is nearly identical. You can follow along in the video, but here's the break down:
- Pre-heat your oven for 3-5 minutes to allow the entire space to reach operating temperature.
- Load your plastic into the carrier frame and secure in place with binder clips
- Raise the plastic frame to the heater oven
- (Pump & vacuum tank set up only) Turn on your air pump and evacuate the tank to 25inHg.
- Place your item to be vacuum formed (called a "buck") onto the platen
- Watch the plastic - it will begin to deform and wrinkle at first. This will be followed by the wrinkles evening out slightly, then the plastic will begin to droop in the center (pic 1). Different materials and bucks will require different levels of sagging of the plastic, and practice will teach you how much is appropriate.
- When the plastic has the right amount of sag, turn the oven off and lower the frame down to the buck & platen
- (Pump & vacuum tank set up only) Open the air valve on the tank and evacuate he vacuum through the platen
- (Shop-vac set up only) Turn on your shop vac and allow it to run while the plastic cools around the form
- Once the plastic is cooled, remove the binder clips from the frame and remove your buck from the plastic shell.
Step 11: Making Vac Form Bucks
A variety of materials can be used to make the bucks needed for vacuum forming, provided they can withstand heat and vacuum. Wood, tooling foam, resins and some dense plastics all work great. Try to avoid low-density foams and materials that can shatter like hollow polycarbonate and glass.
Vacuum forming bucks need to be flat on their base in order to lay on the platen, and the general shape should not have any inward-facing edges. Edges like these are called "undercuts." The rigid plastic shell formed over these undercuts will lock the buck into the form. Think of trying to remove frozen water from a plastic bottle and you'll start to understand the basic idea of undercuts.
In pic 1, there are three bucks shown. Buck #1 is okay - straight perpendicular edges aren't terrible but they can produce an issue called "webbing" if they're too tall. Buck #2 is ideal; the tapered edges will allow the piece to easily be removed from the rigid plastic once it cools. Buck #3 won't work at all. Once this part is vacformed the only way to remove it will be to cut the plastic off.
These are general rules for making the buck shape however, and sometimes they can be ignored to suit your needs.
The hand sculpt in pic 2 was cut out on a bandsaw so each small plate would have a flat edge. While these do have very small undercuts on each part around the edge of the plate, they are able to be removed from the plastic sheet with a small bit of force.
Pics 3, 4, and 5 show how a complicated shape can be made by cutting it along a central line. This staggered set of polygons was shaped first in urethane tooling foam, cut in half, then formed in .060" styrene plastic. After the parts were trimmed, the two halves are glued back together to make the piece whole.
Step 12: Tips and Tricks for Vacuum Forming
I've pulled a lot of plastic through my forming machines over the time I've had them, and there's a few things you should keep in mind when you're looking to create vacformed parts and the bucks that go with them. Here's a few bits to help you along the way.
Pic 1 & 2: Adding a metal frame or mesh to the space under your part will allow the vacuum to continue to pull the plastic into place after the plastic frame is lowered. Sometimes the holes in the platen can become blocked by hot plastic and this will prevent all the air around the buck from being completely evacuated. A screen, mesh, or frame like the one pictured here will keep that from happening.
Pic 3: Small risers, typically made from scrap MDF, will help in capturing the detail at the bottom of your parts. Plastic tends to wrap around the piece and create a soft edge where the buck meets the platen. Small risers like the ones shown here mean that soft edge is scrap and the raised portion is formed accurately.
Pic 4 shows a common mishap: webbing. This occurs when the plastic is pulled down around the buck in a non-uniform way. Many issues can cause this, ranging from tall vertical walls of your buck, parts being too close together, and plastic being too hot. Experimenting with these factors can keep webbing to a minimum, though it's something I still deal with from time to time.
Very tall bucks will require more droop on your plastic. The bird masks in pic 5 needed a lot more than the hand pieces in pic 4. Too much droop on shorter bucks can cause webbing though, so watch out.
Step 13: Materials to Vacuum Form
For the purposes of this machine, the materials that will prove most useful are:
- Styrene (pic 1) - generally white, fairly cheap, comes in abundance of sizes. Less durable than ABS but less expensive too
- ABS (pic 2) - generally black, pricier than styrene but far more durable. Typically sold in thicker sheets. Requires more heat and vacuum to pull decent copies than styrene
- PETG (pic 3) - clear and can be tinted with polyester dyes. Far more temperamental and susceptible to fogging and static issues while forming than ABS or Styrene. Pricier as well. Finding material thinner than .080" may require a specialty distributor. This is what soda bottles are made out of.
I've used all three materials on this machine, and with practice I've had great results. If you only need a few sheets McMaster-Carr is a decent resource, though they can be somewhat expensive. I buy my materials in 4x8' sheets at a local plastic supplier called Calsak. A little google-fu will probably yield a similar supplier locally.
By contrast, an entire sheet of 4x8' .080" ABS at Calsak is around $25. Through McMaster a similar amount of money will only buy one or two 24x24" panels.
Step 14: Start Pulling Plastic!
This machine has pulled many materials, but my go-to is styrene. I've used up to .12" styrene, but I've also run .060 ABS and .080 PETG as well. Every image in this gallery was something created with this vacuum forming machine!
Enjoy your new ability to create hollow lightweight parts, and thanks for reading!
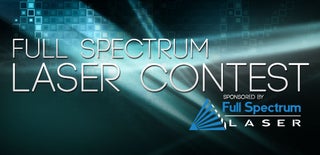
Third Prize in the
Full Spectrum Laser Contest