Introduction: Chibikart: Rapid-Prototyping a Subminiature Electric Go-Kart Using Digital Fabrication and Hobby Components
Chibikart! is a very small yet powerful and maneuverable 2WD electric go-kart that you can build using off-the-shelf industrial and hobby components and digitally fabricated frame parts. Using modern lithium ion batteries and brushless permanent-magnet electric motors, Chibikart can accelerate its diminutive 34" x 26" frame with you attached to speeds of 22 miles per hour.
The design is intended to be extensible according to your own requirements, using an industrial slotted framing system typically used to construct prototype machinery called 80/20. Precision-cut aluminum frame parts are intended for fabrication via abrasive waterjet machining services and can be assembled like a puzzle. Many parts can be sourced from your local hardware store or home improvement store. Some fabrication using common garage and shop tools such as drill presses, hacksaws, bench vises, and belt sanders is required, but there are no parts that require conventional machining such as milling or turning!
The final product is intended to highlight the level of sophistication available to modern makers and builders who may not necessarily have access to a conventional machine shop or collective such as a hacker / makerspace. Especially for students and minors, access to machine tools may be difficult or nearly impossible in our age of overabundant safety and caution. It is designed to show that the world of amateur and hobby engineering extends far beyond Home Depot and hardware stores - something which is generally unknown to many people who may be interested in pursuing engineering as a career, or aiming to explore it as a hobby.
This build will focus extensively on purchasing parts through online industrial supplier catalogs such as McMaster-Carr, specialty & hobby suppliers like Surplus Center, HobbyKing, and digital fabrication houses such as Big Blue Saw. Having access to these electronic resources, which really only became possible in the past few years, will facilitate students and hobbyists in producing higher quality and more awesome projects.
The resources alone, in my opinion, are all that most readers of this Instructable will need - it is often the case that many people who want to build things and know generally the approach they need, cannot proceed because of a lack of proper resources, whether it be tools or materials. In this case, this Instructable is perhaps more useful as another resource and technique guide, similar to my previous writeups on selecting electric vehicle power systems and building hub motors.
Step 1: History of the First Chibikart and Why I'm Building Another One
Chibikart is the latest in a long lineage of vehicular creations that I have built during the past few years, while I was an undergraduate in Mechanical Engineering at MIT (Incidentally, I'm still at MIT, now encouraging undergraduates to build silly vehicles as part of my Master's thesis).
I first took interest in electric vehicles in 2007 when I built Snuffles the First, a whimsically named but extremely overpowered electric scooter - while I intended to use it as a campus cruising appliance, it was better off as a drag racer. Incidentally, Snuffles caused me to write my first Instructables guide on how to build small EVs. My focus in alot of these vehicles was using a custom designed miniature hub motor, for which I also wrote up a guide, to make even more compact vehicles and motorize things which previously were seemingly unmotorizable (or should not be motorized). Long story short, I ended up with several excess 100mm motor parts after testing the waters of production.
CHIBIKART 1
Chibikart 1 was built on a whim, to accomplish nothing in particular. In fact, the real story of the first Chibikart was to build a go-kart which fit into the front half of tinyKart, a similar go-kart project spearheaded by a friend of mine (and another member of the MIT chapter of the Collegiate Silly Vehicle Team), Shane Colton. Since I had pledged to not build another non-hub-motor vehicle before using up my sourced production parts, the choice of drivetrain was obvious.
Chibikart was a pretty big hit, I think, both locally and on the Internets, where for some reason it was hailed as the second coming of MarioKart. In the shop, we would occasionally take it for a ride around the conveniently circular layout of the building when we were at a mental block or in need of amusement.
BUILDING THINGS JUST BECAUSE
I believe that building just for the experience and adventure is a fully legitimate reason to embark on projects. Building personal projects for your own amusement is often dismissed by people as wasting time, which to me is a very disappointing attitude. Especially in engineering academia, there is a seemingly subconscious pressure to always be able to justify why something you are building is useful, optimized, commercializable, groundbreaking, etc.
I contend that no matter what the project, you inevitably pick up experience or new knowledge with each build which contributes to making even better work in the future - for yourself or otherwise. Immersing yourself in project work encourages thinking of creative solutions for problems when they inevitably arise - testing your critical thinking and analysis skills. By picking your own projects, you also invest yourself in them - there's nobody to disappoint or set a bar for you to barely clear, unlike directed 'class projects' or similar. You're only in it for personal gain, and that is a great motivator for many people.
For this reason, this new Chibikart actually does not bring anything that new to the table. All the methods, parts, vendors, and other resources described herein are in common use by mechanical project builders everywhere. Instead of linkdumping, though, I will present them in a format which introduces them as needed and in...mostly...logical order.
A NEW CHIBIKART FOR THE PEOPLE
One of the trends in Internet commentary regarding Chibikart 1 was that it was nearly impossible for anyone else who did not have extensive machinery access to build. Yes, I'm actually bothering to gauge what the Internet is saying in this case, because it was an insightful look into the attitudes of the "techie" and "gadget" crowd - many of the sites that Chibikart made it onto are populated by reasonably technical people, but in a direction which is distinctively not "Maker" centered.
These are people who may have some knowledge the latest processors and chipsets Apple is using in the iPad, or may have some glimpses of the engineering processes involve therein. Some of the sites even post pretty engineering and science heavy content at times, like about the latest 3D printer or swarming quadrotor death-cloud. But what they haven't done is picked up tools and made something. They're not stupid - just they have not been exposed as much to the gritty underbelly of engineering, the machines and people who eventually make iPads.
But the statement about Chibikart 1? Totally true. Those hub motors are nice custom-machined assemblies that have been through 4 or 5 different revisions, and even if I just handed someone all the parts and drawings, they would have to either get access to machinery, learn how to use it, then stumble through much of the same pitfalls as I did just to get one working motor. Or they can spend $3500+ to hire a machinist or shop to make them, and that's just the mechanical parts. A123Systems will definitely not sell you one of those custom 33v lithium ion batteries I used.
THE RISE OF DIGITAL FABRICATION
But say I took away the hub motors and sweet custom battery and replaced it with hobby model airplane motors and commercial Li-ion packs. Then all of a sudden Chibikart becomes very much accessible indeed, the reason being that it actually uses very few traditionally machined components.
"Digital fabrication" is one of those neologisms that has come from the weird design space intersection between engineers and futurists. Along with similar terms like "personal fabrication", it symbolizes the ability for designers to create products on-demand and bypassing the traditional system of toolmaking, assembly lines, design cycles, etc. to arrive upon a working, perhaps not production-ready product in short order. Personal Fabrication is the more specific form that defines "designer" as anyone who wants a custom product or thing. Basically, it's instant design gratification available to anyone. Parts are made in immediately useful or near-net-shape forms by machines which can be reconfigured to make many different parts in short order.
The most common processes which fall under this label are computerized 2D processes - laser cutting and waterjetting - and 3D processes which require minimal operator intervention, such as 3D printing and scanning. Traditional multiaxis CNC machining is usually not considered, because it still takes a trained machinist with years of experience to set up a CNC job quickly and effectively. But the 2D processes have been well-optimized to work for anyone - laser cutters are generally plug and play and accept many 2D graphics formats, waterjetting is much the same, and 3D printing is just like 2D printing (if you don't insist on building your own).
In the past few years, people have taken formerly high priced premium services like laser cutting, waterjetting, and 3D printing to the market. Nowadays, there exist services where you literally send your 3D model to and it comes back a week or two later as a finished thing. Examples of these services includes Shapeways and i.Materialise 3d printing (i.M being the somewhat more upmarket version), and Big Blue Saw for waterjetting and laser cutting. All of these places will give you instant quotes on the spot based on your uploaded model. Are we in the future or what?
You can do alot with just 2D parts, actually. They can be arranged in creative ways, usually involving some kind of wooden dinosaur model kind of right-angle joints, to create functional mechanical structures. They may not have the fit and polish of a new car, but that's not what we're after here.
THE FALLING COST OF ELECTRIC VEHICLE PARTS
Even five years prior, in 2007, building your own custom electric vehicle was still quite difficult. Small ("personal") vehicles especially; which seems strange until you consider that electric forklifts and golf karts and other large rideables have been around for years, and that is where you scrapped parts out of if you were putting together an electric car or bicycle!
During the past few years, the advent of dedicated small-EV parts companies and businesses dealing in low-cost motors, controllers, and batteries has made it easier than ever to build your own small rideable contraption. Part of the reason is the meteoric rise of electric model aircraft component power and energy density at the same time that prices have fallen nearly an order of magnitude - the nitty gritty details of this are covered in my "Scooter power system" instructable.
THE BOTTOM LINE
Given the availabilty of 2D precision-cut metal parts and inexpensive repurposable parts that can be used for vehicles, I thought it was the right time to produce a design which is substantially more accessible, but in roughly the same form factor, as Chibikart 1. The build itself would be intended to be nothing too spectacular, but the concepts and resources presented in the process of would be of benefit to those seeking to build their own vehicles, or mechanical projects, but who may not confident in their knowledge or just need additional places to get parts. This vehicle would have no "unobtanium", or Unobtaining Machines, as I call it, used in the build, and all parts must be sourceable from commercial vendors with an online ordering portal or are very common IRL (e.g. hardware store or hobby shop).
Build one and challenge me.
Step 2: Before You Build - the Rules of the Game
I strongly recommend reading through the entire Instructable first before doing anything - that way, you know what's coming and roughly how it was done. Anyways,
THE RULES OF CHIBIKART
1. Chibikart is not supposed to be "easy".
If you really are just starting out in engineering and building mechanical projects, then perhaps it is wise to read through this Instructable just to glean techniques and resources. Even though I have tried to make this process as painless as possible, it assumes a reasonable amount of garage-shop proficiency and spatial aptitude. I am not writing a "How to use a drill press" guide, and some of the fabrication techniques may in fact be dangerous if you have not used a drill press before. Perhaps a small robot is a better first project, or one of the many other novice-friendly projects on Instructables.
If you are a parent, please do not build such a contraption for your 7 year old child thinking it would be totally cute. This go-kart, while small and seemingly innocuous, is capable of injurious speeds in the right conditions.
2. Chibikart is not cheap
This build will run over $1000 USD if you purchase everything as prescribed. This is a fact of the design, and the methods used in its construction. The biggest ticket items are, in rough order:
- Waterjet-cut frame pieces, about $420
- Battery and charger, about $400
- Chassis materials and hardware, about $250
- Motors and drivetrain parts, about $100
- Electricals and wiring, about $100
Why does it sound like I'm discouraging people from building these? Because you can do so much better. Again I emphasize the guide- and reference-like nature of this Instructable despite its step-by-step construction of a finished project - building the next Chibikart is nice, but for the same amount of money and time, you can exercise your design creativity and make something that is truly yours.
3. Chibikart is not amenable to suggestions for improvement
I'm fully aware that there are many things I could have designed or made another way, or assembly steps reordered for better consistency. I also could have used a different motor or a better seating posture, or less expensive batteries. Many potential improvements upon the design exist and have been considered, but they will not be executed.
Why?
That's your job!
TOOLS YOU MIGHT NEED
I started this project with a limitation of tool usage in mind. Using the tools I had access to as a high schooler in my parents' garage, I thought of ways to work around common fabrication issues - like boring a hole to precise size to pass a shaft through - using hand tools and what I would have done if I didn't have an Unobtaining Machine in the shop. The following tools were used in this build:
- Common 10" 5-speed drill press
- Set of metric and imperial wrenches, adjustable wrenches
- Hacksaw, flat and round metal files, and a rubber mallet
- Several fractional drills (commonly found) and numbered (wire gauge) drills, which can be found at hardware stores
- #4-40 and 1/4"-20 hand taps and wrenches
- Small 36 x 4 belt sander
- DeWalt 18v XRP 2-speed cordless drill
- A nice set of Allen (hex) wrenches in common fractional sizes
- 6" bench vise, 4" drill press vise
- Digital temperature-controlled 80W soldering station
- Combination wire crimper-stripper pliers
- Manual wire strippers
- Multitemperature heat gun
- Some type of electric hand drill with a 1/2" chuck (Basic ones start at < $50 if you don't have one!)
- An adjustable wrench and full set of hex wrenches
- Flat and round files
- #4-40 and 1/4"-20 taps and handle - get these for approx. $20 at a hardware store
- Rubber mallet or deadblow hammer - metal hammers are not recommended
- The exact sizes of drill bits that will be called upon in the instructions
- Plug-in soldering iron of 40W or above
- Manual wire strippers
- Wire crimping pliers
- A lighter to use a heat gun
With motivation-backed creativity, though, I'm sure you could improvise alot of the steps with tools on hand. The process is up to you.
TIME COMMITMENT
Chibikart has been designed to be assembled quickly, but some of the fabrication steps can still take some time. You can expect to take about 4-5 hours to make all the independent subassemblies, 2 hours putting together the frame, and 5-6 hours assembling the electrical components. This is only if you have 100% of the parts, including the random hardware store odds and ends, ready to go.
Lead time for orders is another separate issue. While McMaster generally ships within 3 days to any location and Amazon will vary depending on vendor, Hobbyking, Surplus Center, BBS have at least 1.5 week lead times. If you choose regular airmail from Hobbyking, it could take a month to get your parts - EMS is recommended, even though it will be expensive.
Step 3: Gather Your Parts - 2D Cut Files, Bills of Materials.
BIG BLUE SAW
The most important and first on the list, since they will provide you with the appropriately-designed metal plate parts which fit together into a Chibikart! There are 3 files which I have included at the bottom in a compressed folder:
- 0.250" 6061 Aluminum panel
- 0.125" 6061 Aluminum panel
- 0.125" PETG / Polycarbonate panel
You can also make it from wood. If you do so, I recommend a non-grained wood fiber product like MDF or Hardboard - they are less likely to splinter and crack at the surface.
MCMASTER-CARR
McMaster-Carr is one of the largest industrial supply houses in the world, and the best part about them is that they deal directly with you. Their site has been hailed as a great example of link-rich navigation in the past (when it was a literal wall of text) and the new interface for finding common part with tons of variations (e.g. nuts) is even better.
There's so many things to get from McMaster that I've attached the BOM as a text file. Right now, there's not an easy way to just drag-and-drop that into an order, so you will have to do some copy-paste legwork.
HOBBYKING
HobbyKing is pretty much the premier supplier of East Asia sourced R/C model parts these days. They have many lines of motors, batteries, connectors, wires, and accessories. What we will be needing from them is the drive motors and some wiring products. There is also an extensive BOM from Hobbyking, so I've also included it as a text file.
SURPLUS CENTER
If you ever need parts for your tractor or semi, Surplus Center is the place to go. They are a surplus parts and equipment vendor - as such, if you ever need things like large DC/AC motors, giant sprockets, whole engines, etc. they should be at the top of your list too.
I purchased the centerpiece of Chibikart - a Troy-Bilt lawn mower seat, from Surplus Center. It is part number 1-3289.
I also purchased the motor sprockets and a small amount of #25 drive chain. The motor sprockets are P/N 1-2742-12-A QTY 2, and the #25 chain is 1-1163-25 QTY 1. You will also need at least two #25 master links: 1-1087-25.
TNC SCOOTERS
Along with many other similarly named scooter parts vendors such as Monster Scooter Parts and the aptly-named Electric Scooter Parts, TNC Scooters is a vendor of import-grade shady small vehicle parts. You can build most of a vehicle just using those vendors. However, TNC is the least expensive source of a very rare small vehicle part: the throttle pedal. We need this - their part number THR-101124.
eBay - BOBZHANGXU and his magic e-bike controllers
Buy 2 of these 24v 250W controllers and do not ask questions.
As you can probably see by now, there is no one magic dealer for all small vehicle parts. This may very well be my cue to corner the market, but before I can get all my stock in, you will have to shop around. Chibikart's controllers are nicknamed "Jasontrollers" - pretty much because they have no official name, nor an official vendor.
This nice and very helpful dude (not kidding - I've done business with him off-eBay several times) is based in Guangdong, China and is the only vendor of a small vehicle-optimized sensorless brushless motor controller that doesn't suck. Hopefully there will be better things coming down the pipes here at MIT to be publicly released soon, but in the mean time, Bob-jason is all we have.
Why sensorless? If you read through the Scooteructable you might notice that I wail on sensorless drive several times. I decided that having to wiggle yourself possibly during starting is acceptable compared to instructing people on how to properly assemble, timing-adjust, and hook up a set of Hall-effect rotor sensors to hobby motors. This is something I have personally instructed other people how to do, and it is a very painful process.
AMAZON
Since when did Amazon become an industrial supplier? (Answer: since Amazon Supply opened!)
Power switch
Well, we'll be needing some random other parts from them, like the main power switch. The switch is a "Hella" style battery cutoff switch for automobiles.
These come in 2 flavors: Real (Hella brand), which features silver contacts, pure copper conductors, and heavy ABS and nylon construction, and Shady (knockoffs of an older Hella design), which uses raw brass (copper if you're LUCKY!) everything and is made of... I'm not sure what, but it smells weird. You can find other variants of the knockoff by searching for "Battery switch" or "Master switch".
The decision is yours - the mounting plate for the power switch contains both hole patterns. You need 1.
Fuse Holder
Chibikart's electrical deck is designed to use a "AGU" inline style fuse holder. This is commonly available in car audio shops and electronics retail stores. An example is here.
Batteries
The battery for Chibikart is twoK2B12V7EV 12v 7Ah lead-acid replacement modules. They are lithium ion batteries hiding in a box with a controller that lets them pretend they are lead-acid batteries. Nifty, huh? For more information on these, I did a full teardown of that particular battery - which is why I chose it in the end - on my site.
Short story: the answer to "Why didn't you just use Hobbyking lithium polymer batteries?" is no.
Bearings
Four FR8ZZ type flanged radial bearings are used for Chibikart's steering. My favorite Chinese bearing front, VXB (because all legit bearing manufacturers have cool 3 letter names like NSK, SKF, NTN...) sells these as p/n KIT7578. However, the same goods are also sold on Amazon, so you may prefer to just consolidate an order.
Alternatively, just searching "FR8ZZ" on eBay brings up tons of results, many of which are cheaper per unit and offer free shipping . Sort by Distance First to avoid the ones that are straight from China because they will take eons to ship. My personal favorite eBay vendor for bearings of indeterminate origin is USABearingsAndBelts with UltimateIndustrialSolutions a close second, though they do not have the FR8ZZ type.
BATTERYSPACE
BatterySpace is one of those things made possible only through the Internet. They're essentially a front company for Chinese battery vendors. This is totally not a bad thing - in fact, I love them. From Batteryspace, select a 24v charger for lithium iron phosphate batteries. This model (CH-L2596N) will charge the above K2 bricks in an hour flat.
You can find downmarket 1.5-2.0 amp 24v scooter chargers on Amazon for $20-30 if you are inclined to wait longer, but I think spending the extra $30 to have 66% less downtime is worthwhile.
Incidentally, BatterySpace also has their own line of mysterious SLA replacement bricks. I have not touched these in person, ever, nor peered inside one, and their discharge rates seem awfully low, so I would stay away from them for now.
YOUR LOCAL BIKE SHOP
I sourced many brake parts from Cambridge Bicycle, the bike shop across the street from our building, and they were immensely helpful in helping me sort out bike jargon so I could direct everyone else correctly. You need several generic bicycle brake parts:
- 6mm Barrel Adjuster and 6mm brake cable anchor bolt. These are commonly found in road bike caliper brakes. Example barrel adjuster and anchor bolt (print those out and show them pictures if you have to!). Or just buy it from Amazon.
- 2x 4 foot brake cables and sleeves. At least one end must have a 7mm molded nipple (the round thing)
- 2x road bike brake pads. Get the smallest, most rectangular one you can, and it must have a 6mm stem.
Step 4: The First Assembly Step: Front Corner Plates and Steering Upright Mounts
Each assembly step will have a Parts Required section indicating what pieces out of the panels, loose parts, and hardware are needed. There will also be a Tools Required section. Next, I might indicate if there are any Acceptable Deviations such as substitute parts or tools/techniques - these are known to be compatible with the design.
First, we will construct as many independent subassemblies and modules of the vehicle as possible - including things like motor mounts, drive wheels, shaft mounts, etc. Then these will be combined with cut frame material and the whole vehicle assembled in one shot, culminating in a rolling frame test that signifies mechanical completion. Finally, control electronics will be installed and the vehicle will be wheels-up tested, then ground tested!
STEP 4: Assembly of the front corner plates and steering upright mounts
Parts Required:
- The four front corner plates from the 0.25" panel
- Four FR8ZZ bearings
- A bench vise or arbor press
- A file or sander
Step 4.1: Gather the parts
Snap off the four front corner plates from the 0.25" panel and split them into individual parts - everything is held together by little tabs to facilitate machining, but these will get in the way of the final design (as well as being a serious sharp edge hazard!).
Step 4.2: Clean the edges of the plates
Using a file or sander, remove the remnants of the little tabs from all of the plates.
Step 4.3: Properly orient the bearings and plates
You will need to create mirror image pairs of plates. Arrange the corner plates and bearings as shown in the image - their flanges should face outwards. Each bearing goes with one plate. This must be done correctly, or you could end up with multiple plates of the same type, which would be....inconvenient.
Step 4.4: Press in the bearings
Using a bench vise or arbor press, apply pressure as close to the centroid of the bearing as possible - even pressure is essential for straight installation. Push the bearing all the way in and make sure the flange rests on the plate surface.
Depending on the mood of the waterjet that made your panel, you may find that the bearing is already a little loose! Do not fret; it's fine if the bearings do not press in. There will be a bolt which keeps the whole assembly together in the end. If you want to temporarily secure the bearing, use a strip of tape or fill the bore gap with a retaining compound.
If, however, the bearing is too tight - more than palm pressure is needed to push the bearing in, then DO NOT proceed. You will need to use a round file around the perimeter of the bore to open it up slightly. The holes have been sized such that they are on the safe, loose side, but if you attempt to press in a too-tight bearing, it will degenerate to the slightly less useful case of a solid chunk of metal.
Step 4.5: Verify bearing flatness
Look closely at the side of the plate. Are you suuuuuuuuuuuure the bearing is seated flat? If it is not, the steering kingpin will not install in future steps. Use vise or press force biased on the high side if need be in order to seat the bearing.
Step 4.6: Complete assembly
Verify that you have two mirror pairs of plates each with a bearing flange on the outside (uppermost AND lowermost) faces. Set these aside for now.
Step 5: Step 5: Installing Bushings in the Steering Column Brackets
Parts Required:
- From the other 0.25" panel, the top and bottom steering column brackets.
- Two 3/4" bore, 7/8" OD flanged bronze bushings
- A rubber mallet
- A file or sander
Step 5.1: Gather the bushings and the 0.25" panel
The other 0.25" panel contains all the front end parts like steering mounts and throttle pedal mounts, etc. Find the one in the image and get two bronze bushings.
Step 5.2: Separate and clean the top and bottom steering column brackets.
The top steering column bracket is the single long piece with the ~1" hole, and the bottom one looks vaguely like a spaceship. File or sand off the tabs.
Step 5.3: Install the bushings
Because these bushings are thicker than the material, they cannot be vised into place. Suspend the bushing hole over a gap in the 1/4" panel (which acts as a Convenient Panel Spacer in this case). Use a rubber mallet and gently tap the bushings to seat them - orientation does not matter in this case since the plate is symmetric from top to bottom. When the bushing is seated, then you can give a few more forceful whacks to make their flanges flush with the material surface.
Acceptable Deviation: If you have a real arbor press, use it instead in conjunction with the Convenient Panel Spacer.
If the bushing is loose, then use the same advice as for the steering kingpin bearings - tape them in place for now, since they will have other constraints later, or use some retaining compound.
When bushings are installed in both top and bottom brackets, set these completed parts aside.
Step 6: Step 6: Construct the Rear Motor Mount Modules
Parts Required:
- The panel of 1/4" back end parts
- #4-40 x 1/2" long socket head cap screws
- #4-40 hex or square machine nuts
- 3/8"-16 x 3.5" Hex head bolts, QTY 2
- 3/8" bore x 1/2" length SAE 863 bronze bushings, QTY 4
- 3/8"-16 hex nuts with lockwashers
- 3/32" hex wrench for the 4-40 screws
- Flat metal file
- Rubber mallet or other soft hammer
Step 6.1: Get the RMMM panel, split the parts off, and file the tabs
File or sand off the little tabs that hold the parts together.
This panel is the only example in the current panel revision which has all the part of one assembly. I may reconfigure the other panels to reflect this - it makes the system less confusing.
Step 6.2: Gather Hardware
You will need the two axle bolts with nuts and washers, 4-40 x 1/2" screws, 4-40 hex or square nuts, and the four 3/8" bore bushings.
Acceptable Deviations: You can use a locknut like a nylon-insert nut instead of a discrete nut and lockwasher. I prefer the lockwasher style because it is more responsive to tightening - you can easier feel when the assembly is being tensioned together. The 3/8" bushing is a McMaster part, but similar parts should be available at a hardware store.
Step 6.3: Install the inner axle mount plate into the bottom RMMM plate
The two small rectangles are the inner axle mount plates, and the right-angle plate with two slots is the bottom RMMM plate.
Push (or slide) the tab on the inner axle mount plate into the innermost slot on the bottom RMMM plate. You might need a rubber mallet to do this, but it should not take significant effort. If it does not seat with gentle taps, you will need to file out the slots slightly.
Step 6.4: File out the rectangular slots if necessary
These conventional waterjetted plates have an on-dimension side and a "tapered" side. If you look at the plates end on, they might look vaguely trapezoidal. The fatter side is what could be preventing the tabs from mating fully into the slots.
Use a flat metal file and file out the fat side of the slot slightly, testing for fit
Step 6.5: Install the hex nuts into the inner axle mount plate
Slide a 4-40 nut into each of the 4 slots on the inner axle mount plate. These slots are oversize on purpose, so they might just fall back out again! You may elect to put a strip of scotch tape or similar over the slots to prevent this.
Step 6.6: Install the top RMMM plate and the outer motor mount plate
Slide or mallet-tap the top RMMM plate in place, then slide the outer motor mount plate in from the side. Install all of the 4-40 screws and hex nuts.
Step 6.7: Flush-tighten all the hardware
Throughout the steps, we will be using temporarily tightened screws. This temporary state will be called "flush-tight", and it is the state where you tighten the screw to the point when the head lands on the material (onset of friction). The assembly is very slightly adjustable in this condition, which will be needed for future assembly steps.
Step 6.8: Slide in the rear axle bolt through the 3/8" spacing bushing
Install a 3/8" normal washer under the head of the 3/8"-16 x 3.5" bolt. Then take the bolt and slide it through both of the axle mount holes, skewering one 3/8" bore x 1/2" long bushing, from the inside (L-bracket side) of the assembly. The bolt head and washer should sit flush on the inner axle mount plate.
You might find that the bushing will not just slide between the plates. It may be slightly too long, so you can file the end down a little (or loosen the outer motor mount plate's screws). A needle-nose plier helps in sliding the bushing into the narrow confines between the plates.
Step 6.9: Install the nut and lockwasher and another 3/8" spacing bushing on the outside.
This hardware will eventually secure the rear wheels. Take a 3/8" bushing and slide it on first, then add the nut and lockwasher.
Step 6.10: Make a mirrored assembly
Using steps 3.3 through 3.9, make an opposite-handed assembly. Use the image as a reference.
After completing these assemblies, put them aside. We will return to the pile of assemblies when the frame is ready.
Step 7: Step 7: Assemble the Brake Body and Brake Pedal
Parts Required:
- Brake Shoe Mount and Brake Cable Mount plates. They are the four attached small parts from the 1/8" panel, two of which look kind of like J's.
- Brake Body Plate from the 0.25" panel that contained the steering column brackets.
- Brake Pedal top plate and Brake Pedal side plates from the 0.125" panel
- #4-40 x 1/2" socket cap screws with nuts
- Road bike brake shoes, QTY 2
- Bike brake cable anchor bolts, QTY 2
- 1/4" or M6 flat washer if needed - See Step 7.5
- 3/32" hex wrench
- Flat file
- Rubber mallet
- Small adjustable wrench
Pluck the parts from the images off of their panels. Clean the tabs off the parts as usual.
Step 7.4: Assemble the Brake Cable mounting plate, Brake Shoe mounting plate, and Brake body plate together
This assembly step is pretty much explained by the picture. The assembly can really go together one way - be aware of which "side" you're working on. One will end up looking like " ¯|_ " and the other a "_|¯".
The 0.25" pivot hole in the brake body plate should be located close to the curl part of the brake shoe mount.
Go ahead and fully tighten these screws. They are very small and delicate as far as screws go, so we will define "FULLY TIGHTEN" as 1/4 to 3/8 turn past flush-tight. Going further than that risks stripping out the nuts, which is not cool.
Step 7.5: Attach the road bike brake shoe
The brake shoes should have come on a M6 threaded stem with matching nut and washer. The stem of the brake shoe might have a little taper or fat section on it which prevents the whole thing from seating flat on the brake shoe mount. If this is the case with your brake shoe, use a 1/4" or M6 flat washer between the brake shoe and the mounting plate. It should be flat-surface contact all the way.
Bolt the brake shoe to the mounting plate, keeping it vertically aligned.
Step 7.6: Make a mirrored assembly of the entire brake body assembly
Follow these instructions again, just turning some of the parts upside down. The result should look like the picture.
Step 7.7: Assemble the brake pedal
Side the brake pedal side plates into the top plate - these only fit in one combination. Slide in 4-40 nuts and tighten with 4-40 screws. That's pretty much it.
Step 7.8, or possibly 7.69999: Install the Brake Cable Anchor Bolts
One mistake I made in the design of this brake lever system was that I used an anchor bolt size that was smaller than the standard ones found on bicycles. The design has been changed a little since this example to accommodate them, but I am working with this pedal for now.
Take the two anchor bolts and insert them into the larger set of two holes in the side plates. Contrary to the picture, the bolt head with cross-drilled hole for pinching the brake cable should be on the inside. If you find that this is physically impossible, don't worry - I did too. Take apart the pedal so you can install them.
If your pinch bolts came with a washer on each, they are to stay with the nut, not the head. Temporarily tighten the pinch bolts so they don't fall out.
Set the complete Brake Pedal and Brake Body Assemblies aside.
Step 8: Step 8: Assemble the Steering Yoke and Pitman Arm
We will be abusing a type of shaft collar (metal dongle installed on a shaft to retain parts axially along it) that has face mount holes and pressing it into service as a hub. This is one of my favorite parts because of the ease by which you can make a clamp hub for something, but they only come in sizes of 3/4" and above! Some smaller ones like 3/8" would be helpful for robots, I think.
Parts Required:
- Face-mount bolt pattern shaft collars, McMaster P/N 9677T1, QTY 2
- 1/4"-20 X 1/2" length button head socket head cap screw, QTY 4
- The steering yoke
- Pitman arm from the last unbroken 0.25" panel
- 5/32 hex wrench
- Flat file or sander
The steering yoke is the only piece in the whole 0.25" collection that looks vaguely like something you can grab onto.
I didn't have a picture of the Pitman arm by itself, so 8.2 is a picture from the next step! The Pitman arm is a small, egg shaped plate with the same center hole pattern located on the front steering uprights panel.
I went ahead and ordered some self-locking button-head socket cap screws from McMaster - it is their P/N 92360A314 for the 1/2" length. Chibikart uses 3 different lengths and they can be found in the BOM. I would advise just purchasing these outright since you will need essentially all of them. I chose button head for the majority of the screws on Chibikart because they both look nicer and have a wider contact area.
Acceptable Deviation: Really any of the button head screws can be replaced with plain socket or even hex head screws at your discretion.
Step 8.3, 8.4: Flush-tighten the shaft collars to both parts
The shaft collars have one side which is "counterbored" and one side where the threads start from the face. Orient this side up and fasten it to the steering yoke and the Pitman arm with 1/4"-20 x 1/2" cap screws.
Step 8.5: Verify screw fit
Use a flush-tight fit for now, because once these are installed on the steering shaft, the right-angle clamp screw has to be able to bend the whole shaft collar a little!
Once you have the shaft-collars-turned-hubs attached to the parts, set these aside.
Step 9: Step 9: Assemble the Front Wheel Uprights
Parts Required:
- The 0.25" panel of steering upright components
- The square upright retainer plate from the 0.125" brake parts panel
- Colson Performa 4" x 1.25" with ball bearing hubs, QTY 2
- 1/2" diameter x 1.75" length shoulder screw, McMaster p/n 91259A718 QTY 2.
- 3/8"-16 x 2.5" standard hex head bolt
- 3/8"-16 nut and lockwashers
- #4-40 x 1" socket head cap screw
- 3/32" hex wrench
- Flat file or sander
- #4-40 hand tap with tap wrench
- 1/2" drill bit or reamer and a drill to put it in
- Adjustable wrench
You know the drill by now. You might elect to hacksaw off another one of the 3.5" long rear axle bolts and turn it into a 2.5" one - I did this just because I would have to go out and get two random bolts otherwise.
Step 9.5: Tap 4-40 threads into the bottom upright plate
Oh, dear. Tapping threads is something many people dread, and I'm having you do it as the first major fab exercise!
If you have never tapped threads before, I would recommend taking a piece of aluminum and drilling & tapping some practice holes before trying a "production" part! There are some helpful videos on YouTube about how to use a hand tap and tap wrench - one of them is this one by iHeartRobotics which gets the point across fairly well. If you aren't confident in your hand-alignment skills, you can start the tap in a drill press (unpowered - just turning the chuck by hand).
I strongly recommend buying a "gun tap", also called a "spiral point" tap. These clear their own swarf (cut up bits of metal) much better than a straight-flute generic tap you might find at the hardware store, resulting in less breakage. They cost a few bucks more, but they're well worth it. A 4-40 gun tap from McMaster is p/n 2523A444.
Use a legitimate tapping fluid or cutting fluid if you can - I prefer Tap Magic, which comes in a thinner aluminum-specialized formulation. In a pinch, you can use WD-40 too.
Proceed slowly! Or else....
Step 9.6: Oops, I accidentally..
It happens to everyone. I was just going too fast here, like driving in a screw fast. Taps break because of applied sideways forces which your wrist has to be trained to eliminate. Flute clogging may also suddenly head to a blockage of the rotational motion, then the inertia if your hand is enough to break the tap.
A general rule for tapping is "two turns in, half a turn out". The half-turn back breaks off any long strings of chips which may have formed, and it helps the tap spread the chips out along the flute.
It's better to be extra slow and conservative than to keep breaking taps into your part! This assembly will work fine with only 2 screws holding it together, but that's alot of broken taps...
Step 9.7: Prepare the upright plates for assembly
Find the bottom, middle, and top plates shown in the picture and the retainer plate. There are two large "T-slotted" plates that go in the middle, and the top and bottom plates have smaller square cutouts.
The hex head of a standard 3/8"-16 hex bolt fits into this approximately rectangular area once the plates are stacked together.
First, test the fit of the bolt into the middle plates' T-slots. Many bolts have a manufacturer's stamp on their heads which creates a raised area that will not pass the T-slots. You may need to file off these markings.
Next, insert four 4-40 x 1" socket cap screws through the top plate. These will pass through the two middle plates and then thread into the 4-40 threads you made earlier.
Step 9.8: Stack the upright plates around the hex head bolt
Starting with the bottom plate, lay the hex head bolt with hex flats parallel to the table onto the rectangular divot ( the points do not go into the divot). The width of the T-slot in the middle plates is the point-to-point width of the hex. Stack two middle plates, then stack on the top plate.
Make sure the square nubs that are on one side of the top and bottom plates are aligned. Slide the retainer plate along the bolt until it seats into the stack, upon the square nubs. Depending on how tightly your bolt fits, you might need to wiggle or mallet things into place.
Step 9.9: Tighten down the 4-40 cap screws to secure the stack of plates
The retaining plate does not have fasteners - it is kept in purely by bolting the front wheel in, so make sure it doesn't fall off as you do this. Tighten fully the 4-40 socket cap screws to turn this stack of plates into a solid block.
Step 9.10: Verify that the steering kingpin shoulder bolt clears the holes in the plates
Take the shoulder bolt that will be the kingpin and slide it through the stack of plates. It should either slide loosely through, or require at most thumb pressure. If it doesn't clear, it will generally just get caught on something and will not move.
If this happens, you will need to use a 1/2" drill bit or reamer to clean out the hole.
Step 9.11 and 9.12: Clean out the 1/2" bore, if necessary, but don't try to Superman-grip the upright as you do so!
Even though there looks like a tiny amount of material in the way, your drill bit will likely catch and dig in very quickly because it is all at the periphery. Then the entire upright will suddenly rip itself away from your Superman-grip and may or may not mill out a small portion of your hand in the process.
Put the upright in a vise or clamp it to a bench before drilling out the hole. Proceed slowly with the drill and don't let it catch and chip around!
Step 9.13: Bolt the front wheel on
Take a 4" Colson and slide it right onto the 3/8" axle. Secure with a nut and lockwasher, or locknut. Tighten this well, because this is your front wheels. At least 3/8 turn past flush-tight is recommended.
Step 9.14: Make a mirrored assembly
As with many things on Chibikart, there is another side to the problem. Make a mirrored assembly - this should be identical save for flipping the bottom upright plate around!
After these are done, put them aside and clean off your work area. The rear wheels are the single most complex fabrication step and you will be using quite a few tools.
Step 10: Step 10: Fabricate Rear Drive Wheel Assemblies
Read through the whole process and understand what is expected. There may be some areas you find that can be streamlined, but don't rush through it and mix up the very similar looking small drill bits or break more taps!
The basic process is:
- Use the sprocket hub plate as a template to drill, tap, install 1 screw, to rotationally lock it in place on the wheel
- With the hub rotationally secured, drill the rest of the wheel hub screws and tap them
- Clearance drill the hub plate for the wheel hub screws
- Tap the sprocket mounting holes and install the sprocket
- Mount the sprocket on a 1/2" mandrel in a drill press and file-chamfer the edges
- Install the sprocket and hub plate assembly back onto the wheel and verify that it spins freely
Parts Required:
- Colson Performa 4 x 1.25" wheels with ball bearing hubs, QTY 2
- The sprocket ring and sprocket hub plates out of the 0.125" parts
- #4-40 x 1/2" and #4-40 x 1/4" screws
- #42 drill bit (Tap drill size for #4-40)
- #32 drill bit (Clearance drill size for #4-40). Acceptable Deviation: 1/8" drill bit, slightly looser fit.
- #4-40 tap and tap wrench
- 3/32" hex wrench
- Flat file
- A 1/2" diameter x 2" length bolt with nut and washer to use as a mandrel for the hub plates. I used a 1/2"-13 coarse-thread bolt.
- 1/2" drill bit or reamer, if needed, to clean the hub plate bores.
- Drill press with 1/2" chuck. Acceptable Deviation: Just a handheld drill if you are careful.
Grab the plate of sprockets and hubs and separate & clean them.
You don't necessarily need 1/4" long 4-40 screws if they are hard to get. They are for screwing the sprocket proper to the hub plate, so there's only 1/4" of material there anyway. The 1/2" screws will also work in this application.
Step 10.2: Verify that the center hole of the hub plate clears the ball bearing race on the Colson wheel
The center hole has been designed to be a slight clearance fit for the Colson's inner bearing race. This is so it can be used as an alignment feature without too much wobble in the end. Put the hub plate over the Colson's bearing race and verify that it moves freely - some slop is supposed to be there.
Step 10.3: Clear out the Colson bore if needed
If there is not free movement, then you will need to clear out the bore slightly. Use a round file or a 1/2" drill bit in a handheld drill (not a drill press).
To use the 1/2" drill to clear a greater than 1/2" hole, you must tilt the hub plate while it is being drilled! If you choose to do this, the hub plate MUST BE SECURED WITH LOCKING PLIERS. Do not try to use regular slip-joint or needle nose pliers to try and hold the pressure. You may optionally secure the plate in a vise and tilt & roll the drill instead.
Remove just enough material to ensure that the hub plate spins freely on the inner race.
Step 10.4: Drill 1 hole-to-be-tapped into the Colson wheel
With the hub plate slipped over the Colson wheel, use a drill press with the #42 drill bit to drill a hole approximately 1/2" deep into the Colson, using an inner hole on the hub plate as a guide.
It doesn't matter where you start it, but this hole will become the reference by which other holes are drilled. The reason that we are not doing all 8 hole at once is because you don't want the template to rotate at all while the holes are being drilled, lest they no longer line up!
Step 10.5: Tap the 1 hole with a 4-40 thread
Go about 1/4" deep this time. The Colson plastic is actually soft enough to use the screws as thread-forming screws, but having a small bit of thread at the top will make it start much easier.
Step 10.6: Clearance drill the one hole in the hub plate
Because the wheel will eventually be holding the thread, the hub plate's 8 inner holes will eventually be drilled out ("cleared") to pass a 4-40 screw. Find the hole you used as a template and drill it out with a #32 drill bit. Only clearance-drill this ONE hole.
Step 10.7 and 10.8: Deburr and clean the other side of the hub plate
The drill bit will probably have left nasty flashing and burrs on the side it broke through. Use a hand file to remove these "burrs" and make the surface flat again - it will need to be flat for the next step.
Step 11: Step 11: Continue Rear Drive Wheel Fabrication
Step 11.1: Place one #4-40 x 1/2" screw into the wheel hub
Adding this screw means you can drill the rest out and know they will all fit - that's why we are going through this seemingly circuitous process. Bolt the hub plate to the wheel with 1 #4-40 x 1/2" screw.
Step 11.2: Verify that the hub plate is level
Don't overtighten this screw! In fact, leaving it a little loose is best: the hub plate needs to be able to sit flat on the wheel hub.
Step 11.3: Drill the rest of the wheel hub holes-to-be-tapped with a #42 drill bit
Now, take this back to the drill press, armed with a #42 drill, and drill the remaining 7 holes into the Colson wheel.
Step 11.4: Tap starter threads in the rest of the holes
Maybe I should have started people out tapping plastics...
Step 11.5:Drill out the inner set of holes on the hub plate with a #32 drill
Now we will clearance drill the wheel hub holes to pass the #4-40 screws. Go ahead and drill the inner ring out using a #32 drill.
Step 11.6: Clean the other side as you go
As you drill, you might notice the burrs on the underside making your job difficult. Remove these as they form with a hand file.
Step 11.7: Attach the hub plate to the wheel and verify that it spins freely
This is a critical step, even though it seems to be a waste of time. Use ALL 8 4-40 X 1/2" screws and firmly attach the hub plate to the wheel. Tighten fully - 1/4 to 3/8 turn past flush. This is to double check that all of your drilling and tapping hasn't been biased to one side.
If there is interference or tightness, you will need to remove the wheel hub plate and clean out its center bore a little more. You may be able to see where things are rubbing if you coat the inside of the hub plate bore with a marker and see where it rubs off, then filing away at that spot judiciously.
There shouldn't be much, if any, interference, but putting in those screws can take a while....
Step 11.8: Tap the outer ring of holes #4-40 for the sprocket
While you still have the plate attached, go ahead and thread all 8 outer holes. These will mount the sprocket hub plates.
Step 11.9:Remove the hub plate from the wheel and attach the sprocket
Yes, you have to take the hub screws out one more time! We will be chamfering (machining an angled surface) onto the sprocket teeth in the next step. To do this, they need to be attached to the hub plates so they can be gripped by a 1/2" mandrel.
Step 12: Step 12: Complete Rear Drive Wheel Fabrication
Step 12.1: Mount the sprocket on a 1/2" bolt mandrel
This is where the sketchy stuff starts. We will be mounting the sprocket on a temporary shaft that we can spin, then applying a metal file to chamfer the tips of the teeth. The term for this termporary shaft is a mandrel or arbor. Not to be confused with the monkey species.
Get a 1/2" diameter x 2" long bolt (1/2"-13 is the most common), a nut, and at least one washer. If you have 2 washers, the sprocket should be held between two of them. Else, use the washer on the nut side - this is to prevent marring of the aluminum by the harder steel nut. Tighten the sprocket between the nut and the bolt head.
Visually center the sprocket on the shaft. Absolute centering is not necessary because the file will be handheld.
Step 12.2: Mount the mandrel in a drill press
Any drill with a 1/2" chuck will work, too, but you would probably want someone helping you hold the drill or the file.
Step 12.3: Hold a file to the sprocket teeth while the sprocket is being spun
File a roughly 30 degree (from horizontal) chamfer onto the edge of each sprocket. You want to reduce the thickness of the tips of the teeth by about half - taking them to around 1/16" to 3/32" thick. Chamfering the sprocket teeth ensures that it never snags a chain link square edge on and derails the chain.
Be careful during this process - use the middle of the file, not the tip. The tip could get caught on a sprocket tooth, which would not only be bad for the sprocket, but might launch the file through you. Because really, compared to aluminum, you are not very hard.
Step 12.4: Verify that the chamfers are roughly equal in height
If you chamfered one side a little more than the other, don't worry - it's not critical. If you're really OCD, then you can flip the sprocket over on the mandrel so you can always see what you are chamfering!
Step 12.5: Attach the chamfered sprocket assembly back onto the wheel
Install those 1/2" screws ONE MORE TIME!That's it. Put all of them in and tighten all these screws fully.
Step 12.5: Do it all over again
Yes, now you get to make a second wheel, repeating steps 10 through 12. Are your nerves shot enough?
If you did read ahead, you would know that one way to save time is to do all the steps in parallel - work on both sprockets and hubs at once.
Once you have two completed drive wheels, congratulations! There is no more fabrication on this vehicle. Everything else from here on out is assembly. It might be a good idea to clean the shop a little at this point and reset your tools.
Step 13: Step 13: Prepare the Drive Motors
Parts Required:
- Turnigy 5065-256Kv Brushless Outrunner Motor, QTY 2
- F or 17/64" drill bit
- Phillips head screwdriver
- Drill press or drill
- File or sander
The Turnigy 5065 motor should have come with a little flowery mounting plate. We will be using the mounting plate, but its mount holes are too small. They will be drilled to clear a 1/4"-20 screw.
Step 13.2: Drill out the four outer flange holes
Use the F drill to enlarge all four of the outermost flange holes, on both motor mounting plates. The aluminum that these plates are punched from is very soft, so it will leave gigantic burrs on the exit side. Use a file or sander to remove the meteor-impact-crater-like burrs as they form, so you have a perpendicular surface to work with.
Step 13.3: Mount the motors to the plates using the provided screws.
The Turnigy motors should have come with 4 M4 flat-head screws in a little baggie. Mount the motor securely to the plate using these screws. If you have a threadlocking compound, you should use some of it on the threads to prevent vibrations from loosening the screws.
Add the assembled drive motors to your growing pile of subassemblies when done.
Step 14: Step 14: Cut the 80/20 Extrusion to Length
The following steps begin with cutting the 80/20 extrusion to the proper lengths, then assembling them together with the corner plates and assemblies you put together previously. After that, the brake cables will be routed to the pedal. Then finally the wheels will be installed, and you will have a mechanically completed rolling frame!
Parts Required:
- 6ft 80/20 extrusion, McMaster P/N 47065T101, QTY 3
- Hacksaw, bandsaw, Sawzall, jigsaw... with moderate to fine metalcutting blade
- File or sander
- A square or right angle gauge is recommended.
You can choose to literally behead the tube or twist the cap off - I find that it takes incredible grip strength to wrench the allegedly removable top out of the little crimps.
Step 14.2 and 14.3: Measure out the required lengths of 80/20
Using a tape measure, mark out the lines of cut. The tolerance is +/- 1/16" with preference towards a little too much, since you can always keep reducing length.
Mark according to figure 14.3. We will be producing the following lengths:
- 2x 28" , all of which must have at least one square (factory-cut) end
- 5x 18", 3 of which must have square ends
- 1x 6" with 1 square end
Step 14.4: Cut the 80/20 sticks according to measurements
Anything which can be used to make a straight crosscut can be used. I used a reciprocating saw ("Sawzall") with a fine metalcutting blade. A jigsaw can be used, too, as can a straight up hacksaw. Make the pieces as prescribed in 14.3.
Step 14.5 and 14.6: Clean the cut ends of the 80/20
You can use either a manual file or a power sander if you have one. At the minimum, you should get rid of the sharp edges resulting from the cutting process.
Step 14.7: Verify that the cut ends are reasonably square
Non-square ends won't kill the project (that's why I specified some factory square ends), but they will make squaring up the frame and aligning the corners harder. While filing or sanding, use a machinist square or any right-angle thing to make sure the ends are more or less vertical. Keep filing if need be!
Step 14.8: Double check correct part lengths
I decided to label my cuts so I know which ones were the square ones and not. You may come up with your own nomenclature, but I just used "S" for a square ended piece (located on the square side) or "NS" for a piece with no square end.
You should end up with:
- 2 28" Square-ended (S-28-1 and -2)
- 3 18" Square-ended (S-18-1 through -3)
- 2 18" Non-square ended (NS-18-1 and -2)
- 1 6" Square-ended (S-6-1)
There's a sizeable amount of scrap that was generated by this process. It should set aside in your hopefully growing materials and hardware pile for some other crazy contraption one day!
Hold onto these frame extrusion sections - we will be using them right now.
Step 15: Step 15: Gather All Frame Components
At this stage, gather all the remaining panels of parts as well as the subassemblies you made previously. Additionally, now would be a good time to gather the necessary hardware:
- 1/4"-20 x 1/2" long socket cap screws, about 25
- 1/4"-20 x 3/8" socket cap screws, about 50
- 1/4"-20 x 5/8" socket cap screws, about 50
- #4-40 x 1/2" socket cap screws, about 20
- #4-40 hex nuts
Verify that you can still find the following parts:
- Remaining 1/8" panels of brackets and seat mount plates
- Remaining 1/4" panel of front-end parts
- 1/4" seat mount plate
- 1/8" plastic/wood bottom plate
- The cut lengths of 80/20 from Step 14
- Steering yoke assembly
- Brake pedal
- Steering column brackets with installed bushings
- Rear motor mount modules, both
- Rear wheels, both
- Front wheels on uprights, both
- Front corner plates, all 4
- Two drive motors, assembled
- The front "scoop" that says CHIBIKART on it
- The lawn mower seat!
Step 16: Step 16: End-Tap 80/20 Extrusions
Parts Required:
- 80/20 extrusions S-18-1, S-18-2, S-18-3 (All of the square ended 18" ones)
- 80/20 extrusion S-6-1
- 1/4"-20 tap with handle
Here's more chance to practice tapping threads using a tap which is far, far less likely to break from wrist pressure alone! You must end-tap both sides of each extrusion listed above. That's 8 holes total. Think of it as wrist strength training.
If you have a spiral-point tap, then you can thread all the way in one shot. The spiral point pushes curls out ahead of the cut, which is handy in this case because the hole is essentially infinitely deep. If your tap is conventional straight-fluted, then you should follow the "2 turns in, half turn out" rule. Use a cutting fluid in either case.
1/2" thread depth means that you go 1/2" deep after accounting for the tapered-off section of the tap. All taps have this - it's a few threads that are stunted to let the tap start cutting easier. On typical taps (called "Plug" style taps), it's about 4-5 threads.
Therefore, you want to go to a total depth of 3/4" on the 1/4"-20 tap.
(Other styles of taps include "Taper" in which 10+ threads are stunted - about half of the whole thing. They are designed only for going all the way through a material, like a plate. A "bottoming" tap only has 1-2 threads tapered off, and is intended to go back in after a Plug or Taper tap and finish the job to the very bottom - they're very difficult to start correctly. Here's an example picture.)
Step 17: Step 17: Assemble the Seat Mount
Parts Required:
- Surplus Center 1-3289 Troy-Bilt seat
- The 1/4" "H" seat mount plate
- Extrusions S-18-1 and S-18-2
- 1/4"-20 x 1/2" socket cap screws
- 80/20 slot-compatible nuts: McMaster 98001A130 or 47065T139
- 3/8"-16 x 1.5" socket cap screw with washers, QTY 4
- 5/32" hex wrench
- 5/16" hex wrench for the 3/8" screws
- A small screwdriver for poking at slot-nuts
- Threadlocking compound
You need the seat mounting plate, the thing that looks like an H, the first two square-end 80/20 18" extrusions, at least four slot nuts, four #1/4"-20 x 1/2" long screws, and 4 3/8"-16 x 1.5" long screws. I used socket cap screws, but an acceptable deviation is 3/8"-16 hex head bolts. These may be more common in the required size. Make sure to include washers.
The McMaster part 98001A130 is generic tabbed "weld nut" (for welding to sheet metal) that I found fits into the 80/20 slot, so I favor it because it is generic. Otherwise, cheap bulk packs of 80/20 nuts are available on eBay - look for the 1/4"-20 thread.
While this step only needs 4, you will really need like 100. Get a pile - a literal pile.
Step 17.2: Slide 2 nuts into the top of each 18" extrusion
Pause!
Step 17.3: Understand the 80/20 coordinate system
In the next few steps, there will be a ton of 80/20 nut-sliding, so please take a moment to familiarize yourself with what "Top", "Bottom", "Front", and other locative words mean for the purposes of this Instructable!
Step 17.2: ...now slide 2 nuts into the top of each 18" extrusion.
Step 17.4: Insert 4 1/4"-20 screws through the seat mount plate and into the nuts, but do not tighten
We will need to shift the whole plate back and forth a little, so do not tighten these screws - you can take them to "flush-tight" then back off half a turn.
Step 17.5: Square up the two seat mount extrusions and tighten the seat mount plate 5 7/16" from the square edge
This might seem like a weird dimension, but it was dictated by the seat's own mounting pattern. Using another 80/20 piece, square up S-18-1 and 2 such that they are parallel. Now, using a tape measure or ruler, offset the left edge of the seat mount plate approx. 5 7/16".
Really 5.5" is good enough - you're not going to notice the extra 1/16" of asymmetry!
Tighten all of the screws. 80/20 extrusion is actually a little bit "springy" on purpose. Tighten at least 1/2 turn past flush-tight - 3/4 turn if you can manage it.
Let's quickly review the tightnesses:
- Flush-tight: when the screw head makes contact with the material
- Fully tight: 1/4 turn past flush-tight
- 80/20 special tight: 1/2 to 3/4 turn past flush-tight.
Step 17.6: Collect the seat mounting bolts
You need at least 1.25" long 3/8"-16 screws - 1.5 is good, but 1.75 is actually too long. These are shallow nut inserts molded into the seat base, so they aren't very flexible in the screw depth.
Apply a small patch of threadlocker to each screw.
Step 17.7: Fully tighten the seat mounting bolts
All four of these should line up - the holes are purposefully extra-big because the seats are not precision components!
Put this seat assembly aside - we will return to it soon.
Step 18: Step 18: Lay Out and Install Slot Nuts Into 80/20 Extrusions
Parts Required:
- Extrusions NS-18-1, NS-18-2, S-28-1, and S-28-2
- About 9000 80/20 slot nuts
- A small screwdriver to poke the slot nuts with
First, remember what the 80/20 coordinate system we are using is! Start with the square 28" rails and lay them side by side.
The two non-square 18" rails go on their ends. Use Figure 18.2 as a guide to lay the labeled sides properly - they are the basis for the coordinate system!
Step 18.4 and 18.5: Insert the proper amount of nuts into each slot
This is the part where it could get confusing. Remember, once more, our coordinate system. Prepare your bag of 80/20 nuts - I hope you really do have alot of them!
- NS-18-1: Top 6, Bottom 6
- NS-18-2: Top 12, Bottom 12
- S-28-1: Top 4, Bottom 4, Front 8
- S-28-2: Top 4, Bottom 4, Front 6
Step 18.6: Verify that you have the right number of nuts
If you feel unsafe or need to dispose of more slot nuts, pop some more in each one. Extras don't hurt - the kind that you can drop into the slot in-situ instead of disassembling everything to get in from the side are something like $1.50 EACH.
Don't disturb this arrangement - we'll secure it in the next step.
Step 19: Step 19: Install the Rear Motor Mount Module
Parts Required:
- Pre-assembled RMMMs from Step 6
- 1/8" panel of corner brackets
- 1/4"-20 x 5/8" long screws
- 5/32" hex wrench
- File or sander
There should be a string of 8 1/8" L-plates sort of hanging off eachother. Separate all of these and clean the tabs off.
Step 19.2: Install the left RMMM
These L-brackets are actually height spacers for the corner plates. Lift up the lower left corner (defined by NS-18-1, which is now the back) and slide the left RMMM underneath it (the left RMMM should have its little brake mounting finger pointing forwards). Slide a 1/8" spacer on both sides of the extrusion, and visually line the holes up.
Step 19.3:Flush-tighten the left RMMM
Insert 5 1/4"-20 x 5/8" screws into the top, through the frame spacer, and into the nuts you hopefully remembered to gather underneath first. Do not tighten down anything yet , because in a later step we will make sure the frame is square first.
Do not turn it over and try to insert the 5 screws underneath yet!
Step 19.4: Install the right RMMM
Pretty much every operation from here on will have a right side analog. Install the top side's 5 screws on the right handed RMMM.
Step 20: Step 20: Install the Front Corner Plates and Fully Tighten the Frame
Parts Required:
- Front corner plates with installed kingpin bearings
- 1/4"-20 x 5/8" screws
- 80/20 nuts installed in the slots of NS-18-2
- 5/32" hex wrench
Collect the front corner plates with installed bearings that you put together all the way back in step 4. We will install the top 2 plates first. Find the two that you designated top before - their bearing holes should stick off the frame towards the left and right sides of the rectangle and the Ls should line up.
Place one 1/8" spacer under each front corner plate, line up the 5 nuts required, insert and flush-tighten the 1/4"-20 x 5/8" screws.
Step 20.2: Turn the frame over and install the bottom side front corner plates
Very carefully lift the frame by its front rail (NS-18-2) and turn it over backwards. Keep everything together - if the partially tightened nuts start sliding out on you, it's kind of a pain to fix. Install the front corner plates using the same procedures as 20.1
Step 20.3: Install the remaining screws on the RMMM corner plates.
Flush-tighten these, too. We will be "truing up" the frame shortly, so the corners still need to wiggle a bit.
Step 20.4: Verify the steering kingpins fit through the two bearings
Parts Required:
- 1/2" dia x 1.75" L shoulder screw, first appeared in step 9
Step 20.5: Verify that the frame is square.
Use the 1/8" bottom plate to double check that the corners are square. Additionally, check the width of the assembly - the side edges of the plate are the exact correct width of the vehicle, and the side row of mounting holes on the bottom plate should fall in the center of each 28" extrusion's bottom (or top) slot.
Step 20.6: Fully tighten all the corner plates
Once squareness has been reached, begin by fully tightening all of the screws on the frame's top or bottom (depending on which side you used for squaring). Once one side is tight, flip it over to fully tighten the other side. Remember that with slot nuts, full tightness is about 1/2 to 3/4 turn past flush tight.
Step 20.7: Go back and retighten those RMMM screws
Remember the 4-40 screws I told you not to tighten before? Now that the RMMMs are secured on the frame, it's time to tighten those! These are small machine screws, so fully tighten means 1/4 to 3/8 turn past flush.
At the end of this step, you should have all 40 (!) corner screws fully tightened. The frame should be a rock solid, square-sided rectangle at this point.
Step 21: Step 21: Attach the 1/8" Seat Riser, Foot Bar, and Power Switch Mounting Plates
Parts Required:
- 1/8" plate of seat riser, foot bar, and power switch plates
- S-18-3, the last square-ended 18" extrusion
- 1/4"-20 x 3/8" socket cap screws
- Pre-installed slot nuts in S-28-1 and 2
- 5/32" hex wrench
- File or sander
This panel contains the 4 riser plates that the seat mount bolts to, the plate for the foot rest bar, and the power switch plate. Clean these all up.
Step 21.2 - 21.4: Bolt the 1/8" plates to the left and right side
Starting with the right side in Figure 21.3, bolt the 1/8" plates according to the figures. You should end up with 4 plates on the right side and 3 on the left.
While the seat mount plates and power switch mount can remain loose for now, the footbar plates should be lined up.
Step 21.5: Install and fully tighten the footbar
Using the last 18" extrusion, S-18-3, bridge the two footbar mounting plates and tighten 1/4"-20 x 3/8" screws into the ends. You did end tap it, right?!
Try to keep the bar oriented upwards and square with the rest of the frame. You may need to keep the end-screws a bit loose to adjust it.
Move the whole bar assembly such that the front face of the mounting plates are about 2.5" from where the front corner plates stop. You can move this later according to taste and desire for legroom. This is just for starters!
There is now a 3rd fully tightened cross member in the frame, the footbar. Next, we will focus on continuing front end assembly.
Step 22: Step 22: Installing the Front End Hardware
Parts Required:
- Throttle Mount Top Plate - these have the skinny slotted arm and a large rectangular slot
- Brake Mount Top Plate - looks like the throttle mount, but cut short and with a smooth fillet on the end
- Throttle Mount Bottom Plate - the smallest piece that looks like a middle chunk of the throttle mount top plate.
- Brake Mount Bottom Plate - looks like the brake mount top plate exactly, but without the protruding arm.
- Front Scoop Adapters - the tabbed triangles
- Front Scoop - that thing that says CHIBIKART on it!
- 1/4"-20 x 1/2" screws
- Pre-installed nuts in NS-18-2, the front rail
- #4-40 x 1/2" screws and hex nuts
- 3/32 and 5/32 hex wrenches
- File or sander
They are on the mostly unbroken 1/4" panel from which you pulled off the steering column brackets a while ago. Separate all the remaining parts, clean the tabs off, and lay out the two we need according to figure 22.2.
Make sure the throttle is on the right and brake is on the left. The accompanying" Bottom" plates go immediately underneath - use Figure 22.2 and 22.3 as placement references.
Step 22.2 and 22.3: Flush-tighten the Throttle Mount and Brake Mount Top and Bottom Plates
Move them right up against the corner plates with the slotted arm pointing forward. Wiggle two nuts under each and flush-tighten them. They might need to be moved very slightly later to accomodate the exact spacing of the front scoop's slots, so don't fully tighten yet.
Step 22.4: Mount the Front Scoop Adapters
These slide in between the top and bottom plates that were just mounted. You may need to loosen the top and bottom screws slightly in order to slide these in. Use 4-40 hex nuts in the slots and flush-tighten these with #4-40 x 1/2" screws.
Step 22.5: Mount the Front Scoop
Align the slots in the front scoop with the adapters and push it on. You may need to use light mallet taps to force the adapter & top and bottom plates into position. Insert 4-40 hex nuts into the slots and flush-tighten with #4-40 x 1/2" screws.
Step 22.6: Adjust components and fully tighten all #4-40 screws
This assembly does pretty well aligning itself, but you may need to wiggle some of the parts to seat the tabs fully. After you are satisfied, go ahead and fully tighten all the #4-40 screws only. We still need to add some things to the brake pedal side, so do not fully tighten the 1/4"-20 screws yet.
Step 22.7: Admire your work
It's starting to look like something....
Step 23: Step 23: Install the Brake Pedal Mount on the Front End
Parts Required:
- Brake Pedal Mount side plates, the last of the 0.125" parts
- Brake Cable Sleeve Stop plate and Brake Cable Holder plate from the same 0.25" parts panel that the front end parts came from
- #4-40 x 1/2" screws
- #4-40 hex nuts
- 3/32 hex wrench
- 5/32 hex wrench
These are pretty much the last kibbles of the paneled plates. The 1/8" plates are left over from brake body assembly in Step 7. There are two 1/4" chunks with different sized holes - these are the Brake Cable Sleeve Stop and Brake Cable Sleeve Holder plates. The one with the larger hole is the holder - it keeps the cable sleeve from moving, while the Sleeve Stop lets you pull the cable through the length of the sleeve.
Step 23.2: Assemble the mount first
Make sure the Sleeve Holder goes on the very end of the side plates and the Sleeve Stop is behind it. The #4-40 screw holes will align the parts properly - the gap in between is so either square nuts or hex nuts can be used, the hex sticking out a little past flush with the surface usually. Flush-tighten these screws for now, because...
Step 23.3: Snap the Brake Pedal Mount assembly into the top and bottom plates
You might need to loosen the top and bottom plates' screws a little to accomplish this step. Bend the 1/8" plates outwards a litle and slide the whole thing into alignment with the slots. It should pop in - a little bit of hammer coercion might be necessary.
Step 23.4 and 23.5: Tighten everything fully
Once the side plates are in place, insert #4-40 screws and nuts into the four positions . Now, go back and tighten fully:
- the Brake Cable Sleeve plate screw
- the top and bottom 1/4"-20 screws
- the side plate screws you just placed
Step 24: Step 24: Fit the Steering Column Bushings to the Steering Column
Pressing bronze bushings into holes often reduces their internal diameter slightly. This is by design - they are naturally oversize. However, depending on what you use for the steering column, it could be too large to fit into the bushings.
Drive shafts are usually made with an understanding that they must fit things onto them, like bearings or sprockets, and are purposefully made slightly under size. However, I had originally specified a 3/4" aluminum tube - plain structural tube like you'd make tents or airplane parts from - which is not made to shaft fit tolerances.
I found out that the tube did not fit into the bushings at all, necessitating this step. To save you the pain, I've made some part recommendations that will hopefully avoid this step, but if not, the process I use to open up the bushings is worth noting.
Parts Required:
- Steering Columnn Top and Bottom Brackets with bushings installed, from step 5
- 3/4" OD x 1/16" wall 6061 aluminum tube, 1ft section
- Round file
- 120+ grit sandpaper, a small chunk
- Hacksaw, if applicable, to cut down the steering column tube stock
Step 24.1:Test the fit of the steering bushings on the steering column stock
The fit must be loose and free - a little of play is even acceptable. Tight steering will translate into poor and unpredictable handling!
In my case, there was a good 6 thousandths (0.006", or like 150 micron) of discrepancy between the oversize aluminum tube stock and the bushings!
Step 24.2: File circularly around the bushing bore with a round file if needed
Using a round file and a vise to hold the parts, gently file evenly around the perimeter of the bushing. You may need to rotate the part periodically to get the best vantage point. Keep the file as straight as possible and don't dwell too long in one spot. The filings should be a very fine powder.
I found that adapting to an elliptical-style filing method left the best suface finish and least gouging.
Step 24.3: Test periodically for shaft fit
If you insert the aluminum tube and twist a little, it will leave scrub marks indicating the high points of the bushing which are interfering the most. Focus on these spots first - file them down one by one, then test fit again.
A more legitimate variant of this technique is called "hand scraping" or "scraping" in general and is used, with meticulous detail, to create the best quality flat surfaces for machines possible. We are not being nearly as scientific - a simple "Yes, it fits" or "No, keep filing" is sufficient!
Step 24.4:Verify that the shaft fits freely
There will eventually be a point where the last file stroke you made is the one which will free up the bushing for travel along the shaft. Make sure it is indeed free from tightness - there should be no big scrub or gouge marks like that shown in Figure 24.4.
Step 24.5: Clean up the interior of the bore with some sandpaper
The inside of the bushing is likely full of gouges and ridges now. Wrap a bit of sandpaper around your least favorite finger and scrub the inside a little bit. The goal is just to break some of the hard surfaces.
Step 24.6: Test for free fit along the entire length of the shaft
Slide both bushings up and down the whole length of the steering shaft. If you have longer stock, make sure it at least gets past one foot!
Step 24.7: Trim the steering shaft to 12"
If you started with a long tube, as aluminum tends to be sold in, cut off a 12" chunk and clean off the ends. I elected to just use a hacksaw - it was done in under 10 seconds.
Use a file around the perimeter to deburr the cut as well as make a small chamfer.
Step 25: Step 25: Construct the Steering Column Assembly
Parts Required
- Steering Yoke with shaft collar hub
- Steering Pitman Arm with shaft collar hub
- 12" Steering column tube
- Top and Bottom Steering Column Brackets with now-fitting bushings
- Steering Column Stiffener plate (a T shaped part)
- The short 6" 80/20 piece, S-6-1
- 3/4" single-clamp shaft collars, QTY 2
- 1/4"-20 x 2" long socket cap screw or hex head bolt
- 1/4"-20 x 1/2" socket cap screws
- 1" long, 1/4" ID plain aluminum spacer
- 5/32 hex wrench
- 3/16" hex wrench
- Adjustable wrench
The steering column stiffener plate is one of those little generic shaped things that came off the 1/4" panel. You will need it for this step.
A long 1/4" screw will be needed. 2" long is the recommended length - it has to fit through 1.5" of material and then 1/2" of thread that you put into the end of the 6" piece of 80/20
You'll need 2 more plain shaft collars in 3/4" bore size. Those flange things are expensive, but the normal shaft collars are usually only a few dollars each.
Step 25.2: Fully tighten the steering column bottom bracket onto the front rail (NS-18-2)
Making sure the bushing faces inwards and is well-centered, mount the bottom bracket. Use a ruler to gauge the proper distance between the plates to make the bushing centered.
This will be the "anchor" for everything else in this assembly, so go ahead and fully tighten this piece.
Step 25.3: Assemble the top bracket to the short 80/20 extrusion S-6-1
Using a 1/4"-20 x 1/2" screw, tighten the top bracket to the non square end of S-6-1 (the end that you cut).
This joint will be stressed in torsion, which is a poor way to load a single-screw joint. Use a lockwasher between the screw head and aluminum plate, and tighten it as much as possible - try to get it past the 1/2 turn, but be careful not to strip out the head.
The exact orientation of the 80/20 does not matter - so long as the square end is open.
Step 25.4: Flush-tighten the stiffener plate to the underside and install the aluminum spacer between the stiffener plate and the bottom steering column bracket
Mount the stiffener plate using the last two 80/20 nuts on the underside with 1/4"-20 x 1/2" , and insert the long 1/4"-20 screw through the vertical holes through the 1" aluminum spacer. Flush-tighten the 1/4"-20 x 1/2" screws for now - we might need to wiggle this left and right a little in order to square up the steering column.
Step 25.5: and 25.6 Screw the long 1/4"-20 screw into the square end of the 6" extrusion
Use the 6" extrusion as the world's weirdest-shaped nut and flush-tighten the 1/4"-20 x 2" screw. The bushings should be visually aligned with eachother - do not tighten anything much yet!
Step 25.7: Drop the steering column through the bushings, making sure it can rotate freely
A little bit of friction here is acceptable, because without precision methods, getting 2 bushings to align absolutely dead straight is very hard. You should be able to turn it easily by hand, however.
Tighten the long 1/4"-20 screw on the bottom a little, keeping the bushings aligned, and see if at any point in time the shaft starts binding. If it does, you may need to make sure your 6" extrusion is as square as possible on both ends, maybe necessitating re-filing.
Step 25.8: Attach the Pitman Arm and lower shaft collar
Take out the steering column and place a plain 3/4" shaft collar on the steering column bottom bracket. Drop the steering column through again, skewering the shaft collar.
Now slide the Pitman arm, shaft collar first, up from underneath. The column should end up flush with the bottom of the Pitman arm as shown in Figure 25.8.
Tighten the clamp screw on both shaft collars while holding them together. The collars are supposed to compress a little, so you may be looking at a full turn or more of tightening after "flush tight".
There shouldn't be any axial 'slop' between them when they are fully tightened - keep them both against the bronze bushing. This is the fully constrained end of the steering column, and it shouldn't do anything but rotate.
Now fully tighten the 1/4"-20 flange screws that are holding the Pitman arm onto the face mount collar.
Step 25.9: Add the top shaft collar
Drop another plain 3/4' shaft collar from the top and seat it against the top bushing. Tighten its clamp screw fully.
Step 25.10: Verify vertical alignment of bushings visually and tighten all screws
Make sure that the steering column is as vertical and straight as you can get it - not skewed. Next, tighten all of the 1/4"-20 frame screws on the bottom bracket and stiffener plate. Really crank down on the long 1/4"-20 bolt that anchors the 6" extrusion through the standoff at the bottom, and make sure once again that the top bracket's single mounting screw is very secure.
Step 25.11: Add the steering yoke
Using the same procedure as the Pitman arm, tighten the clamp screw on the shaft collar first, then the face screws. This whole assembly now should move together.
Visually align the yoke and the Pitman arm. When the yoke is pointed straight forward, the Pitman arm should be facing straight backwards and its flat face should be parallel to the footbar and front frame rail. You can loose the shaft collars a little to adjust the angular alignment. Take some time to get this correct.
Also, test for excessive friction again. You should easily be able to move the yoke with 1 finger at the ends. If you have some light machine oil or bike chain oil, add a little to the steering bushings (Do not use WD-40 - it is actually not a lubricant, despite what many people think!)
Wrap the steering yoke in some bicycle grip tape or other soft material if you don't feel like grabbing cold, hard metal.
We're getting close to putting this thing on wheels. Actually, let's do that right now.
Step 26: Step 26: Mount the Brake Pedal
I also neglected to order proper spacers for the pedal, so I improvised with a Tower of Washers! If you already have a pile of 1/4" ID washers, this will work out just fine.
Parts Required:
- Brake Pedal assembled according to Step 7
- 1/4"-20 washers, at least 14 (standard 0.05" - 0.06" thickness)
- 1/4"-20 x 2" screws or hex head bolts, QTY 2
- 1/4"-20 lockwashers, QTY 2
- 1/4"-20 hex nuts, QTY 3
- Adjustable wrench
- Needle nose pliers
If you have, or can get, 1/4" ID x 3/8" long and 1/2" long spacers, they are much better than trying to stack washers. I neglected to order them and the hardware store was closed, so I improvised! Either plastic or metal types will work. An example is McMaster P/N 92510A764 and 92510A765.
Step 26.1 and 26.2: Gather the parts and hardware
Get 2 more 1/4"-20 x 2" long screws. Make sure they both have lockwashers. 3 hex nuts are needed - two will go on the bolt end, but one of them will have an extra nut in the middle.
Make sure the anchor bolts are already installed in the brake pedal as discussed in step 7! If not, take this chance to do it now (See step 7)
Step 26.3: Space the pedal out 3/8" from the inside-most wall and begin threading the bolt through
First, install the brake pedal stop bolt all the way through the topmost set of holes in the side plate This is the second bolt in Figure 26.3 - it's already been secured with a nut.
Now, line up another 1/4"-bolt with the bottom hole in the brake pedal side plates. Start inserting the 1/4" bolt through from the center of the frame (bolt head facing towards the center). Skewer 6 washers or the 3/8" spacer and push it through the first side of the pedal.
It may help to have the frame propped up vertically against a stool or bench for this step since you are working on the bottom.
Step 26.4: Insert 1/2" of spacers in between the pedal plates and secure the whole pedal with a nut
Skewer 8 washers (or 1/2" spacer) with the 1/4"-20 screw, and keep pushing. When it emerges from the other side, begin threading a 1/4"-20 nut onto it. Keep driving the screw through, keeping the nut in the same place, until the screw threads emerge on the other side of the spacer.
Acceptable Deviation: The nut in the middle is purely to hold the pedal in place. You may elect, instead to pile on a bunch more washers or another 3/8" spacer.
Step 26.5:Tighten the bolts
Tighten the 1/4" bolts until the lockwashers are flat, but no more. There is nothing actually resisting the compression of the bolt, so if you keep tightening, you will just buckle the side plates!
The brake pedal should swing freely up and down, being stopped by the frame on one side and the crossing bolt on the other. When the cables are installed, it will be kept by default in the upper position.
Step 27: Step 27: Mount the Front Wheels
Parts Required:
- The two front wheels mounted to uprights (assemblies)
- 1/8" thick nylon or bronze washers, QTY 4
- The 1/2" x 1.75" shoulder screws
- 3/8"-16 nuts and lockwashers
- Needle nose pliers
- A small screwdriver or other pokey thing
- Adjustable wrench
There is 1.25" of space between the corner plates, and the upright itself is only 1" thick. This was deliberately to pervent metal-on-metal rubbing which would occur if the corner plates were too close together. Chibikart 1 had this issue where the uprights were essentially riding on the bearing flanges, and there was alot of ugly rubbing and metal grinding going on.
A set of precision spacers will keep the uprights from loading anything but the rotating inner race of the bearings. These are supposed to be 1/8" thick, and I just picked up some 1/8" thick, 1/2" bore nylon washers from the hardware store. If your hardware store has bronze washers instead, so much the better.
Step 27.2 through 27.4: Mount the uprights on the kingpins, making sure there is 1/8" of spacing on the top and bottom
How do you tell which wheel is left and which is right? Well, the steering link ears should face the rear of the vehicle, and be biased towards the inside. That is, the 0.25" hole on the end of the tab should be closer to the frame than the 1/2" kingpin bore.
Figures 23.7 and 27.4 show how to skewer the 1/8" washers while pushing the shoulder screw through. First, push the should bolt through 1 bearing and loop a washer onto the end of the threads. Then, pull out just enough to slip the upright in.
You will need likely need a very small screwdriver or other narrow pokey thing to align the 1/2" washer with the 1/2" shoulder of the screw. After you do this, the shoulder screw will keep pushing through the upright. Slide another 1/8" shim in from the side and poke it to align with the shoulder screw (Figure 27.4).
Step 27.5: Install a lockwasher, then a nut, on the ends of the shoulder bolts
A normal 3/8" washer can't be used here because it is too big in diameter. We are only trying to fasten the inner bearing races together so the whole thing spins smoothly. Tighten a 3/8"-16 nut against the lockwasher until it flattens out against the inner bearing race, then tighten another 1/4 turn.
The whole assembly should now be able to pivot freely on the bearings.
Step 27.6:Install the other wheel!
Don't forget, no matter which wheel you started with, do the other one too!
Step 28: Step 28: Make and Mount the Steering Tie Rods
Parts Required:
- 1/4"-28 B7 class threaded rod, 3ft
- 1/4"-28 threaded shielded ball joint linkages, McMaster P/N 6058K25, QTY 4
- 1/4"-28 regular hex nuts, QTY 8
- Hacksaw or abrasive cutting disk
- Needlenose pliers
- Adjustable wrench
- File or sander
Look inside the McMaster shipping tube. Are you sure it's empty? If you ordered the BOM, then the threaded rod would have come in the shipping tube, buried under the 80/20!
These ball joint linkages are only available in 1/4"-28 fine thread. There is literally nothing else on this vehicle that uses 1/4"-28, so you might want to just run to the hardware store and get some one-off screws this time around. You will need at least 8 1/4"-28 nuts and 1/4" washers.
Step 28.2: Mark out two 8.75" lengths on the threaded rod and cut with a saw or grinding wheel
The two lengths you need are 8.75" +/- 1/16 with preference towards minus. A hacksaw is probably the best way to make these cuts. DO NOT use a bolt cutter! Regular pinch-action bolt cutters will destroy the thread so much that you will not be able to use it again.
Step 28.3: Clean up the ends of the threaded rod with a file or sander.
The end of the threaded rod will probably be all gunky from cutting. Deburr and file chamfers on the ends and check with a 1/4"-28 nut that the thread is sufficiently clean again.
Step 28.4: Place 1/4"-28 nuts at a distance of 8" apart
On both rods, roll some nuts on and make sure their outer faces are 8" apart.
Step 28.5: Thread on a linkage and tighten one end
Pick one end of a rod and thread on a ball joint link. Once the ball joint hits the nut you placed, tighten the two against eachother - hold the ball joint with pliers and tighten the 1/4"-28 nut against it. Do this for both tie rods.
Step 28.6: Install linkage on steering uprights first
Bolt the ball link's 1/4"-28 stud through the 'ears' on the uprights. Go ahead and tighten the 1/4"-28 nut fully.
Repeat this step for the other upright.
Step 28.7 and 28.8:Install a ball link on the other end and flush-tighten it through the Pitman arm
Screw on another ball link on the free end and butt it up against the nut. Do not tighten this yet. Instead, park the Pitman arm (/steering yoke) in the straight-down horizontal position. Swing the wheel attached to this tie rod up such that you can stick the 1/4"-28 stud through the Pitman arm. Either hold it with your hand or temporarily hand-tighten a nut on the other side.
Step 28.9: Fine adjust the length of the tie rod using the untightned ball link
Look at the angle of the wheel. It should not be pointed in or outwards at the front - this is called "toe angle".
To adjust the length of the tie rod, unfasten the hand tightened ball link end you put in the Pitman arm bolt hole. Thread the 1/4"-28 nut on the tie rod away from the ball link a little, then tighten the ball link into it. You're basically shortening the threaded rod little by little by putting more of the thread inside the ball link.
The nuts were deliberately placed slightly too far apart so you can do this kind of fine tuning.
Get the wheel as visually straight as you can. You may record the length between ball linkages to duplicate it immediate on the other side.
Step 28.10:Adjust other side and tighten all bolts
Once you are satisfied, tighten the ball link and the 1/4"-28 nut against eachother. Finally, tighten the ball link to the Pitman arm, this time for good.
Step 28.11: Turn Chibikart over and rejoice
The front end is off the ground!
Turn the yoke a few times and get a feel for the steering. The inside wheel should turn slightly more than the outside wheel at the limits of travel - this is fully intentional, and the geometry is called Ackermann Steering Geometry. Chibikart does not have "true" Ackermann geometry, but it is a close approximation for the wheel travel ranges it has.
Step 29: Step 29: Mount the Drive Motors
Parts Required:
- Preassembled Turnigy 5065 motors
- 1/4"-20 x 5/8" screws, QTY 8
- 1/4"-20 nuts, QTY 8. Locknuts are preferred.
- 5/32 hex wrench
- 7/16" wrench for the hex nuts, or an adjustable wrench
- Flat metal file
By this time, your stock of 5/8" screws might be running a little low. Get 8 more of them - 1/2" long screws are just barely not enough - and some nuts, too. I used some 1/4"-20 "Keps" style locknuts, but a discrete nut with lockwasher works too, as does a nylon insert nut.
Step 29.2: Insert the 1/4"-20 screws through the motor mounting flange
There should be just enough space to slip the head of the bolt past the motor's can and into the mounting flange. Their heads should be on the motor's side of the flange, and the threads should stick out the shaft side.
Step 29.3: Hand-tighten the 1/4"-20 nuts on to secure the motor
Use 4 1/4"-20 nuts on the outside face of the motor mount and secure the motor to the mounting plate. Don't tighten these yet. The motor can move up and down slightly to tension the drive chain. Eventually, it will be tightened a little further up.
Step 29.4: File a flat onto the motor shaft
The sprockets we will be using use set screws for gripping a shaft. Without a shaft flat (or in some cases, a drilled dimple), a set screw cannot resist a substantial amount of torque before slipping and damaging the shaft.
Use a flat file to file a roughly 1/2" long flat on the shaft of the motor. Going about half a millimeter down is sufficient. You can just guide the file using the motor mounting plate. Even though it will gouge the plate a little, this is fine.
Step 29.5: Repeat for both motors
Make sure both motors are hand-tightened on their mounting plates and have a small flat on the shaft.
Step 30: Step 30: Make Bore Adapters for the Motor Sprockets and Mount Them
Parts Required:
- 12 tooth #25 sprockets. Surplus Center 1-2742-12-A or McMaster 2737T101, QTY 2
- A soda can
- Scissors or small shears
- A 1/8" hex wrench
Wait, did you say soda can? Absolutely! Soda cans are kind of miracles of modern manufacturing - over time, their walls have gotten thinner while holding the same pressure and the alloys used to make them have gotten stronger yet remain easily formable. A soda can's walls range from 0.004" (0.1mm) near the center of the can to about 0.006" (0.15mm) closer to the ends (not counting the actual caps themselves). They are consistently made in the billions each year, and we usually just toss these beautiful marvels of engineering when we're done chugging from them!
Find a soda can. We will be cutting a thin strip from one for each sprocket, coiling up the result, and stuffing it into the bore.
Step 30.3: Cut a roughly 1" long, 1/2" wide strip from the soda can near its middle
A 1 inch strip will wrap about 1.5 times around the 6mm shaft, which creates enough of an area where there is 4 soda can thicknesses total (measuring across a diameter) to keep the sprocket in line.
Curl up this strip around the shank of a screwdriver or similar. BE CAREFUL! Soda can metal edges are sharp and will cut you without provocation.
Step 30.4: Stuff the curled up strip into the sprocket bore
Make sure the end of the coil is flush with the sprocket's face. It can stick out of the hub side.
Step 30.5: Wiggle the adapted sprocket, soda can coil first, onto the motor shaft
First, align the flat you filed previously with at least one of the set screw holes. For the set screw to work properly, it has to smash into this flat.
Try literally wiggling the coiled strip on, since it may need to deform a little to slide onto the motor shaft. Once it's on, push the whole thing inwards such that the motor shaft ends up flush with the sprocket face. The coiled can strip will be mostly hidden by the mounting plate at this point.
Step 30.6: Reinstall the set screws
I recommend using a threadlocking compound in the threads this time around. Making sure once again that at least one of the set screws is over the flat, put the set screws back in but do not tighten them just yet. We need to line them up with the wheel sprocket first.
Step 30.7:Do the same for the other sprocket & motor.
Step 31: Step 31: Install the Rear Wheels
Parts Required:
- Rear wheel assemblies
- Adjustable Wrench
- 1/8" hex wrench for the sprocket set screws
- Needlenose pliers
Since we will be putting the wheel right against the spacer, it can stay on.
Step 31.2: Slide on the rear wheel, sprocket facing inwards, and tighten the bolt
You may need some needlenose pliers (or a straight 9/16' wrench) to hold onto the head of the bolt on the inside of the RMMM plates.
Step 31.3: Align the motor sprocket
The reason you shouldn't have tightened the motor sprockets before is because the sprockets need to be aligned vertically in order for the chain to not jump and pop off. Pry at the sprocket with a screwdriver or similar tool until their inside faces are flush. The sprockets are not the same thickness, so the outer faces will be slightly offset.
Tighten the motor set screws fully now.
Step 31.4: Finish the other side.
Bolt the other wheel on and tighten the other set screws.
Chibikart has officially reached criticality. In nuclear engineering and particle physics, that's when a nuclear reaction becomes self-sustaining and you're about to get totally boned, but for vehicle builds, it is when they can fully support their own weight.
You can probably go joyride this frame right now as a scooter! Try it - it's kind of fun.
Step 32: Step 32: Install the Brake Bodies and Route the Cables
Parts Required:
- Brake body assemblies from Step 7
- 6mm Barrel Adjusters, QTY 2
- 4 foot brake cable with sleeve and 7mm nipple, QTY 2
- 1/4"-20 x 1 screw or hex head bolt, QTY 2
- 1/4"-20 nuts, locknut preferred. QTY 2
- 1/4" ID, 1/16" thick nylon washers, QTY 6
- M6 x 1 nut, QTY 2
- Compression spring, 1/4" to 3/8" rod diameter x 2" long, as stiff as possible
- Adjustable wrench
- Bike cable cutters or cable shears
Hopefully you have collected the major brake parts listed in the BOM from a bike shop or the Internets. You will need 2 sections of cable with 2 nippled ends.
The long 1/4"-20 screws are for forming the pin joint that the brake mechanism swings upon. Using a nylon insert nut is recommend this time, since their prevailing torque (friction) means you can finely tune how sloppy the mechanism is.
I had two compression springs from a band brake accessories kit, but your hardware store should have small compression springs. The critical dimension is 2" length. The firmer the spring is, the more force the brake pedal will take to depress (But keep in mind we are still talking single-digit pounds). The coil should also fit over a 1/4" shaft - that's the outer dimension of the barrel adjusters. Otherwise, McMaster p/n 9657K387 is acceptable.
Step 32.2 and 32.3: Assemble the brake bodies onto the motor mounts
Use 2 nylon washers between the brake body and the motor mounting plate's little tab, and one between the head of the screw and the brake body. There is no orientation of the screw that is preferable - pick the one which is easier for you to assemble. Tighten the nylon locknut until the mechanism can swing freely, but has very little side-to-side slop. Let's say < 1/32" is the threshold.
Step 32.4 and 32.5: Cut the brake cable sleeve (just the sleeve) to length
You must have real cable shears or some other method of slicing a wound steel brake cable sleeve cleanly, like a Dremel with cutting disc. Diagonal cutters and wire cutters will not work.
Cut one 22" length of cable and one 33". These lengths are essentially all arbitrary and represent what I determined to be a good visual compromise between floppiness and a straight line. If you have a cable sleeve that is longer than 4.5-5 feet, you can just cut it in the middle somewhere approximating these lengths. A 4 foot sleeve is not sufficient to split in two.
If your bike shop gave you those little crimpable endcaps, stick one on the cut end of the cable sleeve. You may also need a nail, tiny screwdriver, or other sharp pokey thing to open up the cable passage again, after the cutting action.
Step 32.6: Mount the brake cables at both ends
The shorter sleeve is for the left side and the longer is for the right. Take a barrel adjuster and put it on one end of the short sleeve.
Insert the barrel adjuster into the outer hole on the brake bodies, and thread the M6 nut onto the other side. See Figure 32.8 for the arrangement.
Take the other end of the cable and stuff it into the brake cable holder on the brake pedal mount. Do the same for the other side.
Step 32.7: Slip the compression spring onto the brake cable and keep it close to the nipple
The cable has to go in loose-end first, so everything that it has to skewer has to be on it already.
Step 32.8: Thread the Brake Cable through the sleeves
This step might take a little prodding because you are literally pushing a noodle, but the sleeve should prevent the cable from bunching.
Step 32.9: Push the 7mm nipple into the circular slot and wedge the compression spring in between the barrel adjuster and the motor mount
Pretty self explanatory. The circular cutout on the motor mount is designed to hold the nipple end exactly. It may take some plier-pushing.
Step 32.10: Pull the cable all the way through on the other end, threading it through the anchor bolts.
You might actually have done this already in conjunction with 32.8, but if you did not thread it through the cross holes in the anchor bolts, loop it back and do so. Pulling on the cable afterwards should immediately unkink the loop.
Step 32.11:While keeping some tension on the cables, tighten each anchor bolt
Don't pull hard enough on the cable to start moving the mechanism on other side! Just enough such that you take up the loose slack.
Keep the pedal itself butted up against the stop bolt while you do this - that will ensure the springs keep the pedal tensed up. Tighten both bolts onto their cables, keeping your tension consistent between them.
Step 32.12: Cut off the excess cable
Cut the cable off about 4" past the anchor bolt such that it's long enough to grab in the future if needed, but is not flopping everywhere. If your bike shop gave you "aglets" to crimp onto the ends, do so. This prevents stabby-cable syndrome and the ends fraying.
Step 32.13: Test the brakes
Gently push on the brake pedal and observe both mechanisms for movement. They should start moving at roughly the same time. If not, then you need to adjust the tension of the lagging side. Untighten the two M6 nuts on that side's barrel adjuster and unscrew the adjuster a little (making it stick further out of its mounting hole). Do this incrementally and stop when the movements are essentially equal.
With about 10 pounds of pressure on the pedal, the motors should be nearly impossible to turn by hand.
Step 33: Step 33: Install the Drive Chains
Parts Required:
- ANSI #25 chain, at least 2 feet (A box is specified in the surplus center BOM)
- #25 Master Link (Surplus Center BOM or McMaster 6261K108
- Chain breaker tool (local, or Surplus Center 14-1037)
- Needle-nose pliers
Step 33.1: Gather your equipment
The chain breaker is a bit of a special piece of equipment. Usually sold for about $20 at good hardware stores, the bike shop is bound to have one they might let you use if you don't want to get one. They might even sell them.
The concept of a chain breaker is fairly simple. It grips the outer plates of a riveted roller chain and lets you use a screw mechanism to force the pin out of the hole, thus freeing the chain.
#25 chain is commonly found on small vehicles like scooters and mini-bikes (and some lawn mowers, apparently), but not for bikes. Bike chain is in the #40 family, or 1/2" pitch between links.
Step 33.2: Measure the length of chain needed
With the motor in its lowest position, wrap a length of chain around both sprockets and count the closest integer number of outer links needed for the chains to join. Basically, a master link supplies a removable outer link. I counter 19 outer links ("pitches"). There will be an outer link which, if only it could be removed, could expose an inner link which the master link can then connect.
Step 33.3 and 33.4: Mark the chain and break it
You have to push both pins out of one side plate in order to break the chain fully, so each break actually involves two actuations of the breaker.
Figure 33.4 shows what a properly broken chain looks like. If any of the inner plates are bent, use needlenose pliers to straighten them out - if the plates are bent outwards, the master link might not be able to connect across them.
Step 33.5: Master link training, part 1
If you haven't installed and uninstalled master links, you should practice a few times!
The master link comes in 3 parts: a removable plate, a permanently pinned plate (the pins are pressed into it), and a retaining clip. They are all small and annoying parts that you will kick yourself if you drop.
First, slip the permanently pinned plate into the inner links that form the ends of the chain.
Step 33.6: Master link training, part 2
Drop the removable plate over the exposed pins and make sure the little groove is exposed. If the plate does not sit below the groove, then the inner links might have been damaged from the breaking process and will need to be squeezed back into shape.
Step 33.7: Master link training, part 3
The retaining clip has a section where it can drop over the pins, and a section it snaps into. Slide the clip on from the side - the chain must be in a "bending" region to do this, since you can't really get at the end to push it sideways if the chain is straight.
Step 33.8: Master link training, part 4
Use fine needlenose pliers to push on the round end of the clip with one jaw while bracing the other jaw on one of the pins. The clip should seat into the groove with a firm pop as you squeeze the plier handles.
To remove the clip, push on the open end of the clip with one jaw while bracing the other against a pin.
Get good at this because...
Step 33.9: Install the master link onto the drive chain after it is in place
Wrap the chain and sling the two ends on the motor sprocket so you can easily access it from the top. Now pop in a master link. You can face it in either direction - I found it much easier to insert the pinned plate from the outside.
Step 33.10: Fully tighten the motor
Now you can tighten the four motor bolts. Gently lift up on the motor - enough to take the slack of the chain and no more (do not pry it upwards - the chain will be too tight). Then tighten the motor bolts one at a time.
Once you tighten one, you can let go of the motor to tighten the rest.
Repeat this process, chain included, for the other side.
Step 33.11: Prepare for the rolling frame test
Once you have both chains hooked up, you should be able to test the brakes. Roll Chibikart by hand slowly across the floor and hit the pedal while it's moving. Both wheels should engage at the same time. If one engages signficantly earlier, then follow the instructions in Step 32 to reduce the slack of the laggy one.
Step 34: Step 34: Install the Seat and Perform Rolling Frame Test
Parts Required:
- Assembled seat on mounts, from Step 17
- 1/4"-20 x 1/2" or 5/8" long screws
- Assembled frame
- 5/32" hex wrench
- Possibly a helping hand or two to assist with lowering the seat into the mounts
Find some left over 1/2" or 5/8" screws and the seat mount. Basically, the procedure will be mounting one of the rails via its end-tapped holes first, then lowering it down and fastening the others.
Step 34.2: Install one screw into the back seat rail, right side
Step 34.3: Insert a screw into the same rail on the left side
This should let the seat pivot up and down.
Step 34.4: Move the front two seat mount riser plates forward until they line up with the end-tapped holes in the front rail, and fully tighten all screws.
Insert screws on both sides of the front rail. Fully tighten both seat mount riser plates to the frame, since they should be in this exact position later.
You are now ready for...
Step 34.5: Rolling frame test
Get a friend to push you around looking all silly. Test that the brakes can stop the vehicle - start gently, then progress to harder and harder stops. Try to avoid locking up the rear wheels, because that will grind flat spots into the tread like a scooter wheel. This would make the ride more unpleasant...
Take a breather and clean your workspace. It's time to start wiring up!
Step 35: Step 35: First Electronics Work - Mounting Components
We will be working with batteries and 24v electric power systems. Common electrical work sense must be applied here: NO jewelry, watches, rings, etc. must be worn while you are working around things which can apply electricity to them. Use safety glasses when solderign to prevent MOLTEN SOLDER BLOBS FROM GETTING IN YOUR EYES. Do not eat the solder, even if it's lead free.
All of these parts are in the McMaster BOM or have otherwise been described in Step 3.
Parts Required:
- 24v 250W Jasontrollers, QTY 2
- K2 Energy K2B12V7EB 12.6v, 6.6Ah lithium ion battery modules, QTY 2
- 6-position, 3/8" spacing terminal block with #6 screws
- 12" Hook-and-loop nylon straps, QTY 4
- AGU inline fuse holder, audio style, with 30A or greater AGU fuse
- Bottom plate
- #10-32 x 1/2" button head cap screws
- #10-32 nuts
- 1/8" hex wrench for #10 screws
- Flush cutters
- #9 drill bit for #10 clearance drilling
Step 35.1: Collect the parts
It's a new beginning!
The Jasontrollers I used are "from stock"... I already had them. This is why they have some pre-appended wires. Yours will likely have the same kind of plastic connector shells as the rest of the small wires coming from it.
I decided to get a box of #10-32 screws with the rest of the McMasterables. #10 is the 'standard size' for the rest of the mounting screws because it fits most of the mounting holes, but you can use whatever is lying around.
Make sure the bottom plate is in the orientation shown. Narrow end with the cutouts pointing up, and the little cutouts from the bottom edge are biased towards the right.
Step 35.2: Identify the wires you need on the Jasontroller
These things come with a whole mess of wires because they are designed to be swap-ins for a commercial electric bicycle. There's lots of random electric bike things like cruise control and horns and "test motor" and whatnot, which we do not care about. There are 3 wire bunches which are critical:
- Power inputs. The thick black wire is ground. The red is main power input, and the yellow wire is controller logic power. Logic power should be tied to red, so if you are soldering things, these go to the same junction eventually.
- Throttle input. The skinny red, black, and green wire on the end of a 3-pin flat connector
- Motor output wires. These are the large blue, green, and yellow wires with banana plug things on the end.
Give it a haircut very carefully using small flush cutters. Twist the 3 important bundles together so you don't accidentally cut one of them! If you do, you might need to open up the controller and resolder it...
Step 35.4: Drill out the terminal block holes, if needed
Some of these terminal blocks are designed for #10 screws, but others are not. I got one which isn't, so I elected to just drill the holes out using a #9 drill bit (0.1960").
Step 35.5: Mount the terminal block and fuse holder
The bottom plate has slots on one side to accomodate different sizes of terminal blocks and fuse holders. Use the #10 screws and nuts to fasten these two components down.
Step 35.6: Prepare the battery mounting area
The 8 little slots in the bottom plate are for threading the Velcro cinch straps through. The strap should start out under the plate, then the Velcro end should emerge through the closed slots in the middle.
It is a little easier if you feed all 4 straps through first. I did them one at a time, so I had to keep flipping the plate over.
Step 35.7: Finish mounting batteries
Face the battery terminals towards the back (the narrower end with the cutouts) and with them oriented close to eachother, then close the cinch straps over them. You will find that the Velcro straps need to stretch alot to get around the battery. This is on purpose, since they do indeed stretch alot.
Make sure the batteries are roughly in line. The Velcro will let them shift around some after mounting - this is okay.
Step 35.8: Label the terminal block
All of the wiring will come off this terminal block. To ensure you don't accidentally wire 5 volts to 24 volts, label the terminal block. I settled on a naming convention that is depicted in Figure 35.8. I used a labelmaker, but you can very well just scribble this on some tape. Just make sure you have all of the connections in the appropriate places.
Step 35.9: Study the Wiring Diagram
The reason for naming your terminal block is found in Figure 35.9. This is the master wiring diagram for Chibikart. It doesn't show most connectors (removable connections are implied), but is a high level block representation of what we will be constructing in the next few steps.
If the Instructasize picture is hard to read, the full size diagram is here.
Step 36: Step 36: Fabricate Battery-side Wiring
This is a critical assumption I will have to make for this Instructable, but you must know how to solder wires. Big wires. Quite well, because those big wires will be carrying currents of 30+ amperes.There are many "How to Solder" lessons, but if you are not comfortable with putting two 12-gauge wires together with solder right away, then maybe Chibikart should be a build reserved for another day.
Refer, again, to the wiring diagram in Figure 36.12 (bigger). We will be making the wiring connected to BAT+ and BAT- now.
Parts Required:
- 12 gauge "Noodle" silicone insulated wire, red and black
- Fully-insulated 1/4" Quick-disconnect Female crimp terminals for 10-12g wire, QTY 2
- W.S. Deans Ultra (or compatible) female connector, QTY 1
- 6mm Heat Shrink tubing, about 2"
- Soldering iron, 40W or above with electronics solder
- Insulated terminal crimping tool
- 3mm hex wrench
- Heat gun
Shown in the picture is a pretty typical Nice Soldering Iron, the Weller WD-1, but you can do this a regular "dumb iron" of 40W capacity or above.
Acceptable substitutes for 12 gauge noodle wire include 12 gauge automotive hookup wire ("zip cord") and 12 gauge marked speaker wire (not the plain, clear stuff - you must be able to tell wire polarity apart by sight). Unacceptable substitutes include house wire or any solid or coarsely-stranded wire! Do not use house wire - it is too brittle to stand up to constant vibrations and impacts, because houses generally do not move briskly.
The insulated crimp terminals are of the "1/4" QD" style, also called "Faston" or "Quick-connects". Because the battery has male tabs, these must be female ends. I've included some bags of each type we need to use in the McMaster BOM, but this type can also be found in hardware stores or Home Depot.
The solder joints we will be making are pretty large, so keep your temp-controlled soldering station on 800F (420C) or your plug-in iron spooled up and ready.
Step 36.2: Cut a 8" red and 18" black length of 12Ga wire and crimp a 1/4" QD female connector on one end
There are many different ways people get around having a crimper, but I find that having a crimper is the best way.
Regular diagonal cutter crimps do not hold well at all, especially on finely-stranded noodle wire. For large terminals, I used to mash them in a vise.
Step 36.3: Strip approx. 3/8" of the red wire and clamp it in the fuse holder
Take off the "cap" on the fuse holder and thread the wire through. Make sure you use the end closest to the battery terminals!
Step 36.4: Connect the red wire to the + terminal of the right side battery. Also attach the black wire to the - terminal of the left battery.
It's good to organize your wire as you go along - I'm using some mini zip ties to keep the BAT wires together.
Step 36.5: Cut a 4" length of red wire and clamp it in the other side of the fuse holder
Trim both red and black wires to the same length when you're done - just cut down the longer one.
Step 36.6: Prepare a female Deans connector
Slip two 6mm heat shrink chunks (1/2" long is fine) onto the red and black wires, and keep them well away from the ends. Next strip and tin the ends of the wires about 1/4" long.
Epicly tin these - go beyond just flowing through the strands, but actually make a blob. The way to solder Deans well is blob.
Step 37.7: Tin the Deans connector tabs
Drop some solder on the tabs - make a little convex dome of solder. The goal of the next step will be...
Step 37.8 and 37.9: Melt the pre-tinned blobs together
Use helping hands to suspend the Deans terminal and the wires together.
The positive terminal of a Deans connector is the vertical tab if the connector is lying flat on a surface. Usually you attach the wire to the inside of the tab, but these wires are large, so doing it on the inside will risk shorting across the tabs, so we do it outside.
Tin the iron for good heat conduction, but put a little extra solder on (doing these solid blocky connections just involves alot of brute force heat dumping). The best way to get a good joint is to lay the iron tip flat across both the Deans tab and your wire - the blobs will meld together hopefully instantly.
Your iron may need 4-5 seconds to melt the blobs if it is not high enough wattage. Do not hold the joint molten for more than 4 seconds - you risk melting the connector housing if you do so.
Step 37.10: Finish both joints
The negative wire is typically soldered to the top of the horizontal tab. The tabs are clearly biased towards an edge when you look at them end on, so it's fairly easy to tell.
Wait for the joints to cool down, and...
Step 37.11: Slip the heat shrink over both joints and shrink them
Push the heat shrink all the way to the connector face and shrink that portion first. Use a heat gun on moderate (400 to 500F) heat - too hot can damage heat shrink as well as harm the connector housing. This should take less than 3 seconds.
Acceptable Deviation: You may really use any polarized (polarized!!) connector rated to 30 amps you feel like - Anderson Powerpoles and XT60s are typical other options for these small vehicles. Do not use Tamiya (r/c car) connectors - they will not carry anything near the currents we need. The rest of this Instructable will keep using Deans connectors - but if you have your own in mind, substitute at will!
Step 37: Step 37: Fabricate Power Switch Harness
Parts Required:
- 12 gauge Noodle wire or similar
- 5/16" stud ring terminal for 10-12 gauge wire
- #6 stud spade terminal for 10-12 gauge wire
- Wire crimper
- Phillips #2 screwdriver for the terminal block
These two connectors are kind of special, so you may not be able to find them just anywhere (but they are in the McMaster BOM!). One is an oversize ring terminal for hooking up 10-12 gauge wire to the big power switch terminals. Typically you find these made for 8 or 4 gauge wire.
The other one is a "spade" terminal specifically designed to fit snug into terminal blocks. Regular spade terminals for this size wire are generally too wide for the 3/8" compact terminal block I specified. You can elect to sand or grind down a normal 10-12ga spade terminal if needed.
Cut two lengths of wire, each about 18" long. I decided to use a random length of stranded 12ga copper wire instead of more of the nice "Noodle" wire - and because it was a different color to specifically identify the switch wire. This is, needless to say, not required.
Step 37.2: Crimp the ring terminals to one end of each wire, and the spade terminals to the other.
Step 37.3: Arrange the wires like shown in Figure 37.2, to the terminals labled "SW".
You'll need to fold over one wire such that it crosses over the terminal block. The rings on the other end will end up about 1.5 to 2" apart.
Step 38: Step 38: Fabricate Vehicle-side Power Wiring
Parts Required:
- 12 gauge noodle wire
- Deans male connector, QTY 1
- About 1" of heat shrink
- #6 spade terminals for 10-12 gauge wire, QTY 2
- 1/4" QD Female fully-insulated crimp terminals, QTY 2
- Wire crimper
- Phillips #2 screwdriver
The male Deans works the same as the female - the vertical tab when the connector body is laying flat on the table is positive. Insulate both solder joints with heat shrink (slip it on before soldering, keep it well away, then slip it over the joint once cool).
Step 38.2: Fabricate an approx. 6 inch wire that is terminated with 1/4" QD female connectors on both ends
This is the "bridge" between the two batteries that puts them in series.
Step 38.3:Attach the red spade terminal to BAT+ and the black spade terminal to BAT-
Run the new cable next to the rest and keep it retained with zip ties.
Step 38.4: Label the vehicle and battery sides of this connection
This breakable Deans link is what you will use as a charging port. The female side goes straight to the battery through a fuse - it is the only portal for power to the battery, so if anything terrible happens the fuse will blow. You should clearly label which side is vehicle power and which side is battery. I used a label maker again, but some robust tape labels will also suffice.
As you might have guessed, your future charger will have a male side Deans plug.
Step 38.5: Install the bridging wire onto the battery pack
Take the short 6" wire and bend the ends around. Slip the terminals onto the remaining + and - terminals of the two batteries.
Careful! The BATTERY connector is now energized with 24 volts. We will not be plugging this in until the very end, so keep metal things from stabbing it. Anything that can source power should always be terminated with a female side connector because the conductors are recessed.
Tape off the rest of the exposed terminal sections on the battery with some electrical tape for extra security.
Step 39: Step 39: Mount and Connect Motor Controllers
Parts Required:
- 24v 250w Jasontrollers
- #10-32 x 1/2" screws, with hex nuts
- 16 gauge noodle wire
- #6 spade crimp terminals for 10-12ga wire
- 6mm and 3mm heat shrink tubing
- 20-24 gauge hookup wire in 3 colors
- Soldering iron, 40W or greater
- Heat gun
- Wire crimper
The row of 4 holes immediately next to the batteries are for the Jasontrollers. They mount using the center holes in their mounting bases. Mount them with cable ends facing eachother (all the wires come out from the center).
Step 39.2: Make power extension leads for the Jasontrollers
Using 16 gauge wire, extend the (Red + Yellow) and Black wires each about 6 inches. The red and yellow wire on each one must be connected together!
At the end of the 6" extensions, you can combine the two 16 gauge wires and stuff them into one 12-gauge crimp terminal. Strip a little more than usual - maybe 1/2" or so, and twist the two wires together before inserting them into the terminal.
Otherwise, you could give each wire its own terminal, but this is more difficult to fit in the terminal block. The 12 gauge crimp sleeve will also be loose on a 16 gauge wire, so it is riskier. You might decide to buy 14-16 (blue sleeved) terminals instead.
Step 39.3: Connect these leads to PWR+ and PWR- on the terminal block.
I twisted the two cables together for neatness more than anything. Twisting wires can avoid EM interference (and prevent its broadcast), but the very sparse twists used do not contribute much to that. This is the DC power side anyway!
Step 39.4 and 39.5: Twist/join together the red, green, and black signal wires from each controller.
Both controllers will be receiving the same signal, so twist the signals together .
Step 39.6: Make 6-8 inch signal wire extenders from hookup wire
You will now need to break out some stranded hookup wire. This can be scrounged from just about anywhere - about 6 to 8 inches of #20-24 wire will work. Try to make it 3 colors so each of the 3 throttle connections has its own. Otherwise, make sure you label the wires at both ends.
Twist the wires together along the length of the stripped section to make soldering easier.
If you have small (3mm) heat shrink tube, use it on these joints. Otherwise, use electrical tape.
Step 39.7: Hook up the extended throttle signal wires to the terminal block
Red to 5v, Green to SIG, and Black to GND. Or replace with your choice of colors.
These wires are small enough that jamming them under the screw heads is enough. If you want more robustness, 22-26Ga wiring terminals are included in the BOM, so you can use those instead. I went ahead and bare-wired it.
Step 39.8: Inspect your work
Figure 39.8 shows the state of the "electronics deck" as completed. Make sure your wires are well-secured with zip ties. This whole unit will drop into the frame in one piece!
Step 40: Step 40: Install the Power Switch and Throttle Pedal
Parts Required:
- Hella or generic Hella-style key switch with 5/16" studs
- Hall foot pedal throttle (TNCScooters THR-101124)
- #10-32 x 1/2" bolts and nuts
- Adjustable wrench
- 1/8" hex wrench
The foot pedal is something which took me a LONG time to find - I was going to make a custom pedal for the first Chibikart, but luckily I was able to find a vendor!
The bolt circle on the switch mount has both a real Hella and fake knockoff Hella circle. The vertical set is for the generic type, and the horizontal for the real one.
Step 40.2: Remove the seat
Yes, take it back off. Undo the 4 screws and set the seat aside - it will be much easier to work on the electronics without that thing there.
Step 40.3: Mount the power switch
Using 2 #10 bolts in the appropriate holes. Tighten these fully.
Step 40.4: Mount the throttle pedal
While I designed the holes in the frame to use 1/4" screws, I've found that the actual punched size of those throttle pedal holes is so inconsistent it's safer to use #10 screws!
Talk about quality. Tighten all of these screws fully.
Step 40.5: Run the throttle cable towards the back of the frame using the 80/20 slot as a wire raceway
Cool, huh? 80/20 is great for doing this kind of stuff. Use zip ties or electrical tape to keep the wire in the slots - once at the front and once at the back.
Step 41: Step 41: Install the Electronics Deck Into the Frame
Parts Required:
- Assembled electronics deck
- 1/4"-20 x 3/8" button head socket cap screws
- 5/32" hex wrench
- Adjustable wrench
- Small screwdriver for poking 80/20 nuts
Lay the frame on its back, making sure to not drop it on the steering yoke.
Step 41.2:Position the electronics deck, component side down, between the corner plates
It's almost like I designed it to be there or something.
Time to break out the remaining 1/4"-20 x 3/8" screws...
Step 41.3: Using a small pokey device, arrange the 80/20 nuts underneath the holes.
Notice that not all of the holes are being used. Go with an "every-other-one" type of layout. I decided that it was sufficient to do this because otherwise the number of 80/20 nuts was getting unmanageable (and I was...uhhh... running out.)
Step 41.4: Insert all the 1/4"-20 x 3/8" screws first before tightening them
If you insert and tighten one by one, you could bias the plate towards one rail's preferred orientation. The holes are loose fits, but not that loose! Insert all of the screws and tighten a few turns. Once all of them are in, then go back and fully tighten each one.
Step 41.5: Turn the frame back over and hook up the power switch
The big ring terminals go on the big studs of the Hella switch. Tighten until the lockwasher on the Hella switch flattens out.
Step 41.6: Fully insulate the terminals of the switch with electrical tape
Those big metal terminals are begging for something to short right across them. They must be insulated - wrap electrical tape around them until no more metal is visible.
Step 42: Step 42: Finish Wiring Harness Details
Parts Required:
- 16ga noodle wire
- 6mm heat shrink
- Soldering iron, 40W or greater
- Phillips #2 screwdriver
- Heat gun
Red to 5V, White to SIG, and Black to GND/RET.
Step 41.2 through 42.4: Make extension wires for the motor leads if needed
I noticed that my Jasontrollers did not have wires long enough to reach the motors by about an inch! That was a bit embarassing.
Basically what I did to fix it was to cut each motor output wire somewhere in the middle and splice in a 3" chunk of noodle wire. You might need to do the same, unless Jasontrollers magically come with longer wires now.
Step 42.4: Connect the motors
The weird connectors on the motor wire outputs are supposed to be for "banana plugs", but the 4mm bullet connectors on the turnigy motors are the same diameter. Just cram the connectors on the motors in, and you're all set. It's even pre-insulated. If you really feel the need, you can use a set of matching female bullet connectors.
At this point, the colors do not matter. We will find out later which way the motors spin, and if need be, swap two of the connections.
Step 42.5: Secure the rest of the new wiring
Zip tie the motor phase wires together, but do not put a zip tie over the connectors yet since we might need to swap them.
Step 43: Step 43: Wheels-up Test
That's it. Everything in the electrical system has been hooked up, and we're ready to turn it on. Before you drop it on the ground and fly off, though, we must do a "wheels up" sanity check to make sure, for instance, that the wheels are spinning the right way...
Step 43.1: Put the rear wheels up on blocks
Find something - just about anything will work, since this thing is so low - and prop the rear wheels off the ground.
Step 43.2: Plug in the BATTERY and VEHICLE PWR connector
You have now connected the battery to the system. It's not live yet, because...
Step 43.3: Flip the Hella switch forward
Did the fuse blow?
If it did not, CONGRATULATIONS! The system is now powered up.
If it DID then the most likely explanation is that you wired something backwards. Go back and inspect every power wire and make sure reds go to positives and blacks go to negatives! The MOSFET switches in these controllers conduct backwards freely, so if the polarity is incorrect, it is a dead short.
Step 43.4: Gently tap on the throttle and observe the motor behavior
Watch the demonstration video here.
The sensorless starting routine of the controllers will cause the motors to shudder suddenly, then start spinning in one direction.
If nothing happens, verify that the throttle is connected correctly: 5v to red, SIG to white, RET/GND to black, and correct on the other side also.
If this is correct, then use a voltmeter to double check that the throttle is putting out a signal between approximately 0.8 and 4.1 volts. It may be a little out of this range, but it should be smoothly varying with the depth you push the pedal.
Also check that the 5v terminal is actually 5v, and no less than approx. 4.85 volts. Any less could indicate a failure of the throttle (shorted) or some other unusual load.
Are the motors spinning in the correct direction?
If one of your motors (or both...) is spinning backwards, don't worry! Pick any two of the motor wires and swap them.
Yup. That's it. Sensorless drive is nice like that.
If your system passes the wheels-up test, it's time to remount the seat! Turn the power switch off.
Take the vehicle down from the blocks and remount the seat similar to the procedure in Step 34.
If there is no response and all the wiring is correct, the problem is beyond the scope of this instructable. Sorry :(
Step 44: Completion and Ground Testing
I assume you took off immediately after Step 43 and began zipping around whatever space you were working in.... or perhaps you tried and it just kind of stuttered at the beginning and never quite went. That's because
CHIBIKART MUST BE ROLL-STARTED!
You've uncovered one of the biggest weaknesses of sensorless motor drive - the startup! Chibikart must be rolling forward slowly - about 2mph - before the controllers will positively pick up the motors.
Why does this happen? A multitude of reasons, some of which are covered in the Scootertructable. The biggest reason is that in regular sensorless drive, the controller pulses 2 out of the 3 motor wires and observes the voltage behavior on the 3rd, undriven wire. It uses this reading - either a positive-going or negative-going voltage - to determine which winding to swich next. This works well if the motor is reasonably normal - the resistance and inductance of the windings is such that you can obtain a high enough voltage to detect.
The average R/C outrunner is purposefully wound for very low R and L, because they are meant to run at high speeds. Repurposing these things for vehicles is often a delicate task of making sure your controller can handle the motors. Even sensored controllers, which have absolute position information of the rotor at all times, can be stymied by the high pulse currents these motors can draw (R essentially dictates how much current the motor can draw and L dictates how fast it can start doing so).
The Jasontrollers have an internal current limiting circuit set to about 25 amps. The fact of the matter is, 25 amps into a typical R/C outrunner of this size does not create enough torque, nor does it effect a signficant change in voltage in the windings. Therefore, the Jasontrollers either 1. cannot detect the result of its startup pulse, or 2. the startup pulse is not enough to move the motor at all, generating no voltage pulse whatsoever!
Why did you pick sensorless, then?!
As covered at the very beginning, I was designing solely for simplicity. Adding Hall Effect magnet sensors to a motor which you do not have the winding information (which coil is on which phase) about is extremely difficult and requires alot of tuning. The sensors also have to be precisely placed as well as wired up to the controller. I can literally add another 20 steps just on configuring sensors.
Even worse, the optimal position of the sensors changes as the motor draws different amount of current and changes with different speeds. A robust sensorless startup and running algorithm is much better, but also much harder, than a simple state-commutated sensored controller.
In the end, I decided the low cost and simplicity of the Jasontroller was worth the roll start you had to give to yourself (or to a friend). Chibikart1 has to do this too, so it's not just because this is a more public build.
Tips for driving your Chibikart
- Don't jump on and just floor it - it will be a little anticlimactic.
- Use your left leg to shove off while you are throttling up.
- Gently ease in the throttle at the start. Once the vehicle is moving, you can pretty much do whatever.
- Practice "hump starting". This is, unfortunately, exactly what it sounds like. Perform a moderately forceful in-place hip thrust as you ease in the throttle. As you thrust forward, your body's inertia will push Chibikart forwards - just enough for the controller to pick up.
Step 45: Care and Feeding of Your Chibikart
CHARGING BATTERIES
Charging your Chibikart is fairly simple.
Single purpose chargers
I specified a 24v battery charger in the BOM, and you probably have it by now. These 24v chargers typically come with either alligator clips or "XLR" connectors, which are typically used for microphones and audio equipment. Strange.
There isn't much I can recommend besides cutting off the existing connector and adding your own. Figure 45.2 and 45.3 are relevant to "single purpose" chargers - you might need to check the polarity of the wires if they are not indicated outwardly.
R/C Multichargers
These are handy utensils to have. They can charge about every type of battery (Lithium of all flavors, nickel, and lead), and start from $25 for the basic ones which can handle up to 6 lithium cells and start from about $40 for the ones which can handle 8 and up. I have a 1010B+ that I've used for several years, and I love it. A good 8 cell charger which will handle the 24v pack of Chibikart is the Accucel 8.
BATTERY MAINTENANCE
These 12v bricks are pretty self-contained, but over time, their charge levels could start drifting apart. You will typically experience this as a sudden loss of power even though Hey, I swear I Just Charged This Thing. The batteries have internal safety cutoff boards that will make it "faint" if the voltage on the pack goes under approximate 10 volts.
To wake them back up and refresh their HP, you have to use a 12V charger and individually charge each battery. This is when having the multicharger will come in super handy.
The Jasontrollers have an internal safety cutoff of 21 volts, so they will hypothetically prevent the batteries from 'fainting'. It is likely that the vehicle's performance will become unacceptably dull before this point anyway.
MECHANICAL MAINTENANCE
There aren't many mechanical things to go wrong on Chibikart besides the brakes and drive chain. The chain should, of course, be regularly oiled with bike chain oil or similar. If it gets too floppy, untighten the motor screws and slide the motor up to retension. The brake pads will eventually need replacing, but so do bike brakes, so run back to the bike shop.
Do not operate Chibikart in the rain or anywhere that is wet - the controllers and battery are pretty well sealed, the entire rest of the electrical system is not. The danger isn't so much shock hazard (it's only 24v) as accelerated galvanic corrosion of the metal conductors.
OPERATIONAL SAFETY
While Chibikart fits well indoors, be well aware that it is made of metal and has sharp edges. It's at a great height to shear someone's ankle directly. Be careful when operating it around any people. It will dent walls and floorboards and chances are the owner of your impromptu racing venue will be unhappy with that.
Step 46: Conclusions and Epic Link Dump
I hope everyone has found this Instructable a great help to starting in the world of building mechanical projects or furthering their existing ones!
This has been a veritable BOOK (seriously, shorter books have been written). Writing a comprehensive how-to has never really been my style, as I usually try to encourage exploratory learning and finding it out yourself. However, this build of Chibikart was my chance to combine that style of "guidebook" writing with an immediate application. I hope it has turned out well. Many parts were left deliberately vague, and parts some times magically materialized, to encourage filling in the gaps.
My design mistakes were included in the open, as part of instructions (with advice to avoid them, of course), to show that even if you think you know what you're doing with this super simple thing, there are always things which can come up that you haven't thought of before. That's true for any engineering project, no matter the magnitude, and it's something that beginning builders especially have to keep in mind - setbacks are a regularly occurring thing and it will probably not work right the first time you do it unless you know everything about it already.
I don't intend on cheapening the build any further, nor really making drastic changes to this design. Once again, it is my hope not to see a thousand Chibikart clones flying around at Maker Faires, as hilarious as that would be, but for the reader (you) to use the concepts presented in this Instructable to build your own wacky, possibly small-form-factor vehicle. The resources for parts and fabrication methods will be the most beneficial to those who can apply them on their own.
LINK DUMP AND RESOURCES
I always include this at the end of my Instructables, and this is no different! This is a general resources list - not all of these are for vehicle parts, some are for robots too.
First off, here's Chibikart 1 and the Democratic People's Republic of Chibikart's ("this Chibikart's") static pages on my site.
Parts
HobbyKing Distributor of a mind-boggling amount of import-class R/C model motors, batteries, chargers, controllers, etc.
McMaster-Carr Best online source for industrial, mechanical, and hardware components.
Digi-Key Like McMaster... but only for electronic components!
Big Blue Saw Custom fabricated parts designed by you. Upload DXF files and get instant quotes.
ShapeWays Custom 3d printed parts to BBS's 2D waterjet and laser parts. General turnaround time of 10 days, and real cheap!
Kelly Controller Specialized EV controllers and hardware. Want an upgrade path for Chibikart? Check out the KBS line.
Monster Scooter Parts Imported small EV parts dealer - has just about every wheel, brake, motor, throttle, etc. you can think of.
TNC Scooters Similar market space to MSP, but they have the rare foot pedal throttle too.
HobbyPartz A hobby distributor similar to Hobbyking, but with more selection in the U.S....because they're IN the U.S.!
Robot Marketplace General vendor of most robot parts - motors, controllers, materials, transmission parts...
Pololu Vendor of custom-designed robot parts and useful small motors, controllers gearboxes, and robot kits.
Speedy Metals My favorite Internet metals dealer when eBay can't save my day.
Online Metals Another online... metals.... place, one of the original from many years ago.
All Electronics One of the best electronics surplus sites for robot builders.
Goldmine Electronics Another good electronics surplus website
Adafruit Industries Custom open source DIY-style electronics projects and kits.
Sparkfun Electronics Essentially the same market as Adafruit, but with a much larger distribution network and product selection.
People
Many people put their projects up online in the form of build journals, logs and blog posts. I'm not counting shiny "finish product" portfolio sites here. Just the dirty, unpolished side and tales that tell it like it is. I believe that this section is in fact more valuable than the resources, because they show how different people creatively use the same parts and techniques to achieve different ends.
MIT current and alums
Charles Guan (me!) Custom EVs, combat robots, quasi-flying objects, 3d printers...
Shane Colton Custom EVs and motor controller designs, flying things
Amy Qian A very clean custom hub motor "penny farthing" bicycle, small go-kart, and several all-wooden vehicles!
Jordan Jin Stone Self-balancing skateboard and quadrotors, fashion advice
Daniel Fourie Several machine design projects from MIT
Jed Storey 4-hub-motor electric longboard!
Eli Davis Builder of Elikart, incidentally featured in its own Instructable!
Daniel Kramnik Part of the MITERS high voltage squadron; tesla coils, induction heaters, and other HV
Tyler Christensen Fusion reactors, tesla coils, and high performance audio; part of the MITERS HV Squad
Jackie Sly One of the students who was in my build-your-own-electric-rideable class, "2.00EV"
David Wise Another student in 2.00EV, he and Jackie were responsible for the Melonkart.
Bayley Wang Part of the MITERS HV Squad and also a student in 2.00EV; high power electronics, tesla coils, and overclocking.
Daniel Gonzalez Another student blog; excellent custom waterjet-frame scooter with sensored control
Victor Rodriguez A student electric scooter with sensored control and a slightly different frame approach. And LED cubes.
Other Builders
Jamison Go Part of the Georgia Tech chapter of the Collegiate Silly Vehicle League. Custom EVs with hub and non-hub motors, combat robots.
Aaron Fan Also part of the GT chapter of the CSVL. Segboards galore. Robots with strange coordinate systems.
Xo Wang Another member of the GT chapter of the CSVL. Quad-hub-motor longboard with custom everything
Adrian Tanner The BU Chapter of the CSVL. Scooters, minibikes, and custom motors!
Adam Bercu Real Life Electric Motorcycle; combat robots.
Dane Kouttron A little bit of everything. Custom polar-coordinate 3D printer. Space balloon.
Dale Heatherington One of my mentors during my earlier years, a cofounder of the legenday Hayes Microcomputer Products. Many custom and innovative robots. Ball-balancing Segway-like vehicle.
Cool sites in general
These are sites I find myself going back to alot, for whatever reason, whether it's a treasure trove of information or knowledgeable people or whatever else.
Gizmology Many great guides to parts and rule-of-thumb lessons for common engineering problems
The Machine Tool Archive A great history lesson into many classical machine manufacturers!
RoyMech In-depth scientific treatment of many engineering topics such as machine parts, power transmission, linkages...
My favorite drill and tap chart
CHIBIKART'S AUTODESK INVENTOR DESIGN FILES
I designed the whole vehicle in Autodesk Inventor 2012 software, which incidentally Autodesk will give to you for free (as in beer, not dom) if you are a student. All it takes is a .edu email or some other proof that you are doing learny things. Chibikart's DXF cut files were edited in AutoCAD Mechanical 2011.
Here are Chibikart's original Inventor files (they are hosted on my site).
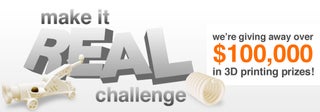
First Prize in the
Make It Real Challenge