Introduction: Cast Concrete Desk Clock
Finally moving into a new place where I can have more than a shoe box-sized workshop. I decided to make this clock so I don't have to drop and or get my phone dirty to check how late I've been puttering around. Plus, being a solid chunk of concrete, I won't have to worry about it accidentally getting knocked off the shelf. Making this takes some patience, but it is doable. I may update or refine this Instructable down the line, but for now I like the more rustic look and feel of it. Enjoy!
Safety gear!! Definitely use hearing and eye protection, as well as gloves. A dust mask or better is a good idea as well. Working with the melamine and power tools, adhesive caulking, concrete and dyes can be all sorts of messy and dangerous.
Materials:
3/4" melamine
1 1/2" drywall screws
drill/ screw driver
100% silicone caulk (not white)
razors/ exacto knife
scrap of rigid foam insulation
saw (table saw; (or circular saw and 4' straight edge and clamps)
framing and/or speed square
tape measure
pencil/ fine marker
protractor
wood dowel 3/8"
clear packing tape
cork board
cement
pigment
5 gallon bucket
trowel or similar (to mix with) OR concrete or mortar mixer (I used a hand held paddle type mixer)
clock movement
inlays for hour markers (I used Euro coins)
Optional:
wet stone polisher and diamond polishing pads
concrete sealer
decorative aggregate (I used smashed black granite)
dremel rotary tool
glass fibers
compass (the geometry kind, not the "where am I?" kind)
Step 1: Design
It's always better to start with a plan; whether it's a drawing, or even just some ideas jotted down. Originally I wanted to go big and make a ~16"x16" wall mount clock, but then I thought about a few concrete table tops I have experimented with and decided it would be better to scale down to a 12"x12" and make it a self-standing desk clock. Besides, that made it more fun to come up with a design and then build the form. I figured that if I tipped the face of the clock back a few inches so it about lined up with the back end of the base, and made it thicker at the bottom, it would stand up fine. I tried playing around with some scrap plywood and 1/2"x3" strapping just to sort of double check.
I drew it up until I liked the look, sketched it on graph paper so it was proportional, then scaled it up to real size on a drawing pad. That looked good to me, so I measured everything and made a cut list for the form. For the hour markers, start with a line at the exact midpoint to make a cross between 12/6 and 3/9. Then take a protractor and mark every 30* and mark those lines, making sure they go through the center point so that the hours line up properly (e.g. 1 and 7, 2 and 8 etc). To mark the coins at an even distance from center, I could have used a compass if I could find it. Instead I drilled a screw vertically into the center point. Then I took some mason line (string etc will do) and looped one end around the screw, while wrapping the other end around a pencil. With a few minutes practice I nailed a nice circle. All these markings can go on the clock face form, but I wanted to sketch it up in detail first. This might be overkill, but my OCD tendencies were in full swing.
Step 2: Build and Prep Mold
With the design and measurements all set, I cut all the pieces out of 3/4" melamine. This gives you enough to screw into, and the white laminate coating is waterproof, which is important because if concrete cures too quickly or gets moisture sucked out by the wood/particle board, it gets weak and you'll end up with a mess. You might not have access to a nice table saw, but that's ok; I didn't either. For nice straight cuts, clamp down a straight edge on the marked melamine, such as a level, and use that as a guide for a circular or jig saw. Take your time, measure more than once before cutting, and you can get nice cuts too.
Dry fit all the pieces together as you go. As I was doing this I realized the bottom of the 12x12" form that made up the face needed to be cut at an angle to fit better with the base piece of the form. Dry fitting is a good chance to see what the finished product will be, instead of just trying to picture it based on a drawing, and allows you to change anything you want or need to before the form is all screwed together and sealed with caulk.
Once everything fits good, pre-drill for the screws (this keeps the form pieces from cracking or bowing out). I used 1-1/2" drywall screws, which worked fine. Just make sure the screws aren't so long that they poke through the form at any point but that they are long enough to grab the melamine firmly. Screw the form together. (Think ahead to make things easier - I realized the cross piece that makes the top of the base (that is missing from the first picture in this step) would have been in the way of setting in the inlays of coins and shamrock, so I left it for later).
Seal all joints with 100% silicone caulk. This keeps the water in the concrete from bleeding out, which could warp the form and weaken the end product. It also gives a subtle rounding to the finished edges once you pop it out of the mold. Run a bead of caulking down one or two of the joints at a time to make sure you can tool them before they firm up too much.
I tool them with an empty pen tube that I cut at an angle (kind of like cutting the tip off the caulking tube). I supposed you could use a gloved finger, but the modified pen gives the sealed edges a nice uniform shape and size. Start in one corner of a joint and drag the fancy new joint tool at an angle, trying to get all the way down the joint in one motion before you wipe off the excess. NOTE: Try to find black silicone caulking - it shows up better on the white melamine so you leave nice clean joints and don't leave any smeared on the form. The best I found when I bought materials was an almond color, which was alright.
After tooling, there will be three lines of caulk on each joint - the middle is the joint you want to leave and the other two need to be cleaned up. A nice clean razor blade works well.
Hold the razor so you can slide it along the form surface at a sharp angle, almost laying flat. Use one finger as a guide to keep a constant distance on the piece of form you aren't yet scraping. NOTE: some (all?) razors have one side that slides along the melamine easier; you want this side down against the form to make things neater. The best way to clean the caulking off the razor is to slice it through a scrap of rigid foam insulation if you have any. You should be able to see what I mean from the blue foam in the back ground of a couple of these pictures hopefully.
Cover any non-coated edges of the form with clear packing tape to seal the entire form.
After the form was built and the caulk had over night to firm up, I marked the clock face form for the inlays. NOTE: I should have done this before building the form - getting my framing square or any long straight edge into the completed form was impossible; I had to carefully re-measure everything out in the cramped form and spend way too much time drawing everything out with a small protractor. Again, it worked out with a bit of patience, but save yourself the aggravation and mark this ahead of time.
Draw the lines for the hour markers - in this case I used Irish Euro coins (50-cent pieces for 12, 3, 6, and 9; with 10-cent pieces for the rest). I spent the time to trace exactly where each coin would go to satisfy my occasional OCD. Then drill into the form halfway through in the center for a wood dowel (I used 3/8"). This will leave a channel for the clock mechanism to run through. Drilling into the face-form just made it more sturdy so I didn't have to glue the dowel directly to the form and have it easily knocked off. Don't forget to give the dowel a quick wrap with packing tape to seal it from the moisture. For the shamrock recess, I used an exacto knife to cut out the shape from cork board. The cork was a nice depth for the effect I wanted, and easy to cut. Cover it in the clear packing tape to seal it, then spread a very thin layer of caulk on the face down side to glue it to the form, and fit it over the dowel. Do the same with a thin film of caulk on each of the coins (I used a razor to spread it, and cleaned up excess like I did with sealing the form joints). Let these inlays set over night so they don't shift around when you pour the concrete. If the cork curls, leave a book or other weight on it over night.
At this point you can put in any decorative aggregate if you want and are going to grind/polish the surface at all. I had a spare tile that was a nice black granite, so I smashed it up and sprinkled some in.
Step 3: Mix and Cast
Get everything you need for mixing ready ahead of time. I used a countertop quickrete mix because the thinnest part of this clock is smaller than the crushed stone aggregate in normal bagged concrete mix. I also used some green precast concrete pigment - I took an educated guess on the amount (based on the fact that one packet of powdered pigment is pre-measured for one bag of concrete mix and the approx weight of mix I was using) and mixed it dry with the concrete mix and a small handful of glass fibers (for strength) before adding any water. Add water and pigment as you go, but you don't want a thin/watery concrete. The drier the mix you use is, the stronger it will be in the end. Basically just follow the instructions on whatever bag of mix you use and you should be just fine. I used a drill/auger type mixer and mixed in a 5 gallon bucket you can get at any hardware store. But you could mix in the bucket with a square trowel, garden trowel, or mixing spoon if you want, just make sure to mix everything thoroughly, let it sit for 2-3 minutes, and then give it another good mixing.
Once the mix is at the right color and consistency, place it in the mold by hand. ...GLOVED hand! Work it into the corners and around the inlays. If you have a palm sander or similar, you can vibrate around the form to get any air bubbles out. Or you can lightly rap around the form with a small hammer or something.
Use a straight scrap piece of form to screed the concrete by making a sawing motion across the top of the form to give an even surface.
Step 4: Cure and De-mold
After cleaning the excess concrete off the form, cover the form with some plastic, or even a trash bag, making sure the plastic does not rest on the concrete - it will make the surface wavy and uneven. Leave it covered up to cure for a few days - this holds the moisture in longer, which also makes the end product stronger and helps prevent any hairline surface cracks.
After 4 days, I stripped the mold and GENTLY popped the (mostly) cured concrete from the form. Then I let it cure for an additional day, mainly because I didn't have time that day to grind and polish it.
Never pry directly against the concrete. It will feel hard, but it is still easy to scratch or chip with tools. Again, take your time and think it through. I used a flathead screwdriver to pry only between pieces of the form. If you try to bend or pull the dowel out, there is a real good chance of chipping or cracking the piece. Instead, drill down through it all the way. Start with a small drill bit and work up to a bigger bit, then you should be able to squeeze it and pull it out with pliers. To get the piece off the last bit of form, which was the face form with the inlays, I gently hammered the screwdriver into the uncoated edge of the form, about in the middle. This wedged the melamine apart enough to pop the concrete loose.
Step 5: Polish
I used a variable speed wet polisher and diamond polishing pads, which is completely an optional step. I wanted to try to bring out some of the black granite I sprinkled into the form before pouring (along with the natural small stone aggregate in the concrete mix) by grinding down the finished concrete. There are plenty of youtube videos on grinding and polishing that can show you how much better than I can, especially the Cheng/Concrete Exchange videos. Besides, it was impossible to take any pictures myself while I was polishing. Follow the video if you decide to do any polishing, it's worth taking more time and being patient again. Bringing out the aggregates by grinding and polishing made a nice contrast in color to the plain green shamrock recess, I think.
When I was done and the piece was dry, I fit the clock mechanism on and realized it was too short to get all the way through the concrete! Good thing I have a dremel tool and was able to notch out a small square for the mechanism to sit in. You can buy the mechanism at a hobby/craft or hardware store (although I took mine from a wooden clock my Grandfather made years ago, since it matched the Euro coins nicely).
Note that the streaks on the back of the piece are mainly from the dusty process of cutting out the recess for the clock mechanism to sit in; should have wiped it all down to give a better view I guess.
Step 6: Clean Up and Install the Mechanism
I used a small rubbing stone to ease the back edges of the concrete. You can use a piece of brick, a stone, or a file. Basically you just want to file/rub down the back corners and edges because they are jagged after coming out of the form. They can easily chip off or cut you. After everything is set, flush the piece down with plenty of clean water and a rag. If you want to seal it, this would be the time, as per the product instructions. But this is staying inside and I like the feel of the concrete as it is; first attempt at polishing and all. Down the road, or if I make another similar piece, I might fill any pin holes with a cement and pigment "slurry" and seal it for a more "finished" appearance. But as this is a piece for myself, and I like it like this, it stays :-)
The clock hardware/mechanism (clock movement) is simple to install, and should come with instructions. But basically fit the threaded tube through the clock face from the back, screw on the nut, slip the clock hands into place, and put the final nut/cap on.
If you want anything clarified or have questions, or if I overlooked describing any step (I've been playing with concrete for years so I might have, sorry), please let me know and I'll help if I can.
Thanks, and I hope you use this as some inspiration to make something up yourself!
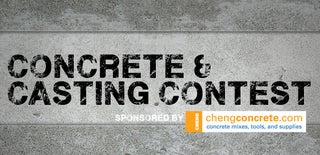
Participated in the
Concrete and Casting Contest