Introduction: Customized Cubic Lamp
I've created a previous tutorial here in which I designed a low-cost way to incorporate a coin cell battery into laser cut layers. For this tutorial, I was playing around with it some more, coming up with new ways to use that simple concept.
This was somewhat designed as an "intro to laser cutting class," and people could customize the lamp to their liking. Using simple graphics softwares, you can turn online images into cutouts on the lamp faces. For example, for a lamp specific to me, I had a face for the Deathly Hallows (happy birthday, Harry), a face for Naruto's hidden leaf village emblem, a face for Yuna's staff from Final Fantasy X (the good old childhood days..), a face for my golden bear pride, and finally. a face for a "Made at UMakers by Yu (since my last name is Yu.. and since it was a demo piece I thought it'd be funny if I said made by Yu but could be made by you.. get it?)
Step 1: Lighting Concept
How does the light work? A coin battery is snugly fit on the side of the base, sandwiched in the layers. To turn on the light, you roll it one direction (depends on your design). To turn the light off, you roll the battery back to the original position. Simple, cost-effective, relatively robust.
And how is this done? You have two terminals of an LED, which are soldered to longer pieces of thin wire to lengthen the terminals. One wire wraps around a loop in one layer of the base while the other wire routes down to the layer underneath before wrapping around a loop in that layer below. Then the battery is fit into a pocket in a layer in between those two layers so that one side of the battery is in contact with only one of the terminals. To have the "roll forward for on, roll back for off" functionality, you have different sized loops. One loop is small enough that it'll be in contact with the battery only when you roll the battery forward.
Step 2: Materials
- wood (I used 1/8" birch plywood)
- glue
- LED diode (simple 1.5-2V ones are fine, as long as they are below 3V)
- CR2032 (i.e. 3V lithium coin battery)
- paper
- wire/solder wick (can be anything, from copper strands stripped from scrap electronics to jewelry wire, but it is HIGHLY suggested that you choose THIN wire. The thinner it is the better, since it'll need to be sandwiched between layers, but the thinner it is the easier it'll snap so be careful. It's hard to find a compromise between thinness and strength for wire, but I eventually settled with solder wick, which has a strong braid that's also very flexible.)
- laser cutter (Full Spectrum hobby 20x12in)
- vector graphics software --- I used Adobe Illustrator (OPTIONAL but for those who want to customize their laser cutting designs)
- soldering iron (OPTIONAL but suggested for robustness)
Step 3: Circuit for Battery Base
The bottom base that contains the battery is based on a concept that I tested in my previous tutorial, though it's slightly different to accommodate a different lighting design. I attached the Adobe Illustrator files and all to step 1, but I also included pictures and walkthroughs for how I designed it (next steps) so you can see more clearly how it works. You could alternatively just use the template and add your designs (see steps 4-8 on how to vectorize images easily) and skip to step 10 for cutting and assembly.
The battery base design consists of three main layers:
The first layer has three holes. The left-most hole close to the bottom edge is for the left terminal to go through and avoid the loop that the right terminal will make. The middle and right-most holes are the holes that the right terminal will go through to make a loop. The LED terminal goes down the middle hole and back up through the right-most hole to make a diagonal which will interface with the top of the battery once it's inserted.
The second layer features a slot on the right side where the battery will slip into for sliding on/off. It also has a hole in the bottom right for the left terminal of the LED to go through to make it to the fourth layer for looping.
The third layer has two holes that the LED's left terminal will go through to make a loop that interacts with the bottom face of the battery once it's inserted. The terminal goes down through the hole closer to the bottom edge and back up through the other hole before wrapping around where it went down in order to fully close the loop.
Step 4: Designing Slots and Holes for Laser Cutting
This step briefly goes over how the shapes are made and positioned. Mostly on this step is showing how third layer's slots are made from splicing together two circles, some lines, and a square. There's also a picture on using lines to outline where your wires will cross so that you can see where to position your circles for the wire to go through.
In any case, see the notes in the pictures above for step-by-step instructions. Quick nutshell: for each layer you are designing, put an slightly transparent/faint copy of the layer above it so you can see how the wires will come down. Draw a line indicating how I want my wire to pass through the layer, and add circles at its endpoints before deleting that line. BE SURE that your lines indicating wire position make sense; they have to start where they ended on the previous layer (since the wire is one whole strand...
Note that one of these squares will later be replaced with a square with finger joints since it'll be part of the cube, which is connected using finger joints.
Step 5: Top Cube Design
I used a website called makercase.com that produced the files for a box with finger joints.
Once you save the resultant files, open it up in your graphics software and turn the lines into pure red (R 255, G 0, B 0 on the RGB spectrum) and stroke weight 0.01pt (or called hairline for some softwares).
The overlapping red lines where two faces meet are darker because there are actually two lines; one from the face on the left and another line from the face on the right (or top/bottom). Delete one of them by using the scissor tool (press hotkey C) to snip the path at the anchor points and delete the extra line.
One of these faces will become the bottom of the lamp, and thus it needs holes for the LED terminals to stick through. Copy and paste this chosen face into your file from the previous step (with holes for the circuit to snake through). Center the pasted face with the original square (that was supposed to be the face) before deleted that square. You can see that now one of your circles might be too close to the edge (see image five above). To fix this, copy and paste a duplicate of the layer that you designed to go below this layer. Reposition the circles using that duplicate layer as a guide (to ensure that your wire will have adequate contact with the battery face) (see image six above).
Step 6: Vectorizing Images, a Guide
As a quick guide on easily converting online images into vector cut paths, I included this and the next step on different options. I used Adobe Illustrator as my graphics software of choice, but Inkscape and Gimp and CorelDraw would work just as well.
The most helpful tool for vector conversion is image trace. This option appears at the top in Illustrator when you have a picture selected. If you click the drop down menu button, different options appear. For pictures with predominately dark colors, I go for Sketched Art and Silhouette for a clean black and white result. For pictures with lighter colors, I'd use 3 Color or 6 Color (this splits the image into its dominate 3 or 6 main colors because sometimes Sketched Art won't recognize the light color. Then just use magic wand tool to select the different colors and convert them into RGB pure red or blue for cutting). For the FabLab logo I went with Sketched Art, though Silhouette would probably do the same.
After you've traced the image, click expand (will be on the top menu bar where image trace was) to turn them into paths. Then just change the stroke/fill to the combination used by your laser cutter (usually stroke of 0.01pt/in in RGB pure red for cutting, fill of RGB pure blue for raster.
SIDE NOTE: The white parts will create extraneous lines for laser cutting so you need to get rid of them since you only want the black part here. Use the magic wand tool on the left toolbar to select any of the white parts of the image and press delete. If you don't, the laser cutter might take the black parts as one path and the white parts as another, and thus you'll have two overlapping lines for the laser.
Step 7: Lighter Colors for Vectorization
For a lighter image like this (Yuna's staff from Final Fantasy X), Sketched Art won't pick up on the light yellow. To preserve the yellow, I chose 6 color as the image trace option (not three since there's yellow, blue, black and white -- four colors so one would be skipped). There are some parts you may want to clean up -- for example, I used the magic wand tool to get rid of this awkward black outline -- but this does most of the work for you.
Again, there may be white parts that will need to be deleted so use the magic wand tool to click on white parts and press delete (or you can use the white arrow tool on the left toolbar and select this path to delete).
I had a little trouble with some overlapping paths that were present in different colors (grey interfered with black, minor and rare issue but it's described in the notes of images 5-7 if you're interested).
Step 8: Tips With Text
Typography: reliant on the art of selecting good fonts. I was taught never to use a default font that anyone recognizes (Arial, Calibri, Cambria, Georgia, etc.) so I went wild with testing different fonts I had that matched the "tone" of my piece. Since this is sort of a product demonstration project for UMakers, I wanted to include some sort of plug/advertisement. For the font, I wanted something slightly professional but not too formal. A bit of a techy touch, so straight lines and fewer curves. I also decided against serifs (except Jura, one of my favorites) in the end since I tend to associate that with business, but UMakers is a fun, hobby makerspace rather than business/marketspace.
Since the real estate I had was less than 2 square inches, I had to use small text to fit in addresses and such. With such small text, I was a bit worried that the raster setting might create scorch marks that would interfere with the text visibility, so I wanted to do a quick vector cut rather than rasterized text (so cut fast in one go at medium power as opposed to cut fast in multiple passes at low power. In this case, you have to select a "single-line font" that doesn't have a stroke, and thus has only a single line through it instead of the standard outline going around each letter for regular fonts. These special single-line fonts are commonly from the Hershey subset of fonts (fonts, not chocolate!) which you can download for free on the internet. Alternatively, if you're not afraid of rastering, go ahead and do that at a faster-than normal speed to avoid scorching. I actually went with this option in the end since Hershey fonts weren't working well on my computer for some reason.
I also wanted to make the letters more spaced out so that the scorching that might occur wouldn't make the text look smeared. To do this, press ctrl/command + T to get the text tool bar and change spacing.
Expand all text to preserve the outlines for raster engraving by going up to the Image tab, then Expand and click object and fill. You can actually get by without expanding, but I do it in case I want to play around with the letter more later (you can enter the group of text to reposition or rotate specific letters if you do this.)
Play around with how you want your text in terms of vertical vs horizontal too. To make your text lie vertically, go to text (top menu bar) > type orientation > vertical.
Step 9: Laser Cutting Prep
Once you've vectorized and put designs on the faces of the cube, you're ready to cut!
This step will depend on what laser you have access to, but at UMakers there's the Full Spectrum hobby 20x12" model. It's compatible with the software called Retina Engrave, which can be downloaded from the full spectrum website.
Begin by pressing print to "print" your artwork, as the laser cutter registers as a type of printer for your computer. Select the Full Spectrum Engineering Driver as your printer and go to the Preferences button next to it. In the next Layout window, press Advanced in the bottom right to get this window. In paper size, select FSL Hobby Series Gen5 20x12", which matches the specs of UMaker's laser cutter. Continue pressing OK to finally print (i.e. send the file to Retina Engrave. You will need to have Retina Engrave window open before you press print! This is a glimpse of what the Retina Engrave window looks like.
Side note: to raster the 1/8" birch plywood, cut at 95% power and 40-50% speed, and for cutting through, cut at 95% power at 25% speed.
Step 10: Cutting and Staining the Wood
Once you've sent your file to the "printer," cutting and rastering will start.
Be careful with all the small holes and pieces that might fall out of your designs, since you might need some of them to glue onto the lamp. I later decided that I wanted to keep my cutouts for the Deathly Hallows and FFX faces rather than gluing in the small pieces that would've been inside (for the deathly hallows example, I would've glued the little triangles and circle halves).
I also stained the wood with a dark walnut stain since I wanted to hide the scorching of the wood from the cutting (To avoid the scorching, try putting masking tape on top of the wood before laser cutting your designs. Just a warning though: removing the tape is a pain.).
Step 11: Assembly
Begin by cutting out paper to put behind your lamp's cutouts (unless you do want to be able to see the lamp's guts..). Alternatively you could use opaque acrylics and whatnot. Assemble the five top faces of the cube (last face is part of the battery/circuit on the bottom of the lamp).
To diffuse the LED, rip off a bit of paper towel or tissue and wrap it around the LED. This makes the glow less harsh.
Poking the two terminals of the LEDs through the first layer's (the finger joint face with no design cutout) left-most and bottom right holes. Ideally, put the positive terminal through the hole on the right so that you can have the battery inserted positive side up later on. Poke the terminal [that went down the bottom right hole] up though the top left hole before winding the end around where it went down in the bottom right hole (see image 3 above). This is where your right terminal ends, so trim and glue. The left terminal of your LED that went through the left-most hole now goes through the only hole of the second layer. Put this remaining terminal through the middle hole of the fourth layer like so before bringing it up the hole close to the edge. Pull the wire end as tight as you can after you apply glue between the second and third layers to bring them as close together as possible. Now wind this left over wire around between the second and third layer in a clockwise direction in order to create a loop around where it went down (just like you did in between the first and second layer -- sorry, it's hard to explain..).
For more pictures that might give you a better perspective, check out this other tutorial, step 11.
Step 12: Finished and Future Work
To turn on the lamp on, simply stick a CR2032 coin cell battery into the slot in the bottom base. Roll it forward and backward to turn the lamp on and off (since the solder wick contact is present only for half of the slot, rolling the battery away from the gap of wire will remove the contact between the battery and wire, so the circuit will be broken and the light will be off).
Now that this initial lamp is done, you can go crazy with your next one: what new ideas can you come up with to furthur personalize this simple lamp? Some suggestions for inspiration:
- I chose to stain all the pieces of the wood that I used, but you can stain only, say, half of your pieces for an interesting light and dark contrast effect.
- Instead of just wood stains, try out paints to make your art pop.
- Rather than just a pre-programmed RGB LED, insert an RGB LED or neopixel to program the LED yourself and thus create a certain blinking and color-changing pattern.
- Cubes are overrated -- try a pyramid, icosahedron, etc.
As always, leave questions and comments below, and I'll get to them when I can. Enjoy.
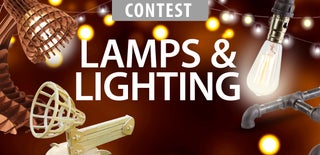
Participated in the
Lamps and Lighting Contest 2016
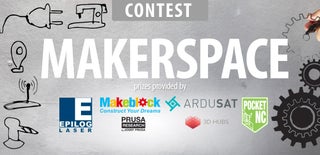
Participated in the
Makerspace Contest
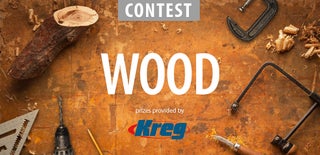
Participated in the
Wood Contest 2016