Introduction: Creating Helmets and Armor From Videogames for Fun and Profit!
This Instructable will present my somewhat peculiar method for creating replicas of helmets and armor from video games. Admittedly I'm not the world's greatest sculptor, and to make up for my lack of skill in this area, I've devised a way to use 2D templates as guides for making complex forms as easily and symmetrically as possible.
In reading this guide, you may think that the only end result is an identical Draugr helmet from the game Skyrim. In fact, there are many methods here which are useful for creating any sort of 3D shape from shoulder pauldrons to other game helmets.
Note that this process involves some potentially dangerous chemicals and tools, so if you're looking to replicate the things seen here than please exercise caution. A respirator is mandatory for almost all steps outside of the molding process, and in some instances gloves and safety glasses are a good thing to use as well. Be careful!
The methods that follow will furnish you with not only a replica helmet or armor, but also molds from which to produce copies for sale or outfit other friends in similar costumes. Moldmaking is somewhat tricky and expensive however, so if this is your first attempt at such an endeavor, I recommend starting with smaller pieces than a helmet first.
Onto the process!
Step 1: Blueprinting and Scaling
The lovely thing about basing a project off of a video game is that a designer somewhere has gone through the immense trouble of making a beautiful 3D model for you to work from. If the game you're basing your project on happens to be available for PC, then chances are there is a modding community out there that has extracted these files and can help source some perspective still images or even the 3D model itself. (Pic 2)
For this project I'll be building the female "Ancient Nord Helmet" (also called the female Draugr helmet) from Skyrim. The models for this helmet were provided to me by a gent who mods these games, and I used the perspective screenshots in order to make 2D blueprints of the top, sides, bottom, and front/back of the helmet. (Pic 3)
There is a rather large community of costumers who also employ a method called Pepakura (essentially complex paper folding and cutting) in order to achieve very similar results using game files as a base. While this is an excellent method, I personally suck at it, hence this Instructable!
One of the questions I have received the most concerns how to scale blueprints. Recently I've found a great method for this: Print off a 1" grid onto a sheet of plotter paper, then trim out a space for your subject to stand. Photograph this as close to perpendicular as possible, then import the photograph into an image editor such as Adobe Illustrator. By scaling the image so that the 1" squares are indeed 1" in size, you can then import your blueprints over the image and find all the dimensions of your finished part! (Pic 4)
Once your blueprints are scaled, print them at full scale on a plotter. A local print shop can assist here if you don't have access to one of your own.
Step 2: Making the Base Form
Using the 2D blueprints as guides, trim out the perimeter of your shape in 1/4" MDF. Make sure to trim this where the furthest points of the outer edge of the blueprints are located. (Pic 2) For this helmet, I trimmed out the profile as well as the head-on view, then the outermost points from the upper and lower perspectives. All of these pieces of MDF were slotted and then pushed together to form a rough blocky form which was secured with wood glue. (Pics 3, 4, 5)
After letting this dry overnight, polystyrene foam is inserted into the blocky cavities. You can find this material at Home Depot (where it is pink) and LOWE'S (where it is blue). A two-inch-thick sheet works great, as you don't have to cut quite as many pieces to fill the gaps. (Pic 6)
Many different types of glue can dissolve pink foam, so be sure to test before you start gluing these blocks in. In the photo shown (Pic 1) I am using some old urethane casting resin that was past it's prime, but other water or urethane based adhesives will also work. I like Gorilla Glue personally, though you have to be sure to clamp it while it cures.
The end result is far from pretty, but don't leave yet!
Step 3: Refining the Shape
So you've got this ugly mess of foam and glue, time to pretty it up a bit. Start out with a coping saw (or hot wire if you're lucky enough to have one!) and begin to shape the foam, using the MDF spines in the block as guides. Begin by trimming along the guides themselves, then gradually start to refine the rest of the "dome" shapes. Don't worry if you accidentally take off too much, we'll be adding a bunch of filler in later steps. (Pic 2)
Once you've got the base form closer to the shape you like, start shaping with a disc sander to even out the lumps and jagged edges. Eventually you may want to switch to sandpaper (100 grit works nicely) to shave off smaller and smaller amounts at a time. (Pic 3)
Keep in mind that there may need to be deeper recesses carved into your piece for things like eyeholes. For this helmet, I used a dremel tool with a sanding drum to excavate cavities where the eye cutouts would eventually go. Again, don't worry about this being rough right now - things will get tightened up later on in the process. For now, we're only concerned with a rough base. (Pic 4)
Once you've got the foam and wood to where you want it, seal this little accomplishment of sculpture with acrylic or latex paint. In the following steps we'll be using spray paint as well as polyester resin fillers, and these will dissolve your polystyrene foam base. (Pic 1) Adding a couple layers of paint between these coats ensures that nothing reacts and dissolves all your hard work so far.
Step 4: Sculpting With Filler
The title of this section may seem a bit misleading. Didn't I say I suck at sculpting? Well, yes, but I'm pretty good at sanding, and thats where this method shines. You'll need a pretty large canister of Bondo or similar polyester resin filler (in this tutorial I used Evercoat's RAGE GOLD filler) as well as some fresh canisters for your respirator, lots of heavy grit sandpaper (50 and 120 grit works great), plastic trowels for your filler, and a place you don't mind turning into a giant mess with all the sanding dust.
Start out by filling any holes left from the foam process with filler, then build up an initial coat about 1/4" thick around the entire part. (Pic 1) A lot of people will say that polyester resin is a complete pain to sand; they're right, but only once its fully cured! Keep an eye on your coat of filler - at a certain point it will no longer be spreadable, but you will still be able to dent it with your fingernail. When it is at this stage, break out your 50 grit sandpaper and start shaping! The lumps disappear easily and you've got nice, even shapes. Scratched to heck and back, yes, but we'll worry about that later! (Pics 2, 3)
Repeat this process until you've got all your curves nice and smooth, and use a contour gauge to make sure the curves from the left side mirror those on the right. (Pic 4)
Step 5: Adding Details
Once your base shape is defined, its time to start adding the layers on top which will define the piece. Working in layers like this can be much easier than trying to form an entire lump of clay into the finished product.
There are two antlers which jut from the temples of this helmet, so the first step is to mark where one will come out (Pic 2). Use your blueprints as guides here to make sure this falls on the same place as the original in-game helmet - a set of bow calipers will really help with the symmetry as well. (Pic 3)
Once you've determined where these parts will be mounted, cut out a couple of recesses with a dremel tool and seal the underlying foam with more acrylic paint (Pic 4). This may seem specific to this helmet, but many other helmets from video games have crests/horns/pointy bits sticking out of them. Looking ahead to the mold making step, this would make molds and castings very difficult. The more modular you can make things, the better.
I wanted the antlers to bolt in from the sides of the helmet, so I vacuum formed small recessed blocks to serve as "plugs" for their mounting points. These were glued into place with epoxy. (Pics 5, 6)
The base of the helmet is another part that needed some additional shaping. Looking back at our blueprints, you can see the side profile has a gradual curve to it, and the underside of the helmet has a beveled edge. Adding an MDF or (as shown here) sintra block to the base will create this lip, which can then be shaped with a dremel tool to the proper bevel. (Pic 7)
In Pic 8 you can see a series of numbers placed along each inch of the lower lip. One half of the helmet was shaped first, then these numbers were added. By measuring the height at each number then transferring these measurements over to the opposite side, you can make sure that both sides of this complex shape are identical. (Pics 8, 9)
Add a bit more filler to blend these new additions into the rest of the helmet, and continue on to step 6!
Step 6: Cleaning Up the Shape
At this point, your base helmet or armor is starting to look more like the finished result, but probably is still covered in deep scratches from the 50 and 100 grit sandpaper you've been using. Get a can of "Filler Primer" from a local auto supply store and coat your sculpted piece in a few coats. I prefer the Duplicolor brand personally. This stuff sprays thick so be careful when painting as it is very easy to have runs everywhere. (Pic 1)
Let this cure overnight, then sand your part the next day using 220 or 320 grit sandpaper. You'll be able to see areas where the filler primer is filling the deeper scratches. You may need to repeat this step more than once depending on how deep some of the gouges are. (Pics 2, 3)
Step 7: Texturing
I wanted this helmet to have a very exaggerated hammered texture like it shows in the game, and the rather tedious solution I came up with was to carve each light divot out individually with a dremel tool. After this was done, the entire piece was then sanded with a 100 grit sanding sponge to blend these dents into one another. (Pics 2-4) This process took the better part of three days, and eroded a generous portion of my sanity with it.
That said, now is a good time to think about the texture your finished piece will have and how best to approach it. Keep in mind you'll be molding this later, so whatever you do to this base shape will be transferred to your final plastic castings. Stone texture paint, vinyl decals for subtle raised accents - a multitude of things should be added at this point to make your finished casting as ideal as possible.
Once you've got this base form textured, coat the entire piece with another layer of primer such as Krylon's Ruddy Brown or similar. Do not use filler primer for this step as it sprays very thick, and can fill in all the texturing you've been working on! Regular primer will be fine. (Pic 1)
Step 8: Adding Raised Details
In the previous step, you may have noticed that the hammered texture stops just shy of the eye holes and front section of the helmet. On the Skyrim modeled helmet, this area has a raised "plate" that covers the front section and surrounds the eye cutouts. No need to sculpt what will be covered over later!
My preferred material for things like this is a product called "Apoxie Sculpt" - it is a 2 part non-toxic clay that is easily smoothed with water and has around a 45 minute working time. After drying overnight, it can be sanded and smoothed to an almost glass-smooth finish.
For these raised parts around the eyes and the filigree on the back side of the helmet, start out by transferring your blueprint patterns onto the helmet and outlining the areas to be filled in with pencil (Pic 2). Always refer to your blueprints when building - for me, whenever I eyeball something is when it goes horribly wrong!
Start out by roughly filling in areas with Apoxie Sculpt. Initially it will be very soft, almost like play-doh, and you can use a serrated sculpting trowel to even out the surface into a smooth coat (Pic 6). Don't worry if things initially look very rough, the clay will stay malleable for a long time, giving you plenty of time to make adjustments. To smooth out seams or even an area out, a spray bottle followed up with a sponge works great. Apoxie Sculpt smooths very easily with water while uncured.
After the clay has started to cure slightly, you can use the backside of a domed handle (in my case, an engraving tool) to make the hammered dents in the surface of these newly sculpted bits (Pics 1, 7). If your piece is something that needs to be textured using a spraypaint method, consider sculpting areas like these before you do the final texture coat.
Step 9: Sclupting Antlers
I said earlier that a lot of the steps in this Instructable can be transferred to similar projects, but this set might be pretty specific to horned helmets. That said, the basics of sculpting with an armature may prove useful to people looking to make complex shapes without spending a ton of money on clay.
To start with, I inserted plastic plugs into the sockets on the side of the helmet where the antlers would eventually mount. The antlers themselves started out as bent pieces of sculpting wire attached to these plugs. Symmetry here is kind of a pain but the bow calipers will help here too (Pic 1).
The spikes for the antlers were added with more wire, secured in place with hot glue. These, like the helmet, will be molded later so there's no need to be concerned with durability or weight (Pic 3).
In order to keep our costs down (Apoxie Sculpt isn't cheap!) the base sculpting wire is filled out with tinfoil in order to make the thicker antler shape. This is then wrapped in more wire to give the final clay coat something to grab on to (Pic 4). Things are still bendy at this point, so make sure you've got everything symmetrical before moving on!
Once you're satisfied with the armature, start layering the horn shape with Apoxie Sculpt. Again, don't worry about everything being nice and smooth - the great thing about this process is that you can always sand things down later. Just concentrate on getting the base shape correct, then let the antlers dry for twelve hours (Pics 5-7).
Apoxie Sculpt sands brilliantly, so once its dry, start out by sanding it with 120, then 220 grit sandpaper (Pic 8). Additional details like the deeper lines in the surface or the texture at the base of the horn can be added with a dremel tool, or by layering on more Apoxie Sculpt once the piece has been shaped (Pics 9, 10).
Step 10: Last Minute Details
The last bit of detail I wanted to add were the large rivets and the "battle damage" on the helmet. For the rivets, I found some furniture tacks at Home Depot that had the same hammered texture as the rest of the helmet. Furniture tacks work wonderfully for this sort of thing and come in a myriad of different shapes (Pic 2). Since the eventual molded part will be made from solid resin, you don't need to be concerned with durability or odd materials choices. I've used stick-on googly-eyes for big fake rivets before and they work great!
Since this is a molded piece, each scrape and dent in the master sculpt will be transferred to the final casting. I decided I wanted all of the "battle damage" scars to be a part of the helmet itself, instead of carving them all out on the cast helmets after they're made (Pic 3). If you're looking for more individuality in your pieces, you may want to leave your master sculpt more clean and undamaged, and then add these details in later.
After you've got all your detailed bits finished, give your final master part a coat of primer (Pic 4), then glossy paint. This will help the mold silicone release better since its a smooth non-porous surface, and in my case it adds another light layer of texture to the final part, since I used hammered paint (Pic 1).
Step 11: Molding the Helmet (or Armor) Part 1
Mark off your seam with non-sulfur oil clay, making sure to add registration keys in the surface for the other mold half (Pic 2, 3). Registration keys are the small bumps in the clay; these were added using the back side of a paint brush handle. These ensure the two halves of the silicone mold meet up in exactly the same place every time. Start out with a thinned coat (Pic 6), gradually building up thickness until you've reached .25" to .5" of silicone around the entire section. For this helmet mold, Smooth-On's Mold Max Stroke silicone was used.
Make sure to add registration keys on the outside of the mold as well (Pic 7, 1), to align the flexible rubber mold with the rigid mold jacket which will be added later. These registration keys were poured separately, using disposable plastic cups as forms. They were made using Mold Max 30 silicone, which will bond to Mold Max Stroke, but is specifically made for pour molds. For a bit more information about brush on molds, check out the following video by Smooth-On:
Once one side of the mold is complete, repeat the process for the other half of the helmet. Remove the clay wall separating the two halves of the mold, and brush it with mold release wax or a similar product (Pic 5). Once the seam of the silicone has been waxed, move on to molding the other side of the helmet.
Step 12: Molding the Helmet (or Armor) Part 2
For my mold, I chose to make separations using 1/4" MDF to split the mold jacket into two parts (Pic 2). With a complex shape like a helmet, a one-piece mold jacket will be impossible to remove. Drill aligned holes in the MDF partitions, then join them together with wingnuts before placing this over the main seam of the mold. In order to make sure the mold jacket material doesn't flow under the halves of the MDF spine, hot glue is used to build up a barrier along the seam (Pic 3) - just make sure you don't hot glue the MDF into one piece! Also, it helps to trim the seam of the silicone mold with an exacto knife before making the mold jacket, as the brushed-on silicone edge can be jagged and uneven.
Smooth-on's Plasti-Paste is my preferred material for mold jackets (Pics 4, 1). Make sure to apply it evenly in each section before moving on. You'll want to make sure all of the mold silicone is covered by the mold jacket to avoid any registration issues.
Plasti-Paste can dry very jagged. In order to make the mold jacket easier to handle later on, use rubbing alcohol and a rag to smooth out the surface as the material cures. Make sure to only do this on the top coat, as pressing in on the mold jacket while its curing may cause some registration issues with your mold later on.
After the jacket cures, remove the master from the mold materials and re-assemble everything into one empty hollow helmet mold (Pics 5, 6).
Step 13: Antler Molding
Ok, sculpting the antlers was a weird and specific step, but this one is even more singular. In actuality, it isn't terribly different from molding the helmet itself, and there have actually been some very informative Instructables and tutorials written on how to mold antlers for taxidermy purposes.
After anchoring your sculpted antlers to a base with hot glue and some length of PVC, paint a thin coating of silicone over the entire piece and allow to cure for about 45-60 minutes before adding a follow-up coat (Pic 2). For these, I used Smooth-On's Mold Max 30 and Mold Max Stroke silicones. Build up thickness until your molds are about .25" thick all around, then allow them to cure for 24 hours (Pic 3).
The mold jacket is applied in a very similar way to the helmet, using non-sulfur clay as a barrier in place of the MDF spines (Pic 4). Allow one side to cure for at least 12 hours before making the other half of the antler mold jacket, and make sure to apply mold release wax to both surfaces to make sure you don't glue the entire mold jacket into one solid lump!
Once these have dried, remove the mold jacket then the master sculpt. Since this is a one-piece "glove" mold, you'll need to make a slice along one edge with an exacto knife in order to remove the master (Pic 6). Make sure that this cut is not along one of the seam lines of the mold jacket, as the pressure of joining the two halves back together can press it out of alignment (Pic 7).
Step 14: Casting the Parts
The video below is pretty dry, but it gets the general point across. Skip to about 4:20 to get the the relevant information, though there are some good tips about mold prep beforehand as well.
For this helmet, I used Smooth-On's ONYX urethane casting resins. Start by mixing 1/2 cup of resin (1/4 cup of part A mixed with 1/4 cup of part B) and pour it into the mold cavity, rotating it slowly by hand as the resin cures.
Repeat this process, moving the mold around to cover all areas of the inside of the helmet, until a uniform thickness of 3/16" is achieved. If some spots are a little thicker, that's fine; slushcasting is a tricky process that can take some getting used to. One helmet usually takes about 32oz of resin.
This specific helmet is also "Cold Cast." Cold casting is a process where you use metal powders mixed with the resin to make the final casting have a metallic effect. With this helmet, aluminum powder was first dusted into the mold, then sifts around to coat all the inside surfaces evenly with a thin layer of powder. After removing the cast part from the mold, the part will be a dull gray color (Pic 2). Use fine steel wool (000 gauge) to buff the surface to a metallic shine (Pic 3).
After the helmet is fully cured, remove it from the mold and trim out the areas for the mouth and eyes, as well as the neck area, using a dremel tool and hand files.
The antlers were a bit more difficult to cast. These are made with Smooth-On's 320 series resin, chosen because it cures to an off-white antler-ish color. Since some spots sit higher than the pour spot openings, these have to be cast in sections. Start out by pouring a small amount into the mold to fill the furthest areas from the pour spout with resin, then allow these sections to cure. Work in small batches and continually move the mold around in order to dislodge any air bubbles (Pic 4). After you've filled the rear section of the antlers, pour resin into the front tip and the base, then allow the casting to cure for at least an hour before demolding (Pic 5).
Trim off the pour spouts, drill 2 screw holes into the antler, then mount to your cast helmet!
Step 15: Painting and Weathering
If you've used a cold casting technique like shown here, the weathering process will be much shorter. For other types of armor and helmets not using this method, you'll need to first sand your cast part lightly with fine grit sandpaper or a sanding sponge, then paint a primer coat and base color coat of your desired choice.
Once your base coat is established, start by painting low lying areas with dark washes of acrylic paint in varying shades of brown to give a bit more definition to deeper areas. Places like the "battle damage" gash marks, as well as the seams between the helmet front plate and side filigree will benefit most from this treatment.
While an airbrush isn't absolutely essential to weathering, it can add a nice gradient to shaded areas (Pic 2).
Also in pic 2, you can make out a bit of gray powder dusted onto some areas of the helmet. This is where iron powder has been dabbed onto the surface of the helmet, mixed with a very small amount of watered down black paint to help it stick to certain areas.
To get this powder to rust quickly, use a mixture of hydrogen peroxide and lemon juice in a spray bottle (it stinks, so try not to get it on you!) then spray these areas and dab any runoff away with a paper towel. This reaction works extremely fast; you can pretty much watch the rust forming on the surface (Pics 3, 4).
Let this cure overnight, and examine the results. If necessary, knock back some areas of the rust with a bit of purple or dark red acrylic to give the weathering a little more depth (Pic 5).
Painting the antlers is a bit trickier. Ultimately you'll need to decide to go with a more realistic or a more exaggerated look to either be more faithful to reality or the game you're emulating. I started by shading in the recessed areas with dark brown (Pic 6), then gradually layering thin coats of airbrushed brown on top of this which were "scratched" away using a stiff bristle brush and warm water over the acrylic paint (Pics 7, 8).
Step 16: Enjoy!
After the weathering coats of paint on the antlers and helmet have dried overnight, clear coat the entire piece with matte clear (for the antlers) and semigloss clear (for the helmet, Pic 2) I prefer Krylon paints for clear, but always test to make sure that your clear coat won't react with any of your base coat layers. Don't worry if the initial coat of clear changes the base colors of your paint and weathering slightly; once everything is cured it will go back to its original shade.
Another 24 hours of dry time and you can assemble your finished helmet. Enjoy!
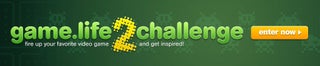
First Prize in the
Game.Life 2 Challenge