Introduction: Captain America Shield From Used Satellite Dish
I had been wanting to make a Captain America shield for some time, but had a hard time finding a suitable item to make it from. I originally tried using an old plastic sled, but it gave me all sorts of grief. The type of plastic would not take paint very well (not even Krylon Fusion for plastics), or any type of adhesive that I tried.
I eventually came across a used satellite dish, and with a little bit of modifying this turned out to the be best option for a Captain America shield.
If you are interested in making one of these, you may have to do a bit of searching and asking to find a used satellite dish. I've seen them show up at thrift stores from time to time. Keep your eyes open, and you should be able to find one.
If you don't have access to an old satellite dish I would recommend using a round metal sled.
I have a separate instructable on how to make a flyable version out of cardboard and duct tape, which you can check out here: Flying Captain America Shield.
Thanks for looking!
Step 1: Disassemble the Dish
I began this project by disassembling the dish and components. Some of the nuts and bolts were kept and used later on to attach the handles.
Step 2: Draw Circle
The satellite dish was an oval shape, and Captain America's shield is a round concave disk.
I was worried that a circle cut from the oval-shaped dish would look warped. But once it was cut out, the circle looked perfectly fine.
I eyeballed where the center of the dish was and put down three or four pieces of masking tape, which provided a place for the needle of my homemade compass to bite. I then drew as large a circle as would fit within the back lip of the dish.
Step 3: Cut Out Circle Shape From Dish
I initially tried using a metal cutting Dremel attachment to cut out the circle from the dish, but it was too tedious. I found that my metal snips worked much better for this task.
After cuts were made all the way around the lip, I used a dead blow hammer to pound the tabs all flat. Then I used my sips to cut out the circle.
I used a Dremel grinding bit to take off the sharp, jagged edges around the disk that were left from cutting it out with the snips.
Step 4: Fill Bolt Holes
There were four sunken areas in the dish for the bolts that needed to be filled somehow, and then ground off.
I used a Dremel grinding bit to remove the finish from the dish and roughen up the area around the bolt holes. I then used JB Weld to fill up the spots where the bolts had been. Masking tape was used to cover the backside of the holes while the JB Weld cured.
Step 5: Grind Off Bolt Hole Nubs
The bolt hole nubs that were now filled with cured JB Weld were cut off with a metal cut-off attachment.
These areas were then sanded with 80 grit sandpaper.
I also removed the tape at the center of the shield and used a nail punch to mark the center of the shield. This was needed to help lay out the concentric circle design later.
Step 6: Smooth Out Bolt Area With Body Filler
Bondo body filler was used to fill in and smooth out the areas where the bolt holes had been. This was actually my first time using bondo. My dad used it for everything, so the distinct smell brought back all sorts of memories of stuff my dad had either made for fixed with it.
After the bondo cured, it was sanded smooth with 100 grit sandpaper.
Step 7: Attach Bolts for Handles
Epoxy was used to attach four bolts to the backside of the shield. The handles were later attached to these bolts, which were left over from when I took apart the dish.
Prior to the epoxying of the bolts, the surface of the dish was roughened up with a Dremel grinding bit.
Step 8: Prime Shield
With the bolt holes filled and smoothed over, the shield was ready to be primed.
It received three coats of primer, and was sanded with 220 grit sandpaper between each coat, along with a final sanding after the last.
The backside of the shield received a coating of flat black paint at this point.
Step 9: Paint First Coat
The shield received three coats of white, as the base. All the painting was done with spray paint. I avoid hand painting if at all possible, although this could have been painted by hand with the same amount of trouble.
I deliberated for some time as to the best way to paint this. I will admit, this was one of the most difficult things I've ever tried to paint. It involved a lot of masking, and a very specific step by step process.
Step 10: Add Red Stripes
When the base coat was dry (about 45 minutes), I masked over almost the entire surface of the shield, and drew out the design.
An exacto blade was used to cut away the tape in the areas needed to create the red stripes. Prior to painting the red, a couple of heavy coats of white were put down to seal up the tape edges and prevent "bleeding."
Step 11: Add Star
All the tape was removed from the previous step, and when the red paint was dry the inner white circle was remasked.
A star shape was drawn on the tape using a stencil. An exacto blade was used to cut away the needed areas, and the rest of the shield was masked off. The inner circle was then painted blue.
Painting this blue circle was especially tricky because the method used to seal up the tape in order to create clean lines and avoid bleeding only works if the tape is masking between two colors. Here, there were three colors I had to deal with all at the same time.
Before painting the blue coat, I very carefully spayed the edges of the taped star white, and the edge of the circle red. This sealed up the white star and the red circle from blue bleed-through. This worked very well and prevented any ugly bleeding.
Step 12: Make Handles Using Old Belt
An old belt was used to make the handles for the back of the shield. Holes were drilled through the ends of two pieces of the belt, and these were attached to the bolts that were epoxied to the back of the shield.
Step 13: Touch Up Blemishes, Add Clear Coat
I had to touch up a handful of small blemishes and imperfections with a small paint brush, primarily where I wasn't careful while removing the masking tape and smudged a few spots. (I prefer to remove masking while the paint is wet. I think it makes for cleaner lines, but you run the risk of getting into a lot of trouble if you're not really careful as you take it off.)
Once everything was dry I lightly sanded the entire thing with 400 grit sandpaper, which gave it a cool weathered, battle-scarred look.
It was finished and sealed with three coats of crystal clear acrylic spray. It turned out very nice.
Thanks for looking. Let me know what you think!

Finalist in the
What Can You Do with a Dremel Tool?

Finalist in the
Joby Transform It! Challenge

Participated in the
Epilog Challenge
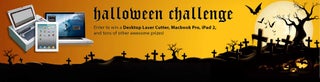
Participated in the
Halloween Props Challenge