Introduction: Cardboard Barrel Biplane. the Flyin' Lion
This Instructable will show how I built a two seat biplane using cardboard barrels, an old garden cart and a ceiling fan. This plane was designed to tow behind a small garden tractor. As always when working with any tools always wear safety glasses and wear appropriate safety gear for what you are doing.
While trying to design a tow behind train car for my daughter, I looked at an old ceiling fan and had an idea. I decided that a plane, instead of a train, would be way more fun. With the ceiling fan as the engine and propellers one of the hardest parts was done.
Step 1: Collecting the Parts.
After deciding to build a plane, I rounded up anything I thought might be useful. Some of it was put to good use and some never made it on the plane.
First were the cardboard barrels. I got these from my work but if you check around people give them away all the time. Be careful of the product that was in them previously, as they are used to ship almost everything. Mine were full of springs originally.
Next was the axle and tow bar assembly from an old rubbermaid garden trailer. I also had some wheels and large casters from an electric wheelchair.
I started by adding a wooden frame on top of the rubbermaid axle. The original axle was not the right size for the wheels so I needed somewhere to bolt them instead. I made uprights out of scrap 2x8's which were attached to a 2x8 cross bar. The angle was determined by where the cross bar fit when they where tipped back.
Step 2: Engine and Prop
The first barrel will hold the "engine". The ceiling fan blades make nice propellers once cut down. I removed the blades from the fan and cut about 4 inches from the tips with a jig saw. I used a coffee can to draw the curve on the first one then used it as a pattern for the rest. To sand them down I stacked them together in a vice and used a palm sander then hand sanded each one to smooth the edges.
To allow the ceiling fan to sit into the barrel, I needed to make a large hole in the metal lid. The fan has a rather flat top so I measured the diameter that would allow it to sit flat and still leave metal to attach too. I marked the center of the lid then drew a circle to hold the ceiling fan. I used a drill to make a hole in the center of the metal lid, then slowly and carefully, spiraled out with metal shears. It is much easier to cut thin strips and clip them off every so often than try and cut it all at once. Be very careful whenever working with metal shears as they leave an extremely sharp edge on both pieces. It is best to wear gloves for this step. Once the hole was done I removed the sharp edge with a round file and some sandpaper. The ceiling fan now sits into the barrel with the brass cover looking very much like a radial engine.
Step 3: Fuselage and Landing Gear
I eyeballed the dimensions for the landing gear and cut some scrap 2x12's down. These were attached to some pressure treated 2x4's that form the lower frame. The barrels were then screwed to the 2x4's to form the fuselage. Really starting to look like something now.
Step 4: Top Wing
The wings were originally the bottom panels in a king sized waterbed. To start the top wing was temporally mounted on some 2x4's so I could check the proportions. I think it looks pretty good so far.
Step 5: Bottom Wing
The bottom wing was screwed on from underneath with a 2x4 and 1x6 as support to the front and back. The back edge of the lower wing will be a step into the front cockpit so I wanted it strong. The corners where trimmed off at a 45 degree angle. I trimmed off the back more than the front to give it the classic biplane wing look.
Step 6: Lucky Find, Tubes of Steel
I had the best luck with this project at this point. I had some stainless tubes with angle mounts on both ends that turned out not only to be two mirror pairs but they also had almost perfect angles for mating the top wing to the fusalage. I had to do some bending to get the plates to fit perfect but once done, they looked awesome. These could easily be made from 1x2's like the other wind supports but having these was a super lucky break. The top wing was reinforced with 2x4's to keep it from flexing and as a place to attach the support brackets. The center rear of the wing was cut out with a jig saw. This was for more visibility on the real planes and, I thought it would look more authentic.
Step 7: Opening Up the Body
I laid out an opening on the top side of the barrels using a large T-square and a coffee can lid, to get the curves. The opening is roughly 1/3rd the size of the barrels circumference. The opening is made at the bottom of the barrel so the bottom then becomes the back of the seat. I left about an inch of material at the bottom edge to attach the foam pipe insulation.
Step 8: Make a Seat
To make the seat I first cut a floor board out of plywood. The corners need to be notched to fit around the bulges where the support bands are connected to the barrel. Next I traced the barrels curve on to two short 2x4's then cut them with a jig saw. Finally a smaller piece of ply for the seat top. Next we needed a control stick so I cut down the spare handle from an old mini roto-tiller. The control stick was attached through a hole in the front seat riser. I drilled a 1/4 inch hole through the control stick and used a piece of rod as a hinge. Attaching the end to the bottom piece of plywood with a spring gave it the resistance I wanted. This was just the prototype as I planed on building a full joystick to work the rudder and rear elevators at a later point.
Step 9: Tail Wheel and Test Flight
The tail wheel from the same electric wheelchair needed some modifications. The tire was made from foam and broke like styrofoam it was so old. Luckily, I had a second set of caster wheels the same size that had real rubber tires. Of course the bearings and axle bolts were not the same size so I had to enlarge the holes with a forsner bit. Once drilled out the new wheel worked great. I made a test piece to mount the tail wheel then installed the vertical bracing at the wing tips and my test pilot was ready to go.
Step 10: The Tale of the Tail
Now that it had passed its first test flight, it was time to put on the tail. The 2x4's originally holding the top wing were reused to extend the tail back another 3 feet. To the end of these, I mounted a 8" stainless steel ring from my scrap pile. The ring already had two lugs wielded to the sides with holes that I hoped to use as a hinge. Using 1x2's I started to piece in the tail section. I wanted it to have a nice taper. Once again, I eye balled the proportions to give the tail the authentic look.
Step 11: Ribs and Slats
I cut down some pieces of 2x4 into braces and placed them behind the rear seat. These were used to attach the 1x2's for the tail, keeping them even with the outside of the plane. The tail ends were bolted through the stainless ring with some large carriage bolts. A little overkill but it's what I had on hand from another project.
Step 12: Priming and Diagonal Bracing
To keep the wings together, more 1x2 diagonal bracing was installed. Starting from the top leading edge down to the bottom leading edge and from the top trailing edge to the bottom trailing edge. With all three braces installed, the wingtips are very sturdy. At this point I removed the middle barrel and sprayed the metal rings with a metal primer. I used a small palm sander to go over the wings and bracing as well as the main frame removing splinter hazards. A few minutes with the leaf blower to get the dust off and.....
Step 13: Recycled Blues
It's blue! The first coat of paint and it looks good. The blue was left over recycled exterior grade paint. Not only did I have plenty of it but it matched the mane on my daughters favorite stuffed lion. This helped with the color choice and the name for the plane. The Flyin' Lion.
Step 14: Stabilizers, Elevators and Some Rudder Action Too
The horizontal stabilizer (the little rear wing) and most of the tail pieces were made up from the third piece of ply from the waterbed. The vertical stabilizer was doubled up so I could recess a pair of door hinges to hold the rudder. The rudder has a slot down the front to hold the hinges. Some scrap piano hinges hold the elevators (little horizontal tail flaps). Eventually the two elevators will be linked together with a rod through the tail ring.
Step 15: Tail Wheel and Butt Plate
The tail wheel was mounted onto a piece of 2x8 that I cut at some really crazy angles to get to fit right. You can see it is already rubbing and I've sanded some of the wood away above it. On the very end, I used some 1/2" ply scrap trimmed down makes a nice rear cover plate. The tail was covered with cardboard cut from another barrel. Using the jig saw, I cut the ends off the barrel then split it up the middle. to match the taper of the tail simply twist the ends and you can get all sorts of shapes. Once carefully trimmed down, it made perfect panels to screw to the framework.
Step 16: Braces
After the first test flight, it was obvious that the fuselage needed some stiffening. I added 2x4 braces inside the "engine" barrel and right behind the rear seat. These braces were tied together with 1x4 hardwood strips running down the outside of the fuselage just under the cockpit openings. The idea was to create a set of stiffening bars going down both sides and tying the front too the back. These pieces were cut on the table saw to give the edges a 45 and to make a relief curve to fit the barrels.
To make this curved cut requires making a temporary fence on your table saw and running the material through at an angle. If used correctly this causes the blade to cut it's profile and you can create long concave curves. I recommend looking online for more information before trying this method. A good place to start is Fine Woodworking http://www.finewoodworking.com/how-to/video/how-t...
Step 17: Supports and Covering
Finally the tail got it's last bit of skin. Once the skin was on, the 1x4's were attached to the outside and into the new 2x4 supports hidden inside. The 1x4 stiffeners where screwed to the barrels from the outside, as well as, all along the inside. The lower wing also got some supports attached to the landing gear brackets.
Step 18: Cowling
The radiator cowl is made from the bottom of a 55 gallon plastic barrel. I got this from my work and it had already been triple washed and rinsed, so I only washed it out once more. Always be sure that you know what was in a barrel before using it. Some stuff just can't be washed out that easily or could be toxic. I used a circular saw and just rolled the barrel along the ground to cut the bottom off. These barrels came with ridges molded in, so it was super easy to follow the ridge all the way around.
Here is where I made one error. I painted the barrel end before cutting the center hole out. Oh well. To cut the center hole out I used a scrap piece of wood a little bigger than the barrel and two sheetrock screws. I put one screw through the center of the board and into the center of the barrel. This acted as a pivot. The second screw went into the scrap wood where I wanted the edge of the hole to be. This screw was just barely through the board so that only the point sticks out. Now spin the board around, if you marked the center right, it will give you a nice circle. Once I was sure it was centered, the rest was just a matter of spinning the board and slowly driving the screw in deeper till it cut a grove all the way around. Because of the unevenness of the bottom, I couldn't cut all the way through just using the point of the screw. Once Most of the grove was cut through, I went around with a utility knife and cut the rest. Leaving the board screwed through the center kept the drop attached til the end, making it easier to cut. Once done, just clean up the edge with a scraper or some sandpaper and it's ready to go.
Step 19: Engine Mounts
Up till now the fan "engine" was simply screwed right to the metal lid. This caused some flexing and bounce that had to be fixed. To stiffen everything up a disk of 1/2" plywood was cut out using a jig saw. The disk was cut just big enough to fit inside the metal lid and then another hole was cut in the wood for the ceiling fan to go through. A whole lot of little screws on the front and then it was on to the back side. On the back some scraps and 1x6 decking were stacked up and a cross piece installed. The cross piece was drilled out to hold the original ceiling fan drop rod and once this was all screwed together there was no more flexing. A little black paint and with the brass cover on it looks great.
Step 20: Stiffeners and Flaps
After the wooden stiffeners were put on the exterior, I still thought it had too much flex. I purchased some 1 1/4" steel channel from my local steel yard. These are cut to match the 2x4's that made up the main lower frame. I then drilled holes using a 1/4" steel drill at regular intervals down the center of the channels. These will be bolted and screwed to the edge of the 2x4's and will stiffen them up a lot. At this point it made sense to paint the steel and the tail pieces before they were installed.
Step 21: Problems
After a few more test flights a couple other problems showed up. The first was the tow bar, because it was a rubbermaid trailer originally, the bar was plastic and bent when I would turn the plane. To temporarily fix this I used two ratchet straps from the wheel axels to the front of the bar. This worked OK and was to be replaced by a metal bar and stiffeners, that never came to be.
The second and much more annoying problem was the rear caster wheel. Because of the angles and stress involved, the rear wheel kept rubbing under the bottom of the plane. To temporarily fix it, I simply ground down more of the wood above the wheel with an angle grinder. This worked for a while but it didn't last long. In the end the problem turned out to be the wood that the wheel was attached, it was crushing under the weight. I had to re-enforce it with screws and washers.
Step 22: Off We Go......
Although not fully finished, it is more than ready for some flying time. My little test pilot and her co-pilot have a great time zooming around the yard and doing circles in the drive way. There is no suspension, so it gets a little bouncy but I keep the throttle at minimum and just let the lawn tractor putt along. The occasional burst of speed on a straight keeps things fun and some tight turns and figure eights in the driveway are always a big hit.
Step 23: The Flyin' Lion
Here it is folks, "The Flyin' Lion". This took me about a month and a half working primarily in the evenings and on the weekends. It is quite large, almost 14 feet long and nearly 7 feet wide. I would guess, with pilot and crew it weighs in around 350+ pounds. I am super happy with how it turned out and my little pilot was also super happy to be able to "fly" around the yard.
I still have several things left to do on it, but those have to wait. Before I could totally finish this plane to my satisfaction we had to move. From one side of the country to the other, not just down the street. Even though I knew I wouldn't be able to drive it around at our new house, less than 3/4 acre, I packed it in the truck anyway. The Flying' Lion now waits to be transformed into the sickest flight simulator any 4 year old ever had. But that is for another Instructable. Stay tuned...
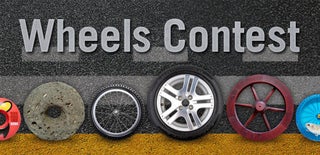
Third Prize in the
Wheels Contest