Introduction: DIY Bicycle Turn Signals
Living in a city, I use my bike as means of transit, riding from home to work, work to studio, errands, etc. When I ride at night, I am often concerned if other vehicles/people on the road can see my hand signals when I am about to turn. To make my night rides safer, I decided to build a turn signal system for my bike!
The following instructable will go over how to use a 555 timer to flash an array of LEDs, and how to mount LEDs in an acrylic panel, and cast it in resin.
Step 1: Materials
Materials:
The circuit
Turn signal and circuit housing
silicone
bike handlebar wrap
zip ties
Tools used:
glue gun
utility knife
angle grinder/palm sander
laser cutter
Step 2: Assembling Your Flash Timing Circuit.
After you have gathered your materials, assembly begins!
Please reference the attached fritzing file for the construction of your circuit.
You want to mount the 555 Timer IC so it straddles the center of your proto board. Solder into place.
Attachments
Step 3: Assembling Your Flash Timing Circuit. (cont.)
Add a jumper wire that will connect pin 2, to pin 6. Solder that wire into place, and trim your leads.
Next, set your resistors as show in the image into your proto board - solder into place. The 100ohm output is in-line with pin 3, then directed down to a separate rail that is later connected to the anodes on your LED array.
The 10K resistor is mounted between the positive rail and pin 7. Lastly your 100K resistor is mounted in series with the 10K resistor, and pin 6 on the 555 timer.
Step 4: Assembling Your Flash Timing Circuit. (cont.)
Install the 4.7uF 50V capacitor. The positive lead connects to the pin 6 rail, and the negative lead is grounded.
Step 5: Assembling Your Flash Timing Circuit. (cont.)
Trim your long wire leads from the back of your circuit.
There are 3 jumper wires that need to be set into place. Connect the negative lead on your capacitor to the ground rail, pin 8 to your positive rail, and pin 1 to the ground rail. Also, wire in the battery clip to the corresponding ground and positive rail.
Measure the distance from the back of the bike, where the light will sit, all the way to where the buttons to activate the indicators will sit. Add about eight inches to that measurement, and that is how long your wires for your buttons will be. Cut four wires at this length.
Step 6: Making and Wiring Your Back Plate
I used a laser cutter and orange acrylic, and designed a plate for my LEDs to sit in. The vector file for the laser cutter is attached to this instructable if you would like to replicate my design. I knew I wanted to embed my circuit in resin to waterproof the entire thing, so this template was the best method of seating my electronic components.
In my experience with DIY, I have learned the importance of multiples. It's nice to have extra parts around, so I cut two of these acrylic plates.
Attachments
Step 7: Insert Your LEDs
Thread all of your LEDs into their holes on the acrylic plate so that all of the cathodes are on one side, and all of the anodes are on the other. I bent all of the cathodes one way, and the anodes another, so that I could keep track as to which was positive and negative when I was soldering all of this together.
Step 8: Wire You LEDs to the Plate.
You are going to daisy chain your LEDs together, once they are all threaded to the plate. Go through and solder all of your positive leads together in a zig zag shape working from one end of the plate to the other.
Trim your leads as you go.
Go through each LED and connect all of your positive leads together, and all over your negative leads together.
You will end up with two leads on each side, negative, and positive, that respectively connect to your circuit board.
Step 9: Wire Your Circuit to the LEDs on the Plate, Connect Your Switches.
Connect two wires from the ground rail on your circuit to your negative LED arrays on the acrylic panel.
Extend two very long wires from your resisted output rail to two tactile switches. These wires should be the distance you need your wires to travel on your bike frame, running from the rear, to your handlebars. Mine were a bit longer than 5 ft long, and then I trimmed as necessary later.
Wire your tactile switches so that the wires are soldered caddy-corner to eachother, then run two more 5 ft wires back to the positive leads on the LED arrays.
Step 10: Securing, and Waterproofing Your Circuit.
Cut your positive wire from your battery clip to the circuit board, and solder in your SPST switch where you cut the wire. This switch is added so that power is not being run to the 555 timer at all times.
Add a dab of hot glue to the back of your circuit board, and adhere it to your acrylic panel.
Then go through the back of the acrylic panel, and coat all of your LED leads with hot glue as well. This step insulates your wires. If your glue goes anywhere you don't want it to be, you can clean it up with a razor blade or utility knife.
Add another dab of hot glue to the leads on your switch.
Step 11: Encapsulate Your Circuit in Resin.
Knowing that I wanted to trap all of my electronics and lights in resin to waterproof the circuit, I used an easy silicone mold making technique to create a basin for me to embed my electronics in resin.
Utilizing the extra acrylic plate I laser cut from step 6, I used masking tape to cover up all of holes in the plate, and squished it into the mold, allowing it to sit for a day, and properly cure.
After the mold had cured, I poured 4 oz of catalyzed resin into the mold, and then pressed my project down into the resin. Set aside, and allow to cure for a day.
Remove from the mold, and begin polishing.
Step 12: Polishing the Light.
The best way to polish resin is with sand paper. I worked with an angle grinder - turned on its side, clamped to a work bench, like belt sander - to remove the extra bits of resin and smooth the light.
With a palm sander, and finer grit sand paper, I went back over the the entire light again, giving it a smooth frosted finish.
Be careful that you don't sand down too much material, and hit your circuit.
Step 13: Attach the Hoseclamp to Your Light.
I used a dab of quick set two part epoxy adhesive to adhere a hose clamp to the light. Set it, make sure it doesn't fall over, and don't touch it while the glue is hardening.
After the glue is set, attach the light your bike's frame.
Step 14: Run Switches From Your Handlebars.
Mount your switches for the right and left signal on the corresponding right and left brake handle. By splaying the leads flush with the surface of the hand brake, I was able to wrap the wires around the brake, then I used blue painters tape to hold the switches in place.
Using electrical tape, wrap the four wires running from the handle bars to the circuit. Or use heat shrink. I used zip-ties to hold my wires in place along the frame of the bike.
When you get to the end of your bike frame, separate the wires so that you are wrapping the two wires that lead to the handle bar mounted switches.
There should be enough slack in your wire-lines so that you may still safely turn your bicycle. When you have mounted your switches, begin enclosing them in handlebar wrap - not too tight though, other wise your switches will always be in the on position.
I used a smaller zip-tie to mount the battery and switch to the frame too.
Step 15: Go for a Ride!
Test out those signals, and be the safest cyclist on the streets!
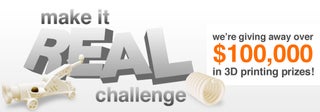
Participated in the
Make It Real Challenge