Introduction: Cast an Aluminum Bowl!
This Instructable will cover the general process I followed to cast an aluminum (or aluminium) bowl, a replica of a glass kitchen bowl. This is the story of scrap aluminum, melted to a complete liquid, and remade into something awesomely new. My guide will not go into great detail as to the construction of the furnace, the molding flasks, or the crucible tools. See more about these in the Requisites section.
Before we begin, I'd like to throw in the necessary word on safety. Safety isn't always fun or exciting, but the hospital is less so. Don't pour molten aluminum or slag onto concrete as this will create violent (really - these are forceful) exlosions that will propel molten or just-solidified chunks of aluminum many yards into the air and sideways. I know from personal experience. Also, wear safety glasses, boots, and jeans. These are great for those insignificant but annoying cinders that make little burns. Alright - enough "safety" talk, let's get melting!
Step 1: Requisites
If I were to explain everything I did to make the aluminum bowl, this Instructable would be 70 pages long. Thus, is is prudent to list off some things that you will need as basics to this casting project. Here we go:
- The Furnace: Arguably the most important part, save for the aluminum to melt, the furnace will melt your metal and hold the fuel's heat in. This can be (with lower performance) as simple as a paint can with a hole near the bottom of the side to blow air into through a pipe. Mine, however, is party helium tank cut at the top, lined with 2" of a refractory cement made of fire clay and sand. It has a 2" steel pipe coming in near the bottom of the side to supply extra air to the combustion of charcoal in the tank. The cut-off lid has a hole in the top for the exhaust. Find more info about this at:
- The greensand: Another important part of the casting process, this is the material which you will shape into your mold to pour the metal into. Mine is a 12:100 ratio mix of powdered cat litter and sifted play sand, by weight, moistened a small amount. Find more info on the greensand at:
- The crucible and tools: These are what you melt and handle the aluminum with. The crucible can be as simple as an empty camping size propane tank with the top cut off, but I have had some bad experiences with this type of crucible becoming holey and dropping aluminum into the furnace. I used a clay-graphite crucible from http://www.budgetcastingsupply.com/. You will also need tools to handle the crucible with. If you are using a metal can like the propane cylinder, a pair of long pliers will work fine. If you use a real crucible, I recommend building 2 pairs of tongs, one to lift with and one to pour with, from 1/4" steel stock. This is what I did, with the assistance of a friend.
- The flasks: The containment for the sand, the cope (upper) and drag (lower) molding flask boxes are used to provide firm walls to ram the sand into and against. I made mine as 5"x9x"x9" plywood boxes (no top or bottom) with holes in blocks on the sides for dowels to slide into. These dowels provide alignment to make sure that the sand molds line up right each time. This site has some decent info on building your own flasks: http://www.penguinslab.com/furnace4.htm
Step 2: Make the Molds I
Phew! I hope those requisites weren't too scary! The finished product and the limitless possibilites for future projects are well worth the effort, though! :)
Now that you have a small foundry's worth of equipment in your backyard, it's time to get some results! Take your template bowl, the one that you will be making a replica of, and place it face down in the upper flask (the cope), as the cope sits right-side up on a smooth board. The Microsoft Paint illustration in the images for this step helps visualize this setup. After sprinkling it with some baby powder for better release and less sticking, begin to pile non-clumped sand over the bowl. As you go, press it down firmly with your hands. Once you get to the top of the cope, pack on more sand and then ram it down as hard as you can with a 2x4 or some similar piece of wood. Then, take a long board and scrape the excess sand off the top so that it is flat. Yay! You have finished your first half of the mold.
For the drag, invert the cope so it is upside down and attach the drag using the alignment pins. Thoroughly sprinkle the exposed sand with baby powder and also powder the bowl's inside surface, but don't dump it so much that it makes piles. This will help the two halves and the bowl to release cleanly without breaking the sand. Next, pack the sand in like you did with the cope. Pay special attention to packing the sand firmly into the inside of the bowl, as you don't want loose sand with lots of gaps that the molten metal will flow into, making a rough texture. When you reach the top, repeat the same process as you did with the cope, ramming and then scraping smooth. Your mold is now packed!
Step 3: Make the Molds II
After you finish the previous step, carefully place the mold assembly right-side up and remove the cope from the drag. The bowl will stick to one of the two halves; being light and gentle, remove it and set it aside to be washed before being eaten out of. Your molds should now look like the picture above - nice and spherical!
Now is the time to cut the sprue, or the hole that the molten aluminum will be poured into. Take a thin-wall pipe about 1-2" in diameter and press down firmly into the apex of the concave cope mold. This will cut out a nice hole, which can be tapped from the pipe to remove it. Your cope will now look like the second picture.
If we pour molten metal into the mold (assembled of course) now, it might fill the bowl cavity, or it might not. There will be air that has to escape to somewhere when the aluminum tries to displace it. To curb this potential problem, take a thin rod or maybe even a thick wire and poke some holes clear through the concave cope section. These are called risers and will allow air to escape easily. The mold will look like the third picture; you probably don't need 8 risers like I have if you use that big of a rod.
Hang in there - your cope and drag are nearly ready! Lastly, set the cope upright and use a spoon to carve a slight funnel leading into the sprue hole, on the top side of the flask. This will make pouring the molten metal much easier. After blowing out any sand particles that remain, assemble the two flasks slowly and carefully, using the alignment pegs to match them up. You are ready to pour!
Step 4: Melt the Helpless Aluminum!
Bwa ha ha ha ha!
All evil scientisty stuff aside, light up your furnace. I used charcoal as fuel; you may have a propane furnace. Next, look at your bowl template and judge how full you should fill your crucible with aluminum in order to fill the mold. Always go on the side of extra. Once you have done this, put in the crucible and aluminum. When the aluminum is in the crucible ready to be melted, turn on your air source. I found that a ShopVac worked really well for this. Put on the lid (actually do this before you turn on the air and create a superjet of flame) and sit back for a few minutes. After you've relaxed a little, check on the fuel and see if the aluminum is melting. Refill and refuel until you have enough aluminum melted in the crucible. Next, (this is important), after all the aluminum scraps/ingots have melted, keep the furnace on for 3-4 extra minutes. You needn't refuel or refill, but you want the aluminum to be really hot and runny so that it will fill the relatively thin walls of the bowl mold. Once you have done this, remove the crucible and proceed to the next step.
Step 5: Skim and Pour
With the crucible on a heat-proof surface, take a flat metal rod and skim off the slag and crud on top of the molten aluminum. DON'T place this dross on concrete! I did this once in the video and was greeted with explosions of 1200F metal! Next, pour 1 tbsp. each of washing soda and table salt onto the liquid metal. These act as degassing and fluxing agents, respectively, removing bubbles and slag from the melt. Stir this around and then remove excess. Also be sure to skim off the created dross again with the flat rod. When you have done this, take a second (but only a second) to admire your awesomely liquid metal!
After you stand in awe of the shiny molten aluminum, grab the crucible with pouring tongs and take it over the the assembled cope and drag molding flasks. With one smooth motion, rotate the crucible to pour the molten aluminum into the sprue. Continue to pour at a medium pace until the metal flows up the sprue to be level with the flask top. Next, step away from the mold and put the crucible back in the furnace, with the lid on, to prevent temperature shock. Leave the mold undisturbed for an hour at least. You wouldn't want your hard work to break or come flowing out of the mold as you open it!
Step 6: Break and Clean
Once you have waited for an hour, undo the cope and drag. Look at how it turned out! My bowl made a cool ring of aluminum in the cope (this is actually the rim of the bowl showing out of the sand). Break the bowl and the flasks out of the greensand and set the sand aside for reuse. You will need to crush it again and possibly add more water before reuse.
Take your bowl over to the sink and wash it off. A light scrubbing brush works, too. Once it is clean of sand, move on to the next step, or use the bowl as a weird sci-fi hat with risers poking out of the bowl surface (picture 2). A cursory inspection reveals that the bowl turned out amazingly well! This was also my first try at greensand casting, so even better!
Step 7: Finishing Touches
Using a hacksaw, cut off the sprue and risers. These will be a lot of work to remove, but the bowl is amazing when finished, so get to it!
Finally! Victory over that annoylingly big sprue (picture 3)! After you have it rough-cut (picture 1,2,3), take a file, clamp the bowl to a worksurface, and put some elbow grease into filing that thing (picture 4)! File off cutting imperfections as well as stray bumps and sharp edges.
After this is done, sandpaper is an optional extra. I chose to keep the cast look, so I skipped the sandpaper. However, I did opt to use a heavy-duty wire brush to remove discoloration and give the entire bowl an amazing shine. Once again, the more work you put into brushing, the better it will look.
Step 8: Admire!
Sit back and admire your handiwork! If you got this far (I hope you did), then you have definitely earned it! You can do lots of things with this bowl, like giving it as a gift, putting it in a display case, using it for fruit (most likely not avacados and bananas in the same bowl), or putting candies in it. Wash it thoroughly before using it for food, though. My bowl also functions really well as a bell. Rest it in your palm on its bottom and flick the side. Ding! I would say that this casting project was an astounding success!
Note: This was my first time doing a greensand aluminum casting. Without fancy sand, tools, or knowledge, I got amazing results. If I did this on my first try, just imagine what you can do! Even if it seems hard at first, it will be an extraordinary learning experience and will most likely produce shining results. Give it a try!
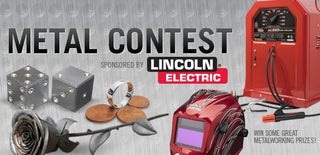
Runner Up in the
Metal Contest