Introduction: Cardboard Radio Controlled Dalek
Here I will show you how I made my scratch built Dalek using items I rescued from our recycling bin, a broken but functional radio controlled tank, and other bits and peaces I had laying around crying out to be used. I hope this Instructable will give you some inspiration to make your own Dalek, as I think we need more of these poor misunderstood creatures roaming around our own little planet (even though they are hell bent on controlling the universe).
Here is a list of materials I used.
A radio controlled tank, broken but still functional
Corrugated cardboard
Sheets of scrap A4 size paper
Thin Cardboard (from a cereal box or similar)
PVC carpet underlay foam sheet, 12mm thick
A plastic lid from a gravy jar
3 flat top plastic lids from deodorant cans
1 rounded plastic lid from a shaving foam can
4 dried out thick marker pens
Some length of thin steel wire
Electrical wire
2 red LED bulbs
1 green LED bulb
2 round ended plastic tubes
1 Christmas tree ball ball decoration
A WiFi web cam
A Bluetooth speaker
Bag of small modeling tacks (tiny nails)
1 kiddy size football
7 8cm long screws
A 9 volt battery snap connector
A strip of 10 Blue battery powered LED's
Items I had to buy.
Bag of 50 polystyrene balls, 3cm diameter (about £3 / $5 inc shipping)
1 can of grey spray primer 500ml (about £4 / $6.50 i/s)
1 can of gloss black spray paint 500ml (£6 / $9.80 i/s)
1 can of gold spray paint 500ml (£6 / $9.80 i/s)
Tools and adhesives.
Phillips screwdriver
Set of small electrical use screwdrivers
Drill
Craft knife with new blades
Scissors
Wire cutters
Soldering iron
Insulating/electrical tape
Aluminum tape
Duct tape
Super glue
1 tube of Grab adhesive and applicator (No more nails/ Gripfill or similar)
Black permanent marker
Pen or pencil
Ruler
Very fine sanding paper
So on with the build. Lets begin with the base.
Step 1: The Base.
I feel I should mention without trying to put a downer on things, a Dalek really is not the easiest of things to make. But with a bit of research, trial and error, perseverance, and a little luck, it is worth it. The good thing is, if I did go wrong on something (which I did a couple of times) it was no real bother, as most of the materials I was using were destined for the rubbish/recycle collection anyway, and there was always something else I could end up using.
The radio controlled tank I had collecting dust, was old and damaged, which was mostly bodywork and a missing wheel, but after replacing the rechargeable batteries and testing it functions, it burst in to life. So now I had a working chassis, forward, reverse, left and right, and a motorized turret which turns about 270 degrees. The motorized cannon which went up and down was also broken, but the motor did still work which I was really pleased about because I had a great use for it. More on that later.
The tank chassis measured 35cm by 15cm and 5cm deep from top of chassis to the ground. To make the base, What I did first was to take apart the body from the chassis and remove the cannon motor, battery leads, and aerial wire. I then cut and extended the wires, then pushed them through a small hole I made in the top, slightly off center, of the turret. I then started to make the base. Here's how it was done.
1.) Using a sheet of A4 paper as a template, measure and mark out the 11 sides that will help form the Dalek body shape. Using the paper template helped me a lot, as getting the right shape was a bit of trial and error. Measurements I used are as follows starting from what would be the back of the Dalek and finishing with the pointed front. It should be noted that these measurements are what I worked out using photos I found online as finding exact specifications that I could scale down, at the time, proved to be difficult, so I used my best judgment.
Back, 12cm
Back sides, 6cm
Main sides, 10cm
Off center sides, 5cm
Front sides, 8cm
Fronts, 6cm
To help make it clearer, the measurements can also be seen on the in-photo information. When the sides are marked out and your happy that both left and right sides look equal,, cut out the template.
2.) Using a peace of strong corrugated cardboard the same size or larger than an A4 paper sheet, place the paper template on to the cardboard and use a pen to draw around it. Then cut around the marked edges of the cardboard using a craft knife and ruler (or a peace of straight wood) to help keep the edges nice and straight.
3.) This part is a bit of trial and error. I needed to cut out a circle of the center of the now shaped cardboard to fit over the turret of the tank, and leave enough room for the turret to move freely with no obstruction, as the gap between the chassis and turret was not completely flat. So cut small to start then cutting more where needed to avoid cutting out to much cardboard and making it weaker. As seen in the photo, I did not cut out a circle but rather cut to shape of the protruding body parts of the tank and helping make the base level.
4.) Using some more corrugated cardboard, cut out some 2cm wide strips, cut the strips in to 4cm peaces (about 22 peaces should do), then bend them in half to make "L" shape brackets. Now glue 2 brackets to each edge of the base with the hanging part facing towards the outside of the base and as flush as possible.
5.) Now using a thinner peace of cardboard like a cereal box (or pizza box like I did), you want to cut out some strips that will cover the sides to hide the wheels and to attach some under chassis lighting if you wish. The measurements I used were 3 an a half centimeters deep leaving 1.5cm ground clearance, and enough cardboard to go all the way around the base plate made previously.
6.) Using some glue (I used super glue) apply some drops on to the outside of your "L" brackets then attach the cardboard strips. I held the strips in place using some cloths pegs until the glue set.
7.) Attach the base to the tank chassis using either glue or some screws and washers (I used glue).
8.) Finally in this stage, I had a strip of 10 battery operated blue LED's left over from an old project.(cheap to buy, around £3 / $5). Using some duct tape, simply attach the lights to the inner side of the sides of the base, making sure the battery pack is at the back of the base so you can gain easy access through an inspection panel to be build in to the body later.
On to the next stage.
Step 2: Body Frame and Head Mechanism.
What was need to be done now was to create some kind of support frame to take the weight of the body, chest, head and mechanisms. I had to keep the overall weight of the Darlek build down, simply because the tank was kinda old and after some testing, found out that it couldn't take too much weight, as it would not turn properly and the cogs connected to the drive motors would start to slip and make a nasty grinding noise. Not cool. I will give steps on how I made this frame, but there is probably a better, neater way of doing so.
1.) Using a thin plastic lid (I used one from a gravy container), make 2 small holes, 1 small pilot hole for a screw, and a second larger hole to feed the wires coming through the top of the turret.
2.) Using a stubby size screw, screw the lid on to the center of the turret. I would also advise using some glue to stick the lid down aswell, to help add some reinforcement so the lid does not eventually spin on the turret after a period of wear and tear.
3.) With some corrugated cardboard, cut out a long length of about 60cm's which is a bit too long but can be easily cut to size later, then roll into a long tube (enough to put your finger inside), glue together, and wrap in duct tape. Then on one end of the tube, cut down 4 equal lengths about 5cm's and fold out. Glue the 4 tabs on to the plastic lid. I used a small amount of all purpose grab adhesive for this, as you can use your finger to rub it all around to make sure all the tabs are well covered. I will be using this grab adhesive for quite a lot of this project. Its great stuff, easy to work with, drys relatively quick, but not so quick that you cannot work with it. You might also know it as No More Nails or something similar.
Truth be told, when I made this tube axle, I only made it about half the length mentioned, as can be seen in the photos. This was because my original plan was to make the chest/weapons section rotate interdependently to the lower body and head like the Daleks in the 21st century episodes, but I had a change of heart. After watching "Asylum of the Daleks" I had a thought. As I only had 2 motor's to use, one to rotate the chest and one to rotate the head, "I want the eye stalk to go up and down". So that's what I was going to do. Because of this, I now had to extend the length of the tube to reach the base of the head and now have a fixed chest like the older Daleks from the 20th century episodes.
4.) Similar to the previous step, cut out 5 more lengths of corrugated cardboard around 30cm's, then using a ruler of short length of wood, make 5 folds down the length of the cardboard, then glue together to form a square rod. What I did next was to wrap the finished rods in a couple of lengths of duct tape for some added reinforcement.
5.) Using a pen, mark 5cm lengths on each side, top and bottom on each rod then, using a craft knife or some scissors, carefully cut down these marks to form 8 flaps, or tabs (4 top, 4 bottom), then put to one side for the moment.
6.) Grab yourself another peace of corrugated cardboard. You will now want to make similar to what you did for the base plate, only smaller, with different measurements to almost form a hexagon type shape and cutting a hole in the middle for the center tube axle to fit through. Here are the measurements I ended up using.
Back, 5cm
Back sides, 5cm
Main sides, 7cm
Off center sides, 4cm
Front sides, 4cm
Fronts, 4cm
As with the base plate, you could use some paper to make a template, copy it over to the cardboard then cut out using a straight edge to guide for a nice clean cut.
7.) Now this will require a little trial and error, but can be done before any adhesive is used. Using 2 of the struts, position and then fix to the base on the rear 2 corners. Make sure with all the support struts, the turret has enough clearance to fully rotate without obstruction. When the glue has set, position the top plate you cut out and glue to the top tabs of the support struts.
8.) Continue to fix the rest of the struts starting with front middle one. Now the trial and error bit comes in here. You want the top plate to be as level as possible, so here you can alter the size of the strut using and taping up the tabs which will also help to center the top plate and keep the tube axle straight when it rotates. Finish off fitting the last 2 struts and when the glue is dry, simply use a pair of scissors to trim off any excess cardboard from the strut tabs so everything is flush with the top plate.
Next, the lower body skirts.
Step 3: Lower Body Skirts
Time to cover up that unsightly cardboard frame and give it some body. The body skirts are made from thin cardboard, such as cereal boxes or something similar.
1.) As you are now aware from making the base plates, you will need to cut 11 skirt panels in total. After flattening out your peaces of cardboard, with a pen and ruler, mark out the separate skirt panels. These are the measurements I used.
1 rear panel, top 4cm, bottom 12cm, both sides 19cm
2 rear side panels, top 4cm, bottom 6cm, one side 19cm, other side 20cm (the different size on the two sides of the panel make the angled shape)
2 side panels, top 6cm, bottom 10cm, one side 18cm, other side 19cm
2 off center side panels, top 3cm, bottom 5cm, both sides 18cm
2 front side panels, top 3cm, bottom 8cm, one side 19cm, other side 18cm
2 front panels, top 3cm, bottom 6cm, one side 19cm, other side 18cm
Just to reiterate, these are not proper spec sizes, but what I came up with and used, which seemed to work quite well in the end.
2.) Starting from the front, and making sure you have the longest side of the front skirt panel facing forward, bend the top of the panel to make a 1cm tab and marry it up to the top and bottom base plates. Make a slight bend on the bottom of the panels so the fit flat to the side of the base covering the wheels. when your happy they fit right, glue in place (with the tabs sitting above the top plate), and use some clothes pegs to hold in place for a few minutes while the glue sets. Do the same for all other panels making sure the adjoining panel sides are the same size to the one your fitting. Leave the rear panel and 1 rear side panel off for now. (If panels are slightly too wide in places, trim to fit). when gluing the tabs to the top plate, you will want to trim off the corners of the tabs so they don't overlap and are all flat.
3.) Now that most of the panels are fitted and glue is set, carefully cover them with duct tape making sure you cover and seal the all the joins of the panels. This also adds to stability and firms up the skirts somewhat. There is enough room to put your hand in to the body because of the missing panels so you can stabilize the cardboard and smooth out any air bubbles when applying the tape.
4.) Thread the motor wires (now for the eye stalk) along with the aerial wire through the hole of the top plate. (an afterthought which might make things neater would be to thread the wires in to the tube axle from the tank turret and out through the top)
5.) Fit the last rear side panel and duct tape it, again sealing the join to the adjoining panel.
6.) With the final rear panel, I wanted to make this into an inspection or maintenance panel so I could easily access the batteries. I simply covered the panel with duct tape, glued the tab to the top plate which will now act as a hinge, then trimmed off the bottom of the panel so the bottom sat just above the base. I will make a fastener using a small peace of Velcro for this later.
7.) As a finishing touch, I decided to use the grab adhesive to help seal the tape to the top plate. Simply pipe a small amount all around the top plate and rub it flat with your finger, covering the tape and cardboard.
Now the lower body is done, the next step is the weapons panel and chest section.
Step 4: Chest Section and Weapons Panel
Moving on up now, the weapons housing and main chest panel now needs to be done. Lets start with the weapons housing.
1.) Using a peace of thin cardboard, measure out a 14cm by 15cm square and cut. The 14cm length will be the length of the panel, and the 15cm will be folded in to 5, 3cm sections to create a make a square tube and a tab for gluing together. I want to mention that when I made this part, later on, I kinda wist I had made it a bit bigger, as looking back through Dalek photos again, I realized that I did make it a bit small compared to the real thing, but with my overall project finished, it actually didn't look to bad in the end. Saying that though, I would recommend you increase the measurements to about 4x5cm or 4x6cm square.
2.) I had some PVC foam used for carpet underlay sitting around which I am going to use later for the skirt bumper. But what I did for this part was to cut out 6 diamond shapes, 3 peaces glued together, measured to fit snug inside both ends of the square tube to seal off the end, help form the slanted shape, and to help support the weapons (to be fitted later). You could of course use polystyrene or something similar.
You will see in the photos that I have a row of 4 red LED bulbs. The reason for this was simply because the circuit board which controls the motor for the eye stalk had these LED's fitted to a small p/c board on a ribbon wire, and I didn't want to waste them as they all worked. Also, the motor p/c board was also going to be housed in the chest section to leave room inside the head. So I used a little artistic license, and fed them through the back of the weapons panel and made 4 holes with a screwdriver for the bulbs to fit through. A peace of PVC foam at the back of the LED board was placed to help secure it in place, then the 2 ends fitted.
3.) Squeeze out a small amount of grab adhesive on to the weapons panel and smear it all around and leave to dry. You may need to use a bit more just to seal in any gaps on both ends so they come out nice and smooth when painted.
4.) Now make a couple of holes through the front of the panel and the PVC foam (or styrene) where your weapons will be fitted later. When the holes are done, use a bit more grab adhesive and apply to the bottom of the panel, and place on to the top base having the center of the panel slightly set back in to the chest, and enough for both ends to protrude out of the chest (as can be seen in the photos).
When the grab adhesive has set, move on to make the chest cover.
5.) With some more corrugated cardboard, cut out 2 small disks, one about the same size as the top plate of the skirt (measure it so that the front and back are the same size and the 2 sides of the disk overhang a bit) and the other just a bit smaller (I used a desert / breakfast cereal bowl). Then make a smaller hole in the center for the cardboard tube axle to fit through. Cut out around 10 or 12 strips of corrugated cardboard about 14cm's long and 2cm wide. Make sure to cut along the corrugate as these will be acting as support struts. Then bend 2cm each end on all of the strips to create fixing tabs. You may think that they will not be strong enough, but bear with me and all will be revealed.
5A.) The motor for the eye peace had its own circuit board as I mentioned earlier. To house this, I made a small cardboard compartment and glued it to the top base of the skirt section, close to the weapons panel and away from the center axle. 2 wires came from the p/c board that attached to the motor. The motor will sit above the chest section.
6.) Glue all the bottom tabs to the top base above the skirts, evenly spaced, and wait for glue to set. Then glue the newly cut disk to the top tabs of the supports, only doing 2 or 3 at a time, using cloths pegs to hold in place until the glue sets. then poke the aerial wire and eye motor through the top hole.
7.) Using some more cereal box cardboard, this will make the outer chest cover. No measurements here for this, but what I did was use a couple of sheets of scrap A4 paper, measured out 10 cm then cut out a shallow curve, placed it against the chest area, and trimmed off paper that was to high. Then make a cut out to go around the top and sides of the weapons panel. When I was happy with it, I used the paper cutout as a template and marked out 2 sections on the cereal box then cut them out.
8.) Get hold of the grab adhesive and squeeze out a thin piping along the outside of the supports (Only do half of the struts at a time) then carefully place the outer panel on to the struts, gently squeeze together, moving the panel if you need to before it sets. You will have a few minutes to do this before it does set. If (like I had) your 2 outer panels overlap, not to worry. Simply add a bit more adhesive and overlap them. Then finish off by rubbing a little more adhesive over the seams to make a smooth finish.
If you did think the support struts wouldn't be strong enough, When the grab adhesive fully sets, the outer panels will now strengthen the support struts making it nice and sturdy. Trust me, I'm a doctor (not The Doctor) ;-)
9.) Final peace to do is the outer rim that fits to the bottom of the chest panel and runs under the weapons panel.
Cut out a 3cm tall thin cardboard strip ( it can be done in 2 parts like the chest cover), cut out a small section to go around underneath the weapons panel, pipe some more grab adhesive around the bands and attach to the bottom part of the chest, and rub a little bit more over any joins.
One extra thing I did was to make a small cardboard battery holder that fits just inside the inspection panel for easy access, without having to tip my Darlek upside down.
Leave overnight for all the adhesive to properly harden and have a beer, or a coke.
Next we will be making the eye stalk, with an added bonus.
Step 5: The Eye Stalk
We're about half way through the build now and are going to make the Darlek look a bit more like a Dalek now. This was a fun part to make, although a little bit fiddly and delicate to do. I had some good photos to go by to make the eye stalk but I did have to make a few slight modifications to the actual eye peace. The reason for this is because I wanted to add something a bit special, a small WiFi web cam, that could be viewed through an iPhone or PC which could stream real time live video and take photos.
The materials I used were,
A dried out marker pen,
A hollow Christmas tree ball-ball,
2 flat top deodorant can lids,
Some small peaces of thin cardboard,
Super glue,
Aluminum tape,
A small peace of PVC foam sheet,
Some thin lengths of electrical wire,
And of course the disused WiFi web cam.
Here's how I made it.
1.) Using a very sharp craft knife, cut around the hemisphere join of the ball-ball to give you 2 halves. The ball-ball I used had a small hollow nodule to allow a peace of string to pass through to hang it on a Christmas tree. I managed to cut it in half and kept it in tact as this would be useful later.
2.) Colour the 2 halves of the ball ball black using a black permanent marker.
With the camera, it had 2 small PC boards, 1 with the on/off switch, charging port and battery, and the other connected to the camera lens and microphone. They were connected by 4 small wires with a small, plug which I had to cut and extend. If you decide to use a camera, please bear in mind that it will probably differ to the one I used, and the wiring may be different to what is mentioned below.
3.)
A. Pull the end of the marker pen off, pull out the felt cartage, then pull out the felt tip using some pliers to now make the marker pen completely hollow.
B. Cut and bear the ends of 4 lengths of the thin electrical wire almost twice the length of the disused marker pen.
C. Disconnect the plug, cut and bear the ends of one of the 4 wires connecting the PC boards (I only had a small amount of wire to work with so I used a craft knife to bear the camera wires (also doing one wire at a time insures that they are rewired in the correct order) then join and twist the ends of a length of electrical wire to the end of the wire on the camera lens board.
D. Feed the extended wire through the tip of the pen casing first, then out to the back of the pen and join to the PC board containing the battery. Follow this process for the remaining wires.
E. Use some insulating / electrical tape to wrap all the bear wire joins to prevent short circuits.
4.) Hold the 2 halves of the ball-ball together and place the deodorant lid at the opposite side of the nodule and mark around the lid. Then with a craft knife, carefully cut around just inside of the mark (as seen in the photo, unassembled)
5.) Glue one half of the ball-ball / eye peace to the tip of the pen. This is where the little nodule comes in handy, as it will now act as a support for the pen tip. I was lucky, as the 2 nodule halves put together was a perfect fit around the pen tip. After the glue has set, glue around 1 half of the eye peace and on the nodule and fit together. TIP. What I ended up doing was to glue a thin ring of cardboard around 1 side of the inner rim in one half of the eye peace to help make an easy flush fit when it came to fixing the 2 halves together.
6.) Using a craft knife of a drill, make 2 holes in the deodorant lid, 1 in the center, and another towards top center (as seen in the main photo). Pull the lens from the lens cover, feed through the center hole, glue the edges of the lens cover to the lid, wait for glue to set for a couple of hours. IMPORTANT. Waiting a couple of hours insures that glue fumes do not attach themselves to the lens itself, later obstructing the view. Then refit the lens (making sure the lens was the right way up before fixing in place, which I forgot to do at first, oops). What I then did was to glue a very small rubber gromit to the microphone hole, then gently pushed the mic in to place.
7.) Apply a small drop of glue to the top edge of the eye peace cut out, working your way around, then attach the deodorant lid and wait to dry. What I did as an afterthought, go get rid of any white patches of dried glue around the join, and the fact I could not have the eye light up like I originally wanted to (due to lack of room for feeding any more wires going through the maker pen casing / eye stalk, and possible glare on the camera lens) was to cut a small ring of cardboard, cut to length, covered it up with aluminum tape, and glued it around the edge of the deodorant lid. Then using some more aluminum tape, I covered the full length of the eye stalk.
8.) The last thing that needed to be done, was to make to pivot to allow the eye stalk to go up and down. Using the second deodorant lid, make a hole on the edge of the lid about the same size of the eye stalk so it could be a tight fit, and a second smaller hole about a third of the way around for the camera wires to fit through the other side. Feed the camera wires through the hole and then about 1 or 2cm's of eye stalk for a tight, flush fit. Use a small peace of PVC foam or polystyrene cut to tightly fit inside the lid, breaking a tiny peace off so the camera wires go around the inside of the lid, and not through the center.
9.) Lay the lid flat, use a small screwdriver or drill and make a hole through the dead center of the lid, safe to do as the wires are safely tucked away. This is where a small axle will fit through inside the head. The lid I used was red and the foam was dark grey so I used a black permanent maker to colour it all in.
10.) Now this was all done, 1 final thing to do was the 5 rings that go on the eye stalk towards the eye itself, simply using a peace of thin cardboard I cut 1 large disk, 2 medium and 2 small disks. With a craft knife I cut out some inner holes about the same circumference as the eye stalk (trial and error), coloured them black, made a small cut through 1 side of the ring, placed the on the eye stalk in this order, small, medium, large, medium, small. Applied a small drop of glue on the eye stalk about 1cm off the end near the eye, then slid the rings in to position, one at a time leaving about 1/2 a centimeter gap between them. Prop up the entire eye stalk keeping it level and allow the glue to set. Finally, use a tiny tiny peace of black insulating / electrical tape to join the cuts made to fit the rings on the stalk. Or put the rings on whole, without cutting, before you attach the pivot section and glue at the end. (Wish I did that, ha ha. I simply forgot).
I should note that in some of the photos, where the camera lens joins the eye peace, it can be seen where I did originally use PVC foam but it looked really rough which is when I decided to use the deodorant lid instead which I think looks much neater.
Now we are rocking and rolling. Time to do that famous domed shape head.
Step 6: The Head
Ok, lets give this guy some character. Now before I continue, I have to admit something. I got VERY lucky with the actual dome shape, as throughout the build, I didn't really know how I was going to achieve a smooth dome with a good size. Thoughts were a top of a fizzy drinks bottle (not big enough) a bowl from the kitchen (the chef of the house disagreed), and various other ideas, one of which was a kiddies football that was in the garden and hadn't been kicked in years. I dug it out of the bushes along with another, slightly larger one, washed them, and cut them in half with my craft knife starting with the smaller one. I measured it up against the top of the chest, too small. So I cut the larger one in half, measured it, and I guess my luck was in that day. It was a PERFECT fit, made to measure. That did make me smile.
The materials I used for this were,
Half of a kids small football (obviously),
2 red 12 volt LED bulbs,
Wire,
A 9 volt battery snap connector (to be connected later),
2 small screws,
1 long thin bolt about 8cm's long,
2 peaces of "L" shaped plastic I cut from an old VHS cassette box,
Thin cardboard,
2 yellow plasticy tubey thingies the size of my little finger, that came from a Christmas cracker (I really don't know what they are for, but I know what they are going to be),
A long screw about 8/10cm's long,
and the eye stalk.
So, here's how I made it..
1.) Using a craft knife, carefully cut a rectangular hole at one side of the half ball, just slightly larger than the eye stalk pivot all the way around so the pivot can move freely. This will form the eye socket. Remember to cut small to start as you can always cut bigger and not the other way around.
2.) With a very small screwdriver, make 2 pilot holes half way up beside the newly cut out eye socket, about half a centimeter away from the cut on both sides. Do the same on the 2 plastic "L" shape brackets cut from the video tap box, on one side. On the other side you need to make 2 more larger holes which will hold the pivot axle. Using the 2 small screws, screw them in to the pilot holes you made in the head, screws pointing inwards. Now screw the plastic "L" brackets through the small pilot holes, attaching them to the inside of the head, with the standing up part of the brackets flush with the eye socket cut out.
3.) Use a large drill bit (or a screwdriver then a craft knife, but this will be more difficult to do, but possible) and make two holes on the left and right sides of the head, about 3/4 of the way up, and insert the yellow plasticy tubey thingies which will form the "Luminosty dischargers" or ears that flash when a Dalek speaks. The yellow tubes I used were smaller on the top sealed end, and wider on the bottom making a nice tight fit.
4.) Grab the 2 red LED bulbs (I had to solder some wires to mine, using red wire for + and black wire for - polarity) then poke them in to the bottom of the ears, and use a small peace of polystyrene to wedge in to the bottom of the ears to keep the bulbs in place. then join both black wires together and red wires together. What I liked to have done here, would have been to fit either a flashing light circuit which i didn't have, or a sound activated flashing light circuit which I did have laying around but I was saving this for my next project.
5.) Before fitting, get the eye stalk and place it on your work surface the right way up (so your camera view wont be up side down) then with a screw measuring about 8 to 10cm's long, screw it in to the middle edge of the pivot (6 to 8 turns should do it), about 3/4 of the way up so the screw protrudes about 45 degrees facing up. This will be the counter leaver for the eye stalk. Then using a length of electrical wire, tie around the screw as close to the screw head as you can. Cut a little peace of duct tape and wrap around the screw and wire knot to stop the wire slipping down the screw.
6.) Time to attach the eye stalk. With the head up side down, use the thin 8cm bolt, poke it through one of the brackets, so the bolt is just poking through. Place the eye stalk pivot, also up side down, in to the eye socket, then push the bolt through the hole you made earlier through the center of the pivot, then push through the other bracket. This can be fiddly to do, but very satisfying once its done.
Just test to see if the eye stalk moves up and down freely with no obstructions, and does it straight and true. At this point you can always reposition one of the brackets if needed.
7.) To finish the head off, and to add some much needed stability, grab a peace of cardboard, lay on the work surface and place the head on top. Draw around the head on to the cardboard and cut out a cardboard disk. You will now need to cut out an inner circle to make a ring, about 3cm deep. Use the ever faithful grab adhesive and pipe some out around the edge of one side of the entire ring. Then place the head on to the ring making sure all around is flush with the ring edge. You will have a good few minutes to get it absolutely perfect before the adhesive begins to set, so don't panic and feel you have to rush this step. It will pay off with the end result.
So lets give this little fella a neck. That's next.
Step 7: The Neck Section
This next part was relatively straight forward to do, but I did have a couple of trial and error episodes with some quite comedic results (sorry, I deleted the photos of my first 2 attempts). The only difficulties I had were getting the measurements between the rings correct. My first attempt, after laying the head on just to see what it would look like, ended up having a really tall neck, so much so I would have had to call him "Dalek Giraffe". My next attempt was an improvement but still to tall. Third and final go was a success.
To make this section I used,
Cereal box cardboard,
6x 5.5 cm screws,
Some PVC carpet underlay foam 12mm thick (or you could use some polystyrene sheet,
And some grab adhesive.
Here go's.
1.) Using the dessert / breakfast dish used earlier to make the disk fitted above the skirt section, and some cereal box type cardboard, mark and cut out 5 disks. Now with 4 of the disks, use a smaller plate to mark, then cut out an inner circle to make rings about 3cm deep. The 5th disc leave whole.
2.) Cover both sides of the 4 rings with a thin coating of grab adhesive, using your finger to rub it in and completely cover the rings. Leave to dry which will only take a few minutes. They might bend a bit when dry, but they will straighten up later when fully assembled.
3.) To make the supports, use a peace of PVC foam and cut in to 6 peaces measuring 5.5cm tall and 3cm wide. On the edge of each section, starting from one end, gently screw in one of the 5.5cm screws, trying to keep it as straight as possible to make a spine (see photo). Screw them in the full length of the PVC foam supports.
4.) With a pen, measure and mark each strip with the following... 1cm, 1.5cm, 1.5cm. Now with a craft knife, cut down the width of the supports down to the screws (see photo). If any of the grab adhesive peels off, not to worry. this can be re applied at the end.
5.) Now slot the rings in to one support at a time, spacing then equally, with the screw spine facing inwards. To finish, apply a little drop of super glue around each edge of the supports and rings when your happy with the positioning.
6.) Final steps for this section. Grab the forth cardboard ring, then apply a thick amount of adhesive on to the bottom of each PVC foam support and attach disk to the ring section. The bottom of the ring section is where the supports are shorter, and the top will be taller (as seen in the main photo).
7.) The housing of the camera on/off switch and charging port will be situated in the center of the ring section. So for the final part, I added a small metal hinge, measuring about 3cm by 1.5cm which I got from a small plastic jewelry box which easily slid out. I simply opened it up and super glued 1 end to the bottom of the ring panel, hinge join facing out, and positioned so both corners were flush with the edge of the disk so it would be out of sight. This will be at the back of the Dalek.
8.) Marry up the 5th cardboard disk you cut and ring section, with the metal hinge facing the rear, making sure you have a perfect fit all the way around and make a small mark where the hinge is to be fixed. Having the super glue to hand, open up the metal hinge fixed to the ring section to 90 or 180 degrees (what ever is easier), apply some glue to the cardboard disk and attach the the hinge plate and wait to set. You will need to wait for the glue to completely dry as you don't want the the hinge to stick together.
Now that's done, next we will be attaching the camera switch, eye stalk motor and fixing the ring section to the chest section.
Step 8: Eye Stalk Motor and Camera Switch Housing
The two parts I needed to fit together were the lower housing for the camera on/off switch which also contained the rechargeable battery, made of plastic, and the motor housing for what was the tank cannon to make it go up and down, again made from plastic and had 2 screw holes for fitting. Both peaces were about the same size and together would fit nicely inside the ring section.
1.) Make a small mark with a pen on the base disk of the ring section directly opposite the hinge placement. This will now mark the very front of this section.
2.) I needed to make a wheel for the pulley system to work the eye stalk. The motor had a small white cog fixed to the motor drive shaft. Using a flat top lid from another deodorant can, I cut around the sides of the lid and cut out the flat top part of the lid. I then punctured a small hole through the center and another near the outside of the wheel, and with a craft knife carefully cut out some small teeth in the center hole to fit around the motor cog. Then i squeezed the lid on to the cog and applied a small drop of super glue.
IMPORTANT NOTE. I placed the motor on a small length of wood with the newly made pulley wheel laying flat and below the motor cog. This was to prevent any excess glue running down the drive shaft and then seizing the motor.
3.) The power switch and charging port for the camera is located on the side of the housing. I needed easy access to these so they were going to be facing the front. The eye stalk motor needed to be facing upward but towards the rear of the ring section (as seen in photo). I simply positioned the 2 parts together until I has happy with the placement, marked, and made 2 pilot holes through the motor screw holes into the camera housing, then screwed together using 2 small stubby screws.
4.) After cutting the motor wires, extending them a bit, and feeding them through the small hole in the ring section base, along with the aerial wire, I then made 2 more pilot holes about 1 centimeter apart, in what would now be the the base of the camera housing. Then lining up the front of the camera housing to the front of the ring section, I screwed through the ring section base into the base of the camera housing pilot holes making a sturdy fit, then reattached the wires. For now I just rested the ring section on top of the chest.
Time to put it all together.
Step 9: Head, Neck and Ring Section Assembly.
Time to put this little guy together by first fixing the ring section to the chest, and then the head to the ring section.
All the wires for the lights and aerial should be connected and running through the center of every panel. You should have a good length of the center axle which will turn the head, poking through the top of the chest section. I should mention here that on a real Dalek, the ring section stays fixed to the chest section and only the actual head dome rotates. I went a little different with this as I didn't want the 4 wires coming from the eye stalk pulling to much on the housing, and I need room for the pulley system for the eye stalk.
1.) Cut the center axle so you have about 10cm's poking out the the top of the chest. Using a craft knife, carefully cut 4 evenly spaced slits straight down the length of the axle down to the chest section, and flatten out to create 4 fixing taps that the ring section will be attached to.
2.) This step is optional but does help. Using some aluminum tape, stick some to the top of the chest section, the wrap some around each of the 4 fixing tabs. Smear some grease or some petroleum jelly (Vaseline) to the aluminum tape on top of the chest section to provide a smooth movement.
3.) Using a peace of PVC foam sheet, cut out a disk the same size as the top of the neck. Then cut out an inner circle to make a ring about 1cm deep. Then glue to the top of the neck panel. This will keep the head level and hide the axle fixing tabs.
4.) Making sure the turret of the tank is facing forwards (centered, so it has equal measurement of turning left and right), apply some grab adhesive on the upside to all 4 fixing tabs of the axle, and place the ring section with the pen mark you made earlier facing forwards, on to the fixing tabs making sure no wires are caught in-between both sections. Leave overnight for adhesive to fully set. I actually put a drill battery and some card on top of the ring section to weigh it down while the adhesive hardened. One thing I did as an after thought was to cut some strips of paper and fit them inside the ring supports which would later on become black after painting.
Now comes another fiddly bit. It can be done yourself, but having another pair of hands will make life much easier. Before the head is permanently attached to the ring section, we need to fix the pulley wire coming from the eye stalk counter lever, to the wheel on the motor described in step 8.
5.) Insure the hole you made in the outer rim of the wheel fixed to the motor, is at the highest point (at the top of its rotation). Rest the head half on top of the ring section, and with the counter lever wire, feed it through the hole made in the outer edge of the motor wheel and tie it off a couple of times. To make this a little easier you can raise the eye stalk so it is pointing straight up to give you a little extra wire to work with. With the wheel at the highest point, the eye stalk should be looking straight ahead or pointing down a bit (as seen in the main photo) and when it is at its lowest point, it will be pulling the wire and raise the eye stalk so it looks up. Then plug in the camera plug to the battery circuit board.
At this point, you can check the eye movement by plugging in the main battery and, with one hand holding the head in place, pulse press (quick multiple presses) your controller to check that the eye stalk moves freely and that your happy with the highest and lowest resting points, adjusting the wire length if necessary.
6.) To attach the head, apply some blobs of grab adhesive to the top of all 6 of the PVC foam supports and rest the head down on to them, applying a little pressure downward, insuring the head is on straight and even all the way around, then leave to set.
7.)The base bumper. Using some more PVC foam, cut out some strips about 4cm's wide and long enough to go around the entire base of the Dalek. I didn't have any foam long enough to go all the way around in 1 peace, so I had to use 2 shorter lengths per layer. Cut enough to make 3 layers to make the complete bumper. 1 layer at a time, pipe some grab adhesive down the center length of one side of the foam, and apply to the sides of the base under the skirt panels, gently squeezing it on, insuring it is straight all the way around. You will have a few minutes to do this before the adhesive begins to set. Do the same to the 2nd and 3rd layers waiting about 1/2 hour between layers. The foam is light enough so it shouldn't slip down.
One little thing you can do now if you had to use more than one peace for the final layer, is to use a little more adhesive, put some on your finger, and rub over all the joins to eventually make it look like one peace . When finished, leave overnight.
7A.) One thing I forgot to mention, I wanted to insert a small switch in between the last 2 outer layers to switch the under chassis lighting on and off. I did this by cutting a small hole though all 3 layers before fitting to the base. This was done at the rear of the Dalek, just below the maintenance panel. The switch was glued between the 2nd and 3rd layer keeping the switch flush with the outer layer.
8.) To finish off, the next day, pipe a heavy load of grab adhesive all around the join of the base and the first applied foam bumper to fill any gaps. Simply rub your finger all the way around to make a nice smooth join (you may need to do this more than once) to fill any small holes that may appear when it sets.
9.) To prepare for paint, we are going to cover the entire Dalek with more grab adhesive. Bumper, skirt, weapons panel, chest, chest band, NOT the ring section as this is already done, and the head. Before you do, mask off the ears and weapons panel LED's (if you have any fitted). You should also poke a little bit of PVC foam in to the under chassis light switch. Have a peace of cloth to hand to wipe your fingers every so often. I tried to use a spatula to apply and smooth the adhesive, but it wanted to stick to the spatula more than it did to the body, so my finger was the best bet and worked really well because the heat from my finger made the adhesive really pliable and easy to work with. When dry, rub any rough parts with some very fine sanding paper.
The football I used for the head had shallow grooves all around it. After the 1st coat of adhesive dried, it went a brown / creamy colour and the head actually looked a bit like a brain (not very well seen in the photos) and although it did make me giggle a bit, it was not the look I was going for. So I applied a further 2 thick layers of adhesive, smoothing it with my finger, concentrating on the groove areas, then a 3rd thinner coat and rubbed it down. The end result I was very pleased with.
A small note, when applying the adhesive around the lower chest and band (seen in photos) use a small screwdriver or something to clean out any adhesive between the 2, because you don't want these to be a flush fit and want the band to stand out a little (which will be more noticeable after painting.
Okay, starting to look like a Dalek now I hope you'll agree. Next we will give him (or her. Are there any female Daleks?) some firepower. Weapons next.
Step 10: Weapons
A fun and easy part was to make the manipulator arm (sucker) and the laser / gunstick. The materials I managed to source for these were as follows,
3 used up marker pens (1 wasn't quite used up but it made the sacrifice)
A rounded lid from a shaving cream can
Some thin steel wire
Aluminum tape
Glue and a small screwdriver
1 screw and small peace of PVC foam (or polystyrene)
1 LED bulb + wire (I used green but wanted to use a blue bulb, but didn't have any)
and a working black marker pen.
1.) Hollow out the 3 marker pens, removing the ends then the felt cartridge's and nib's.
To make the manipulator arm
2.) Colour the rounded lid with the black permanent marker inside and out (unless you have a black lid)
3.) Make a small pilot hole in the top center of the lid and insert a screw. Then twist a small peace of foam on to the screw.
4.) If you can, insert 2 of the marker pens in to each other, if not, then glue together. Then carefully wrap some aluminum tape around the length of both pens making it as smooth as you can, twisting the pens and smoothing the tape slowly.
5.) Squeeze the foam and lid in to one side of the pens for a solid fit. Glue together if you wish. And it's done
To make the gunstick
7.) Wrap the leftover pen with aluminum tape. Then on the main body of the pen, using a very small screwdriver, make 6 equally spaced pilot holes near the tip end, and then 6 more about 3cm's from the end.
8.) Poke the wires of the LED bulb through the tip of the pen and out the back end. Glue the LED to the end of the pen tip.
9.) Cut off 6 equal lengths of the steel wire, and bend both ends to the same length of the the pilot holes, end to end of the pen. The bends need to be about 2cm long.
10.) One at a time, poke the bent ends of the wire in to the pilot holes, enough that the length of the wire sits above the pen shaft about 1cm, then add a small drop of super glue to each hole to secure the wire in place. (In the Photos, You will see a grey pen lid. I didn't use it in the end as the LED didn't illuminate it enough).
Put the weapons to one side for now, as they will be attached after painting. Speaking of painting, guess whats next?
Step 11: Hemispheres and Chest Slats
Haha, Not painting quite yet. Only one more step before we do though (although a little paint will be used here). A couple of peaces to complete to make our Dalek look a little more, well, like a Dalek. The chest slats and the all important Hemispheres. A Dalek wouldn't be a Dalek without them.
The materials I used for these parts are,
Cereal box cardboard
polystyrene balls measuring 3cm diameter (I had to purchase these online)
Small pot of touch up emulsion paint
Grab adhesive
22 small modeling tacks (tiny nails). These are normally used as model railway track pins, fixing the track to a baseboard.
And some thin steel wire.
Lets start with the chest slats.
1.) Using the cereal box cardboard, cut out 8 small slats measuring 6.5cm x 3cm, and 14 slats 8cm x 3cm. I should mention here that it wasn't until later after I painted them, I realized that 3cm's was a little bit too wide as photos of other Daleks have about 16 long, thinner slats and about 6 short ones, so feel free to play around with the numbers. With the measurements I used, I ended up using 4 short slats and 7 large ones, which at the end didn't look too bad.
2.) On half of the cut out slats, you need to mark and cut out an inner section (as seen in one of the photos). Now apply a little grab adhesive around the edges of the cut out slats and stick on to the whole peaces. To help with the smoothness and shine, use the laminated side of the cardboard facing outwards.
3.) Now push 2 small tacks in to each slat, one at the middle top, and one in to the middle bottom. Then using a scrap peace of card, polystyrene or something similar, push the tacks in to it, keeping a small gap between the slats and keeping the slats raised slightly above the polystyrene surface so they don't stick, and you don't end up pulling any paint off the slats when it has dried. This will help all the slats stay in one place and not blow around when you spray paint.
Now for the hemispheres.
3.) I purchased a bag of 50, 3cm diameter polystyrene balls which cost me about £3 / $5. For the hemispheres I needed 26 balls to be cut in to 52 halves. To start with, using some thin steel wire I used earlier, I cut 30, 5 to 10cm long lengths and bent one end of each in to a hook. I then pressed the other end in to the center join of the balls about half way through. I did 30 balls for some spares.
4.) Then using the small pot of paint (doesn't really matter what colour) dip each ball in to the paint and flick off any excess drips. Then while still holding the wire, slowly tip each ball up and down to make sure each ball is evenly coated and reducing the size of any drip bubbles. Hang the balls up and when you have done all of them, go back and check for any major droplets hanging off the bottom of the balls and just repeat the process of moving the ball around again. As seen in one of the photos, I used a couple of thin strips of wood suspended on the paint cans I will use later. Leave overnight to dry.
5.) When dry, gather all the balls and remove all the wire hooks. Now with a sharp craft knife, cut down the center of each ball as straight as possible, making equal size halves, starting where the little hole is where the wire hook was poking in.
A WORD OF WARNING just in case your not aware. Polystyrene and spray paint are not friends (As seen in the last photo).
At this stage I mounted all the halves on to a couple of small pizza boxes with tacks pushed through the top of the boxes at equal spaces, and mounted the half balls on to the tacks still leaving a small gap so they wouldn't stick to the boxes. I then primed and spray painted all the half balls with a couple of coats. When they completely dried, some disaster. Some of the spray paint got underneath the small gap I left between the half balls and box, and started eating away at the bear flat side of the polystyrene leaving some really rough edges on some of the halves.
This was lack of forethought on my part as I already knew the paint would react with the styrene, which was the whole point of dipping them in the emulation paint in the first place.
6.) So after that hiccup, I Used some more spare balls, dipped in paint, dried, and cut in half. This time I covered the bare styrene base with some grab adhesive to seal it up and this time it worked.
Another obvious way would have been to cut the balls in half then dip and spray. My problem with this was that a small hole made by the wire hook might cause an issue later and become viable after spraying. Or of cause I could have poked the wire in from the flat side, which I tried, but the halves kept coming off the wire and stayed in the pot. Spray painting a whole ball might have cracked or chipped paint away when cutting. Final way would have been to get a small pot of gold emulation, but I couldn't get hold of any.
Anyway, all the parts are ready for painting. My favourite part.
Step 12: Prime and Paint
Let the fun begin. After a couple of days of looking at many many pictures, and indecisive thinking of what colour scheme I wanted to use, I really liked the idea of black and gold, so, that's what I went with.
1.) Mask off the ear lamps, eye stalk (with a plastic bag and tape), as much the eye stalk pivot as possible (I used electrical tape poking it in as far as I could), and weapons panel LED's (if fitted). Now you can apply the first coat of grey spray primer. Place a small sheet of scrap wood or corrugated cardboard on to the surface where your going to paint, then place the Dalek on top. This will make it easy to turn the Dalek without touching it while painting. Now apply the first coat of primer with thin even coats over the entire body. Leave to dry (as per can instructions) then apply a second coat, keeping about a quarter can primer left over. Just to note, I used 1, 500ml can of primer, 1 gloss black, and 1 gold.
2.) Next, apply the rest of the primer to the chest slats and half spheres. You should get 2 coats out of whats left of the primer.
3.) Using a strip of black plastic mesh used for gardening, place the paper template you used to mark out the cardboard chest cover, and cut the mesh to roughly the same size with a pair of scissors. Marry it up to the chest and trim the mesh where needed. Apply some grab adhesive to the chest cover, doing it a section at a time, then attach the mesh. Wait a few minutes for the adhesive to go off and continue all the way around. Any overlap of the mesh, simply cut off and if it is not a perfect match it wont matter as it wont bee seen when the slats are attached.
4.) Use a refuse bag and cover the head. Open up the ring section where the camera switch is located, and tuck the edges of the bag underneath. Just double check to make sure the bag is not overhanging any part of the body. Tape up any parts of the bag that are. Now Spray the entire lower body with the black spray, again using thin even coats. You should get about 3 to 4 coats. Leave for at least 24 hours or until totally dry with no tackiness anywhere.
5.) When the black paint is totally dried and cured, carefully remove the refuse sack looking out for any paint that may be joining the bag to the top of the neck. Now do the same process of masking with the same or another refuse bag, this time covering the all of the black section of the lower body. Now you can hit it with the gold paint. As there is less surface area for the head, you should get 2 to 3 coats of gold paint leaving you just under half a can of paint. Use this half can to spray the chest slats and spheres, making sure you get every angle of the spheres. Again, you should get about 2 coats of gold. Leave again for 24 hours to properly dry.
6.) 24 hours later, you can now carefully remove ALL the masking. Just make sure the bottom of the ring section is clear of any over spray, and not stuck to the top of the neck by inserting a small screwdriver and slide it all the war around. You can also plug the battery in and use the controller to turn the head in each direction to check everything is hunky dory.
Side note. Both the gold and black spray paints I used advised against using paint lacquer, the black saying it will dull the shine, and the gold saying the gold wont be as gold and will be more of a silver colour. So I didn't use any, and the end result was great.
That's the painting all done. Fun while it lasted. Time for the finishing touches.
Step 13: Finishing Touches. Attaching Weapons, Hemisheres and Slats
Wow, we're nearly there. If you stuck with me so far, your a real trooper, and if you skipped to the end to look at the good pictures, that's cheating (and they're on the next steps haha ;-). Only joking. Right, let's get this bad boy done and dusted.
1.)Chest slats. Remove the chest slats from the scrap polystyrene holder. Now at this point, I was going to remove the tacks from the slats but a liked the look of them as they looked like little gold rivets. Using some wire cutters, I tried to cut the end of the tack, and it cut really easily. If you do this, cup one hand over the upside down slat and cut. This will stop the excess tack flying off somewhere only to be found later when you step on it. Ouch.
2.) With all the tacks now cut, leave the slats upside down on the work surface and apply a little drop of super glue to each tack and leave a few minutes to set. Next, starting with the smaller slats, apply with a line of grab adhesive down the back center of the slats, one at a time. Then attach to the chest panel over the black mesh with a very gentle push, just slightly off center of the front of the Dalek, over the weapons panel. Then do the same for the next small slat. Then add the next two small slats, making sure they are all level and evenly spaced. The texture of the grab adhesive will hold the slats in place without you having to hold each one in place until it sets.
3.) Now continue with the rest of the larger slats. Its best to attach the first longer slat beside the weapons panel first, then fix your second slat to the rear directly over the inspection panel. This helps you evenly space out the slats all the way around. Done.
4.) Hemispheres. Starting from the top of the skirts, you will need one sphere per panel, with the exception of the larger side panel which will have two. Simply apply a small blob of grab adhesive to the flat side of the spheres in the middle. Then gently press them to the middle of each small skirt panel, and two side by side on the two larger panels. Work your way around doing every panel. Insure that all the spheres are level with each other, gently sliding any in to place that need to be repositioned.
5.) Now repeat the process, this time around the base just above the bumper. When the base is complete, go panel by panel adding the final two spheres (four on the two larger side panels), making sure they are evenly spaced down and across the skirt panels. Done.
6.) Weapons panel details. The pizza boxes I used to fix the half spheres to, had a healthy coat of shiny gold paint. Shame to waste it, so with a craft knife, I cut out a small section and then very carefully cut the corrugate off to leave a thin sheet of card. I then cut out two 3 x 3cm squares and a 5 x 2cm rectangle. With the craft knife, I cut out two circles in the square cut outs the same circumference as the weapons, and a smaller rectangle in the 5 x 2cm peace, enough for the 4 LED's to fit inside. Then I simply super glued them in place. Done.
7.)Weapons. starting with the simpler weapon, the manipulator arm (sucker), squeeze some grab adhesive (yup, still got some left) in to the left hand hole of the weapons panel and push the arm in, pointing it in the direction you want. This will set hard and you will not be able to move the weapons once the adhesive has fully set. If you would like poseable weapons, you could use plasticine, Blu-tack of something similar. unfortunately I didn't have any to hand.
8.) Gunstick (laser). With a drill or screwdriver, make a hole going through the already made gunstick housing hole in to the chest panel. With a thick peace of scrap wire, poke it through the hole and feed in to the base and out of the inspection panel. With the end pointing out of the gunstick housing, attach the two wires from the LED in the gunstick and pull the end hanging out of the inspection panel, feeding the LED wires through the body and out of the inspection panel.
9.) Now remove the scrap wire from the LED leads and wire them to the 9v battery snap connector you put aside earlier in the build. Now pipe the grab adhesive in to the gunstick housing and push the gunstick in to place, while gently pulling the leads from the inspection panel. Done.
10.) Final finishing touches. Using a little bit more of the PVC foam, cut out some small strips, size enough to fit between the rings and ring supports. Colour them black with a black marker. Then apply a little drop of super glue to the uncoloured side and place between each of the rings between the support panels. Use a couple of small screwdrivers to push in place and attach to the paper inside the ring section. Last thing as an optional extra, I wrapped the controller with some cardboard, coloured it black, and added some of the damaged gold half hemispheres using some grab adhesive. Done and done
HURRAY. "I christen thee, Dalek BOB (Built Out of Boredom)". And now the build is pretty much finished. All that needs to be done now is to recharge the main and camera batteries. Have a look at the final 2 steps for a fun and interesting optional extra, as well as some more photos and some final thoughts.
Step 14: A Fun Optional Extra
Now we are all done, here is an idea for a quick and easy optional extra to add a little bit more authenticity. Dalek BOB pretty much looks the part, but he is a little quiet, so here's how I made him talk (sort of).
I used a Bluetooth sun visor car kit and my iPhone. The speaker was small enough to fit inside the inspection panel and didn't cause any obstructions to the tank turret which turns the head. I made a second battery compartment made from cardboard, attached it on the top of the turret, and placed the main battery in to it. I now used the original compartment I made to rest the speaker in to it (as seen in the second photo).
I then downloaded a soundboard creator app from the app store, found some Dalek voice samples online, and recorded them to the soundboard app. Paired the phone to the speaker, opened the app, and started pressing buttons to make BOB talk with the words and phrases I recorded.
Now we're pretty much done, please have a look at the last step for some final thoughts and some final photos of Darlek BOB showing off his new lights in the dark, even shooting his new laser weapon.
Step 15: EX-TERM-IN-ATE in the Dark
I still have got quite a few materials waiting to be used, and our recycle bin fills up fairly quickly, so, I have decided to start a new build, this time building my favourite Doctor Who character of all time, K-9, and with a fun Idea to make him speak even better than Dalek BOB, using an iPhone/Android/PC app I found.
And if you were wondering how I got Dalek BOB to shoot a laser (as seen in a couple of photos), It not CGI, photo editing or anything like that. Quite simply, I used a translucent green drinking straw fitted to the end of the green LED. A bit of fun but I hope you'll agree, quite effective. My only wish was that the bulb was a bit brighter. Oh well.
If you made it this far, I would like to take the time to thank you for reading, and I really hope you found my instructable entertaining and useful. I have tried to keep it as simple as I could, but also detailed enough for novice and seasoned builders alike. If you haven't already, check out the short video I made showing of BOB's various movements and features. I also mode another short video showing both my K-9 and Dalek BOB builds interacting with each other. The video is no cinematic masterpiece, but just a bit of fun showing off how K-9's A.I programming responds to the pre-recorded phrases from Dalek BOB, sometimes with some interesting results. So have a quick look, it might make you giggle. We (Dalek BOB and I) would love to hear your comments, thoughts, ideas, and suggestions, along with any questions or quires you may have. And If you do decide to take up the challenge of building your own Dalek, we would love to see what you come up with.
That's all from me for now. Thanks again for reading and, "Happy Building".
Steve (and BOB).
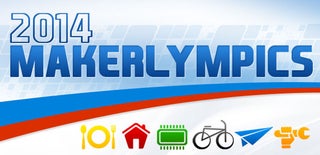
Participated in the
Makerlympics Contest