Introduction: Casting With Molds Made With Papercraft Models
You dont't have to use paper. Cardboard, plastic sheets, even metal would work.
Any cast starts with a mold. You need something to pour your material into, be it concrete, plaster, resin, wax, whatever. You can user everyday objects like bowls, packaging or make molds from existing objects.
But what if you want cast something completely different? Something you can't make casts of?
Paper to the rescue. Everyone has some lying around, has scissors and glue. And paper can take pretty much any form you want.
It does have it's limitations though. It's not waterproof and will lose it's strength when getting wet. So before you can use it as a mold, you'll have to make it waterproof. I'll just use spraypaint. Also it's strength is limited. So making huge casts doesn't work. The "Venus de Milo" is 36cm (14 inch) high - and it worked out just fine.
Paper is great to work with, it's easy to cut, fold and glue. But if you want to make more than one cast of your mold you might want to try sheets of plastic. While it is a lot harder to work with it is reusable. You can make many casts with the same mold over and over.
Here are two different routes I took
Step 1: The "gothic" Vase
This is the last one I made and it's the one I documented best.
It's a cast made from David Huffmans "Hexagonal column with cusps". I took the blueprint from the following paper by Erik and Martin Demain and Duks Koschitz.
There is a tutorial on youtube on how to fold it:
Attachments
Step 2: Printing and Folding David Huffmans Vase
The paper I mentioned before includes the template seen above. You'll need to print it out the size you want your vase to be. I used A4 the resulting vase will be 13 cm (5 inches) high. If you want a bigger one adjust your print size.
I knew that I wanted to try out many different materials, so I used a sheet of translucent plastic I got from my local craft department. I then scored the lines using a tool to pinch holes. Just make sure you don't punch through the plastic. If you do, you can just cover the hole with scotch-tape.
Now comes the tricky part, folding it. If you have trouble here, take a look at the video in the previous step.
Attachments
Step 3: Making It Watertight
3D-modelers know the term watertight. On the screen it's just a virtual term. This is real life. It actually has to be watertight or else whatever you will pour into the mold will splatter all over your workplace.
Start with the back. tape the two sides together.
Then trace the resulting top and bottom and cut out the parts. Make sure you leave a hole in the top. We need an opening to pour the casting material into.
I used a glue-gun to seal the top and tape for the bottom.
The cardboard I used worked surprisingly well. It does get soaked but it strong enough to hold it's shape.
Step 4: Prepare the Casting Material
The first material I used was Acrystal (in german). A water based mineral resin. I like it because it doesn't smell. You can actually use it indoor. It cures reasonably fast making it ideal for roto-casting.
After it has cured it is not totally waterproof. More like terracotta. It holds liquids and won't dissolve, but over time water gets soaked up. I just pour in a layer of paint at the end. that seals it off.
I successfully made casts with plaster and resin-plaster.
Concrete should work if you build a second inner form. Rotation-casting doesn't work with concrete. After all, that what the concrete mixers do to prevent the concrete from getting hard. Maybe there is a form of concrete that can be roto-casted. Does anyone know?
The images above show what I've done. I wanted the cast to have a color, so I mixed the mineral part of the resin with petrol colored pigments. The pigments you'd use to make your own acrylic paint for example.
Shake to get an even distribution of the mineral and pigments.
Add the liquid part of the resin and stir until all is well mixed.
Pour into the mold.
Step 5: Rotation Casting
Now roll and rock ;) your form. the resind has to flow into all parts of your mold. Just make sure it doesn't drip out of the hole on the top. If you want to make sure that it doesn't cover it up with tape.
It will take a few minutes. Don't be hasty with your movements, the resin will become less and less fluid and will stop to move after about 5-10 minutes.
Yeah! Almost done...
The wall thickness of your vase will be too thin by now. So you will have to repeat this step a few times to build up a stable wall. I used a second colored layer. Then a layer where I mixed in sand as a filler. and a fourth plain layer.
Step 6: Cleaning Up
Not your workspace, the vase. ;) Removing the cast from the mold is easy. Only the top and bottom made of cardboard stick to it. The can be removed with water.
I left mine out overnight to cure and dry.
The next day I applied the inner layer of paint to seal it.
After the paint dried I used rasps and files to trim the hole at the top.
Step 7: The First Vase - Done
This was part one. It actually took me longer to take the pictures and write this up, than to make the vase. So while it might seem a little intimidating at first, believe me - it's not that hard. And you'll be amazed how a flat sheet can turn into such a complex vase.
On to the next one - Venus:
Step 8: Start - Venus De Milo
Some of you have seen my first instructables. It explains how you can turn a virtual 3D-model into a real paper model. The deer is the example it took back then, check it out.
I used a model of the Venus de Milo this time using the same technique as with the deer. So again, if you want to see how the cast ist made, look at how I made the deer. The only difference is, that I spray-painted the paper model to make the paper watertight.
Then I used the same resin as with the "gothic" vase in the steps before.
Step 9: Birth of a Venus
I didn't get the model really watertight. So I made quite a mess with drops of resin coming out all over the model. Need to be more careful the next time.
After it cured I started to peel back the paper on her back. It came off surprisingly easy. The paper mold gets destroyed though. I don't think there is a way to save it.
A great feeling to see it emerge from the mold.
Step 10: Failure
Whenever you experiment or you are trying something new - be prepared to fail.
Not all models make good molds. Some are just too delicate as the one above.
And yes, sometimes the color is just too tacky. ;)
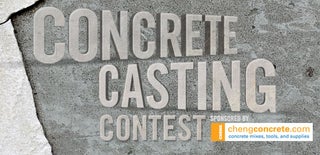
First Prize in the
Concrete & Casting Contest
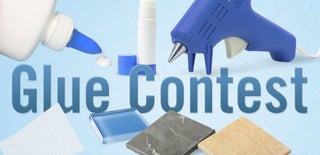
Second Prize in the
Glue Contest
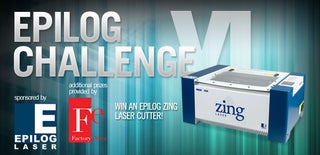
Participated in the
Epilog Challenge VI