Introduction: Custom Solid Surface Cutting Board
This Instructable will teach you how to make a custom cutting board using solid surface material that is normally used for kitchen counter tops. Most people refer to it as corian, but corian is a brand name of solid surface material.
These custom cutting boards are great if you want something a little different for a gift or for your own use. You can personalize them for each person.
It can be a little difficult to find solid surface material, but patience usually pays off. Check with local kitchen and bathroom installers. Sometimes they will have old stock material that isn't going to be used that they will sell cheap. Other times they will have cut-outs for sinks that can sometimes be the perfect size for cutting boards or other projects.
Step 1: Materials and Tools Needed
MATERIALS
- Scrap solid surface (corian) material
- Sand paper of varying grits. I used 150, 180, 400, 800 and 1200 grit. The 800 and 1200 grit were Wet/dry automotive sand paper.
Tools
The tools I used on the project were as follows:
- Band saw
- Oscillating spindle and belt sander
- Random orbit sander
- Router
- Router table
NOTE: If you plan on using any tool for a project please make sure you are familiar with the tool and all of the dangers associated with it. If you are not familiar with a tool then you should ask someone who is to show you the proper way to use it. A lot of communities have classes at local colleges on the proper use of tools and machinery. There are also local woodworking clubs that offer classes at very reasonable rates for beginners. I highly recommend using these resources for your safety and for the most efficient use of the tool.
SAFETY FIRST
Always wear eye and hearing protection.
Always work safe with the proper safety equipment and guards on your tools.
Step 2: Find Your Shape
You can get shapes from a variety of sources.
1. You can do searches online using Google Image Search or other search engine. Use keywords like "profile" or "outline" in your search.
2. Use a picture that you have taken yourself:
3. Throw an object on your flatbed scanner.
4. Sketch out the shape you want using pencil and paper.
5. Look through clipart on the internet or in Microsoft Word.
I used the image of a squirrel I found on the internet.
Step 3: Make a Pattern
If you are using a picture and want to make it into a pattern I suggest tracing the picture with a photo editing program. I use Paint Shop Pro, but others will do.
Open the picture and crop only the part of the picture that you want to use.
Make a vector layer and place it in front of the background layer so what you trace will show up on top of the background.
Select the pen tool and trace the outline of the shape you are copying. Under the MODE section select draw freehand.
Make sure to add plenty of vertices as you trace the shape. Later if you want to modify the shape you can drag these vertices around.
Step 4: Print Your Pattern
How you print your pattern will depend on your printer and software used. Basically you want to print the pattern to the correct size to fit your piece of solid surface material. If there is someone you know that has access to a large size printer then you can have them print your pattern on one sheet of paper. Most printers will allow you to print your your images to multiple sheets. You may want to add a grid to the pattern prints so you can match up the multiple sheets without too much trouble.
One other option is to take you file to a local print shop where they will most likely be able to print your pattern out to the size you need. Make sure to call ahead to verify that the print shop can print from the file format you are using and that they can scale the print to the size that you need.
Next you need to modify the pattern to remove any inside corners that have a radius smaller than the radius on the router bit guide bearing on your roundover bit.
To remove the inside corners in the pattern the easiest thing to do is take a circle template and move it around your pattern. At each inside corner you connect both edges of the corner with a radius using the template. I only had a couple locations on my pattern that needed to be adjusted. See the pictures for what these look like.
Step 5: Transfer the Pattern to the Material
The steps are as follows:
- Cut out the pattern to the outside line.
- Tape the pattern to the piece of solid surface material as shown in the picture. I use blue painters tape so it peels off the pattern easier.
- Take the marker and trace around the outside edge of the pattern.
- Remove one of the tape pieces and trace the edge of the pattern where the tape piece was.
- Replace the tape pieces until you are finished.
- Continue tracing where the tape pieces are until you have the entire pattern traced.
Step 6: Cut Out the Shape
Use a band saw to cut out the pattern. This is relatively easy, but can take a little time if you have a complicated or large pattern. Try to make your edge free flowing as this will make the edge sanding much easier.
I used a 1/4-inch wide 14 Tooth Per Inch raker bandsaw blade to cut out the squirrel. This allows for some of the tighter corners in the pattern. The edges of the cutting board are going to get sanded in the next step so don't worry about them looking a little rough with the bandsaw blade marks when you cut it out.
Step 7: Sand the Edges
Now you will want to sand the edges of the cutting board to remove all band saw blade marks. Do this by sanding around the perimeter of the cutting board using a spindle sander. Start with a 100 grit or 120 grit sanding drum and move to the higher grit drums such as 180 grit and 220 grit on each consecutive pass around the entire cutting board.
Try to use as large of a diameter sanding drum as possible as this will help minimize adding spindle marks to the edges of the cutting board.
I used an oscillating spindle/belt sander by ridgid. I've been using it for years and it has been an incredibly useful and reliable tool at a great price compared to some of the others.
Step 8: Router the Edges
Next you need to use a router bit to round over the edges. A 90 degree corner on the edge of the cutting board can be a little dangerous (and sharp). Set your router bit depth and practice on a scrap piece of material to make sure it is cutting at the depth you want.
I used a 1/8 inch roundover bit with a 1/2 inch guide bearing. The guide bearing is essential for obvious reasons.
Route all edges of the cutting board on both sides. Check the edges repeatedly on both sides to make sure you didn't miss an area.
Step 9: Sand It Smooth
To sand the cutting board top and bottom faces I used multiple grades of sandpaper. I started with a random orbit sander with 180 grit sandpaper. From there I used 400 grit dry sanding paper.
Next I used 800 and 1200 grit wet/fry sandpaper. I used these on all surfaces of the cutting board. It makes the cutting board nice and smooth on all surfaces. You would probably be fine with just going up to the 800 grit paper.
Use a soft cotton cloth with a little mineral oil to polish up the cutting board. Another option is to use a solid surface polishing agent from your local hardware store.
Step 10: Use It or Lose It
That means now you can use it or give it away. Give it to that special person. This one was obviously made for someone who loves squirrels. The squirrel is about 28 inches wide and 29 inches tall. It is a little large and rather heavy for a cutting board, but then it has a large usable area. Besides, if you want to make something that makes an impact on people then make something you wouldn't be able to find in a store.
Cheers!
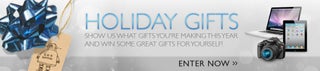
Participated in the
Holiday Gifts Challenge