Introduction: DIY Metal Stamping
So I'm all about pushing the limits of DIY fabrication, and the thought crossed my mind to try out one of the more intensive manufacturing techniques: metal stamping! I've had quite a bit of experience with 3-axis CNC Milling, so I decided to try my hand at making some stamping dies.
I'll be doing some more complicated stamping in the future, but to start out I wanted to make something a little bit on the smaller scale. I decided on stamping out a simple metal watch face out of some thin aluminum sheet I found lying around. The materials cost me only around 5 or 6 dollars, although I admit that access to CNC machines and tooling is not included in that sum. I'm hoping, however, that the lessons I learned from this project will be valuable to the DIY community, especially as I continue to explore more DIY-friendly improvements to this process.
I would love to hear your feedback or any experiences you've had with this and similar processes. I'm hoping to share everything I learned but I'm also hoping to learn anything I can before I try some more involved projects!
Here's a quick run-down on the materials and tools I used:
Materials:
.019" Aluminum Sheet (not sure what series of aluminum it is, but the label on the box said that it was some sort of photosensitive aluminum?) - I used about 4"x24" of the sheet for this project
2.75" Diameter Steel Round Bar (Mild steel) - I used a length of about 2-3" total (approximately 1.5" per side of the die)
.100" Stainless Steel Round Bar (Hardened Steel) - I used two 3" lengths
Tools:
Haas 3-axis CNC Mill (3/8" Flat End Mill, 1/4" Ball End Mill, 1/8" Ball End Mill, .100" Drill Bit)
Hydraulic Press
Flathead Screwdriver (to pry the dies apart)
Propane Torch (we'll talk about this in detail later)
Step 1: Make Your 3D Model
First, I made 3D models for the positive and negative dies. I use Fusion 360 since it's free for students, hobbyists, and startups. For those of you that are not very familiar with 3D modelling, this is an excellent program to get started with. There are tons of "how-to" videos and a great support system with answers to any questions you might have.
This is a good time to mention the offset between the two dies. Since the sheet metal has thickness of .019 inches, there must be a "gap" between the two dies that allows the sheet metal to "fit" during the stamping process. While it would be possible to include this offset in my 3D models, I decided to incorporate it later on in the process. This saved me subtracting .019 inches from all of the geometry used to make the 3D model (or from figuring out a scale factor that would match the .019 inch offset).
Depending on the capabilities of the programs you may or may not have access to, this offset may be included at various steps in the process. Just remember to include it! Without this offset, your die may end up cutting your sheet metal instead of forming it to the desired shape.
The last thing I would like to point out on this step is that you want to design your model with your tooling in mind. What that really means is that if the smallest tool you can put in your CNC machine is 1/8", you can't make any features on your 3D model that are smaller than that. There's no use in designing something that you can't make. So be aware of your limitations and then get to it!
Fusion 360 Stuff:
Step 2: CAM Your Model
CAM is an acronym that stands for "Computer Aided Machining". In this step, I used my 3D model to create a series of "tool paths" to be able to create the two dies. These tool paths, along with pre-determined speeds and feeds, will determine how the steel blanks will be cut and formed into the final product.
The CAM program I used is called MasterCAM. Personally, I find MasterCAM intuitive and straightforward; it gives me all the control I need, even with the complicated surfaces we'll be dealing with in this project. Fusion 360 comes with its own CAM software (which is super convenient because you don't have to worry about any file transfer, etc.), but I haven't had enough time to play around with it and get comfortable with how it works, so I decided to stick with MasterCAM.
Without going into specifics, I'll explain my approach to the CAM/CNC process for this step:
I didn't want to take too much time cutting these dies out, but I did want a good surface finish. I decided to use a 3/8", four-flute HSS finish endmill to remove the bulk of the material, and then I cleaned up the surfaces with a four-flute 1/4" ball end mill and 1/8" ball end mill.
This is where the offset comes into play. MasterCAM has a setting that controls how much material is "left" between the cutting edge of the tool and the edge of your 3D model. In order to create the offset, all I had to do was tell it to "leave" -.019 inches of material on the edges. Well it turns out that "leaving" a negative amount of material really corresponds to removing an extra .019 inches, which is exactly what we want! If you decide to go about it in this fashion, remember that this only needs to be done on one of the dies. If we were to have done it on both sides, the offset would have been .038 inches and the metal would have had too much room to wiggle around.
It's time to CNC! After preparing the two steel blanks and placing them firmly in the vise, I was ready to run the CAM program and watch the 3-axis Haas CNC do all the work! Each side took about 45-60 minutes, but I can only imagine that with larger dies it could take hours to get a good-quality finish.
Step 3: Lessons Learned While Making the Dies
So here are some pictures of the finished dies, and I'll explain a few lessons I learned from this process.
Big Lesson #1: Just because you want these dies to mesh together perfectly doesn't mean they're going to.
So I pulled my two dies out of the CNC, slapped them together, and voila! They fit together just right. It was a very fulfilling moment. I then had the unfortunate realization that if the two sides weren't lined up perfectly, pressing down on them with thousands of pounds of force would result in any number of undesirable outcomes. I also realized that I had no way of ensuring that they were lined up perfectly. So my quick remedy was to drill two holes through the dies and feed two stainless steel rods through these holes. These rods would allow the two halves to "index" into the right position every time. Moral of the story: have some reliable way of making sure that your dies line up.
Big Lesson #2: This is a DIY project after all, so there's no need for overkill.
When I used the 1/8" ball endmill to cut the cleaning passes on the dies, I used a "stepdown" of .004 inches. That means that if a die is .5 inches deep, the machine would make 125 trips around the profile of the die before reaching the final depth. Hopefully the pictures can help you see what I'm talking about, but basically I found that these "stepdowns" were totally redundant. I probably could have increased the stepdown to .008 or .010 without noticing a difference in the final, stamped watch face. This would have significantly decreased the cutting time to make the dies. Next time, I guess!
Step 4: Preparing the Sheet Metal for Stamping
For this particular set of dies, I needed a piece of sheet metal with a few features to ensure that it would stay in the correct position during the stamping process. The rectangle has a large hole in the center and two semicircle indentations on either side. These indentations line up with the two steel rods, and the hole in the center lines up with the extrusion in the middle of the positive die. The pictures should help clarify.
You may ask: why would you put a huge hole right in the middle of your piece? Initially, I was under the impression that having the hole there would relieve some of the stresses in the metal during the stamping. We'll talk about this in future steps, as this will come back to bite me in the butt. Thanks to some great feedback from the Instructables community, however, I was able to change my ways and improve on this step of the process. To see what I'm talking about, check out steps 8-10!
Step 5: The Stamping Process
It's time for stamping! This process is pretty straightforward, it basically consists of three steps:
1. Place the sheet metal in the correct position on the positive die and slide the negative on top! It's like a little metal sandwich!
2. Find a long, metal cylinder that will fit between the two stainless steel rods. Place this cylinder on top of the metal sandwich and place the entire assembly under the press.
3. Cross your fingers and engage the hydraulic press!
The video isn't too exciting, so we'll get to the results in the next step.
Step 6: Results (Round 1)
Complete and utter failure. Isn't it great?
On the bright side, we know that the dies match up because there wasn't any binding going on during the stamping process. In fact, I was surprised by how easily the two halves separated.
So there were a number of tears, most of which stemmed from the large hole in the center of the sheet. So basically, for all the stress that the hole relieved, there was still too much stress for the aluminum to handle. The other areas on the watch face formed pretty well, but unless torn watch faces become a new trend, I think we're gonna need to give it another shot.
Step 7: Results (Round 2)
So, it turns out that our failure from round 1 was probably inevitable. Why? Because we used aluminum (and we didn't use any lubrication, but we'll talk about that a little bit later). Aluminum is notorious for tearing or cracking when it deforms. Additionally, without knowing the specific series (or "type") of aluminum, it's hard to know exactly how it's going to react to our stamping. So, before taking another shot at it, I decided to do the only thing I could think of: heat it up! Heating up the aluminum (just shy of the melting point) and allowing it to cool will "anneal" the material. This annealing process will "soften" the aluminum and make it more ductile.
The same process was followed as in the previous stamping attempt, except that the aluminum was heated up with a propane torch prior to the stamping.
And voila! It worked! Mostly. There were still a few tears, but luckily these were near the bottom edges of the watch face, where we wanted it to remove anyway. Looking closely at the edges of the stamping, we can see that the aluminum is pretty close to giving way, but it still managed to stay together. Also, the back of the aluminum discolored quite a bit from our makeshift heat-treatment. This was most likely due to the surface treatment it had received as "photosensitive" aluminum, however.
I was pleased with these results, but there are still a few opportunities for improvement. First and foremost, the main hole was warped in the stamping process and isn't quite circular. In future iterations, I would decrease the initial size of the hole (which would involve adjusting the dies as well, unfortunately). This would leave enough extra material so that after all is said and done, I could punch out the finish diameter, leaving a perfect circle.
I hope to repeat this exploration process with a similar thickness of stainless steel, and I hope to be posting those results soon! Please leave comments with your experience and expertise so that we all can get a little bit better at metal stamping.
Step 8: Adjustments/Improvements!
I got a ton of good feedback and advice from the Instructables community on my first seven steps, so I decided to make some of the advised adjustments and see how it goes!
First of all, I received a lot of commentary on materials. notingkcool, bpark1000, sailor_sid, and others made valuable comments on the complicated nature of aluminum heat treatment, so I decided to try a out a more resilient material: stainless steel! Call me lazy but I had the feeling that using stainless steel would save me from the frustration of heat-treating the aluminum. And it just so happens that my friend had a bunch of .019" stainless steel sheet hanging around! He let me borrow enough for a few blanks and so I took another shot at it!
A number of comments also involved or hinted towards the use of lubrication (Prfesser, carl5blum, KarcsiS1, and others). I didn't have die lubrication on hand, so I ended up using some "Way Oil" (the oil used to lubricate the ways on mills, lathes, etc) to lubricate the metal blank as well as the two halves of the die. I made sure to apply a very thin coating so as to avoid the entrapment of oil bubbles within the die.
Carl5blum mentioned the removal of the hole from the initial blank, which required some adjustment to the die. I stuck the die in the lathe and removed the central column from the positive die. Luckily, no adjustments to the negative die were necessary. This change, however, requires the hole to be punched after the stamping of the watch face.
Step 9: Results (Round 3)
The attempt with aluminum (lubrication, no heat treatment) was almost successful! But not quite. Looks like heat treatment would have to be involved in order to make it work for this specific series of aluminum. The lubrication, however, did cause significant improvement in the results.
The attempt with the stainless steel was fantastic! It did get stuck a little bit in the negative mold, but I was able to remove it with a reasonable amount of force. The surfaces looked great, the edges were clean, and there were no tears whatsoever. The edges of the blank suffered from quite a bit of the potato-chip effect, as I have not yet been able to design a corresponding pressure-plate (as suggested by carl5blum). I look forward to incorporating a pressure plate in future stamping endeavors!
Really the only downside with using the stainless steel is the wear on the die. Because the die itself is made of a mild steel, repetitive stamping of stainless will eventually wear down on the edges of the dies. Luckily, I'm not going into production any time soon so I won't need to worry about that!
Step 10: The Final Result!
In summary, if you're going to try metal stamping in the future I would suggest shying away from aluminum (unless you also have the resources to correctly heat-treat your aluminum). Steel just seemed to be more resilient and fit for the task. Additionally, I would agree with the comments of many of my fellow DIYers in saying that lubrication is an absolute must. It really does make all the difference.
The stainless steel face turned out to be quite beautiful in my opinion. The lubricant allowed for smooth forming of the metal, and the sheen of the stainless wasn't marred at all by the process. Makes me wish I was actually building an entire watch!
Thank you once again for your input and advice; I enjoyed implementing the changes and seeing the results improve. It's another testament of what a great DIY community is capable of. Feel free to continue sharing advice and pictures of your own metal-stamping endeavors!
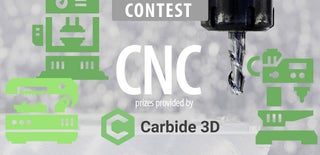
Participated in the
CNC Contest 2016
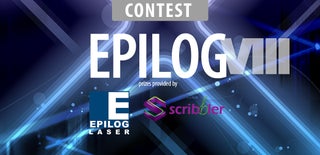
Participated in the
Epilog Contest 8