Introduction: CNC Laser Cutter Journey
I want to share with you the journey had had , creating my very own CNC laser cutter.
This projects is about 2 years in the making, due to research and development, and spending allot of time on www.instructables.com it took me a bit longer than anticipated , but I finally decided to start building my very own CNC laser cutter in the middle of 2014.
Motivation behind this was that I fly and build model airplanes , and wanted an easier more precise method of manufacturing parts for these planes etc.
Step 1: The Prototype - Version 1.0
To save on money and material I decided to build a wooden version of my CNC machine to see what I would have to invest to get it working.
I ordered some some parts from iTead Studio to get the ball rolling.
1. 3 x stepper motors - https://www.itead.cc/catalogsearch/result/?cat=&q=42BYGH3404
2. 3 x stepper motor driver (Big Easy Driver) - https://www.itead.cc/big-easy-driver.html
Due to some stock shortages, I got the rest from www.sainsmart.com
1. 1 x UNO R3 Arduino board - http://www.sainsmart.com/arduino/control-boards/sainsmart-uno-r3-atmega328-au-development-board-compatible-with-arduino-uno-r3.html
The rest of the electronics, I had laying around at home e.g.
1. 1 x PC 300W power supply
2. Enough cables to connect everything
3. An old CD-Rom drive (harvested the parts for the z-axis)
The wood and other hardware I got from my local hardware store
1. Pressed wood cut to size
2. Enough screws to keep it together
3. Kitchen drawer rails ( 2 x for the X-axis, and 1 for the Y-axis)
To control the machine, I loaded GRBL 0.8 on the UNO , and used GRBL Controller to send the g-code to the UNO board running GRBL.
To generate the G-Code I did my designs in InkScape and used a g-code plug-in I found online.
I put everything together and I was amazed, I got it working. (see video of my first g-code processed , the machine writing my name)
Step 2: The Birth of Xarius CNC Machine
My wife and I have twins, Xander and Darius, and going on to the next steps of this project, I had to give my invention a name, so I combined their names and called it "Xarius CNC"
I downloaded Google SketchUp and started with a design to make a better more robust version as version 1 was only good enough to play around with a pen and make fancy drawings for the kids.
With the completed plan in hand I went to one of our local engineering companies and got a copy of this plan cut out of 5mm mild steel. This was basically for the base (x axis) , and the top half was cut out of 4mm aluminum ( y and z axis to save weight on the moving parts)
The parts arrived a few days later, powder coated , and looking good.
The whole design was based on using linear bearings from a local 3D Printing store and when it arrived it fitted perfectly, and could continue with the assembly. I used 10mm BMS rods from a local steel merchant which was straight as an arrow, and created a very smooth linear movement on the x,y and z axis.
Step 3: Completed : Mechanically Assembled, Adding a Spindle
The assembly went well, took my a couple of hours, as I only had a few hours spare each week, but in the end it was all worth it.
The design catered for more than one application when it came to cutting material, I could add a spindle to cut wood, plastic etc. Or I could add a Laser to make things interesting.
Due to a tight budget I started of by adding an existing "dremel" tool, which worked OK, but I was not a fan of all the dust.
Step 4: Laser Time , Turning Up the Heat..
Being fascinated by lasers for some time I decided to search for a laser to add to my CNC machine.
I had a project I want to get off the ground , building my first balsa airplane model, and needed to cut wood perfectly without all the dust, as the CNC machine now moved inside the house :)
I stumbled across a Laser module at www.banggood.com - 450-500mW Violet Laser Module With Holder For Mini Engraving Machine , and I ordered it as the price was not too extreme.
After a bit of a wait, I finally received it in the mail and modified my wiring layout to allow me to control my laser with my G-code using the M3 and M5 commands.
The other challenge I had was that the g-code generator for InkScape could not generate G-code for my Laser with the M5 and M3 commands, but a website called http://www.qcgeek.com/laseroko/ came to the rescue as the allow you to upload your G-code and all Z axis commands are replaced with the correct M3 or M5 commands (M3 turning the laser on , and M5 turning it off again) - thanks to http://www.qcgeek.com/laseroko/ !
So I did my first "cut" with the www.banggood.com laser, and I was a bit disappointed , in hindsight I should have actually purchased a stronger laser, but at the time they only had 500mW available, but it was good enough to cut vinyl sticker, so I could decorate my planes, and I could burn the plans of my balsa plane on my wood, and just cut it by hand.
Step 5: Time to UPGRADE
So, I needed a bit more power, and found what I was looking for , the guys at http://jtechphotonics.com could help me out, their 2.8W Laser upgrade kit had ore than enough power at a price that would not break the bank.
The laser kit details can be found here : 2.8W Laser and Driver Kit, International
Delivery was quick and prompt and I installed it as soon as I could.
I now had to make a few chnages to my CNC machine as a few elements have changed.
1. New TTL power supply using PWM for the laser output
The new laser came with a pretty fancy power supply, with TTL (allowing me to control the laser power with G-Code M3 S200 for example - M3 switching the laser on at a strength of 200), so I had to upgrade my GRBL on the UNO board, and I loaded GRBL version 0.9j which supported PWM on Pin 11.
2. Wiring had to be updated to accommodate the new power supply and Laser Diode on the Z-axis.
I then also installed a new G-code generator from JTech Photonics which allowed me to generate more laser friendly g-code, allowing me to specify the number of passes, adjusting the Z-axis after each pass, laser PWM signal strength etc.
The GRBL Controller software I used was also a bit out of date, and I upgraded to 3DP Burner Sender which is awesome.
Step 6: Cutting and Engraving - at Last!
So, with everything installed, upgraded, calibrated I had to celebrate by cutting one of my long time favorites, a simple firewall from www.flitetest.com which they provided the the plans for. Going to put this on my next Delta wing for sure.
The guys at 3dpBurner also had a very nice Image to G-code converter which allows you to engrave with a laser, works great. Video also shows you the engraving on my CNC machine (I am a HobbyKing fan as well). The kids also wanted their share, and being Jurassic Park fans, I could not resist to engrave the logo in the photo :)
Now after it all, I must say that I am very happy and pleased with the outcome, now the only thing is to start on those projects I originally wanted to do , and with the laser cutter / engraver it is only a matter of getting into it and enjoying the results.
Thanks for allowing me to share this project with you. Next project , maybe a 3d Printer :)
Step 7: It Is Better to Give Than to Receive - the Plans :)
For all of you waiting so long, I have consolidated the plans, and here it is :)
The four panels on the left is cut from 5mm mild steel, and the rest from 4mm aluminum.
The whole machine is held together by m3 screws and bolts.
The Stepper motor holes is for a NEMA 17 motor setup
Currently my machine also works with GT2 timing belts and pulleys, and holes to attach the timing belts to the machine is not on the plans, and left to your own discretion.
Send me your build photos , would love to see how your efforts turn out, and enjoy.
Attachments
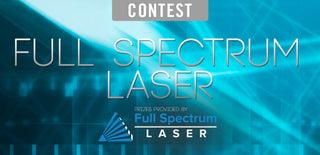
Participated in the
Full Spectrum Laser Contest 2016