Introduction: DIY LED Replacement Bulbs for 12 Volt Landscape Lighting Wedge Base Bulbs
A while ago I decided to minimize our energy usage using LED lights wherever possible. Why not start in the front yard? I was using a 500 Watt supply and now use a 44 Watt supply! I looked online for Wedge Base LED Bulbs. I saw lots of fancy circuitry and weatherproof housings that were going into an enclosure on a regulated 12 Volt supply. They provided dim light and were not cheap! The cheap ones are a few dollars now. But you can make one for about 25 cents in materials. They also don't combine colors. We need to make a Wedge Base Bulb that will run comfortably on 12 Volts. This integrated circuit requires four components. In this case they will all be diodes, hehe.
So here is what you will need to have on hand:
An existing 12 Volt landscape lighting configuration, Malibu, Toro, ect.
Materials:
White 5MM LEDs ($4 per 100, Ebay)
Perforated circuitboard ($4 board, Radio Shack)
18 gauge copper wire
Rosin Core Solder for electronics
Tools:
Soldering Iron
Dremel Tool (possibly a coping saw)
Wire Cutting Dykes/Stripers
Small Needle Nose Pliers
Heat Dissipators (hemostats, alligator clips)
Step 1: Cut the PerfBoard
Cut the PerfBoard into strips. The strips must be the width of a Wedge Base Bulb. So mark each fourth row of perforations for cutting with a ruler and a thin Sharpie. You might want to double check your particular board with one of the Wedge Base Bulbs for width but this should be accurate. Then cut with your Dremel using an acceptable cutting attachment. I used the detachable wheel for metal. Don't forget to wear some breathing protection of some kind. A coping saw may work as well. I tried shears and wire cutting dykes with poor results as shown. When the strips are properly cut they will have three rows of perforations as pictured. Then clip each strip into sections with wire cutting dykes, or Dremel. Clip each one off at the 14th row. This will give you the right size and shape to mount 4 LEDs.
Resources:
http://en.wikipedia.org/wiki/Perfboard
Step 2: Mount LED1
LED1 will be mounted on the top of the bulbs circuit board. First choose which end of the board is the going to be the top. This will be the end that is smoothest. The rough cut perforations will help hold the contacts on the bottom end later. They don't hurt anything on the top so don't worry about that. Just put the most pronounced end on the bottom. Now slip LED1 into the outer top holes and bend the legs around the board and back up between themselves. Then bend them down and outward as shown. I used hemostats to get the leads under and through themselves and bent out. Wrap it fairly tight. I wrapped one leg at a time on LED1.
Note: LEDs are diodes and as such allow current flow in only one direction. Current passes from the (+ long lead) Anode to the (- short lead) Cathode. The Cathode is also known as the Anvil. In this case the LEDs are connected in series and polarity must be observed. So basically the Leds must be joined at opposing leads for current to continue to flow through. Attach Anode to Cathode. Never wire two anodes or cathodes together. Even if you pay attention you will probably mess up at least one. No worries though, it's an easy fix. But not one you will want to repeat too many times, hehe.
Resources:
http://www.theledlight.com/technical1.html
http://en.wikipedia.org/wiki/Light-emitting_diode
Step 3:
Mount LED2 on the board as shown. Be sure to observe the polarity of the Led before bending the leads. This time try bending both leads at the same time up with your thumbs. Again use the hemostats to get the lead ends between the leads and flared out.
Step 4: Mount LED3
Mount LED3 on the other side of the board. Again, be sure to observe the polarity. It is reversed on the opposing side of the board.
Step 5: Mount LED4
Mount LED4 as pictured. It doesn't matter which side of the board you mount LED4. But polarity must still be observed in order to maintain continuity.
Step 6: Mount the Contacts
Here's where the copper wire comes in. A wire diameter just smaller than the hole is best. You can see now how the cut perforations are used. Use them to hold the contact wire when bending it around to meet at the other side where the wire starts. Clip the ends off high at the overlap point. The contacts need ample travel space in order to slide freely into the receptacle.
Step 7: Solder Contact Points
Before you go heating up the soldering iron keep in mind that LEDs are sensitive to high heat . So you will need to protect them from your soldering iron heat by using hemostats, or alligator clips, to dissipate the heat before it gets to the LED itself. You will need at least 2 diodes protected at a time as you solder along. But you will have to move a clip forward as you work so the next diode is protected. They make little clips just for this purpose and they will work as well.
As you are getting ready for soldering double check and make sure all the diodes are running in the same direction. Review the connection points. Soldering will add a considerable amount of stability. But this is your last chance to spot any problems before soldering. Trying to desolder one of these isn't an option in my book.
Note: My poor old soldering station (since replaced) was on it's last legs. So if my soldering isn't up to snuff that's why, hehe.
Step 8: Replace the Old Bulb !
It's time to change out the old bulb with your new LED bulb! It should light right up. But if it doesn't pull it and turn it around and try it again. If it still doesn't work plug the old one back in. If it still lights up it's time to troubleshoot the LED bulb. One of the LEDs may be backwards. Or there is a short, or broken connection somewhere. If it's an Led just clip the offending leads off at the halfway point. This will give you something to solder the new one onto. Don't try reusing the one you clipped off. The short leads are a pain and chances are it won't survive soldering anyway. Besides it's preferable to solve the problem outright rather than chance further time loss and aggravation over a single diode, hehe.
You can also use different color LEDs that have a Voltage rating near that of a white LED. Colors with lower Voltage ratings can of course also be used. But I'm pretty sure the number of LEDs would have to increase to five. I posted resource links if you want investigate further. I made the RWB light below with Straw Hat LEDs for Red and Blue. Because they are what I had on hand. Straw Hat LEDs have a wider light dispersal and so are less focused. Great if you want something more moody. I finally went with a few white/blue bulbs near the entry among the sea of bluish white lights in the rest of the yard. One final thing. The lighting units you see here had three outer plastic rings. One is the lid. The other two slide over the lense. In these pics you can see that the center ring has been removed. This was to allow for maximum light to emit from the device and improve the visual quality of my new LED landscape lights! You might think, "This is gonna take forever!". But I did 16 bulbs in three nights while watching a movie. It was really very rewarding to change out that 500W transformer. Just remember to watch out for...
Have fun and good luck!
Resources:
http://ledcalc.com/
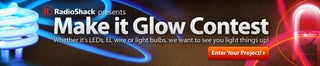
Participated in the
Make It Glow