Introduction: DIY Mini Forge
Lately I've been wanting to make some pocket knives for my friends and family.. So, I'm going to make a simple mini forge at TechShop to temper the steel...
This forge is meant to burn coal.. You can you lump charcoal and wood, but it will take a lot more of it to keep the heat at the right temperature for the duration of the process..
Step 1: Things You Will Need..
MATERIALS USED
-- 1 1/4" Scrap Black Iron Pipe..
-- 1/2" Scrap Black Iron Pipe..
-- 1 1/4" Scrap Iron Pipe Tee..
-- 1 1/4 Scrap Iron Pipe Cap..
-- 1/8" Scrap Angle Iron..
-- Small Scrap Plate of 1/8" Steel..
-- 11" Diameter Scrap Brake Drum..
-- Cheap Hairdryer or Other Blowing Device..
TOOLS USED
-- Horizontal Bandsaw..
-- Cold Saw..
-- Flow Waterjet..
-- Angle Grinder..
-- Lincoln 255xt (MIG)..
Step 2: Waterjet?.. Duh..
We need to plug the five holes in the bottom of the brake drum, and also reduce the diameter of the main hole... Sooo?.. DUH! We're at TechShop, lets waterjet that piece!
We'll cut a small plate with a 1.27" diameter hole in the center. This plate will allow us to mount the black Iron pipe to the bottom of the brake drum.
Step 3: Choppin' Some Pipe..
Time to start cutting that pipe! we got a forge to build!!!
The length you cut on the pipe is up to you. Just think of how tall you want it to stand. This forge is a little over 3 feet..
-- Cut the 1 1/4" pipe down on the bandsaw so that you have two longer pices and one short piece..
-- Make sure the shorter of the pieces has a threaded end so we can attach a cap to let debris out of the pipe..
-- The longer piece that will be mounted to the brake drum should have a threaded end as well. This will allow the blower arm to pivot..
Step 4: Plug Doz Holes and Mount Some Pipe..
-- Hammer the 1/8" steel plate onto one of the longer pipes that were cut..
-- Grab that brake drum and get it ready for some welding..
-- Position the plate and pipe so the that the pipe opening is in the center of the brake drum hole..
-- Weld the plate and pipe together..
-- Weld that plate to the brake drum.. Crank that MIG and make sure you get good penetration..
Step 5: Tee Time..
-- Thread the tee to the pipe coming from the Brake drum.. Thread it enough so that it's almost all the way tightened, but will still let the blower arm rotate..
-- Weld the blower arm to the tee so that it forms a 90° angle with the pipe coming from the brake drum..
-- Weld the shorter pipe to the bottom of the tee..
-- Thread the end cap on.. This will allow us to release any ash or debris that falls into the pipe..
Step 6: Get Your Angle On..
-- Cut down some of the 1/8" angle to make a square on the base of the brake drum..
-- Weld up the little frame on the bottom of the brake drum.. Again make sure you get good penetration on this weld!! This frame will be used to help mount the legs to the brake drum..
Step 7: A Little Mo Choppin'..
-- Cut down that 1/2" pipe on the band saw to the desired height of the forge..
-- Cut down some smaller pieces of pipe to be used as horizontal supports for the legs..
Step 8: Legs and Supports..
-- Cut the ends of 1/2" pipe on the cold saw at a 75° angle.. these ends will be mounted to the frame and brake drum..
-- Weld the legs to the frame and the brake drum.. It's crucial that these are securely welded!
-- Weld some supports for the legs.. this will help with any wobbling..
-- If any of the pieces are uneven.. Cut them down with the angle grinder..
Step 9: We're Blowin' Up..
-- Mount the hair dryer to the blower arm.. I just used duct tape and a slightly larger piece of pipe to mount the blower. I did this because I only want to affix this blower temporarily. I will find a more suitable one in the future..
-- If you use a hair dryer, put a piece of tape over the cool button.. We don't need the blower to blow hot air when the fire will do that for us.. Plus I was worried bout this old thang over heating..
Step 10: Kick the Blower and Spark That Flame..
-- Now you're ready to get that forge burnin'.. I'm not going to get into the details of how to use a forge yet.. I will post another Instructable soon showing you how I temper some of the knives I'm making.. But in the meantime here's a couple shots of it in action..
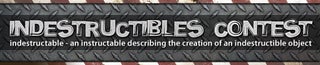
First Prize in the
Indestructibles Contest