Introduction: DIY Copper Clay Trilobites
Learn how to make your own 'metal clay' using powdered copper and organic binders.
The first precious metal clays were introduced in the 1990's - made from pure silver powder and organic binders (Mitsubishi Materials Corp. makes PMC = Precious Metal Clay and Aida Chemical Industries makes Art Clay). The silver clay behaved kind of like a ceramic clay, could be molded, sculpted, carved, extruded etc. The metal clay was then 'fired' in a kiln or by torch, to produce a pure metal item.
Fine silver (.999 pure silver) is a noble metal, meaning that it resists oxidation and corrosion. Many noble metals are also precious metal, gold, silver, platinum. Because it resists oxidation, fine silver can be fused by heat in an oxygen (normal atmosphere) environment such as in a kiln or open torch flame. When particles are heated, close to melting temperature, but not melting, they move close together and become sticky, adhereing to each other. This compaction and partial fusing is called 'sintering'. Sintering produces metals that are more porous and lighter than cast metal, also not as strong. Gold clay later became available, but required higher firing temperatures and was very costly.
Precious metals are costly, and in recent years have grown even more expensive. Many people worked on trying to make 'base metal' clays. Base metals, such as copper, bronze (copper and tin) and brass (copper and zinc) do oxidize and corrode. When heated in an oxygen atmosphere, base metal particles oxidize and do not stick together (sinter). Industrially, metal powders are sintered in special kilns filled with inert gases. This is virtually impossible to do in a home or small studio setting. The inventor of BRONZClay (tm) and COPPRClay (tm), Bill Struve, found a wonderful way to fire base metals in a home kiln. He used activated charcoal in a closed, stainless steel container to produce a low oxygen environment for sintering base metal clay. When heated to high temperatures, the charcoal tries to burn and uses any available oxygen in the area, thus preventing (and even reversing) oxidation of metal particles.
Step 1: Copper Clay Recipe
The basic recipe is organic binders, atomized metal (-325 mesh or smaller), glycerin and water. Wear a fine particulate mask when handling dry powders, preferable N95 - no excuse not to BE SAFE and use safety equipment. (Photo shows bronze powder: I took this photo after I made the clay and grabbed the wrong bottle)
1/2 tsp. corn starch
1/4 tsp. powdered xanthan gum (do not breathe in the powder! It forms a VERY gummy slime when mixed with water)
glycerin - a few drops adds a little flexibility
3+ Tbsp atomized pure copper*
distilled water in a small spray bottle.
Wear your mask and carefully mix dry ingredients until you have a uniform mix. No clumps of cornstarch visible.
Spray surface with some distilled water and carefully stir. Add more spritzes of water and keep stirring until the mix starts to clump together. Mix well between spritzes until your mixture starts to feel clay-like. Lightly oil your hands with olive oil or natural hand balm and squeeze mixture. If it holds together then you can knead by hand. If mixture starts to crumble, work in a little more water. If it is very sticky, let it dry a bit and rework, or add a little more metal powder or cornstarch. Copper clay will have a reddish tine, shown in the second picture.
Set clay aside in a sealed container or plastic bag.
Let clay rest for a while and go make your trilobite mold in step two.
* Smallest metal particles are best, but it is hard to get finer than -325 mesh, about 44 microns. Really good if you can find 1-20 micron powder, but it is expensive reagent grade copper. Atomized metal is sold for use with plastic resins to 'cold cast' metal art objects. Check art suppliers, Douglas and Sturgess, or TAP plastics.
Step 2: Make a Mold
You need:
Two part silicone mold putty (Amazing mold putty available at Michael's crafts in U.S., various other brands, Smooth-on Equinox, Easy Mold, check craft suppliers, metal clay suppliers etc.)
Find item to mold: Find a good trilobite fossil, intact, but without fine spines. I like more dimensional trilobites, like flexicalymene (Ohio) and calymene. You can also use flatter elrathia kingii from Utah. You want a nice specimen, but not very valuable - in theory making a silicone mold should not damage the original fossil, but you never know. Do not use an irreplaceable or very valuable specimen!
Clean fossil, remove rock dust, dirt, sand etc. No release agent is needed, but you can still apply a thin layer of soap and let it dry - provides extra release for porous items like rocks.
Work fast, usually you only have 1-4 minutes working time. Mix equal part putty: always two colors, so mix until you can only see the blended color, no streaks of one color visible. Usually I knead for 1 minute, press over fossil, press edges down and form a flat bottom (press with a book or board). Wait 20-30 minutes and test if silicone has set - lightly press your finger nail or butter knife into one edge of the silicone. If it leaves an impression, let things sit longer. If there is no impression you can carefully peel the silicone mold off the trilobite: watch for undercuts and pull SLOWLY so you don't damage the fossil oe tear the mold. Clean the inside of the mold with soap and water. Dry well.
Step 3: Molding Your Trilobite
Take a clean silicone trilobite mold (or any other mold). No need for a release agent.
Oil your hands or use a little balm to keep clay from sticking to your skin. Take some homemade copper clay and roll or press into a layer at least 1/8 inch (2-3 mm) thick. Gently lay clay sheet onto your mold and gently push clay into all parts of the mold. I use a greases paint brush handle to push clay into small areas. Try to keep the clay the same thickness all over the mold. Set aside to dry. Silicone is heat resistant, so you can speed drying by setting the mold onto a mug or candle warmer, warming try etc. You can try to remove the trilobite when still wet, but it is difficult to do so without cracking your molded clay. (Optional, you can embed copper wire into the clay: sand off any varnish or anti-tarnish coating. Bend tip of wire and twist into the clay. Think about shrinkage, the clay shrinks as it sinters, but the wire won't.
Consider adding a bail if you want a pendant. Roll a snake of clay and wrap it around a greased straw or dowel. Smooth ends together using a little water or clay paste. Make a few extra on the same straw. Set aside to partially dry. Carfeully slide the bail off the straw - unfired metal clay is fragile. Attach your bail inside the head end of the trilobite (or at the head end if you don't mind a visible bail. Wet contact area on bail and trilobite with a drop or two of water (use a clean watercolor brush). Add alittle clay paste and gently wiggle pieces together. Stop wiggling when the pieces stick together. Smooth join area, adding some soft metal clay as needed to reinforce the join. Smooth away all cracks - if the crack is there when it's dry, the crack will only get bigger when you fire the trilobite.
When everything is completely dry, you can do some pre-finishing with small files or sand paper. Clean up bottom edge and remove any sharp parts. It's easier to smooth edges when the clay is powder than when it is sintered metal.
Use a needle or pin to carve your signature inside, or intials etc... use a light hand so you don't break your molded fossil.
Step 4: Firing Copper Clay - You Need a Kiln
Base metals oxidize - copper will get black firescale when heated to sintering temperature (1700-1750/1800F). Some commercial copper clay with very fine particle size can be torch fired if the pieces are small, I've never had much luck with a torch. Base metals oxidize when you fire them - the oxides ('rust') interfere with the sintering. Commercial sintering is done in an inert gas kiln - a sealed kiln filled with various inert gases. How could you sinter metal at home or in a small studio? Sealed kilns are very expensive an impractical to have at home. A guy named Bill Struve, (inventor of BRONZClay and COPPRClay) came up with the brilliant idea of firing base metal clays in activated charcoal to produce an oxygen poor environment (no oxygen means no oxidizing, so sintering can occur). But, in the first stage of firing base metal clay, we need to remove the organic binders by burning them away. Burning requires oxygen. So, a two part firing cycle works best. (Check out the internet for more info on firing base metal clays, metalclayacademy.com is a great place to start).
To fire our DIY copper clay you need:
1. A kiln with a controller and accurate pyrometer (high tem thermometer). Digital controllers are awesome, but expensive. If you don't have one for your kiln, you can use an 'organic controller', which is yourself with a kitchen timer, constantly checking the pyrometer to monitor the kiln temperature. I have to use this method myself, it sucks, so get a digital controller if you can. Beg, whine or plead as necessary :-)
2. Stainless steel container with a lid (try thrift stores - a small stainless steel bowl will work too - you can cover it with a sheet of metal). For a single firing, you can even fire in a clean food can. To prevent steel from spalling/flaking as it cools and making a mess in the kiln, coat container with glass kiln primer.
3. Activated charcoal: buy online, activated coconut charcoal. Do not use aquarium filter charcoal because it may contain impurities which interfere with the sintering process. I've read that copper is particularly sensitive to impurities, coconut charcoal is more uniform.
4. Put about 1 inch of activated charcoal in bottom of your container, Place copper clay items on top, 1 inch from sides and at least 1/2 inch apart - more if they are thick items. Leave container uncovered and set it on stilts or post in the center of your kiln to provide good airflow all around your container for more even heating. Make sure the metal container does not touch the inside of your kiln or your pyrometer probe tip.
Be safe around kilns, they can cause severe burns. Use special heat resistant gloves when handling hot items and use common sense. Don't touch the outside of the kiln, it can give you a nasty burn.
5. Close the lid and heat kiln slowly. Leave at least one peep hole open to vent burnt binder. If you don't have peep holes, leave the lid slightly ajar until binder is burnt away. Things will start to smell 'burnt' around 400-600... ventilate the room well to remove any smoke or fumes from the burning binders. Continue heating to 800-1000F and hold for 15-45 minutes to fully burn off the binders. Wait a while after you don't smell charred stuff, then turn off the kiln and cool it down. This is the end of the first stage of firing.
6. Your clay items are VERY fragile with no binder. They are black and charred. Do not touch them. When you can safely handle the contianer, carefully blow off any ash (or use a key board vac). Cover items with 1/2-1 inch more charcoal and put lid on onto the steel container.
7. Heat to kiln rapidly to 1700 F and hold at that temperature for 3 hours. (With Douglass and Sturgess copper powder my items did not quite completely sinter at 1730-40, just a little porous and would break if you bent it past 90 degree or hit it very hard with a hammer. Next time I'd ty 1750-80 - but tricky to get correct temp - too low no sinter, too high, the metal blisters or melts. The 'correct' sintering temperature depends on the specifc kiln, so take notes each time you fire: temperature, duration of firing etc.
8. Cool the kiln down until you safely remove the firing container. Use a metal scoop to sift items out of the charcoal. You can dunk items in hot water to cool them quickly. For safety, do not remove container from kiln until it is below 400 or 500 F. Cooler is safer. Do not touch the bare metal until you are sure it is cool - I've 'branded' jewelry shapes into my fingers by being careless and it HURTS.
Step 5: Finishing Your Copper Trilobite
When you take your cooled item out of the activated charcoal, it will look dark black, brown or reddish, very ugly. The surface is microscopically porous and does not reflect light. There are several options for finishing the surface, all of which involve compressing the metal pores in a process called burnishing.
1. Brush with brass bristle brush for a soft, muted finish, lightly burnished.
2. Brush with a steel bristle brush for a brighter, matte finish, slightly more burnished. Copper trilobites in second photo were finished with a steel brush.
3. For shiny finish you can hand rub with a smooth piece of steel or agate - the harder surface and pressure compresses more pores in the surface, creating a reflective surface.
4. Hand burnishing can be hard work, so an easier method is to use a rock tumbler filled with stainless steel shot, water and a dash of soap or burnishing compound.
If you don't like these finishes, you can use sandpaper, coarse to finer, in a traditional polishing technique.
Copper will oxidize or patina over time. Coat your piece with wax, varnish or nail polish if you want it to stay shiny. Lots of patina recipes online if you want to try different looks.
Note: the yellow metal trilobite is made from DIY Bronze metal clay... similar process, but different firing temperature. Hope to have a bronze clay 'ble soon.
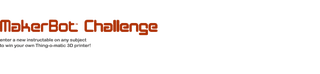
Participated in the
MakerBot Challenge